The Importance of PCB Environmental Control
Printed Circuit Boards (PCBs) are the backbone of modern electronics. They are used in virtually every electronic device, from smartphones and computers to medical equipment and aerospace systems. The manufacturing of PCBs is a complex process that requires strict control over various environmental factors, including light and moisture. Failure to maintain proper environmental conditions can lead to defects, reduced reliability, and even complete failure of the PCBs.
In this article, we will explore the importance of light and moisture control in PCB manufacturing and discuss the various methods and technologies used to maintain optimal environmental conditions.
Why Light Control is Critical in PCB Manufacturing
Light plays a crucial role in the PCB manufacturing process, particularly during the photolithography stage. In this stage, a photosensitive material called photoresist is applied to the surface of the PCB. The photoresist is then exposed to light through a photomask, which contains the circuit pattern. The light causes a chemical reaction in the exposed areas of the photoresist, making it soluble in a developing solution. The unexposed areas remain insoluble and protect the underlying copper layer during the etching process.
However, if the light exposure is not properly controlled, it can lead to several problems:
-
Overexposure: If the photoresist is exposed to too much light, it can cause the circuit features to become smaller than intended, leading to reduced spacing between traces and potential short circuits.
-
Underexposure: If the photoresist is not exposed to enough light, it may not fully develop, leaving residual photoresist on the copper surface. This can cause open circuits or poor adhesion of the photoresist, leading to defects during the etching process.
-
Stray light: Light leaks or reflections from surfaces inside the exposure equipment can cause unintended exposure of the photoresist, leading to ghost images or poor feature definition.
To mitigate these issues, PCB Manufacturers employ several light control measures:
Light Control Measure | Description |
---|---|
Yellow Room Lighting | PCB manufacturing facilities often use yellow light in the photolithography area, as photoresist is less sensitive to yellow light compared to blue or UV light. This reduces the risk of accidental exposure. |
Light-Tight Equipment | Exposure equipment is designed to be light-tight, preventing stray light from entering and affecting the exposure process. |
Collimated Light Sources | Collimated light sources, such as mercury vapor lamps or LEDs, produce parallel light rays that minimize the impact of diffraction and ensure sharp feature definition. |
Photomask Quality Control | High-quality photomasks with precise feature dimensions and minimal defects are essential for accurate light exposure. |
The Role of Moisture Control in PCB Manufacturing
Moisture is another critical environmental factor that must be controlled during PCB manufacturing. Excess moisture can cause various issues, including:
-
Delamination: High moisture content can weaken the adhesion between the layers of the PCB, causing them to separate or delaminate. This can lead to electrical failures and reduced mechanical strength.
-
Corrosion: Moisture can promote the corrosion of metal surfaces on the PCB, particularly in the presence of ionic contaminants. Corrosion can cause open circuits, short circuits, and reduced reliability.
-
Warpage: Moisture absorption can cause the PCB Substrate to expand, leading to warpage or dimensional changes. This can cause misalignment during the assembly process and stress on the components.
-
Soldermask Adhesion: Excess moisture can interfere with the adhesion of the soldermask, a protective coating applied to the PCB surface. Poor soldermask adhesion can expose the underlying circuitry to damage and contamination.
To control moisture levels, PCB manufacturers implement several strategies:
Moisture Control Strategy | Description |
---|---|
Humidity Control | PCB manufacturing areas are typically maintained at a relative humidity of 40-60% to minimize moisture-related issues. This is achieved through the use of dehumidifiers, air conditioning systems, and moisture barriers. |
Baking | Prior to critical processes such as Solder Mask application or final assembly, PCBs are often baked in an oven to remove any absorbed moisture. Typical baking temperatures range from 120-150°C for several hours. |
Moisture-Sensitive Device (MSD) Handling | Components that are particularly sensitive to moisture, such as certain types of surface-mount devices, are handled in accordance with MSD protocols. This includes storage in moisture-barrier bags with desiccants and strict control over exposure time during assembly. |
Conformal Coating | In some applications, a conformal coating is applied to the assembLED PCB to protect it from moisture and other environmental factors. Conformal coatings can be acrylic, silicone, or urethane-based, depending on the specific requirements. |
Frequently Asked Questions (FAQ)
-
Q: What is the ideal relative humidity level for PCB manufacturing?
A: The ideal relative humidity level for PCB manufacturing is typically between 40-60%. This range minimizes the risk of moisture-related issues while maintaining a comfortable working environment for personnel. -
Q: Why are PCBs baked prior to certain processes?
A: PCBs are baked prior to processes such as solder mask application or final assembly to remove any absorbed moisture. Moisture can cause delamination, warpage, and interfere with adhesion, so baking helps ensure the PCB is dry and stable. -
Q: What type of light source is used in PCB exposure equipment?
A: PCB exposure equipment typically uses collimated light sources, such as mercury vapor lamps or LEDs. These light sources produce parallel light rays that minimize the impact of diffraction and ensure sharp feature definition during the photolithography process. -
Q: How does moisture cause delamination in PCBs?
A: Moisture can weaken the adhesion between the layers of the PCB. When the PCB is exposed to high temperatures, such as during soldering, the absorbed moisture can vaporize and expand, causing the layers to separate or delaminate. This can lead to electrical failures and reduced mechanical strength. -
Q: What is the purpose of conformal coating on PCBs?
A: Conformal coating is a protective layer applied to the surface of assembled PCBs. Its primary purpose is to protect the PCB from moisture and other environmental factors, such as dust, chemicals, and mechanical damage. Conformal coatings can be acrylic, silicone, or urethane-based, depending on the specific application requirements.
Conclusion
The control of light and moisture in PCB manufacturing is essential for ensuring the quality, reliability, and performance of the final product. Light control is critical during the photolithography process, where precise exposure of the photoresist is necessary for accurate circuit feature definition. Moisture control, on the other hand, is crucial throughout the manufacturing process to prevent issues such as delamination, corrosion, warpage, and poor soldermask adhesion.
PCB manufacturers employ a range of strategies and technologies to maintain optimal environmental conditions, including yellow room lighting, light-tight equipment, collimated light sources, humidity control, baking, MSD handling, and conformal coating. By implementing these measures, manufacturers can consistently produce high-quality PCBs that meet the demanding requirements of various industries.
As electronics continue to advance and become more complex, the importance of environmental control in PCB manufacturing will only continue to grow. Manufacturers that invest in state-of-the-art environmental control systems and adhere to strict quality control processes will be well-positioned to meet the challenges of the future and deliver reliable, high-performance PCBs for a wide range of applications.
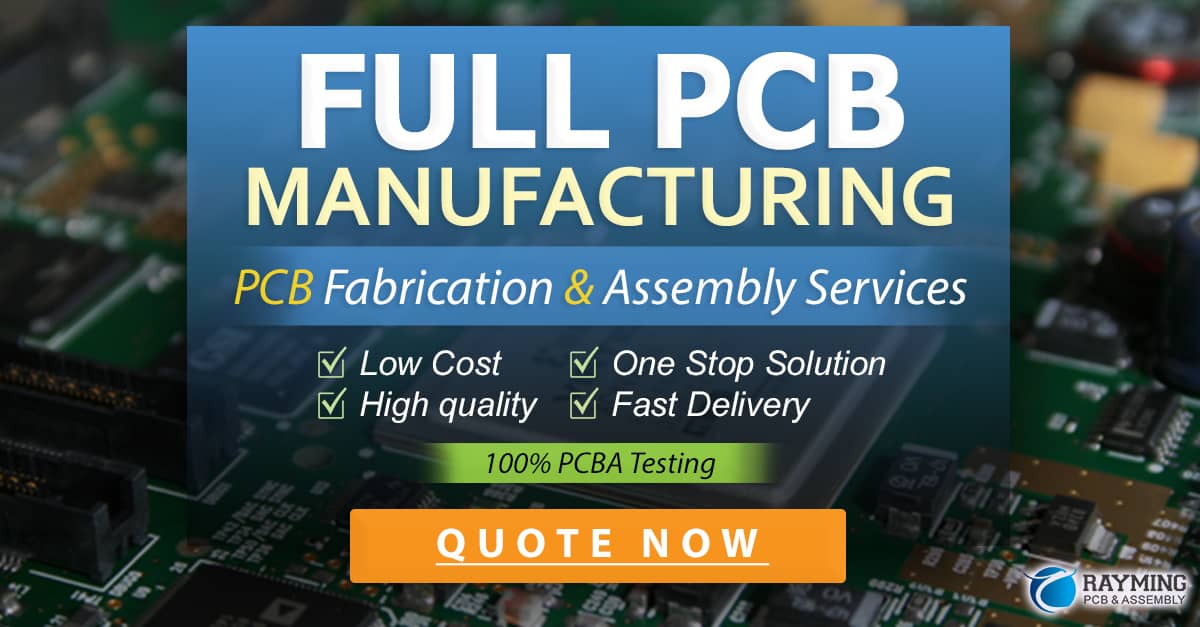
0 Comments