1. Optimize PCB Design for Manufacturing (DFM)
One of the most effective ways to cut PCB assembly costs is to optimize your PCB design for manufacturing (DFM). By following DFM guidelines, you can ensure that your PCB design is compatible with the manufacturing process, reducing the likelihood of errors, delays, and additional costs.
Key DFM Considerations:
- Minimize the number of layers
- Use standard component sizes and packages
- Ensure adequate spacing between components
- Avoid unnecessary complexity in the design
By adhering to DFM principles, you can streamline the assembly process, reduce the risk of defects, and ultimately lower your PCB Assembly Costs.
2. Choose the Right PCB Manufacturer
Selecting the right PCB manufacturer is crucial for cost-effective assembly. When evaluating potential partners, consider the following factors:
- Experience and expertise in your specific industry
- Quality control processes and certifications
- Pricing and lead times
- Customer support and communication
Working with a reputable PCB manufacturer that understands your needs and offers competitive pricing can significantly reduce your assembly costs without sacrificing quality.
3. Leverage Economies of Scale
Ordering PCBs in larger quantities can often result in lower unit costs due to economies of scale. PCB Manufacturers typically offer volume discounts, as the fixed costs associated with setting up the assembly line are spread across a larger number of units.
Quantity | Unit Cost |
---|---|
100 | $10 |
500 | $8 |
1000 | $6 |
By carefully planning your production runs and ordering in bulk when possible, you can take advantage of volume discounts and reduce your overall PCB assembly costs.
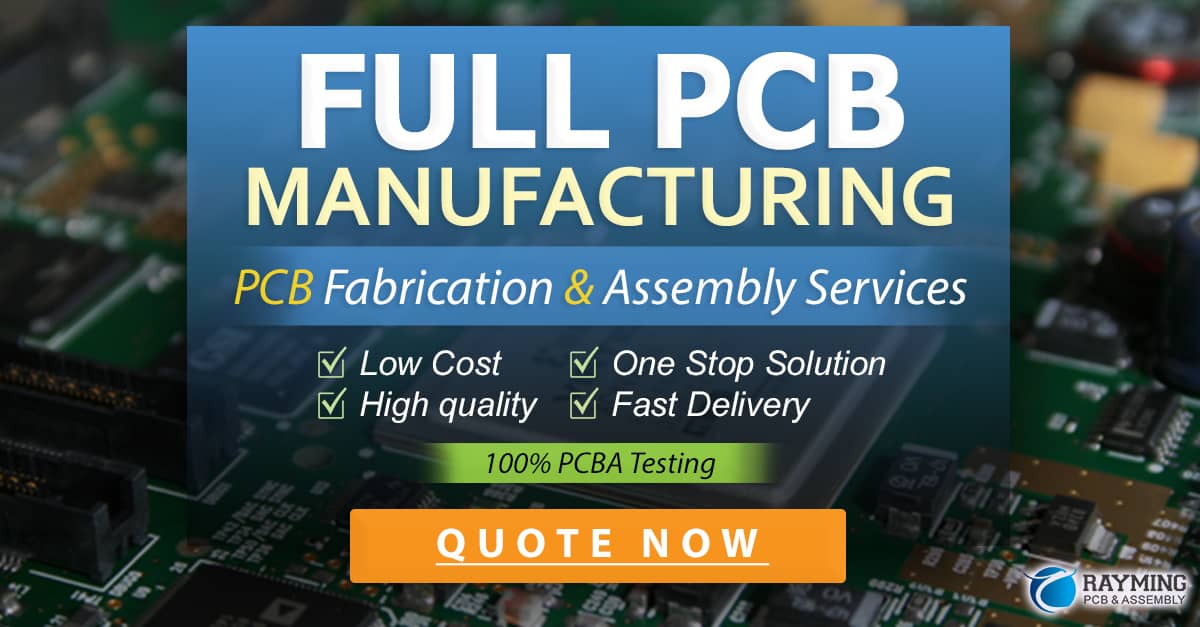
4. Standardize Components and Materials
Standardizing the components and materials used in your PCB assembly can lead to significant cost savings. By using common, readily available components, you can benefit from lower prices due to increased market competition and reduced lead times.
Additionally, standardizing materials, such as the PCB substrate and solder mask, can help you negotiate better prices with suppliers and ensure consistent quality across your products.
5. Implement Automated Assembly Processes
Investing in automated assembly processes can greatly reduce labor costs and improve efficiency. Automated pick-and-place machines, solder paste printers, and reflow ovens can handle a large portion of the assembly process, minimizing the need for manual labor.
While the initial investment in automated equipment may be higher, the long-term cost savings and increased throughput often justify the expense.
6. Optimize PCB Panel Utilization
Efficient utilization of PCB panels can help minimize material waste and reduce costs. When designing your PCB, consider the following strategies:
- Maximize the number of PCBs per panel
- Minimize the space between individual PCBs
- Use standard panel sizes to avoid custom tooling costs
By optimizing your PCB panel utilization, you can reduce material costs and maximize the number of PCBs produced per assembly run.
7. Implement Effective Quality Control Measures
Implementing robust quality control measures throughout the PCB assembly process can help identify and address issues early, preventing costly rework and delays. Some effective quality control strategies include:
- Automated optical inspection (AOI)
- In-circuit testing (ICT)
- Functional testing
- X-ray inspection for complex assemblies
By catching defects early in the process, you can minimize the cost of rework and ensure that your PCBs meet the highest quality standards.
8. Optimize Inventory Management
Effective inventory management is essential for controlling PCB assembly costs. Overstocking components can tie up valuable capital, while understocking can lead to production delays and increased rush order fees.
Implement an inventory management system that helps you:
- Monitor stock levels in real-time
- Forecast demand based on historical data
- Establish optimal reorder points
- Identify slow-moving or obsolete components
By optimizing your inventory management, you can reduce carrying costs, minimize the risk of obsolescence, and ensure a steady supply of components for your PCB assembly process.
9. Foster Long-Term Supplier Relationships
Building strong, long-term relationships with your PCB assembly suppliers can lead to cost savings and improved quality. By establishing trust and open communication with your suppliers, you can:
- Negotiate better pricing and payment terms
- Collaborate on cost-saving initiatives
- Receive priority support and faster turnaround times
- Access valuable industry insights and expertise
Investing in long-term supplier relationships can help you achieve a more cost-effective and efficient PCB assembly process.
10. Continuously Monitor and Optimize the Assembly Process
Regularly monitoring and analyzing your PCB assembly process can help identify areas for improvement and cost savings. Use data-driven insights to:
- Identify bottlenecks and inefficiencies
- Optimize production schedules and resource allocation
- Evaluate the performance of suppliers and partners
- Track key metrics, such as yield rates and cycle times
By continuously monitoring and optimizing your PCB assembly process, you can identify opportunities for cost reduction and implement data-driven improvements.
11. Invest in Employee Training and Development
Investing in the training and development of your employees can lead to significant cost savings in the long run. Well-trained employees are more efficient, make fewer mistakes, and are better equipped to identify and solve problems in the assembly process.
Provide your team with:
- Regular training on best practices and new technologies
- Opportunities for skill development and career growth
- A culture of continuous improvement and innovation
By fostering a skilled and engaged workforce, you can improve the overall efficiency and quality of your PCB assembly process, ultimately reducing costs.
Frequently Asked Questions (FAQ)
1. How much can I expect to save by implementing these cost-cutting strategies?
The amount you can save by implementing these strategies will vary depending on your specific circumstances, such as the complexity of your PCBs, the volume of your production runs, and your current assembly process. However, many manufacturers have reported cost savings of 10-30% by adopting a combination of these approaches.
2. Can I implement these strategies gradually, or do I need to make all the changes at once?
You can implement these cost-cutting strategies gradually, focusing on the areas that offer the greatest potential for savings in your specific situation. However, keep in mind that some strategies, such as optimizing PCB design for manufacturing (DFM), may require upfront effort but will yield long-term benefits.
3. How do I balance cost-cutting with maintaining high quality standards?
The key to balancing cost-cutting with quality is to focus on strategies that improve efficiency and reduce waste without compromising on the materials, processes, and standards that ensure the reliability and performance of your PCBs. Many of the strategies discussed in this article, such as DFM optimization, standardization, and effective quality control, can help you achieve this balance.
4. How can I ensure that my PCB Assembly Partners are aligned with my cost-cutting goals?
To ensure that your PCB assembly partners are aligned with your cost-cutting goals, communicate your objectives clearly and involve them in the process of identifying and implementing cost-saving strategies. Foster open and transparent relationships with your partners, and work together to find mutually beneficial solutions that reduce costs without sacrificing quality.
5. What are the potential risks of cutting PCB assembly costs too aggressively?
Cutting PCB assembly costs too aggressively can lead to several risks, including:
- Compromised product quality and reliability
- Increased likelihood of defects and rework
- Delays in production and time-to-market
- Damage to your reputation and customer relationships
To mitigate these risks, adopt a balanced approach to cost-cutting that prioritizes efficiency, quality, and long-term value over short-term savings.
In conclusion, cutting PCB assembly costs without sacrificing quality is achievable through a combination of strategic planning, process optimization, and collaboration with valued partners. By implementing the 11 strategies outlined in this article, you can streamline your assembly process, reduce expenses, and maintain the highest standards of quality, positioning your business for long-term success in the competitive world of Electronic Manufacturing.
0 Comments