Introduction
In today’s rapidly evolving electronics industry, Rigid-flex PCBs have become increasingly popular due to their ability to combine the benefits of both rigid and flexible circuits. These PCBs offer numerous advantages, such as reduced weight, improved reliability, and enhanced design flexibility. However, choosing the right rigid-flex PCB manufacturer is crucial to ensure the success of your project. In this article, we will discuss nine essential tips to help you select the best rigid-flex PCB manufacturer for your needs.
What is a Rigid-flex PCB?
A rigid-flex PCB is a type of printed circuit board that combines both rigid and flexible substrates. The rigid portions of the board provide structural support and house the majority of the components, while the flexible portions allow for bending and folding, enabling the PCB to fit into tight spaces or conform to unique shapes. This combination of rigidity and flexibility makes rigid-flex PCBs ideal for applications that require compact designs, high reliability, and improved signal integrity.
Advantages of Rigid-flex PCBs
- Space Savings: Rigid-flex PCBs allow for more compact designs by eliminating the need for connectors and cables between separate rigid and flexible sections.
- Improved Reliability: By reducing the number of interconnects, rigid-flex PCBs minimize the risk of connection failures and improve overall system reliability.
- Enhanced Signal Integrity: The elimination of connectors and the use of continuous traces across rigid and flexible sections result in better signal integrity and reduced electromagnetic interference (EMI).
- Increased Design Flexibility: Rigid-flex PCBs can be designed to fit into complex shapes and tight spaces, enabling greater design flexibility and miniaturization.
- Weight Reduction: The use of flexible substrates and the elimination of connectors and cables contribute to significant weight reduction in electronic assemblies.
Tip 1: Look for Experience and Expertise
When choosing a rigid-flex PCB manufacturer, it is essential to consider their experience and expertise in the field. Look for a company that has a proven track record of successfully manufacturing rigid-flex PCBs for various industries and applications. Experienced manufacturers will have the knowledge and skills necessary to handle complex designs, ensure proper material selection, and maintain high quality standards throughout the manufacturing process.
Questions to Ask:
- How long has the manufacturer been producing rigid-flex PCBs?
- What industries and applications have they served?
- Can they provide references or case studies showcasing their successful projects?
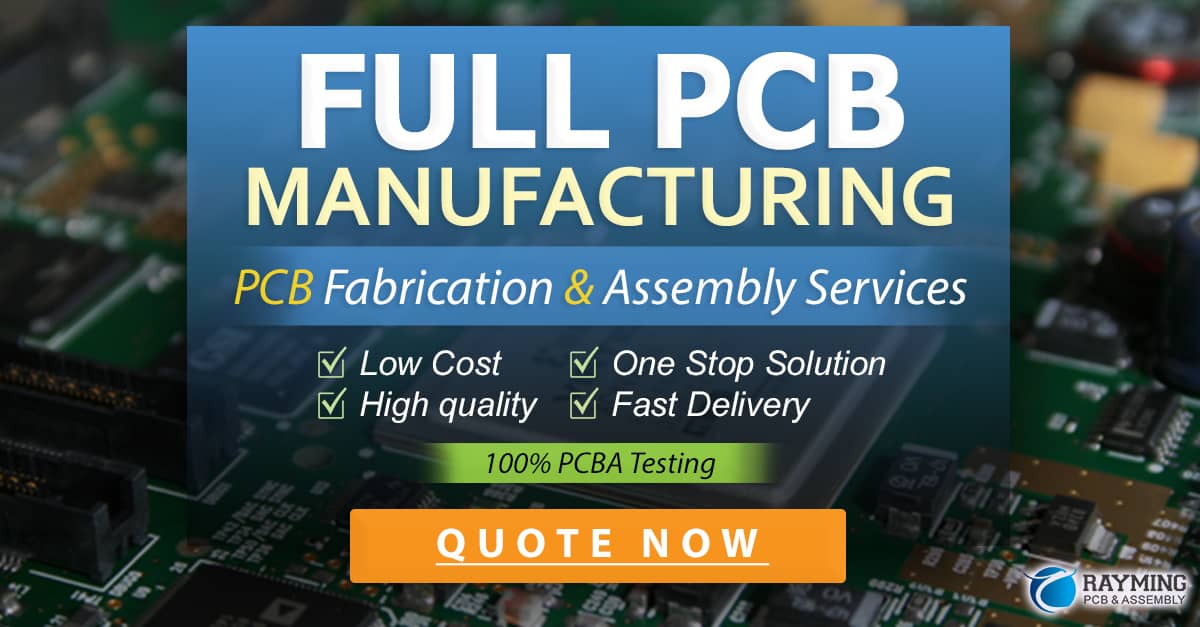
Tip 2: Evaluate Technical Capabilities
Rigid-flex PCB manufacturing requires specialized equipment and processes. When evaluating potential manufacturers, assess their technical capabilities to ensure they can meet your specific requirements. This includes their ability to handle different layer counts, material types, and feature sizes. Additionally, inquire about their design support services, such as DFM (Design for Manufacturability) analysis and prototyping, to ensure a smooth transition from design to production.
Technical Capabilities Checklist:
- Multi-layer rigid-flex PCB fabrication
- High-density interconnect (HDI) technology
- Microvias and buried vias
- Controlled impedance
- Fine-pitch component assembly
- Prototype and low-volume production
- DFM analysis and feedback
Tip 3: Assess Quality Control Measures
The reliability and performance of your rigid-flex PCBs depend heavily on the quality control measures implemented by the manufacturer. Inquire about their quality management system (QMS) and certifications, such as ISO 9001, ISO 13485 (for medical devices), or AS9100 (for aerospace and defense). A robust QMS ensures that the manufacturer adheres to strict quality standards and follows documented processes to prevent defects and ensure consistency.
Quality Control Aspects to Consider:
- QMS certifications (ISO 9001, ISO 13485, AS9100)
- Incoming material inspection
- In-process quality checks
- Final inspection and testing
- Traceability and document control
- Continuous improvement initiatives
Tip 4: Consider the Manufacturer’s Supply Chain Management
A reliable rigid-flex PCB manufacturer should have a well-established supply chain management system to ensure the timely delivery of high-quality materials and components. This is particularly important for rigid-flex PCBs, as they often require specialized materials and have strict requirements for material properties and compatibility. Assess the manufacturer’s relationships with suppliers, their inventory management practices, and their ability to handle potential supply chain disruptions.
Supply Chain Management Factors:
- Relationships with reputable material suppliers
- Material traceability and certification
- Inventory management and availability
- Lead time management
- Contingency plans for supply chain disruptions
Tip 5: Evaluate Communication and Support
Effective communication and support are essential for a successful partnership with your rigid-flex PCB manufacturer. Look for a manufacturer that is responsive, proactive, and willing to collaborate closely with your team. They should have dedicated project managers or customer support representatives who can provide regular updates, answer your questions promptly, and address any issues that may arise during the manufacturing process.
Communication and Support Aspects:
- Dedicated project managers or customer support
- Regular project updates and status reports
- Prompt response to inquiries and concerns
- Technical support and guidance
- Flexibility to accommodate design changes or revisions
Tip 6: Examine Manufacturing Capacity and Lead Times
When selecting a rigid-flex PCB manufacturer, consider their manufacturing capacity and typical lead times. This is especially important if you have high-volume production requirements or tight deadlines. Inquire about the manufacturer’s production facility size, equipment capabilities, and workforce to ensure they can handle your order volume and deliver your products on time. Additionally, ask about their lead time estimates for prototype and production runs to align with your project timeline.
Manufacturing Capacity and Lead Time Factors:
- Production facility size and equipment capabilities
- Workforce size and expertise
- Typical lead times for prototypes and production runs
- Ability to handle high-volume orders
- Flexibility to accommodate rush orders or expedited delivery
Tip 7: Review Certifications and Compliance
Depending on your industry and target markets, your rigid-flex PCBs may need to comply with various standards and regulations. When choosing a manufacturer, ensure they have the necessary certifications and compliance measures in place. This may include certifications such as UL, RoHS, REACH, and IPC standards. A manufacturer with the appropriate certifications demonstrates their commitment to quality, safety, and environmental responsibility.
Certifications and Compliance Checklist:
- UL certification
- RoHS compliance
- REACH compliance
- IPC standards (IPC-6013, IPC-6018)
- Industry-specific certifications (e.g., medical, automotive, aerospace)
Tip 8: Consider the Manufacturer’s Location and Logistics
The location of your rigid-flex PCB manufacturer can have a significant impact on lead times, shipping costs, and communication. Consider whether a local, domestic, or offshore manufacturer best suits your needs. Local manufacturers may offer faster turnaround times and easier communication, while offshore manufacturers may provide cost savings. Evaluate the manufacturer’s shipping and logistics capabilities to ensure they can deliver your products efficiently and securely.
Location and Logistics Factors:
- Proximity to your design and assembly facilities
- Shipping options and costs
- Customs and import/export considerations
- Time zone differences for communication
- Intellectual property protection measures
Tip 9: Compare Pricing and Value-Added Services
While cost is an important factor when choosing a rigid-flex PCB manufacturer, it should not be the sole deciding factor. Compare pricing among potential manufacturers, but also consider the value-added services they offer. These services may include design support, testing, assembly, and supply chain management. A manufacturer that provides comprehensive services and support may be more cost-effective in the long run, even if their initial pricing is slightly higher.
Pricing and Value-Added Services:
- Competitive pricing for prototype and production runs
- Design support and DFM analysis
- Testing and quality assurance services
- Assembly and box build services
- Supply chain management and inventory control
- Warranty and after-sales support
Frequently Asked Questions (FAQ)
1. What is the typical lead time for rigid-flex PCB Prototypes?
The lead time for rigid-flex PCB prototypes can vary depending on the manufacturer and the complexity of the design. On average, prototype lead times range from 2 to 4 weeks. However, some manufacturers may offer expedited services for faster turnaround times.
2. Can rigid-flex PCBs be used in high-temperature environments?
Yes, rigid-flex PCBs can be designed to withstand high-temperature environments. The key is to select the appropriate materials, such as high-temperature laminates and solder masks, and to work closely with your manufacturer to ensure the design is optimized for the intended operating conditions.
3. How do I ensure the reliability of my rigid-flex PCBs?
To ensure the reliability of your rigid-flex PCBs, consider the following:
- Choose a reputable manufacturer with experience in rigid-flex PCB fabrication
- Use appropriate materials and design techniques for your application
- Implement robust quality control measures throughout the manufacturing process
- Conduct thorough testing and validation before final production
4. What are the cost implications of using rigid-flex PCBs?
Rigid-flex PCBs typically have higher manufacturing costs compared to traditional rigid PCBs due to the specialized materials, processes, and expertise required. However, the total cost of ownership can be lower when considering the benefits of reduced assembly time, improved reliability, and space savings.
5. Can rigid-flex PCBs be reworked or repaired?
Reworking or repairing rigid-flex PCBs can be challenging due to the complexity of the design and the presence of both rigid and flexible sections. However, experienced manufacturers can often perform repairs or modifications using specialized techniques and equipment. It is essential to work closely with your manufacturer to determine the feasibility and cost of any rework or repair.
Conclusion
Choosing the right rigid-flex PCB manufacturer is crucial for the success of your project. By following these nine tips and carefully evaluating potential manufacturers based on their experience, technical capabilities, quality control measures, and support services, you can find a reliable partner to bring your designs to life. Remember to prioritize quality, reliability, and long-term value over short-term cost savings. With the right rigid-flex PCB manufacturer by your side, you can create innovative and high-performance electronic products that meet the demands of today’s competitive market.
0 Comments