Introduction to PCB Essentials
Printed Circuit Boards (PCBs) are the backbone of modern electronics. They provide a reliable and efficient way to connect electronic components and create complex circuits. Among the various types of PCBs, 2 layer PCBs are the most common and widely used. In this article, we will dive deep into the world of 2 layer PCBs, covering everything you need to know to design, manufacture, and work with them effectively.
What is a 2 Layer PCB?
A 2 layer PCB, as the name suggests, consists of two conductive layers – a top layer and a bottom layer. These layers are typically made of copper and are separated by an insulating material called the substrate. The electronic components are mounted on the top layer, while the bottom layer is used for routing traces and creating a ground plane.
Advantages of 2 Layer PCBs
2 layer PCBs offer several advantages over single layer and multi-layer PCBs:
- Cost-effective: 2 layer PCBs are less expensive to manufacture compared to multi-layer PCBs, making them a popular choice for low-cost electronics projects.
- Easier to design: With only two layers to work with, designing a 2 layer PCB is simpler and faster than designing a multi-layer PCB.
- Improved signal integrity: The ground plane on the bottom layer helps to reduce electromagnetic interference (EMI) and improve signal integrity.
- Increased durability: The additional layer provides extra support and makes the PCB more durable and resistant to physical stress.
Designing a 2 Layer PCB
Schematic Design
The first step in designing a 2 layer PCB is to create a schematic diagram. A schematic represents the electronic circuit in a symbolic form, showing how the components are connected. It serves as a blueprint for the PCB layout.
When creating a schematic, consider the following:
- Use a CAD (Computer-Aided Design) tool specifically designed for electronic schematics, such as KiCad, Eagle, or Altium Designer.
- Ensure that the components are correctly connected and that the circuit functions as intended.
- Use appropriate symbols for each component and label them clearly.
- Assign unique reference designators to each component for easy identification.
PCB Layout
Once the schematic is complete, the next step is to create the PCB layout. The layout determines the physical placement of components and the routing of traces on the PCB.
When designing the PCB layout, keep these tips in mind:
- Use a CAD tool that supports PCB layout design, such as the ones mentioned earlier.
- Define the board outline and place the components strategically to minimize the overall board size and optimize signal paths.
- Route the traces efficiently, avoiding sharp angles and minimizing the length of high-speed signal traces.
- Maintain proper clearance between traces and components to prevent short circuits and signal interference.
- Create a ground plane on the bottom layer to improve signal integrity and reduce EMI.
- Adhere to the design rules and guidelines provided by the PCB manufacturer to ensure manufacturability.
Design Rule Check (DRC)
Before finalizing the PCB layout, it is crucial to run a Design Rule Check (DRC). DRC is an automated process that checks the layout against a set of predefined rules to identify potential issues and errors.
Common design rules include:
- Minimum trace width and spacing
- Minimum drill size and spacing
- Copper-to-edge clearance
- Solder mask and silkscreen requirements
Running a DRC helps to catch design flaws early in the process, reducing the risk of manufacturing issues and saving time and cost.
Manufacturing a 2 Layer PCB
PCB Fabrication Process
Once the PCB design is finalized and has passed the DRC, it is ready for manufacturing. The PCB fabrication process involves several steps:
- PCB Data Preparation: The PCB design files (Gerber files) are prepared and sent to the PCB manufacturer.
- Material Selection: The appropriate substrate material (typically FR-4) and copper thickness are selected based on the PCB specifications.
- Copper Lamination: The copper layers are laminated onto the substrate using heat and pressure.
- Drilling: Holes are drilled through the PCB to accommodate through-hole components and create vias for inter-layer connections.
- Copper Patterning: The unwanted copper is etched away, leaving behind the desired traces and pads.
- Solder Mask Application: A protective solder mask layer is applied to the PCB to prevent short circuits and improve solderability.
- Silkscreen Printing: The component labels and other markings are printed on the PCB using silkscreen.
- Surface Finish: A surface finish, such as HASL (Hot Air Solder Leveling) or ENIG (Electroless Nickel Immersion Gold), is applied to the exposed copper to prevent oxidation and enhance solderability.
- Electrical Testing: The PCB undergoes electrical testing to ensure that it functions as intended and meets the specified requirements.
PCB Assembly
After the PCB fabrication is complete, the next step is to assemble the electronic components onto the board. PCB assembly can be done manually or using automated equipment, depending on the complexity of the board and the production volume.
The main steps in PCB assembly are:
- Solder Paste Application: Solder paste is applied to the pads on the PCB using a stencil or syringe.
- Component Placement: The electronic components are placed on the PCB, either manually or using a pick-and-place machine.
- Reflow Soldering: The PCB is heated in a reflow oven, causing the solder paste to melt and form a permanent connection between the components and the PCB.
- Inspection: The assembled PCB is inspected visually and using automated optical inspection (AOI) to ensure that all components are correctly placed and soldered.
- Functional Testing: The assembled PCB undergoes functional testing to verify that it performs as intended and meets the required specifications.
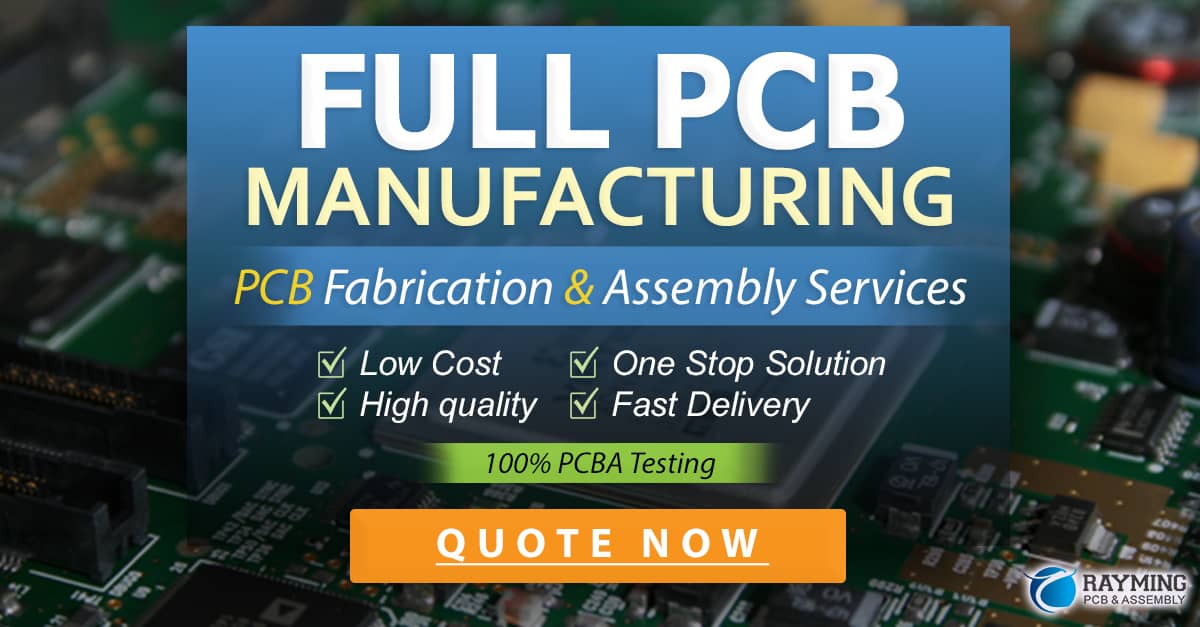
Working with 2 Layer PCBs
Soldering Techniques
Soldering is an essential skill when working with 2 layer PCBs. Proper soldering ensures reliable connections and prevents issues like cold solder joints or short circuits.
Some key soldering techniques include:
- Tin the soldering iron tip with a small amount of solder before use.
- Apply heat to the pad and the component lead simultaneously, allowing the solder to flow naturally.
- Use the appropriate amount of solder – too little can result in weak joints, while too much can cause bridging between pads.
- Keep the soldering iron tip clean and well-maintained for optimal performance.
Debugging and Troubleshooting
Despite careful design and assembly, issues can still arise with 2 layer PCBs. Debugging and troubleshooting skills are crucial for identifying and resolving these problems.
Common issues and their solutions include:
- Short circuits: Inspect the PCB for solder bridges or incorrect component placement. Use a multimeter to identify the short and carefully remove the excess solder or reposition the component.
- Open circuits: Check for broken traces or poor solder joints. Repair the trace using a jumper wire or resolder the joint as needed.
- Component failure: Test the suspected component with a multimeter or oscilloscope. Replace the faulty component with a new one.
- Signal integrity issues: Ensure that the PCB layout follows best practices for signal routing and grounding. Use decoupling capacitors and shielding techniques to mitigate EMI.
When troubleshooting, it is essential to approach the problem systematically and isolate the issue by testing individual components and subsystems.
FAQs
-
Q: What is the typical thickness of a 2 layer PCB?
A: The standard thickness of a 2 layer PCB is 1.6mm (0.063 inches). However, thinner or thicker options are available depending on the specific requirements of the project. -
Q: Can I use a 2 layer PCB for high-frequency designs?
A: While 2 layer PCBs can be used for high-frequency designs, they may not be the optimal choice. High-frequency signals are more susceptible to EMI and signal integrity issues, which can be better addressed using multi-layer PCBs with dedicated power and ground planes. -
Q: How small can the traces be on a 2 layer PCB?
A: The minimum trace width on a 2 layer PCB depends on the PCB manufacturer’s capabilities and the desired copper thickness. Typically, trace widths as small as 0.15mm (6 mil) are achievable, but it is best to consult with the manufacturer for their specific guidelines. -
Q: Can I mix surface mount and through-hole components on a 2 layer PCB?
A: Yes, it is possible to use both surface mount and through-hole components on a 2 layer PCB. This is known as a mixed-technology PCB. However, keep in mind that through-hole components require drilling, which can increase the manufacturing cost and time compared to an all-surface-mount design. -
Q: What are the limitations of 2 layer PCBs compared to multi-layer PCBs?
A: The main limitations of 2 layer PCBs include reduced routing space, limited ability to create dedicated power and ground planes, and potential signal integrity issues for high-speed designs. Multi-layer PCBs offer more flexibility and better performance but come at a higher manufacturing cost.
Conclusion
2 layer PCBs are a fundamental building block of modern electronics. Understanding the principles of designing, manufacturing, and working with 2 layer PCBs is essential for anyone involved in electronic product development.
By following best practices in schematic design, PCB layout, and manufacturing, you can create reliable and cost-effective 2 layer PCBs. Additionally, developing skills in soldering and troubleshooting will enable you to work effectively with these PCBs and resolve any issues that may arise.
As you continue to explore the world of PCBs, keep in mind that 2 layer PCBs are just one of the many options available. Depending on the complexity and requirements of your project, you may need to consider multi-layer PCBs or other specialized PCB technologies.
By staying up-to-date with the latest advancements in PCB design and manufacturing, and continually expanding your knowledge and skills, you will be well-equipped to tackle a wide range of electronic projects and bring your ideas to life.
0 Comments