Understanding Soldermask and CTI
Soldermask, also known as solder resist, is a thin layer of polymer applied to the copper traces of a printed circuit board (PCB). Its primary purpose is to protect the copper from oxidation and prevent Solder Bridges from forming between closely spaced pads during the soldering process. In addition to these functions, soldermask also provides electrical insulation, improves the board’s appearance, and enhances its durability.
Comparative Tracking Index (CTI) is a measure of a material’s ability to resist electrical tracking or carbonization when exposed to high voltage gradients under wet conditions. The higher the CTI value, the better the material’s resistance to electrical breakdown. In PCB manufacturing, soldermask plays a crucial role in determining the board’s overall CTI performance.
CTI Classifications
The International Electrotechnical Commission (IEC) has defined several CTI classes based on the material’s performance under standardized testing conditions:
CTI Class | Voltage Range (V) |
---|---|
0 | ≤ 400 |
1 | 400 < V ≤ 600 |
2 | 600 < V ≤ 800 |
3 | 800 < V ≤ 1000 |
4 | > 1000 |
High CTI boards, typically Class 3 or higher, are essential for applications that require enhanced electrical safety and reliability, such as:
- Automotive electronics
- Industrial control systems
- Medical devices
- Aerospace and defense equipment
Soldermask Material Selection for High CTI Boards
Choosing the right soldermask material is critical to achieving the desired CTI performance in high-voltage applications. The most common soldermask materials used in PCB manufacturing are:
-
Liquid Photoimageable Soldermask (LPISM): LPISM is a UV-curable polymer that is applied as a liquid and then exposed to UV light through a photomask to form the desired pattern. It offers excellent resolution, adhesion, and chemical resistance.
-
Dry Film Photoimageable Soldermask (DFISM): DFISM is a solid film that is laminated onto the PCB surface and then exposed and developed like LPISM. It provides consistent thickness and good electrical insulation properties.
-
Liquid Photoimageable Epoxy Soldermask (LPI-E): LPI-E is a high-performance soldermask material that combines the advantages of LPISM and epoxy resins. It offers superior thermal and chemical resistance, as well as excellent electrical insulation and adhesion.
When selecting a soldermask material for high CTI boards, consider the following factors:
- CTI rating of the material
- Dielectric strength
- Thermal and chemical resistance
- Adhesion to copper and laminate
- Resolution and edge definition
- Compatibility with the manufacturing process
Recommended Soldermask Materials for High CTI Boards
Material | CTI Class | Key Features |
---|---|---|
Taiyo PSR-4000 HV | 4 | High CTI, excellent resolution, halogen-free |
Electra EMP110-HC | 4 | High CTI, superior chemical resistance, RoHS compliant |
Hitachi Chemical SR-420C | 4 | High CTI, excellent thermal and chemical resistance |
Soldermask Application and Processing for High CTI Boards
Proper application and processing of the soldermask are essential to achieve the desired CTI performance and ensure the reliability of the finished PCB. The following steps outline the general process for applying soldermask to high CTI boards:
-
Surface Preparation: Clean the PCB surface to remove any contaminants, such as dirt, grease, or oxidation. This step ensures good adhesion of the soldermask to the copper and laminate.
-
Soldermask Application: Apply the soldermask material using screen printing, Curtain Coating, or spraying techniques, depending on the specific material and manufacturer’s recommendations. Ensure uniform coverage and thickness across the board.
-
Pre-drying: Pre-dry the soldermask to remove solvents and improve its stability before exposure. Follow the manufacturer’s guidelines for temperature and time settings.
-
Exposure: Expose the soldermask to UV light through a photomask to crosslink and harden the polymer in the desired pattern. The exposure time and energy depend on the material and the required resolution.
-
Development: Remove the unexposed soldermask areas using a suitable developer solution, typically an alkaline solution for LPISM and DFISM or a solvent for LPI-E. Rinse the board thoroughly with water to remove any residual developer.
-
Curing: Fully cure the soldermask by exposing it to elevated temperatures, typically between 130°C and 150°C, for a specified time. This step ensures complete crosslinking of the polymer and enhances its mechanical, chemical, and electrical properties.
-
Inspection: Visually inspect the soldermask for defects, such as pinholes, blisters, or incomplete coverage. Use automated optical inspection (AOI) systems for consistent and reliable quality control.
Soldermask Processing Guidelines for High CTI Boards
Parameter | Recommendation |
---|---|
Thickness | 0.8-1.2 mils (20-30 μm) for optimal insulation |
Exposure Energy | 300-500 mJ/cm² for high resolution and edge definition |
Developing Time | 60-90 seconds for complete removal of unexposed areas |
Curing Temperature | 130-150°C for enhanced mechanical and electrical properties |
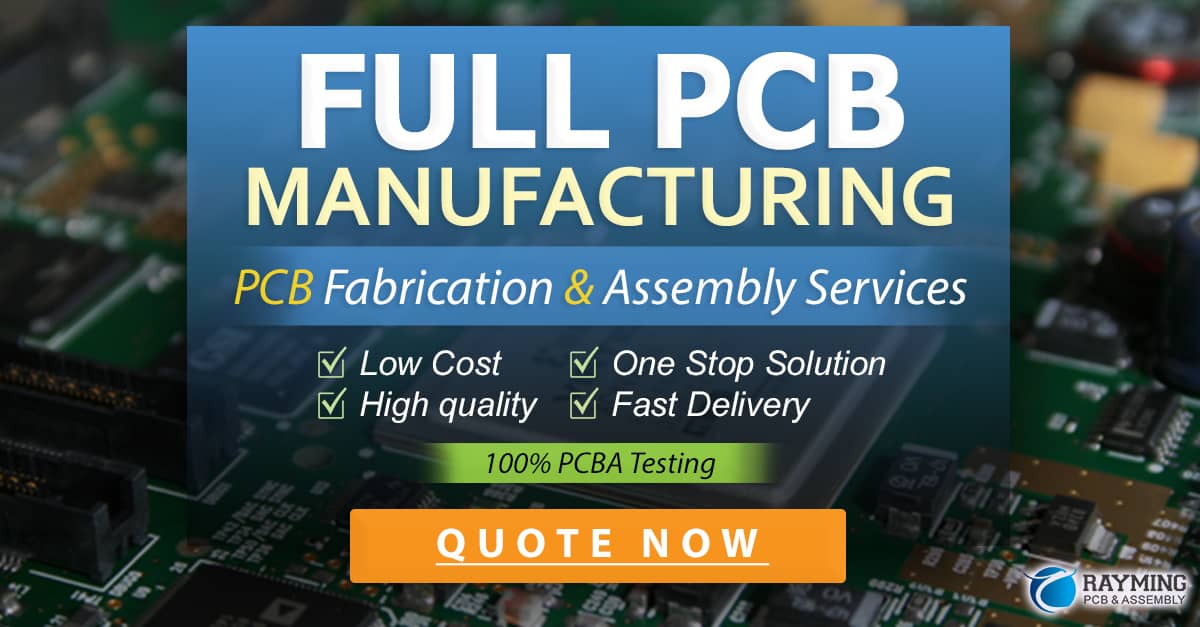
Design Considerations for High CTI Boards
In addition to selecting the appropriate soldermask material and ensuring proper processing, designers must consider several factors when creating high CTI boards:
-
Clearance and Creepage Distances: Maintain sufficient clearance and creepage distances between conductors to prevent electrical breakdown. Follow the IPC-2221 standard for guidance on minimum spacing requirements based on the application’s voltage and environmental conditions.
-
Soldermask Thickness: Specify an adequate soldermask thickness, typically 0.8-1.2 mils (20-30 μm), to provide sufficient insulation and protection against electrical tracking.
-
Via Tenting: Tent vias with soldermask to prevent solder from wicking into the holes and creating potential short circuits. Ensure complete coverage of the via pads to maintain the board’s CTI performance.
-
Solder Mask Defined (SMD) vs. Non-Solder Mask Defined (NSMD) Pads: Consider using SMD pads for improved soldermask adhesion and reduced risk of Solder Bridging. NSMD pads may be necessary for fine-pitch components or high-density designs.
-
Soldermask Color: Choose a soldermask color that provides good contrast with the copper traces and component markings for ease of inspection and assembly. Green is the most common color, but other options, such as black, blue, or white, are available for specific applications.
Testing and Qualification of High CTI Boards
To ensure that high CTI boards meet the required performance and reliability standards, manufacturers must conduct thorough testing and qualification processes. Some of the key tests include:
-
CTI Testing: Perform CTI testing according to IEC 60112 to verify the soldermask material’s resistance to electrical tracking. The test involves applying a voltage gradient to the material under wet conditions and measuring the voltage at which tracking occurs.
-
Insulation Resistance (IR) Testing: Measure the board’s insulation resistance using a high-voltage megohmmeter to ensure that the soldermask provides adequate electrical insulation between conductors. The minimum acceptable IR value depends on the application and the relevant industry standards.
-
Dielectric Withstanding Voltage (DWV) Testing: Apply a high voltage between conductors and the ground plane to verify that the soldermask can withstand the expected voltage stress without breakdown. The test voltage and duration are based on the application’s requirements and the relevant safety standards.
-
Environmental Testing: Expose the board to various environmental stresses, such as thermal cycling, humidity, and salt spray, to assess the soldermask’s durability and adhesion under realistic operating conditions.
Qualification Standards for High CTI Boards
Standard | Description |
---|---|
IEC 60112 | Method for the determination of the proof tracking index (PTI) and the comparative tracking index (CTI) |
IPC-SM-840E | Qualification and Performance of Permanent Solder Mask |
IPC-TM-650 2.6.3 | Insulation Resistance Test Methods |
FAQs
- What is the difference between CTI and PTI?
-
CTI (Comparative Tracking Index) and PTI (Proof Tracking Index) are both measures of a material’s resistance to electrical tracking. However, CTI is determined using a standardized test method (IEC 60112) that compares the material’s performance to a reference material, while PTI is a specific voltage at which the material withstands 50 drops without tracking.
-
Can high CTI soldermask be used on Flexible PCBs?
-
Yes, there are soldermask materials specifically formulated for use on Flexible PCBs that offer high CTI performance. These materials, such as Taiyo LPI-F1000, provide excellent flexibility, adhesion, and electrical insulation properties.
-
Is it possible to achieve a high CTI rating with a matte finish soldermask?
-
Yes, some high CTI soldermask materials, such as Electra EMP110-HM, are available in matte finish options. However, it is essential to consult with the material manufacturer to ensure that the matte finish does not compromise the CTI performance.
-
How does the soldermask color affect the CTI performance?
-
The soldermask color itself does not directly impact the CTI performance. However, some pigments used in colored soldermasks may influence the material’s electrical and mechanical properties. It is essential to choose a soldermask material that has been formulated and tested to provide the required CTI rating regardless of the color.
-
Can high CTI soldermask be reworked or repaired?
- Reworking or repairing high CTI soldermask can be challenging, as the material is designed to withstand high voltage gradients and provide excellent adhesion to the PCB surface. In most cases, it is recommended to strip the damaged soldermask area completely and reapply fresh soldermask material to ensure the board’s integrity and performance. Consult with the soldermask manufacturer for specific repair guidelines and compatible rework materials.
By understanding the soldermask requirements for high CTI boards, selecting the appropriate materials, and following best practices for design, processing, and testing, manufacturers can produce PCBs that meet the demanding electrical safety and reliability needs of various industries.
0 Comments