What is a PCB Testboard?
A PCB testboard, also known as a programming and testing board, is a printed circuit board specifically designed for the purpose of programming and testing electronic components, integrated circuits (ICs), and other devices. These boards provide a convenient platform for developers, engineers, and technicians to verify the functionality, performance, and compatibility of various electronic parts before integrating them into a final product or system.
PCB testboards offer several advantages, such as:
- Facilitating rapid prototyping and debugging
- Saving time and resources by identifying issues early in the development process
- Providing a standardized interface for programming and testing different components
- Enabling easy access to test points and signals for measurement and analysis
- Allowing for the evaluation of different design options and configurations
Key Considerations for Designing a PCB Testboard
When designing a PCB testboard, there are several key factors to consider to ensure optimal performance, reliability, and usability. These include:
-
Purpose and Scope: Clearly define the specific purpose and scope of the testboard. Determine which components, ICs, or devices will be tested, and what types of tests and measurements will be performed.
-
Form Factor and Size: Choose an appropriate form factor and size for the testboard based on the components being tested and the available workspace. Consider factors such as the number of components, their sizes, and the required spacing between them.
-
Power Supply and Distribution: Design a robust power supply and distribution system to provide stable and accurate power to the components being tested. Consider the voltage and current requirements of each component, as well as any necessary power sequencing or isolation.
-
Signal Integrity: Ensure proper signal integrity by carefully designing the PCB layout, including the placement of components, routing of traces, and use of appropriate grounding and shielding techniques. Minimize cross-talk, noise, and reflections to maintain signal quality.
-
Connectivity and Interfaces: Incorporate suitable connectors and interfaces for programming, testing, and measurement equipment. This may include headers, test points, JTAG ports, USB or serial interfaces, and other standard or custom connectors.
-
Modularity and Expandability: Design the testboard with modularity and expandability in mind, allowing for future upgrades or modifications. Use standardized interfaces and connectors to facilitate the addition of new components or features as needed.
-
Documentation and Labeling: Provide clear and comprehensive documentation for the testboard, including schematics, Bill of Materials (BOM), assembly instructions, and user guides. Label all components, connectors, and test points on the board for easy identification and troubleshooting.
PCB Testboard Design Tips and Best Practices
To optimize the performance and usability of your PCB testboard, consider the following design tips and best practices:
1. Component Selection and Placement
- Choose components that are suitable for the intended purpose and operating conditions of the testboard.
- Place components in a logical and organized manner, grouping related components together and minimizing the distance between them to reduce signal path lengths.
- Ensure adequate spacing between components to facilitate easy access for probing and measurement.
2. Power Supply Design
- Use separate power planes or traces for different voltage levels to minimize noise and interference.
- Implement proper decoupling and filtering techniques to ensure stable and clean power delivery to the components.
- Include provisions for current monitoring and limiting to protect sensitive components from damage.
3. Grounding and Shielding
- Use a solid ground plane to provide a low-impedance return path for signals and minimize ground loops.
- Implement proper grounding techniques, such as star grounding or split ground planes, to isolate noisy circuits from sensitive ones.
- Use shielding techniques, such as ground shields or Faraday cages, to reduce electromagnetic interference (EMI) and crosstalk between components.
4. Signal Routing and Impedance Control
- Route signal traces as directly as possible to minimize signal path lengths and reduce noise and reflections.
- Use appropriate trace widths and spacing to maintain Characteristic Impedance and minimize crosstalk.
- Implement proper termination techniques, such as series or parallel termination, to match the impedance of the signal traces and minimize reflections.
5. Connector and Test Point Placement
- Place connectors and test points in easily accessible locations for convenient probing and measurement.
- Use standardized connectors and pinouts to ensure compatibility with programming and testing equipment.
- Provide clear labeling and markings for connectors and test points to avoid confusion and errors during usage.
6. Thermal Management
- Consider the thermal characteristics of the components being tested and ensure adequate heat dissipation.
- Use appropriate heatsinks, Thermal Pads, or cooling solutions to prevent overheating and ensure reliable operation.
- Place temperature-sensitive components away from heat-generating components to minimize thermal interaction.
7. Manufacturability and Assembly
- Design the PCB testboard with manufacturability in mind, considering factors such as component placement, solder mask, and silkscreen.
- Provide clear assembly instructions and guidance for hand soldering or machine assembly.
- Use standard component packages and footprints to facilitate easy sourcing and assembly.
8. Debugging and Troubleshooting Features
- Include test points, jumpers, or switches to enable easy debugging and troubleshooting of the testboard.
- Provide provisions for attaching probes or monitoring equipment, such as oscilloscopes or logic analyzers.
- Consider including built-in self-test (BIST) or diagnostic features to help identify and isolate faults.
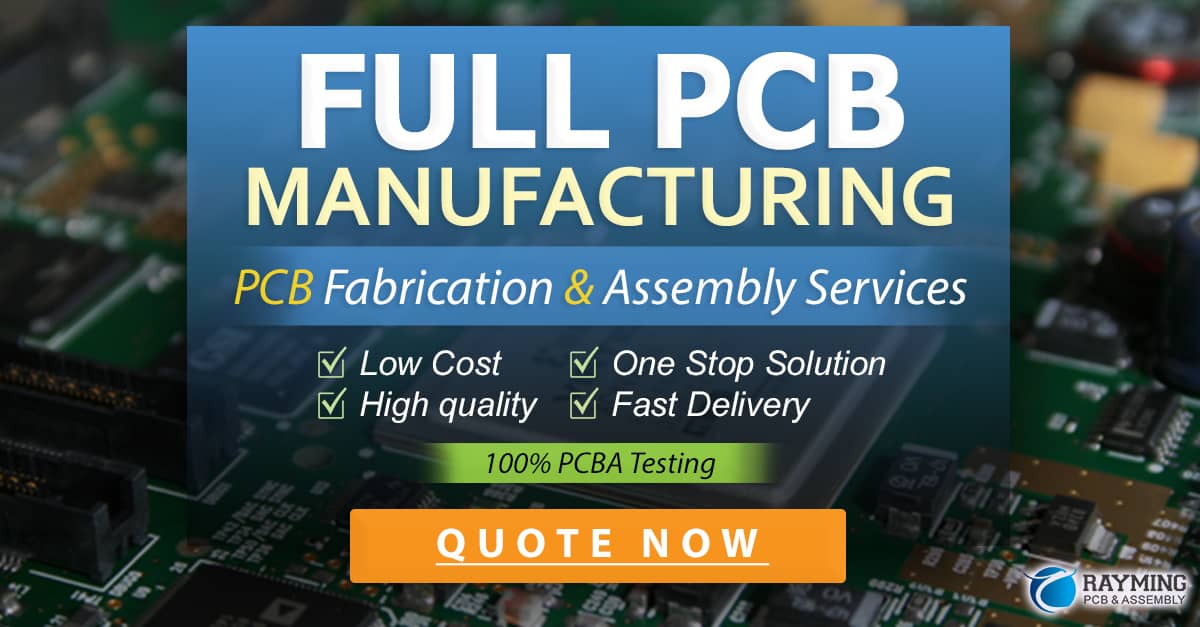
Example PCB Testboard Designs
To illustrate the application of these design tips and best practices, let’s look at a few example PCB testboard designs for different scenarios:
Example 1: Microcontroller Programming and Testing Board
Component | Description |
---|---|
Microcontroller | ATmega328P (DIP Package) |
Programming Port | ICSP (In-Circuit Serial Programming) Header |
Power Supply | 5V USB Input, 3.3V LDO Regulator |
Oscillator | 16 MHz Crystal Oscillator |
Debugging | UART Header for Serial Communication |
Expansion | GPIO Headers for Connecting Peripherals |
This testboard is designed for programming and testing an ATmega328P microcontroller. It includes an ICSP header for in-circuit programming, a USB port for power and communication, and a crystal oscillator for clock generation. The board also features UART headers for serial debugging and GPIO headers for connecting external peripherals.
Example 2: FPGA Development and Testing Board
Component | Description |
---|---|
FPGA | Xilinx Artix-7 (XC7A35T) in FTG256 Package |
Configuration | JTAG Port for Programming and Debugging |
Memory | 256 MB DDR3 SDRAM, 32 MB QSPI Flash |
Interfaces | USB-UART Bridge, Gigabit Ethernet PHY |
Expansion | FMC (FPGA Mezzanine Card) Connector for Expansion Modules |
This testboard is designed for developing and testing designs on a Xilinx Artix-7 FPGA. It includes a JTAG port for configuration and debugging, along with DDR3 SDRAM and QSPI Flash for memory storage. The board also features a USB-UART bridge for communication and a Gigabit Ethernet PHY for network connectivity. An FMC connector is provided for connecting expansion modules and custom peripherals.
FAQ
1. What is the purpose of a PCB testboard?
A PCB testboard is used for programming, testing, and debugging electronic components, integrated circuits (ICs), and devices before integrating them into a final product or system. It provides a standardized platform for evaluating the functionality, performance, and compatibility of various electronic parts.
2. What are the key considerations when designing a PCB testboard?
When designing a PCB testboard, key considerations include defining the purpose and scope, choosing an appropriate form factor and size, designing a robust power supply and distribution system, ensuring signal integrity, incorporating suitable connectivity and interfaces, designing for modularity and expandability, and providing clear documentation and labeling.
3. How can I ensure proper signal integrity on a PCB testboard?
To ensure proper signal integrity on a PCB testboard, carefully design the PCB layout by optimizing component placement, routing traces efficiently, and implementing appropriate grounding and shielding techniques. Minimize cross-talk, noise, and reflections to maintain signal quality.
4. What are some best practices for component placement on a PCB testboard?
When placing components on a PCB testboard, follow these best practices:
- Group related components together and minimize the distance between them to reduce signal path lengths.
- Ensure adequate spacing between components for easy access and probing.
- Place connectors and test points in easily accessible locations.
- Consider the thermal characteristics of components and ensure proper heat dissipation.
5. How can I facilitate debugging and troubleshooting on a PCB testboard?
To facilitate debugging and troubleshooting on a PCB testboard, include features such as:
- Test points, jumpers, or switches to enable easy probing and configuration.
- Provisions for attaching probes or monitoring equipment, such as oscilloscopes or logic analyzers.
- Built-in self-test (BIST) or diagnostic features to help identify and isolate faults.
- Clear labeling and markings for components, connectors, and test points.
By following these tips and best practices, you can design a PCB testboard that is efficient, reliable, and user-friendly for programming, testing, and debugging electronic components and systems.
0 Comments