In the world of electronics, Printed Circuit Boards (PCBs) are an essential component that forms the backbone of most electronic devices. From simple microcontroller projects to complex computer systems, PCBs are ubiquitous. While commercial PCB manufacturing services are widely available, there is a growing interest in DIY PCB fabrication among hobbyists, makers, and students. DIY PCB fabrication allows you to create custom PCBs for your projects, providing a cost-effective and rewarding experience.
In this comprehensive guide, we will delve into the fascinating world of DIY PCB fabrication, covering various techniques, tools, and materials required to create your own PCBs at home. Whether you’re a beginner or an experienced enthusiast, this guide will equip you with the knowledge and skills necessary to bring your electronic designs to life.
Understanding PCBs
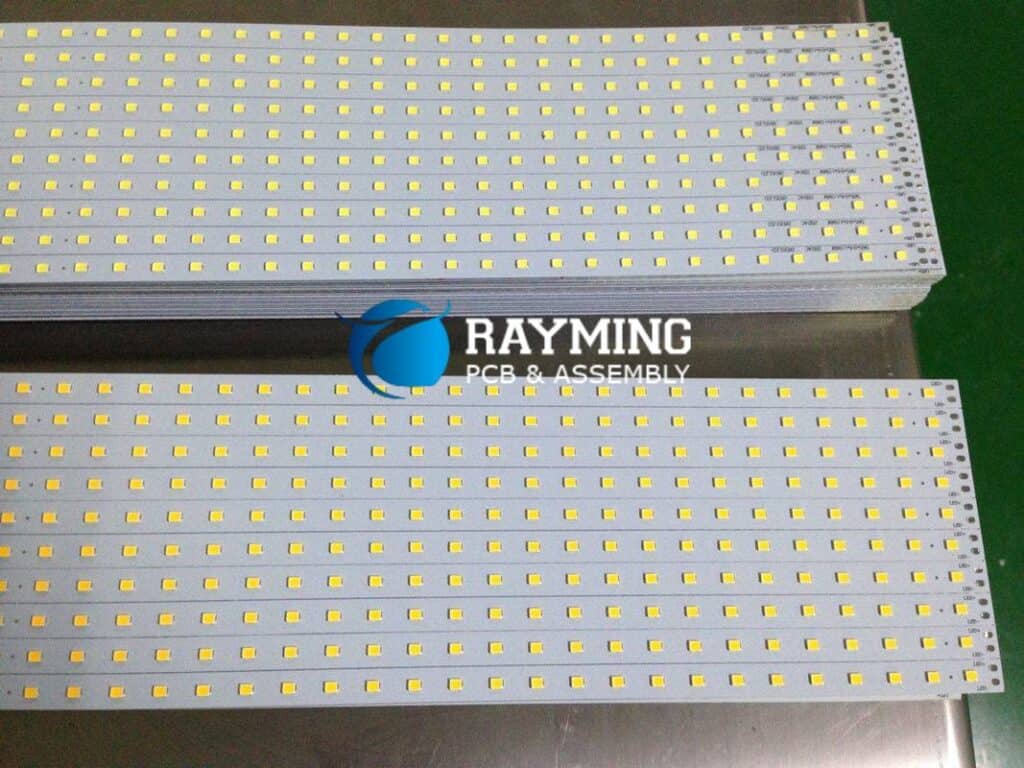
Before we dive into the DIY PCB fabrication process, it’s crucial to understand the fundamentals of PCBs.
What is a PCB?
A Printed Circuit Board (PCB) is a non-conductive substrate, typically made of fiberglass or phenolic resin, onto which conductive copper tracks and pads are etched or printed. These tracks and pads serve as the interconnections for various electronic components, such as integrated circuits (ICs), resistors, capacitors, and other discrete components. PCBs provide a sturdy and reliable platform for mounting and interconnecting electronic components, ensuring proper functionality and signal integrity.
Types of PCBs
There are several types of PCBs, each designed for specific applications and requirements. Here are some common types:
- Single-sided PCBs: These are the simplest type of PCBs, with copper traces and pads etched on one side of the substrate.
- Double-sided PCBs: These PCBs have copper traces and pads etched on both sides of the substrate, allowing for more complex designs and higher component density.
- Multi-layer PCBs: These PCBs consist of multiple layers of copper traces sandwiched between insulating layers, providing even higher component density and better signal integrity for complex designs.
For DIY PCB fabrication at home, we will primarily focus on single-sided and double-sided PCBs, as they are relatively simpler to fabricate and suitable for most hobbyist and educational projects.
DIY PCB Fabrication Techniques
There are several techniques available for DIY PCB fabrication, each with its own advantages and limitations. In this section, we will explore some of the most popular and accessible methods for creating PCBs at home.
Toner Transfer Method
The toner transfer method, also known as the toner transfer process or toner transfer technique, is one of the most widely used and cost-effective methods for DIY PCB fabrication. This method utilizes a laser printer or photocopier to transfer the PCB design onto a copper-clad board, which is then etched to create the desired circuit pattern.
Materials and Tools Required
- Laser printer or photocopier
- Glossy magazine paper or transparencies
- Copper-clad board (single-sided or double-sided)
- Etchant solution (e.g., ferric chloride, ammonium persulfate, or cupric chloride)
- Etching tank or container
- Protective gear (gloves, goggles, and apron)
- Drill and drill bits
- Permanent marker or pen
- Scissors or utility knife
- Sandpaper or steel wool
Step-by-Step Process
- Design the PCB: Use a PCB design software or create the circuit schematic and layout using a vector graphics program like Adobe Illustrator or Inkscape.
- Print the design: Print the PCB design onto a glossy magazine paper or transparency using a laser printer or photocopier. Ensure that the design is mirrored if working with a single-sided PCB.
- Prepare the copper-clad board: Clean the copper-clad board with sandpaper or steel wool to remove any oxidation or contaminants.
- Transfer the design: Place the printed design (toner side down) onto the copper-clad board and apply heat and pressure using a hot iron or laminator. The toner will transfer onto the copper surface.
- Etch the board: Immerse the board in an etchant solution, such as ferric chloride or ammonium persulfate, to remove the unwanted copper areas. Agitate the solution periodically to ensure even etching.
- Remove the toner: Once the etching process is complete, remove the remaining toner from the board using a suitable solvent or abrasive pad.
- Drill holes: Use a drill and appropriate drill bits to create holes for component leads and mounting points.
- Finish and test: Clean the board, add solder masks or component labels if desired, and test the PCB for proper functionality.
UV Exposure Method
The UV exposure method is another popular technique for DIY PCB fabrication. This method involves using a UV-sensitive photoresist to create the circuit pattern on the copper-clad board, which is then etched to remove the unwanted copper areas.
Materials and Tools Required
- UV-sensitive photoresist (e.g., dry film or liquid photoresist)
- UV exposure unit or sunlight
- Transparency film or photomask
- Copper-clad board (single-sided or double-sided)
- Etchant solution (e.g., ferric chloride, ammonium persulfate, or cupric chloride)
- Etching tank or container
- Protective gear (gloves, goggles, and apron)
- Drill and drill bits
- Permanent marker or pen
- Scissors or utility knife
- Sandpaper or steel wool
Step-by-Step Process
- Design the PCB: Use a PCB design software or create the circuit schematic and layout using a vector graphics program like Adobe Illustrator or Inkscape.
- Print the design: Print the PCB design onto a transparency film or create a photomask using a graphic arts service.
- Prepare the copper-clad board: Clean the copper-clad board with sandpaper or steel wool to remove any oxidation or contaminants.
- Apply the photoresist: Apply the UV-sensitive photoresist to the copper-clad board, following the manufacturer’s instructions.
- Expose the board: Place the transparency film or photomask onto the photoresist-coated board and expose it to UV light using a UV exposure unit or sunlight.
- Develop the photoresist: Develop the exposed photoresist by immersing the board in a developer solution, following the manufacturer’s instructions.
- Etch the board: Immerse the board in an etchant solution, such as ferric chloride or ammonium persulfate, to remove the unwanted copper areas. Agitate the solution periodically to ensure even etching.
- Remove the photoresist: Once the etching process is complete, remove the remaining photoresist from the board using a suitable solvent or stripper.
- Drill holes: Use a drill and appropriate drill bits to create holes for component leads and mounting points.
- Finish and test: Clean the board, add solder masks or component labels if desired, and test the PCB for proper functionality.
CNC Milling Method
The CNC (Computer Numerical Control) milling method is a more advanced and precise technique for DIY PCB fabrication. This method utilizes a CNC milling machine to physically remove the unwanted copper areas from the copper-clad board, creating the desired circuit pattern.
Materials and Tools Required
- CNC milling machine (e.g., desktop CNC mill or CNC router)
- Copper-clad board (single-sided or double-sided)
- Engraving bits or milling tools
- CAM (Computer-Aided Manufacturing) software
- Protective gear (gloves, goggles, and apron)
- Drill and drill bits
- Permanent marker or pen
- Sandpaper or steel wool
Step-by-Step Process
- Design the PCB: Use a PCB design software or create the circuit schematic and layout using a vector graphics program like Adobe Illustrator or Inkscape.
- Convert the design: Convert the PCB design into a format compatible with the CAM software used to control the CNC milling machine.
- Prepare the copper-clad board: Clean the copper-clad board with sandpaper or steel wool to remove any oxidation or contaminants.
- Set up the CNC milling machine: Securely clamp the copper-clad board onto the CNC milling machine’s work area and configure the machine settings according to the manufacturer’s instructions.
- Mill the board: Load the PCB design into the CAM software and initiate the milling process. The CNC milling machine will precisely remove the unwanted copper areas, creating the desired circuit pattern.
- Clean the board: Once the milling process is complete, remove any debris or residue from the board using compressed air or a soft brush.
- Drill holes: Use a drill and appropriate drill bits to create holes for component leads and mounting points.
- Finish and test: Clean the board, add solder masks or component labels if desired, and test the PCB for proper functionality.
Additional Considerations
Solder Masks and Component Labels
After creating the PCB, you may want to apply a solder mask to protect the copper traces and pads from oxidation and accidental short circuits. Solder masks are thin layers of insulating material applied over the copper areas, leaving the pads and vias exposed for component soldering.
Additionally, you can add component labels or silk-screen markings to the PCB to facilitate easy identification and assembly of components. These labels can be created using specialized inks or dry transfer films, or even by carefully etching away the copper in specific areas.
Surface Finishing
Depending on your project requirements and personal preferences, you may consider applying various surface finishes to your DIY PCBs. Some common surface finishes include:
- Tin plating: Provides a protective layer against oxidation and improves solderability.
- Gold plating: Offers superior corrosion resistance and low electrical resistance, but is more expensive.
- Immersion silver: Provides a cost-effective alternative to gold plating for surface finishes.
Vias and Plated Through-Holes
For double-sided PCBs or multi-layer designs, vias (plated or non-plated) and plated through-holes are essential for establishing electrical connections between different layers. While creating vias and plated through-holes at home can be challenging, some advanced DIY techniques, such as electroplating or conductive epoxy filling, are available for experienced makers.
Enclosures and Housings
Once your DIY PCB is complete, you may want to consider enclosures or housings to protect the circuit and components from environmental factors and physical damage. Various materials, such as plastic, metal, or 3D-printed enclosures, can be used to create custom housings for your DIY PCB projects.
FAQ (Frequently Asked Questions)
- Q: Can I create multi-layer PCBs at home? A: While it is possible to create multi-layer PCBs at home, the process is significantly more complex and requires specialized tools and techniques. For most DIY projects, single-sided or double-sided PCBs are more practical and achievable.
- Q: How long does the etching process take? A: The etching time can vary depending on the etchant solution used, the copper thickness, and the temperature. Generally, the etching process can take anywhere from 15 minutes to several hours. It’s important to monitor the etching process and agitate the solution periodically to ensure even etching.
- Q: Can I reuse the etchant solution? A: Yes, you can reuse the etchant solution multiple times until it becomes saturated or loses its effectiveness. However, it’s important to store the solution properly and filter out any debris or contaminants before reuse.
- Q: What are the safety precautions I should take during DIY PCB fabrication? A: Safety should be a top priority when working with chemicals and tools. Always wear appropriate protective gear, such as gloves, goggles, and an apron. Work in a well-ventilated area and follow the manufacturer’s instructions and safety guidelines for handling etchants and other chemicals. Additionally, ensure proper disposal of waste materials according to local regulations.
- Q: Can I create PCBs with curved or irregular shapes using DIY methods? A: While most DIY PCB fabrication techniques are designed for creating rectangular or simple shapes, it is possible to create curved or irregular shapes using methods like CNC milling or manual cutting and etching. However, these techniques may require additional skill and effort.
Conclusion
DIY PCB fabrication is an exciting and rewarding endeavor for hobbyists, makers, and electronics enthusiasts. By following the techniques outlined in this guide, you can create custom PCBs for your projects, allowing you to bring your electronic designs to life. Whether you choose the toner transfer method, UV exposure method, or CNC milling method, each approach offers its unique advantages and challenges.
Remember to prioritize safety, follow instructions carefully, and have patience as you hone your PCB fabrication skills. With practice and experimentation, you can unlock the full potential of DIY PCB fabrication and unleash your creativity in the world of electronics. Happy making!
0 Comments