Incorrect Component Placement
One of the most common PCB Assembly Mistakes is incorrect component placement. This can occur due to a variety of factors, including:
- Human error during manual placement
- Incorrect programming of pick-and-place machines
- Inadequate component orientation and polarity checks
- Poor design for manufacturability (DFM) practices
Corrective Actions
To prevent incorrect component placement, consider the following corrective actions:
- Implement a robust quality control process that includes visual inspections and automated optical inspection (AOI) to catch placement errors early in the assembly process.
- Ensure that your PCB design follows DFM guidelines, such as providing clear component orientation and polarity markings.
- Use pick-and-place machines with advanced vision systems and error detection capabilities to minimize the risk of placement errors.
- Provide comprehensive training to assembly operators to ensure they understand the importance of proper component placement and follow best practices.
Insufficient Solder Paste Application
Solder paste is a critical component in the PCB assembly process, as it provides the necessary electrical and mechanical connection between components and the PCB. Insufficient solder paste application can lead to a variety of issues, including:
- Weak or incomplete solder joints
- Increased risk of component misalignment
- Reduced reliability and durability of the assembled PCB
Corrective Actions
To ensure sufficient solder paste application, consider the following corrective actions:
- Use a stencil with the appropriate aperture size and shape to apply the correct amount of solder paste to each pad.
- Regularly maintain and calibrate your solder paste printing equipment to ensure consistent and accurate paste deposition.
- Implement a solder paste inspection (SPI) process to verify the quality and quantity of solder paste applied to each pad.
- Optimize your solder paste printing parameters, such as squeegee pressure, speed, and angle, to achieve the best results for your specific PCB design and components.
Inadequate Reflow Soldering Profile
Reflow soldering is the process of heating the PCB and components to a specific temperature profile to melt the solder paste and form permanent solder joints. An inadequate reflow soldering profile can cause a range of issues, such as:
- Incomplete solder joint formation
- Thermal damage to components
- Excessive oxidation or charring of the PCB and components
- Increased risk of component tombstoning or lifting
Corrective Actions
To ensure an optimal reflow soldering profile, consider the following corrective actions:
- Carefully develop and optimize your reflow soldering profile based on the specific requirements of your PCB design, components, and solder paste.
- Use a reflow oven with precise temperature control and multiple heating zones to achieve a consistent and repeatable soldering process.
- Regularly calibrate and maintain your reflow oven to ensure it is operating within the specified temperature and time parameters.
- Monitor the reflow soldering process using thermocouples or other temperature-sensing devices to verify that the actual temperature profile matches the intended profile.
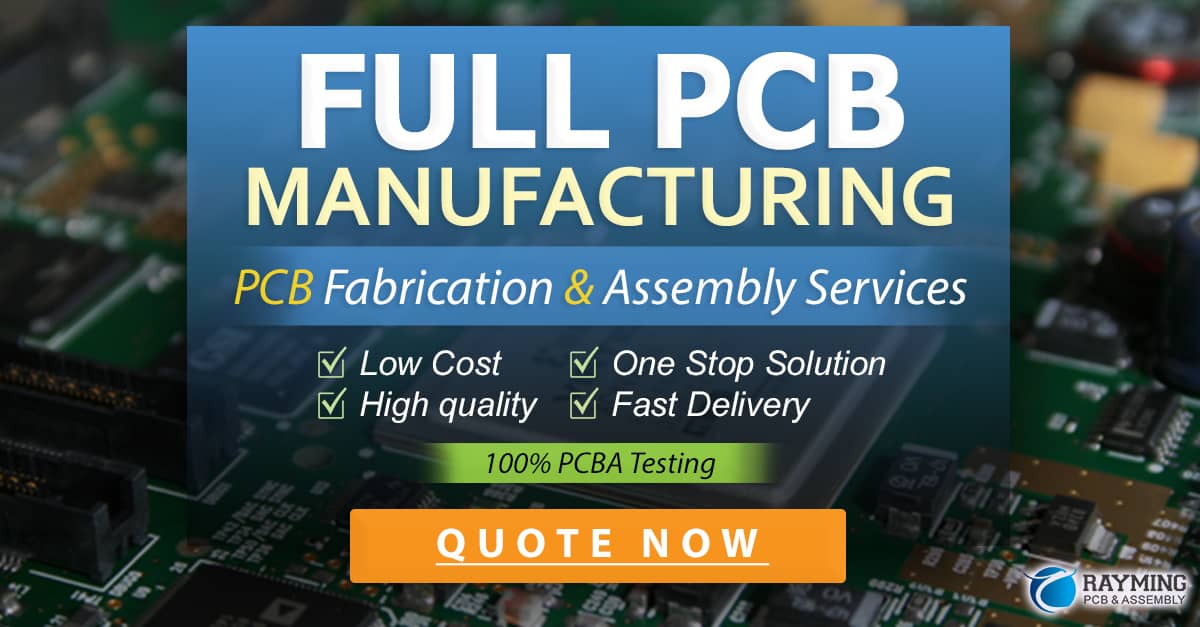
Poor Handling and Storage of Components
Improper handling and storage of components can lead to damage, contamination, and reduced performance. Common issues include:
- Electrostatic discharge (ESD) damage to sensitive components
- Moisture absorption by hygroscopic components
- Physical damage due to rough handling or inadequate packaging
- Contamination by dust, dirt, or other foreign material
Corrective Actions
To prevent component damage and ensure optimal performance, consider the following corrective actions:
- Implement an ESD protection program that includes grounded workstations, wrist straps, and ESD-safe packaging and handling materials.
- Store moisture-sensitive components in a dry, temperature-controlled environment, and follow the manufacturer’s recommended baking and handling procedures.
- Use appropriate packaging materials and techniques to protect components from physical damage during storage and transportation.
- Maintain a clean and organized workspace to minimize the risk of contamination and ensure that components are easily accessible when needed.
Insufficient Cleaning and Contamination Control
Insufficient cleaning and contamination control can lead to a variety of issues that impact the reliability and performance of the assembled PCB. Common problems include:
- Flux residue buildup, which can cause corrosion and electrical shorts
- Solder balls or splashes that can cause short circuits
- Dust, dirt, and other foreign material that can interfere with proper component placement and soldering
Corrective Actions
To ensure proper cleaning and contamination control, consider the following corrective actions:
- Use cleaning agents and processes that are compatible with your PCB materials and components, and follow the manufacturer’s recommended cleaning procedures.
- Implement a regular cleaning and maintenance schedule for your assembly equipment and workspaces to prevent the buildup of contaminants.
- Use air filtration systems and other environmental controls to minimize the presence of airborne contaminants in your assembly area.
- Establish and enforce strict housekeeping and hygiene protocols to prevent the introduction of foreign material into the assembly process.
Inadequate Testing and Inspection
Inadequate testing and inspection can allow defective or substandard PCBs to pass through the assembly process undetected, leading to increased costs, reduced reliability, and potential product failures in the field. Common issues include:
- Missed or incomplete visual inspections
- Inadequate electrical testing and functional verification
- Lack of environmental stress testing to ensure product durability
- Insufficient traceability and documentation of testing and inspection results
Corrective Actions
To ensure comprehensive testing and inspection, consider the following corrective actions:
- Develop and implement a robust quality control plan that includes visual inspections, automated optical inspection (AOI), and electrical testing at various stages of the assembly process.
- Use advanced testing techniques, such as in-circuit testing (ICT), boundary scan testing, and functional testing, to verify the performance and reliability of the assembled PCB.
- Conduct environmental stress testing, such as thermal cycling, vibration, and humidity exposure, to ensure that the PCB can withstand the expected operating conditions.
- Maintain detailed records of all testing and inspection results, including any defects or anomalies found, corrective actions taken, and final disposition of the PCB.
FAQ
-
What are the most common causes of component placement errors in PCB assembly?
Component placement errors can be caused by human error during manual placement, incorrect programming of pick-and-place machines, inadequate component orientation and polarity checks, and poor design for manufacturability (DFM) practices. -
How can I ensure that the correct amount of solder paste is applied to each pad during PCB assembly?
To ensure the correct amount of solder paste is applied, use a stencil with the appropriate aperture size and shape, regularly maintain and calibrate your solder paste printing equipment, implement a solder paste inspection (SPI) process, and optimize your solder paste printing parameters. -
What are the consequences of an inadequate reflow soldering profile?
An inadequate reflow soldering profile can lead to incomplete solder joint formation, thermal damage to components, excessive oxidation or charring of the PCB and components, and an increased risk of component tombstoning or lifting. -
How can I prevent damage to sensitive components during PCB assembly?
To prevent damage to sensitive components, implement an ESD protection program, store moisture-sensitive components in a dry, temperature-controlled environment, use appropriate packaging materials and techniques, and maintain a clean and organized workspace. -
Why is comprehensive testing and inspection critical in PCB assembly?
Comprehensive testing and inspection are critical in PCB assembly to detect and prevent defective or substandard PCBs from passing through the assembly process undetected. This helps to reduce costs, improve reliability, and minimize the risk of product failures in the field.
In conclusion, understanding and addressing common PCB assembly mistakes is essential for ensuring the successful production of high-quality, reliable PCBs. By implementing the corrective actions outlined in this article, you can minimize the risk of errors, improve your assembly processes, and ultimately deliver better products to your customers.
PCB Assembly Mistake | Potential Consequences | Corrective Actions |
---|---|---|
Incorrect Component Placement | – Reduced reliability – Decreased performance – Increased costs |
– Implement robust quality control process – Follow DFM guidelines – Use advanced pick-and-place machines – Provide comprehensive operator training |
Insufficient Solder Paste Application | – Weak or incomplete solder joints – Increased risk of component misalignment – Reduced reliability and durability |
– Use appropriate stencil and aperture design – Regularly maintain and calibrate equipment – Implement solder paste inspection (SPI) – Optimize printing parameters |
Inadequate Reflow Soldering Profile | – Incomplete solder joint formation – Thermal damage to components – Excessive oxidation or charring – Increased risk of component tombstoning or lifting |
– Develop and optimize reflow profile – Use precise temperature control and multiple heating zones – Regularly calibrate and maintain reflow oven – Monitor reflow process using temperature-sensing devices |
Poor Handling and Storage of Components | – ESD damage to sensitive components – Moisture absorption by hygroscopic components – Physical damage due to rough handling or inadequate packaging – Contamination by dust, dirt, or other foreign material |
– Implement an ESD protection program – Store moisture-sensitive components properly – Use appropriate packaging materials and techniques – Maintain a clean and organized workspace |
Insufficient Cleaning and Contamination Control | – Flux residue buildup – Solder balls or splashes – Interference from dust, dirt, and other foreign material |
– Use compatible cleaning agents and processes – Implement regular cleaning and maintenance schedule – Use air filtration systems and environmental controls – Establish and enforce strict housekeeping and hygiene protocols |
Inadequate Testing and Inspection | – Missed or incomplete visual inspections – Inadequate electrical testing and functional verification – Lack of environmental stress testing – Insufficient traceability and documentation |
– Develop and implement a robust quality control plan – Use advanced testing techniques (AOI, ICT, boundary scan, functional testing) – Conduct environmental stress testing – Maintain detailed records of testing and inspection results |
By addressing these common PCB assembly mistakes and implementing the appropriate corrective actions, you can significantly improve the quality, reliability, and performance of your PCBs while reducing costs and minimizing the risk of product failures.
0 Comments