Introduction to 94v0 Circuit Boards
94v0 circuit boards, also known as FR-4 circuit boards or PCBs (Printed Circuit Boards), are widely used in various electronic applications due to their excellent mechanical, electrical, and thermal properties. These boards are made from a flame-retardant material that meets the UL94V-0 standard, ensuring high resistance to fire and heat. In this article, we will explore the key features of 94v0 circuit boards, their applications, and provide a comprehensive diagram to illustrate their structure.
What is a 94v0 Circuit Board?
A 94v0 circuit board is a type of PCB that is manufactured using a flame-retardant material, typically a glass-reinforced epoxy laminate. The “94v0” designation refers to the UL (Underwriters Laboratories) flammability rating, which indicates that the material can withstand burning for up to 10 seconds without causing the flame to spread.
Composition of 94v0 Circuit Boards
94v0 circuit boards are composed of several layers:
- Copper foil: This layer is responsible for conducting electrical signals and is usually made of thin copper sheets laminated onto the board.
- Prepreg: Short for “pre-impregnated,” this layer is made of glass fiber cloth impregnated with a partially cured epoxy resin. It acts as an insulating layer between the copper foil layers.
- Core: The core is a solid, rigid material, typically made of glass-reinforced epoxy laminate, that provides structural support to the board.
- Solder mask: This layer is applied on top of the copper foil to protect it from oxidation and prevent accidental short circuits during soldering.
- Silkscreen: The silkscreen layer is used to print text, logos, and component identifiers on the board for easier assembly and troubleshooting.
Manufacturing Process of 94v0 Circuit Boards
The manufacturing process of 94v0 circuit boards involves several steps:
- Design: The Circuit Board Design is created using CAD (Computer-Aided Design) software, which generates the necessary files for manufacturing.
- Printing: The design is printed onto a photosensitive film, which is used to transfer the pattern onto the copper foil.
- Etching: The unwanted copper is removed using a chemical etching process, leaving behind the desired circuit pattern.
- Lamination: The prepreg layers and copper foil are laminated together under high pressure and temperature to form a solid board.
- Drilling: Holes are drilled into the board to accommodate components and create vias for inter-layer connections.
- Plating: The drilled holes are plated with copper to ensure electrical connectivity between layers.
- Solder masking and silkscreening: The solder mask and silkscreen layers are applied to the board.
- Surface finishing: A surface finish, such as HASL (Hot Air Solder Leveling) or ENIG (Electroless Nickel Immersion Gold), is applied to protect the exposed copper and enhance solderability.
Key Features of 94v0 Circuit Boards
Flame Retardancy
One of the most important features of 94v0 circuit boards is their flame retardancy. The UL94V-0 rating ensures that the board material can withstand high temperatures and prevent the spread of fire, making it suitable for applications where safety is a top priority.
Electrical Properties
94v0 circuit boards exhibit excellent electrical properties, including:
- High insulation resistance
- Low dielectric constant and dissipation factor
- Good high-frequency performance
These properties make 94v0 boards suitable for a wide range of electronic applications, from low-power devices to high-speed digital circuits.
Mechanical Strength
The glass-reinforced epoxy laminate used in 94v0 circuit boards provides excellent mechanical strength and dimensional stability. This ensures that the board can withstand physical stress during assembly, handling, and operation without warping or delaminating.
Thermal Stability
94v0 circuit boards have good thermal stability, allowing them to operate reliably in a wide temperature range. The Glass Transition Temperature (Tg) of the material is typically around 130°C to 140°C, ensuring that the board maintains its mechanical and electrical properties even at elevated temperatures.
Moisture Resistance
The epoxy resin used in 94v0 circuit boards provides good moisture resistance, preventing the absorption of water that can lead to degradation of the board’s properties over time. This makes 94v0 boards suitable for use in humid environments or applications where exposure to moisture is a concern.
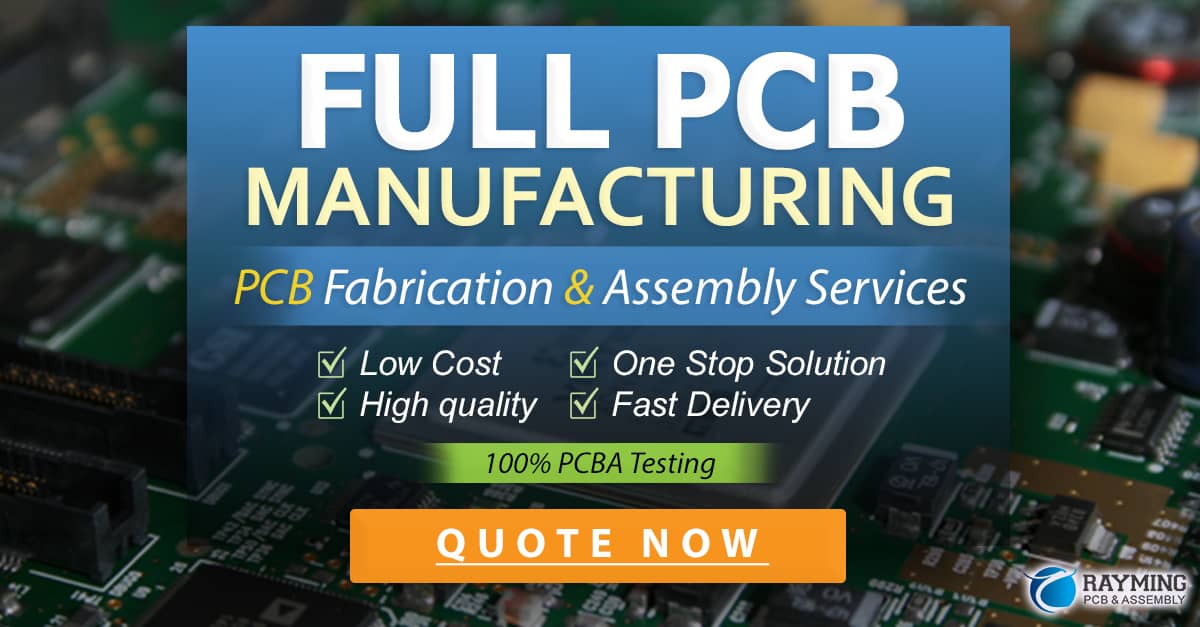
Applications of 94v0 Circuit Boards
94v0 circuit boards find applications in various industries and products, including:
- Consumer electronics: Smartphones, tablets, laptops, televisions, and home appliances.
- Automotive electronics: Engine control units, infotainment systems, and advanced driver assistance systems (ADAS).
- Industrial electronics: Process control systems, automation equipment, and power electronics.
- Medical devices: Diagnostic equipment, patient monitoring systems, and implantable devices.
- Aerospace and defense: Avionics, satellite communications, and military equipment.
- Telecommunications: Routers, switches, and base stations for wired and wireless networks.
The table below summarizes some of the key applications of 94v0 circuit boards:
Industry | Applications |
---|---|
Consumer electronics | Smartphones, tablets, laptops, TVs, home appliances |
Automotive | Engine control units, infotainment systems, ADAS |
Industrial | Process control systems, automation equipment, power electronics |
Medical | Diagnostic equipment, patient monitoring, implantable devices |
Aerospace and defense | Avionics, satellite communications, military equipment |
Telecommunications | Routers, switches, base stations |
94v0 Circuit Board Diagram
To better understand the structure of a 94v0 circuit board, let’s take a look at a typical cross-sectional diagram:
Silkscreen
|
Solder mask| Copper foil
______|_____
| Prepreg |
| ------- |
| Core |
| ------- |
| Prepreg |
|______ ____|
| Copper foil
Solder mask
In this diagram, we can see the various layers that make up a 94v0 circuit board:
- The top and bottom layers are the solder mask, which protects the copper foil from oxidation and accidental short circuits.
- Just beneath the solder mask are the copper foil layers, which carry the electrical signals.
- Between the copper foil layers are the prepreg layers, which provide insulation and bonding between the layers.
- At the center is the core, a solid, rigid material that gives the board its structural support.
- Finally, the silkscreen layer is applied on top of the solder mask to provide text, logos, and component identifiers.
This cross-sectional view illustrates the basic structure of a double-sided 94v0 circuit board. In practice, boards can have multiple layers of copper foil and prepreg, depending on the complexity of the circuit and the desired performance characteristics.
Frequently Asked Questions (FAQ)
-
What does “94v0” mean in the context of circuit boards?
“94v0” refers to the UL (Underwriters Laboratories) flammability rating of the circuit board material. It indicates that the material can withstand burning for up to 10 seconds without causing the flame to spread. -
What are the advantages of using 94v0 circuit boards?
94v0 circuit boards offer several advantages, including excellent flame retardancy, good electrical and mechanical properties, thermal stability, and moisture resistance. These properties make them suitable for a wide range of electronic applications across various industries. -
Can 94v0 circuit boards be used in high-temperature environments?
Yes, 94v0 circuit boards can operate reliably in a wide temperature range. The glass transition temperature (Tg) of the material is typically around 130°C to 140°C, ensuring that the board maintains its mechanical and electrical properties even at elevated temperatures. -
How many layers can a 94v0 circuit board have?
The number of layers in a 94v0 circuit board can vary depending on the complexity of the circuit and the desired performance characteristics. Boards can have multiple layers of copper foil and prepreg, with some high-density designs featuring 20 or more layers. -
What surface finishes are commonly used on 94v0 circuit boards?
Common surface finishes for 94v0 circuit boards include HASL (Hot Air Solder Leveling), ENIG (Electroless Nickel Immersion Gold), and OSP (Organic Solderability Preservative). These finishes protect the exposed copper and enhance the board’s solderability, ensuring reliable connections during the assembly process.
Conclusion
94v0 circuit boards are essential components in modern electronic devices, offering excellent flame retardancy, electrical and mechanical properties, thermal stability, and moisture resistance. Their versatility and reliability make them a popular choice for a wide range of applications, from consumer electronics to industrial, medical, and aerospace systems.
By understanding the key features and manufacturing process of 94v0 circuit boards, designers and engineers can make informed decisions when selecting materials and designing circuits for their specific applications. With the increasing demand for high-performance, reliable electronic devices, the importance of 94v0 circuit boards in the electronics industry is set to grow in the coming years.
0 Comments