Visual Inspection
Visual inspection is the first and most basic aspect of OQC. It involves checking the product for any visible defects or inconsistencies. Some of the things to look for during visual inspection include:
Surface Defects
Surface defects are any imperfections on the surface of the product, such as scratches, dents, or discoloration. These defects can affect the appearance and functionality of the product and should be identified and corrected before shipping.
Dimensional Accuracy
Dimensional accuracy refers to the product’s adherence to the specified dimensions and tolerances. This is important because products that are too large or too small may not fit properly or function as intended.
Assembly and Packaging
Assembly and packaging are also important aspects of visual inspection. The product should be assembled correctly and packaged securely to prevent damage during shipping.
Functional Testing
Functional testing involves testing the product to ensure that it functions as intended. This may involve testing the product’s electrical, mechanical, or software components. Some of the things to look for during functional testing include:
Electrical Testing
Electrical testing involves testing the product’s electrical components to ensure that they are functioning properly. This may involve testing the product’s power supply, circuitry, and other electrical components.
Mechanical Testing
Mechanical testing involves testing the product’s mechanical components to ensure that they are functioning properly. This may involve testing the product’s moving parts, such as gears or motors, to ensure that they are operating smoothly and efficiently.
Software Testing
Software testing involves testing the product’s software components to ensure that they are functioning properly. This may involve testing the product’s user interface, data processing, and other software functions.
Performance Testing
Performance testing involves testing the product’s performance under various conditions to ensure that it meets the required specifications. Some of the things to look for during performance testing include:
Durability Testing
Durability testing involves testing the product’s ability to withstand normal wear and tear over time. This may involve subjecting the product to various environmental conditions, such as extreme temperatures or humidity, to ensure that it can withstand these conditions without failing.
Reliability Testing
Reliability testing involves testing the product’s ability to perform consistently over time. This may involve testing the product’s performance under various load conditions or for extended periods of time to ensure that it can perform reliably.
Efficiency Testing
Efficiency testing involves testing the product’s ability to perform its intended function with minimal waste or energy consumption. This may involve testing the product’s power consumption, heat generation, or other efficiency metrics.
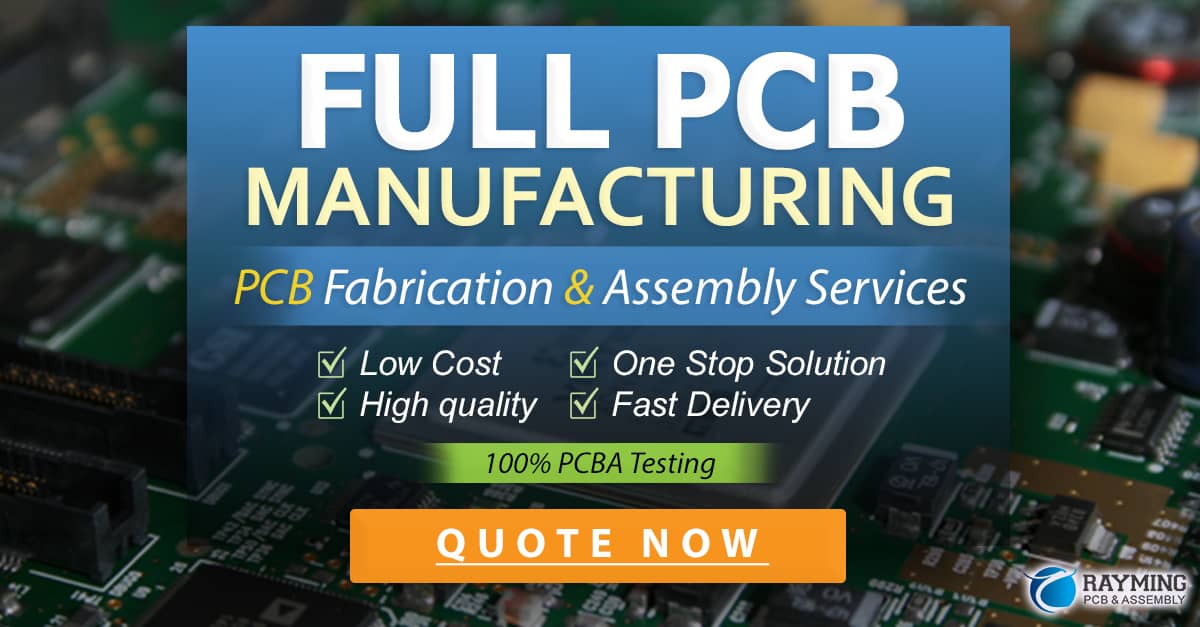
Safety Testing
Safety testing involves testing the product to ensure that it is safe for use by consumers. This may involve testing the product’s compliance with various safety standards and regulations. Some of the things to look for during safety testing include:
Electrical Safety
Electrical safety testing involves testing the product’s electrical components to ensure that they are safe for use. This may involve testing the product’s insulation, grounding, and other electrical safety features.
Mechanical Safety
Mechanical safety testing involves testing the product’s mechanical components to ensure that they are safe for use. This may involve testing the product’s guards, interlocks, and other mechanical safety features.
Chemical Safety
Chemical safety testing involves testing the product’s materials and components to ensure that they are safe for use. This may involve testing the product for the presence of hazardous substances, such as lead or mercury, or for compliance with various chemical safety regulations.
Compliance Testing
Compliance testing involves testing the product to ensure that it complies with various industry standards and regulations. This may involve testing the product’s compliance with environmental regulations, such as RoHS or REACH, or with product safety standards, such as UL or CE. Some of the things to look for during compliance testing include:
Environmental Compliance
Environmental compliance testing involves testing the product to ensure that it complies with various environmental regulations. This may involve testing the product for the presence of hazardous substances or for compliance with waste disposal regulations.
Product Safety Compliance
Product safety compliance testing involves testing the product to ensure that it complies with various product safety standards. This may involve testing the product’s compliance with electrical safety standards, such as UL or CE, or with mechanical safety standards, such as ANSI or ISO.
Documentation and Reporting
Documentation and reporting are important aspects of OQC that ensure that the results of the inspection are properly recorded and communicated. Some of the things to look for in documentation and reporting include:
Inspection Reports
Inspection reports should be detailed and accurate, including information such as the product name, batch number, inspection date, and results of each aspect of the inspection. The report should also include any defects or non-conformances found during the inspection and the corrective actions taken.
Traceability
Traceability is important in OQC to ensure that any defects or non-conformances can be traced back to their source. This may involve marking the product with a unique identifier, such as a serial number or batch code, or maintaining records of the materials and components used in the product.
Communication
Communication is important in OQC to ensure that all relevant parties are informed of the results of the inspection. This may involve communicating with the production team to address any defects or non-conformances found during the inspection or with the customer to provide them with the inspection report and any necessary documentation.
Frequently Asked Questions (FAQ)
What is Outgoing Quality Control (OQC)?
Outgoing Quality Control (OQC) is the process of inspecting and testing products before they are shipped to customers to ensure that they meet the required specifications and standards.
Why is OQC important?
OQC is important because it helps to ensure that products are of the highest quality before they are shipped to customers. This can help to reduce the risk of customer complaints, returns, and recalls, and can help to improve customer satisfaction and loyalty.
What are some of the key aspects of OQC?
Some of the key aspects of OQC include visual inspection, functional testing, performance testing, safety testing, compliance testing, and documentation and reporting.
What should be included in an OQC inspection report?
An OQC inspection report should include detailed and accurate information about the product, including the product name, batch number, inspection date, and results of each aspect of the inspection. The report should also include any defects or non-conformances found during the inspection and the corrective actions taken.
How can I ensure that my products pass OQC?
To ensure that your products pass OQC, it is important to have a strong quality management system in place that includes regular inspections and testing throughout the production process. It is also important to work closely with your suppliers to ensure that they are providing high-quality materials and components and to have a clear understanding of the required specifications and standards for your products.
Conclusion
Outgoing Quality Control (OQC) is a critical process in manufacturing that helps to ensure that products are of the highest quality before they are shipped to customers. By checking various aspects of the product, including visual inspection, functional testing, performance testing, safety testing, compliance testing, and documentation and reporting, manufacturers can reduce the risk of customer complaints, returns, and recalls, and can improve customer satisfaction and loyalty.
To ensure that your products pass OQC, it is important to have a strong quality management system in place that includes regular inspections and testing throughout the production process. By working closely with your suppliers and having a clear understanding of the required specifications and standards for your products, you can help to ensure that your products are of the highest quality and meet the needs and expectations of your customers.
0 Comments