Why is Pad-to-Pad Important?
Pad-to-Pad distance plays a vital role in several aspects of PCB design and manufacturing:
1. Component Compatibility
The PP distance must be compatible with the component package being used. Different component packages, such as surface-mount devices (SMDs) and through-hole components, have specific PP requirements. Adhering to these requirements ensures that the components can be properly soldered and mounted on the PCB.
2. Manufacturing Feasibility
The PP distance also affects the manufacturability of the PCB. If the pads are too close together, it becomes challenging to accurately place and solder components, leading to potential assembly issues and reduced yields. On the other hand, if the pads are too far apart, it may result in an inefficient use of PCB space and increased manufacturing costs.
3. Signal Integrity
In high-speed digital circuits, the PP distance can impact signal integrity. Closely spaced pads can lead to crosstalk and electromagnetic interference (EMI) between adjacent signals. Proper PP spacing helps minimize these effects and maintains signal integrity throughout the PCB.
Factors Affecting Pad-to-Pad Distance
Several factors influence the determination of the appropriate PP distance for a given PCB design:
1. Component Package
The component package is the primary factor in determining the PP distance. Each package type has its own set of dimensions and pad spacing requirements. Some common component packages and their typical PP distances are:
Package Type | Typical PP Distance |
---|---|
0402 (SMD) | 0.5 mm |
0603 (SMD) | 0.8 mm |
0805 (SMD) | 1.0 mm |
SOIC-8 | 1.27 mm |
TQFP-44 | 0.8 mm |
2. PCB Manufacturing Capabilities
The manufacturing capabilities of the PCB Fabrication and assembly facility also influence the PP distance. Advanced manufacturing processes, such as high-density interconnect (HDI) PCBs, allow for smaller PP distances compared to standard PCB fabrication techniques. It is essential to consult with the manufacturing facility to determine their minimum PP capabilities and design the PCB accordingly.
3. PCB Layer Stack-Up
The layer stack-up of the PCB can impact the PP distance, especially in Multi-layer Boards. The thickness of the dielectric material between layers and the presence of ground or power planes can affect the spacing between pads on different layers. The PCB designer must consider the layer stack-up and adjust the PP distance accordingly to ensure proper signal integrity and manufacturability.
4. Soldermask and Solder Paste
The application of soldermask and solder paste also influences the PP distance. Soldermask is a protective coating applied to the PCB to prevent Solder Bridging between adjacent pads. The thickness of the soldermask and its registration accuracy must be considered when determining the PP distance. Similarly, the solder paste printing process and the size of the solder paste apertures impact the minimum achievable PP distance.
Pad-to-Pad Design Guidelines
To ensure optimal PP distances in PCB design, follow these guidelines:
- Consult component datasheets for recommended pad dimensions and spacing.
- Consider the manufacturing capabilities of the PCB fabrication and assembly facility.
- Adhere to industry standards, such as IPC-7351, for generic component land patterns.
- Use PCB design software that provides automatic pad generation based on component packages.
- Perform design rule checks (DRC) to verify that PP distances meet manufacturing constraints.
- Collaborate with the manufacturing team to optimize PP distances for specific components or design requirements.
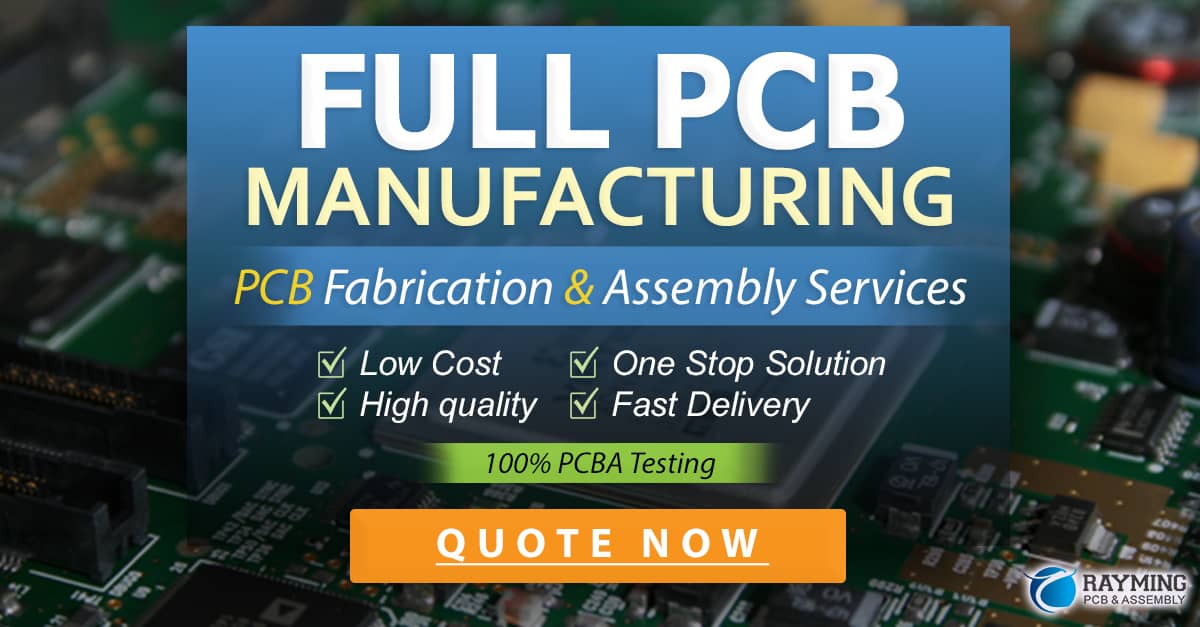
Case Study: Optimizing Pad-to-Pad Distance
To illustrate the importance of PP distance optimization, let’s consider a case study involving a high-density PCB design for a mobile device.
Design Challenges
The mobile device PCB posed several challenges:
- Limited PCB space due to the compact form factor of the device.
- High component density, including fine-pitch SMD components.
- High-speed digital interfaces requiring strict signal integrity.
- Cost constraints necessitating efficient PCB manufacturing.
Pad-to-Pad Optimization Process
To address these challenges, the PCB design team followed a systematic approach to optimize the PP distances:
-
Component Selection: The team carefully selected components with compatible package sizes and PP requirements. They opted for smaller package sizes, such as 0402 and 0603, wherever possible to minimize the PCB space.
-
Manufacturing Collaboration: The design team collaborated closely with the PCB fabrication and assembly facility to determine their minimum PP capabilities. They agreed on a minimum PP distance of 0.4 mm for the majority of the components.
-
Layer Stack-up Optimization: The PCB layer stack-up was optimized to minimize the impact of PP distance on signal integrity. The team used thin dielectric materials between layers and strategically placed ground planes to reduce crosstalk and EMI.
-
Design Rule Checks: Throughout the design process, the team performed rigorous design rule checks to ensure that the PP distances met the manufacturing constraints. They used PCB design software with built-in DRC tools to identify and resolve any PP-related issues.
Results and Benefits
By optimizing the PP distances, the PCB design team achieved several benefits:
-
Reduced PCB Size: The optimized PP distances allowed for a more compact PCB layout, enabling the mobile device to have a smaller form factor.
-
Improved Signal Integrity: The carefully planned PP distances, along with the optimized layer stack-up, resulted in improved signal integrity and reduced crosstalk and EMI.
-
Cost Savings: The efficient use of PCB space and the adherence to manufacturing constraints led to cost savings in both PCB fabrication and assembly.
-
Enhanced Reliability: The optimized PP distances contributed to the overall reliability of the mobile device by ensuring proper component soldering and minimizing potential assembly issues.
Frequently Asked Questions (FAQ)
-
What is the minimum Pad-to-Pad distance for SMD components?
The minimum PP distance for SMD components depends on the specific package size and the manufacturing capabilities of the PCB fabrication and assembly facility. Commonly, for 0402 packages, the minimum PP distance can be as low as 0.4 mm, while for larger packages like 0805, it may be around 0.8 mm. However, it is essential to consult with the manufacturing facility to determine their specific minimum PP capabilities. -
Can Pad-to-Pad distance affect signal integrity?
Yes, PP distance can have a significant impact on signal integrity, especially in high-speed digital circuits. If the pads are too close together, it can lead to crosstalk and electromagnetic interference (EMI) between adjacent signals. Proper PP spacing helps minimize these effects and maintains signal integrity throughout the PCB. -
How does the PCB layer stack-up influence Pad-to-Pad distance?
The layer stack-up of the PCB can affect the PP distance, particularly in multi-layer boards. The thickness of the dielectric material between layers and the presence of ground or power planes can impact the spacing between pads on different layers. The PCB designer must consider the layer stack-up and adjust the PP distance accordingly to ensure proper signal integrity and manufacturability. -
What are the consequences of improper Pad-to-Pad distance?
Improper PP distance can lead to several issues, such as: - Difficulty in accurately placing and soldering components, resulting in assembly issues and reduced yields.
- Increased risk of solder bridging between adjacent pads, causing short circuits and reliability problems.
- Degraded signal integrity due to crosstalk and EMI between closely spaced pads.
-
Inefficient use of PCB space, leading to larger board sizes and increased manufacturing costs.
-
How can PCB design software help in optimizing Pad-to-Pad distance?
PCB design software plays a crucial role in optimizing PP distance. Most modern PCB design tools offer features such as: - Automatic pad generation based on component packages, ensuring consistent and accurate pad spacing.
- Design rule checks (DRC) that verify PP distances meet manufacturing constraints and highlight any violations.
- Interactive routing and placement tools that provide real-time feedback on PP distances and help optimize component placement.
- Integration with component libraries and datasheets, providing recommended pad dimensions and spacing information.
By leveraging these features, PCB designers can efficiently optimize PP distances, reducing design time and minimizing the risk of manufacturing issues.
Conclusion
Pad-to-Pad (PP) distance is a critical factor in PCB design and manufacturing. It directly impacts component compatibility, manufacturing feasibility, signal integrity, and overall PCB reliability. By understanding the factors affecting PP distance and following best practices and guidelines, PCB designers can optimize their designs for optimal performance and manufacturability.
Collaborating with component suppliers, manufacturing facilities, and leveraging the capabilities of PCB design software are key strategies for successful PP optimization. As electronic devices continue to become more compact and complex, the importance of proper PP distance will only grow. PCB designers must stay up-to-date with the latest industry standards, manufacturing technologies, and design techniques to ensure the success of their products in the ever-evolving world of electronics.
0 Comments