Printed circuit board (PCB) stencils are thin metal sheets used to apply solder paste accurately onto a PCB during the surface mount assembly process. But with stencils ranging anywhere from $50 to $300+ depending on size and quality, builders making only a few boards may balk at the cost.
A common question asked: Can I reuse PCB stencils to save money?
The short answer is yes – stencils can often be reused 5, 10, or even 25+ times before quality degrades. But there are also many factors impacting exactly how many solid prints you’ll get before things like fine features start to suffer.
This guide provides a deep dive on maximizing reusable stencil longevity through materials choice, handling/storage methods, understencil cleaning techniques, and when to finally retire an aging sheet of laser cut steel.
What Makes a Stencil Degrade Over Time?
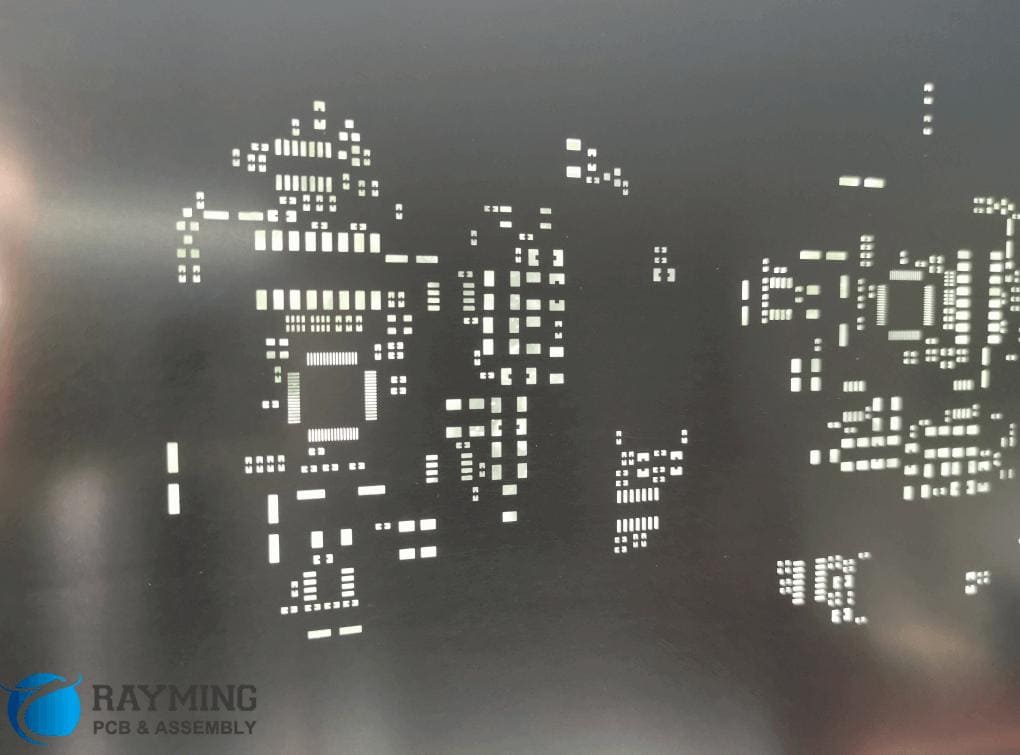
Before examining how to extend usable life, what actually causes stencils to degrade with repeated use? The primary effects slowly building up are:
Warping – Thin steel can warp slightly over time from repeated heating, pressure, and handling. This alters print transfer consistency across the board surface.
Aperture Deformation – Fine stencil features like 0.3mm apertures slowly deform from constant scraping, pressure, and abrasion. This reduces print accuracy.
Particle Buildup – PCB fibers, hardened solder, and other debris gets trapped and slowly clogs apertures/surfaces. This impacts print quality and consistency.
Oxidation/Corrosion – Solder and cleaning chemicals can slowly oxidize or corrode laser cut steel affecting surface properties critical for paste release.
With an awareness of what causes degradation, we can now examine specific methods for reducing these effects to prolong stencil reusability.
Key Factors That Impact Reusable Life Expectancy
Reusable stencil life varies substantially depending on these core factors:
Stencil Thickness/Material
Thicker steel is inherently stronger and more durable through repeated use compared to thinner and more flexible laser cut sheets. Common thicknesses are:
- 3+ mil (75+ microns) – Very durable for many reuses
- 2 mil (50 microns) – Decent strength with some flexibility
- 1 mil (25 microns) – Flexible but faster degradation
Stainless steel offers moderately improved corrosion resistance over plain carbon steel. However, properties only delay degradation rather than prevent it long term.
Stencil Design Complexity
How small and dense are the paste print features? Stencils with primarily large solder pads last far longer than those with intricate 0201 component pads, fine pitch ICs, and a dense component population. Even durable thick steel shows faster breakdown with highly complex layouts.
As component PCBs grow ever more intricate, associated stencils become more consumable too.
Handling Care
Rigorous attention to careful handling reduces deformation:
- Use edge handling frames at all times
- Avoid touching or stacking sheet surfaces
- Keep supported flat to prevent bending
- Gently clean residues after each application
It’s shocking how quickly a carelessly grabbed unframed piece of 3 mil steel will warp permanently out of shape. Treat every use with kid gloves!
Cleaning Process
While cleaning is mandatory for good printable life, improper cleaning conversely accelerates degradation too through aperture and surface damage. We’ll examine optimal cleaning methodology shortly.
Storage Conditions
Environmental factors lead to reduced stencil durability and usable life:
- Humidity causes oxidation even in storage
- Heat exposure accelerates warping
- Stack pressure can crush fine features
- Contaminants rub features even before next use
Store used stencils carefully just like original shipment:
- Sealed moisture barrier bag
- Rigid frame support
- Cleaned residue-free surface
- Flat packed if possible
- Controlled climate if available
Now let’s drill down on methods to get the most service life possible from a reusable PCB stencil.
Step 1: Select an Optimally Durable Laser Cut Steel
If planning to reuse rather than single-use disposal, invest upfront in quality durable materials. 3 mil/75 micron stainless steel is the gold standard – built to last for dozens of careful repeat applications.
Next best is 2 mil/50 micron stainless – still respectable strength with some cost savings. Mix of print accuracy vs affordable replacement timing.
At 1 mil/25 microns acceptable print quality degrades noticeably faster regardless of handling precautions. Only advisable for very simple paste designs without micro components – and still replaced more frequently.
For low volume hobby board assembly with intricate surface mount parts, it’s worth paying a bit more upfront for durable stencil steel that will pay back over numerous maintenance-free repeats.
Step 2: Handle With Care From First Use Onward
The key to getting maximum life from a reusable stencil begins even before its first paste application! Careful handling is essential from initial removal from packaging through all repeats:
Always Edge Handle
- Only manipulate the stencil by firmly gripping dedicated handling edges
- Never touch or move the thin sheet area itself
- This prevents oils and accidental bending/warping
Avoid Surface Contact
- Never allow sheet surfaces to contact other objects
- Prevent pressure, abrasions, dents, and residues
- Incidental contact rapidly degrades fine features
Keep Well Supported
- Do not allow stencils to hang or bend by gravity
- Keep fully backed flat always
- Warping is permanent damage!
Use Storage Frame
- Place back into handling frame after every single use
- Provides rigidity, avoids bending, protects aperture condition
It only takes one casual handling mistake to quickly accelerate irreversible deterioration – remain vigilant!
Step 3: Understencil Clean During Each Use Cycle
The single most important contributor to maximizing reusable life is consistent professional understencil cleaning after every solder paste application.
This prevents residue buildup that impairs printing and degrades delicate stencil features. Properly done it both maintains quality for more repeats AND prepares the surface for longest possible storage between uses.
Employ a Solvent-Soaked Wiper System
Don’t just haphazardly wipe the stencil’s underside! Follow an engineered solvent cleaning process:
Wiper Material – Low-lint proprietary material designed for stencil cleaning without causing abrasion
Solvent Type – Specialized solution like 99% isopropyl alcohol (IPA) able to cut dried solder paste residues
Container – Purpose-made enclosure frames the wiper area and contains sufficient solvent volume to prevent evaporation
Mounting – The wiper fits precisely under the supported stencil area to make controlled contact during pulls
A professional understencil cleaning system makes residue removal safe, effective, and predictable during the production run. No guessing or winging it!
Methodical Multidirectional Wiper Passes
With the custom cleaning rig set up, systematically make multiple gentle passes across the entire stencil:
- Make an initial gentle pull pass left-to-right with wiper slightly moistened with solvent
- Saturate wiper fully with additional solvent
- Make gentler pull pass right-to-left
- Repeat passes in opposite directions applying minimal pressure
- Check for visual residues and carefully repeat as necessary
Take your time and allow the solvent-soaked wiper system to do the work rather than forcing or abrasively scrubbing!
Post Cleaning Inspection
After the final cleaning pass, carefully examine both sides of stencil with bright angled lighting. Any remaining solder particles or obscured apertures mandate additional targeted cleaning.
Don’t skip inspection before wrapping up print and storage steps!
Step 4: Safe Transport and Optimized Storage
Once the complex stencil is all cleaned up after a paste transfer, don’t casually toss it around! We need just as much care (or even more) for storage as during active use:
Handle Protected – Always keep within dedicated frame systems while moving to prevent any physical contacts or bending.
Store Moisture-Free – Residual cleaning solvents and humidity itself degrade laser cut edges over time. Seal thoroughly in desiccant bag or container.
Rest Totally Flat – Any warping from uneven pressure during storage quickly compounds over repeated use. Utilize stiff backing sheets.
Control Environment – Regulate temperature and humidity for long term preserved quality if equipment allows.
Monitor Over Time – Do quick visual inspections while sealed during longer term storage for any progressive damage.
The goal is a pristine “time capsule” condition ready for the next PCB production day!
Step 5: Know When It’s Time to Replace a Well-Worn Stencil
With rigorous care and cleaning, a high quality durable stencil may last for dozens of repetitions over years of service life. But what are the warning signs it’s time for retirement from active duty?
Apertures Show Visible Wear
The most common end-of-life indicator is when small or fine pitch paste apertures exhibit:
- Enlarged openings
- Deformed non-circular shape
- Visibly roughened hole edges
This prevents adequate paste deposition control.
Warping Impacts Release
While stored flat, warping may appear over time from repeated heating cycles. This causes uneven paste transfer across the PCB surface as clearance varies.
Print Failures Increase
If everything is maintained perfectly, stencils eventually physically wear out! Declining print performance despite best practices means it’s served nobly to the end.
When failure rate exceeds cost of replacement, or design demands higher precision, it’s finally time to retire that durable steel veteran.
Frequently Asked Questions
Here are answers to some of the most common questions around reusing PCB solder stencils multiple times.<details> <summary>Can I reuse disposable laser cut stencils meant for one-time use?</summary>
Generally no – they degrade immediately with mishandling or cleaning attempts. Ultra thin “disposable” steel warp and tear easily. Damage causes paste clumping, bridging, etc. Stick to purpose-made reusable designs if planning multiple runs.</details> <details> <summary>How many reuses can I realistically expect?</summary>
Depends highly on materials, design complexity, handling care, and maintenance quality each step. With premium steel and gentle treatment maybe 25-50+ uses. More intricate layouts exhaust reusable life faster regardless. Set expectations accordingly!</details> <details> <summary>Can I clean and reuse plastic stencils too?</summary>
Only use plastics for true single-use applications – they cannot withstand any solvents or abrasion required to remove dried solder paste effectively. Disposable plastics clog up fast with minimal cleaning latitude before falling apart. Go metal if repeating!</details> <details> <summary>What types of cleaners or solvents work best?</summary>
Specialized solder paste removers like 99% medical grade isopropyl alcohol strike the right balance of residue dissolution without attacking steel. Never use acetone, excessive temperatures, or ultrasonic baths – extremely destructive to delicate stencils!</details> <details> <summary>How do I store a used stencil long term?</summary>
Keep in an airtight desiccant bag or container to exclude humidity/oxidation, insert within a rigid frame to prevent bending, rest flat on very smooth surface to avoid damaging apertures or fine features, inspect visually before re-use after long inactive periods.</details>
So in summary – yes, quality steel PCB stencils designed for multiple uses can reliably be reused for many production cycles assuming mindful handling, cleaning, and storage methodology. Plan ahead with initial purchase and process investment to maximize longevity!
Conclusion
Getting the most cycles possible out of durable reusable PCB solder stencils involves care and maintenance at each step:
- Select quality materials able to withstand repeated use without rapid physical breakdown
- Handle delicately and prevent incidental contact, bending, or residue contamination
- Utilize professional understencil cleaning regiment for controlled residue removal
- Transport and store just as carefully as during active paste printing
- Retire when aperture condition or print performance eventually degrade
With prudence maximizing the usable lifespan, the initial stencil cost gets amortized over drastically more applications – saving time and money while maintaining print quality!
Now shift focus to that new board design that can leverage this repeatable process…let the solder printing commence!
0 Comments