What is PCB Silkscreen?
PCB silkscreen, also known as legend or nomenclature, is the text and symbols printed on the surface of a printed circuit board (PCB) for identification and assembly purposes. The silkscreen layer provides essential information about component placement, orientation, and reference designators, making it easier for manufacturers and engineers to assemble and troubleshoot the PCB.
Common Elements Found on PCB Silkscreen
- Component reference designators (e.g., R1, C2, U3)
- Polarity indicators for polarized components (e.g., + sign for capacitors, diodes)
- Test points and probe locations
- Company logos and product branding
- Revision numbers and date codes
- Warning symbols and safety information
- Fiducial marks for automated assembly
Importance of PCB Silkscreen
Assists in PCB Assembly
The primary purpose of PCB silkscreen is to guide the assembly process. The printed information helps manufacturers and assembly technicians correctly place and orient components on the board. This is particularly important for surface-mount devices (SMDs), which can be small and difficult to handle without clear markings.
Facilitates Troubleshooting and Repair
When a PCB malfunctions, the silkscreen layer provides valuable information for troubleshooting and repair. Technicians can quickly identify components and test points using the reference designators and symbols printed on the board. This speeds up the debugging process and reduces the likelihood of errors during repair.
Enhances Communication
PCB silkscreen serves as a visual communication tool between PCB designers, manufacturers, and end-users. By including relevant information such as company logos, product names, and revision numbers, silkscreen helps ensure that all parties are working with the correct version of the PCB and minimizes the risk of confusion or miscommunication.
Design Considerations for PCB Silkscreen
Legibility
One of the most important aspects of PCB silkscreen design is legibility. The text and symbols must be clearly visible and easy to read, even under low-light conditions or when the PCB is populated with components. To ensure legibility:
- Use a clean, simple font (e.g., Arial, Helvetica)
- Maintain adequate font size (typically 0.8mm or larger)
- Provide sufficient contrast between the silkscreen and the PCB substrate
- Avoid placing silkscreen over pads or other conductive areas
Placement
Proper placement of silkscreen elements is crucial for both aesthetics and functionality. When designing the silkscreen layer, consider the following:
- Position reference designators close to their corresponding components
- Ensure that polarity indicators are clearly visible and unobstructed
- Align text and symbols with the component orientation
- Keep silkscreen elements away from the board edges and mounting holes
- Avoid overlapping silkscreen with other layers (e.g., solder mask, copper)
Compliance with Standards
PCB silkscreen must comply with various industry standards and regulations, such as:
- IPC-A-600: Acceptability of Printed Boards
- IPC-7351: Generic Requirements for Surface Mount Design and Land Pattern Standard
- UL (Underwriters Laboratories) standards for safety-critical applications
- RoHS (Restriction of Hazardous Substances) directive for environmental compliance
Adhering to these standards ensures that the PCB silkscreen meets the required quality and safety criteria, and helps avoid potential issues during manufacturing or end-use.
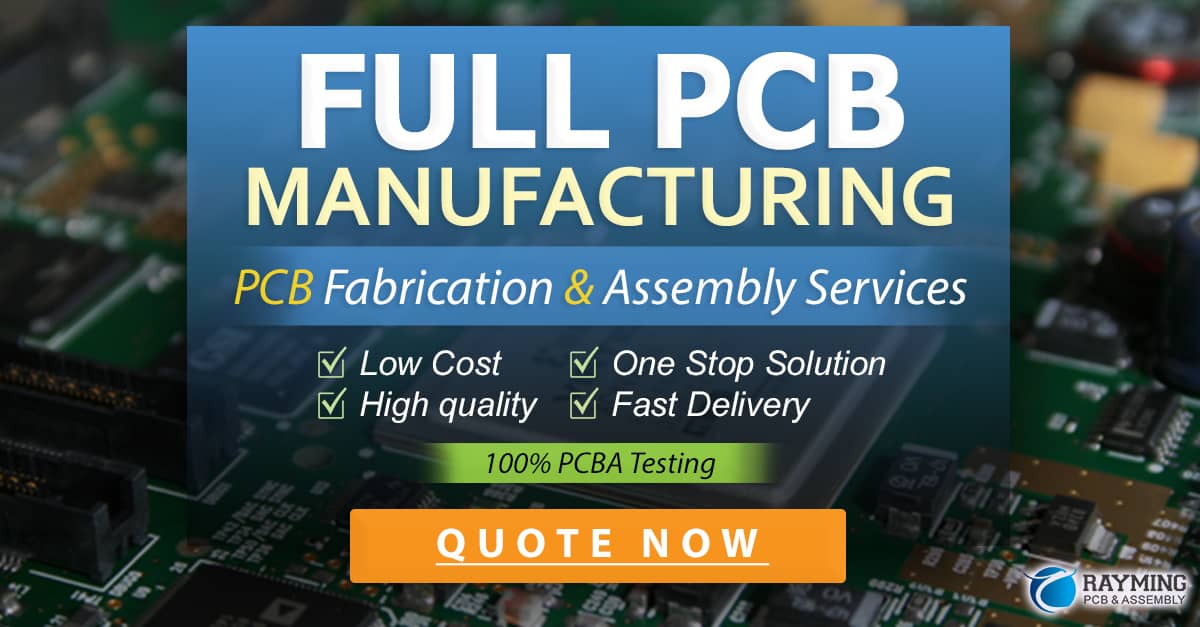
Common Pitfalls in PCB Silkscreen Design
Overcrowding
One of the most common mistakes in PCB silkscreen design is overcrowding the board with too much information. While it may be tempting to include as much detail as possible, an overcrowded silkscreen can lead to reduced legibility and confusion during assembly. To avoid this issue:
- Prioritize essential information (e.g., reference designators, polarity indicators)
- Use abbreviations or shorthand where appropriate
- Consider using a separate assembly drawing for additional details
Incorrect Polarity Indicators
Incorrect or missing polarity indicators can lead to component damage or PCB malfunction. Double-check the polarity of all components and ensure that the silkscreen accurately reflects their orientation. Pay special attention to polarized components such as electrolytic capacitors, diodes, and transistors.
Inconsistent Formatting
Inconsistent formatting of text and symbols can make the PCB silkscreen difficult to read and interpret. To maintain consistency:
- Use the same font, size, and style throughout the design
- Align text and symbols consistently (e.g., left-justified, centered)
- Maintain uniform spacing between elements
Silkscreen Over Conductive Areas
Placing silkscreen over conductive areas, such as pads or traces, can lead to manufacturing issues and potential short circuits. Always ensure that the silkscreen layer does not overlap with any conductive areas on the PCB. Use your PCB design software’s layer visibility and design rule check (DRC) features to verify proper clearance.
Best Practices for PCB Silkscreen Design
Keep It Simple
A clean and simple silkscreen design is often the most effective. Focus on including only the essential information needed for assembly and troubleshooting, and avoid cluttering the board with unnecessary details. A minimalist approach not only improves legibility but also streamlines the manufacturing process.
Use Consistent Naming Conventions
Develop and adhere to a consistent naming convention for reference designators and other silkscreen elements. This helps ensure clarity and reduces the risk of confusion during assembly and troubleshooting. Some common naming conventions include:
- R for resistors (e.g., R1, R2)
- C for capacitors (e.g., C1, C2)
- U for integrated circuits (e.g., U1, U2)
- D for diodes (e.g., D1, D2)
- Q for transistors (e.g., Q1, Q2)
Collaborate with Manufacturers
Work closely with your PCB manufacturer to ensure that your silkscreen design is compatible with their processes and equipment. Discuss any specific requirements or limitations they may have, such as minimum font sizes or clearance requirements. Collaborating with your manufacturer early in the design process can help prevent issues and delays during production.
Conduct Thorough Reviews
Before finalizing your PCB silkscreen design, conduct thorough reviews to catch any errors or inconsistencies. Have multiple team members review the design, including engineers, manufacturers, and end-users, to ensure that the silkscreen meets all requirements and is easy to understand. Use design review checklists to systematically verify each aspect of the silkscreen layer.
FAQ
1. What is the recommended font size for PCB silkscreen?
The recommended font size for PCB silkscreen is typically 0.8mm or larger to ensure legibility. However, the specific font size may vary depending on the PCB manufacturer’s capabilities and the available space on the board. Always consult with your manufacturer to determine their minimum font size requirements.
2. Can I use any color for PCB silkscreen?
While white is the most common color for PCB silkscreen, other colors such as yellow or black can be used depending on the PCB substrate color and the manufacturer’s capabilities. Keep in mind that some colors may have a higher cost or longer lead time. Discuss color options with your manufacturer early in the design process.
3. How can I ensure that my PCB silkscreen complies with industry standards?
To ensure compliance with industry standards, familiarize yourself with the relevant guidelines, such as IPC-A-600, IPC-7351, and UL standards. Incorporate these requirements into your design checklist and work closely with your PCB manufacturer to verify compliance. Many PCB design software packages also include built-in design rule checks (DRCs) that help flag potential compliance issues.
4. What should I do if there isn’t enough space on the PCB for all the desired silkscreen information?
If space is limited, prioritize the most essential information, such as reference designators and polarity indicators. Consider using abbreviations or shorthand for less critical information, or create a separate assembly drawing that includes additional details. In some cases, you may need to adjust the PCB layout or component placement to accommodate the necessary silkscreen elements.
5. Can I use silkscreen on both sides of the PCB?
Yes, silkscreen can be applied to both sides of the PCB if needed. This is common for double-sided or multi-layer boards where components are placed on both sides. However, keep in mind that adding silkscreen to both sides may increase the manufacturing cost and complexity. Discuss your requirements with your PCB manufacturer to determine the most cost-effective solution.
Element | Purpose |
---|---|
Reference Designators | Unique identifiers for each component (e.g., R1, C2, U3) |
Polarity Indicators | Marks to indicate the orientation of polarized components (e.g., + sign) |
Test Points | Locations where probes can be attached for testing and debugging |
Company Logos | Branding elements to identify the PCB manufacturer or end-user |
Revision Numbers | Indicators of the PCB version or revision history |
Warning Symbols | Safety-related information, such as high-voltage warnings or ESD-sensitive devices |
Fiducial Marks | Reference points for automated assembly equipment to align the PCB |
By following these guidelines and best practices, you can create a clear, concise, and effective PCB silkscreen that enhances the manufacturing, assembly, and troubleshooting processes. A well-designed silkscreen layer not only improves the overall quality of the PCB but also helps ensure its long-term reliability and functionality.
0 Comments