Understanding Microwave PCB Fundamentals
What is a Microwave PCB?
A microwave PCB is a specialized printed circuit board designed to handle high-frequency signals, typically in the range of 300 MHz to 300 GHz. These PCBs are used in various applications, such as wireless communication systems, radar, and satellite communications.
Key Characteristics of Microwave PCBs
Microwave PCBs have unique characteristics that distinguish them from traditional PCBs:
- Higher operating frequencies
- Shorter wavelengths
- Increased sensitivity to noise and interference
- Stricter manufacturing tolerances
Designing a Microwave PCB
Step 1: Define Design Requirements
Clearly define the design requirements for your microwave PCB, including:
- Operating frequency range
- Signal power levels
- Required bandwidth
- Environmental conditions
- Physical dimensions and constraints
Step 2: Choose the Appropriate Substrate Material
Select a suitable substrate material for your microwave PCB based on its dielectric properties, loss tangent, and thermal stability. Common substrate materials include:
- Rogers RO4000 series
- Taconic RF-35
- Isola I-Tera MT40
Step 3: Determine Layer Stack-up
Decide on the appropriate layer stack-up for your microwave PCB, considering the number of layers, their arrangement, and the thickness of each layer. A typical stack-up may include:
- Top and bottom signal layers
- Ground planes
- Power planes
- Dielectric layers
Step 4: Select Appropriate Trace Geometry
Choose the appropriate trace geometry for your microwave PCB based on the desired characteristic impedance and the substrate material’s properties. Common trace geometries include:
- Microstrip
- Stripline
- Coplanar waveguide (CPW)
Step 5: Calculate Trace Dimensions
Use microwave transmission line equations to calculate the required trace width and spacing for your chosen trace geometry and desired characteristic impedance.
Step 6: Optimize Signal Routing
Route high-frequency signals on the top or bottom layers of the PCB to minimize signal loss and crosstalk. Avoid sharp bends and keep trace lengths as short as possible.
Step 7: Implement Proper Grounding Techniques
Ensure proper grounding techniques are used throughout the microwave PCB design, including:
- Solid ground planes
- Via stitching
- Microvia technology for multi-layer boards
Step 8: Incorporate Impedance Matching Networks
Design and incorporate impedance matching networks where necessary to ensure maximum power transfer and minimize signal reflections.
Step 9: Use Appropriate Connectors and Transitions
Select appropriate connectors and transitions for your microwave PCB, such as:
- SMA connectors
- SSMP connectors
- Microstrip-to-coaxial transitions
Step 10: Simulate and Optimize the Design
Perform electromagnetic (EM) simulations of your microwave PCB design using specialized software tools like Ansys HFSS or Keysight ADS. Optimize the design based on simulation results.
Step 11: Consider Thermal Management
Address thermal management issues in your microwave PCB design by:
- Using high-thermal-conductivity substrate materials
- Incorporating heat sinks or thermal vias
- Designing for adequate airflow
Step 12: Implement EMI/EMC Mitigation Techniques
Employ electromagnetic interference (EMI) and electromagnetic compatibility (EMC) mitigation techniques, such as:
- Shielding sensitive components
- Using filters and ferrites
- Proper grounding and isolation
Step 13: Follow High-Frequency PCB Manufacturing Guidelines
Adhere to high-frequency PCB manufacturing guidelines, including:
- Tight tolerances for trace width and spacing
- Controlled impedance manufacturing
- High-quality surface finishes (e.g., ENIG, ENEPIG)
Step 14: Perform Design Rule Checks (DRC)
Conduct thorough design rule checks (DRC) to ensure your microwave PCB design complies with the manufacturer’s guidelines and industry standards.
Step 15: Prototype and Test
Manufacture prototypes of your microwave PCB and perform rigorous testing to validate its performance, including:
- S-parameter measurements
- Signal integrity tests
- EMI/EMC compliance tests
Step 16: Iterate and Refine the Design
Based on the prototype testing results, iterate and refine your microwave PCB design to optimize performance and address any issues identified during testing.
Microwave PCB Design Best Practices
To ensure optimal performance and reliability of your microwave PCB, follow these best practices:
- Keep trace lengths as short as possible
- Maintain consistent characteristic impedance throughout the design
- Use a solid ground plane and proper grounding techniques
- Avoid sharp bends in traces
- Use appropriate substrate materials and layer stack-up
- Simulate and optimize the design before manufacturing
- Follow high-frequency PCB manufacturing guidelines
- Test prototypes thoroughly and iterate the design as needed
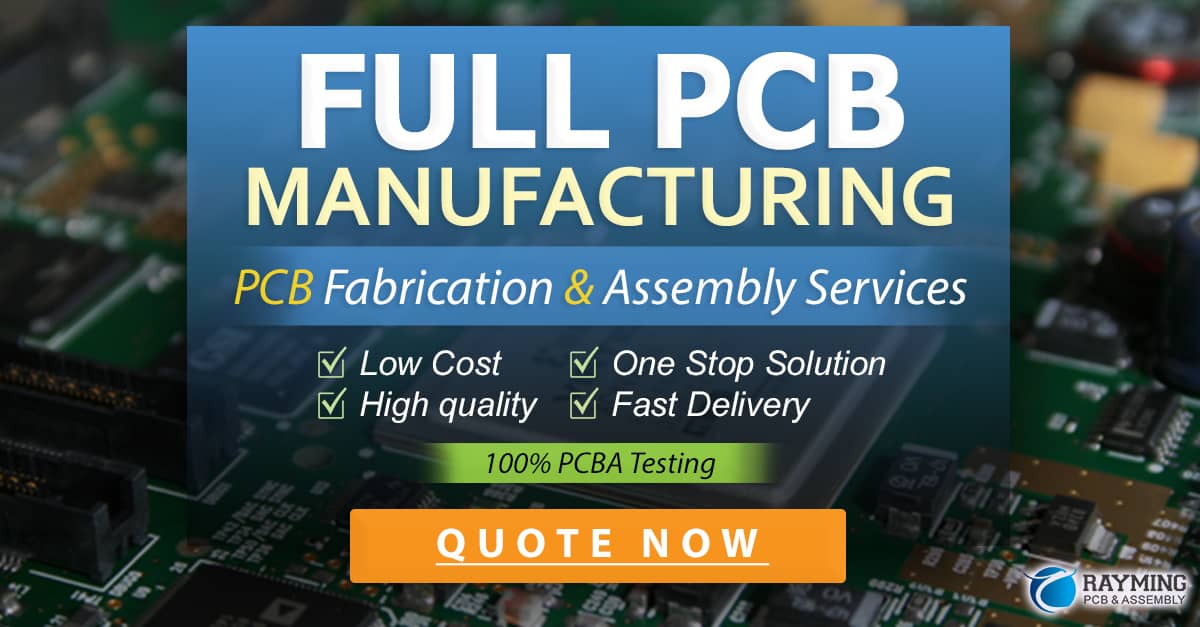
Microwave PCB Design Tools
Several software tools are available to aid in the design and simulation of microwave PCBs, including:
Tool | Description |
---|---|
Ansys HFSS | 3D full-wave electromagnetic field simulation |
Keysight ADS | Electronic design automation software for RF and microwave |
Cadence Allegro | PCB design and analysis tool with high-speed design features |
Altium Designer | PCB design software with integrated 3D modeling and analysis |
CST Studio Suite | 3D EM simulation software for designing and optimizing high-frequency components |
Microwave PCB fabrication and Assembly
When fabricating and assembling microwave PCBs, consider the following:
- Choose a reputable PCB manufacturer experienced in high-frequency PCBs
- Provide clear and detailed manufacturing instructions
- Specify controlled impedance requirements
- Select appropriate surface finishes and solder mask materials
- Use experienced assemblers familiar with high-frequency components and techniques
Frequently Asked Questions (FAQ)
1. What is the difference between a microwave PCB and a traditional PCB?
Microwave PCBs are designed to handle high-frequency signals (typically 300 MHz to 300 GHz) and have stricter manufacturing tolerances, specialized substrate materials, and unique design considerations compared to traditional PCBs.
2. What are the most common substrate materials used in microwave PCBs?
Common substrate materials for microwave PCBs include Rogers RO4000 series, Taconic RF-35, and Isola I-Tera MT40. These materials are chosen for their favorable dielectric properties, low loss tangent, and high thermal stability.
3. Why is impedance matching important in microwave PCB design?
Impedance matching is crucial in microwave PCB design to ensure maximum power transfer and minimize signal reflections. Mismatched impedances can lead to signal degradation, reduced efficiency, and potential damage to components.
4. How can I mitigate EMI/EMC issues in my microwave PCB design?
To mitigate EMI/EMC issues in microwave PCB designs, use techniques such as shielding sensitive components, incorporating filters and ferrites, and implementing proper grounding and isolation. Adhering to best practices and industry standards can also help minimize EMI/EMC problems.
5. What should I consider when selecting connectors for my microwave PCB?
When selecting connectors for your microwave PCB, consider factors such as the operating frequency range, signal power levels, physical dimensions, and compatibility with your chosen trace geometry. Common connector types for microwave PCBs include SMA, SSMP, and microstrip-to-coaxial transitions.
In conclusion, designing a microwave PCB requires a thorough understanding of high-frequency signal behavior, specialized design techniques, and adherence to best practices. By following the 16 steps outlined in this guide and leveraging the appropriate tools and resources, you can create a high-performance, reliable microwave PCB for your application.
0 Comments