1. Assess Your Requirements
Before you start searching for a PCB assembly service provider, it’s essential to assess your requirements thoroughly. Consider factors such as:
- The complexity of your PCB design
- The volume of PCBs you need
- The timeline for your project
- Your budget constraints
- Any specific certifications or standards your PCBs must adhere to
Having a clear understanding of your needs will help you narrow down your search and find a provider that can meet your expectations.
2. Look for Experience and Expertise
When evaluating PCB assembly services, it’s crucial to consider the experience and expertise of the provider. Look for companies that have been in the industry for a significant period and have a proven track record of delivering high-quality PCBs. Experienced providers are more likely to have the knowledge and skills necessary to handle complex designs and overcome any challenges that may arise during the assembly process.
Additionally, check if the provider has expertise in the specific type of PCBs you require. Some companies specialize in certain industries, such as automotive, medical, or aerospace, and may have a better understanding of the unique requirements and regulations associated with those sectors.
3. Check for Quality Control Measures
The quality of your PCBs directly impacts the performance and reliability of your end product. Therefore, it’s essential to choose a PCB assembly service provider that has strict quality control measures in place. Inquire about their quality assurance processes, such as:
- Automated Optical Inspection (AOI)
- X-ray inspection
- In-circuit testing
- Functional testing
A reputable provider will have multiple quality checkpoints throughout the assembly process to ensure that any defects or issues are caught and rectified early on. They should also be willing to provide you with detailed quality reports and documentation.
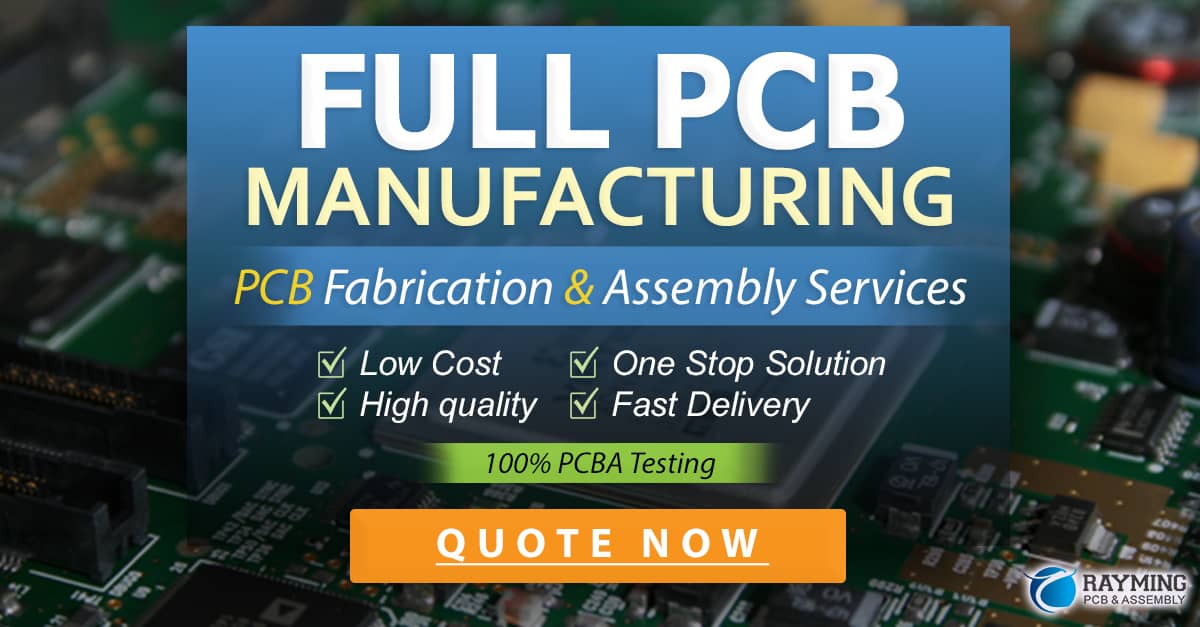
4. Consider the Manufacturing Capabilities
Different PCB assembly service providers have varying manufacturing capabilities. Some may specialize in small-scale prototyping, while others are equipped to handle high-volume production runs. Consider your current and future needs when evaluating a provider’s manufacturing capabilities.
Additionally, inquire about their equipment and technology. State-of-the-art machinery and automated processes can significantly improve the speed, accuracy, and consistency of PCB assembly. Look for providers that invest in advanced equipment and regularly upgrade their technology to stay ahead of the curve.
5. Evaluate Turnaround Time and Flexibility
In today’s fast-paced business environment, time to market is crucial. Choose a PCB assembly service provider that can deliver your PCBs within your required timeframe. Inquire about their standard turnaround times and whether they offer expedited services for urgent projects.
Furthermore, consider the provider’s flexibility in accommodating changes or modifications to your design. As your product evolves, you may need to make updates to your PCB design. A flexible provider will be able to adapt to these changes quickly and efficiently, minimizing delays and ensuring a smooth production process.
6. Look for Comprehensive Services
Choosing a PCB assembly service provider that offers comprehensive services can streamline your production process and save you time and money. Some providers offer end-to-end solutions, including:
- PCB design and layout
- Component sourcing and procurement
- PCB fabrication
- PCB assembly
- Testing and quality control
- Packaging and shipping
Working with a single provider for all your PCB needs can simplify communication, reduce the risk of errors, and ensure a more seamless production process.
7. Consider the Location and Logistics
The location of your PCB assembly service provider can have a significant impact on your project’s timeline and costs. Consider factors such as:
- Proximity to your facility or target market
- Shipping and logistics costs
- Import/export regulations and tariffs
- Time zone differences and communication challenges
While offshoring PCB assembly to countries with lower labor costs may seem attractive, it’s essential to weigh the potential risks and drawbacks. Local or nearshore providers may offer faster turnaround times, better communication, and easier quality control.
8. Evaluate Customer Support and Communication
Effective communication is key to a successful partnership with your PCB assembly service provider. Look for companies that prioritize customer support and have clear communication channels in place. Consider factors such as:
- Responsiveness to inquiries and concerns
- Availability of technical support
- Regular project updates and status reports
- Ease of communication (e.g., language barriers, time zone differences)
A provider with strong customer support and communication will be more likely to address any issues promptly and keep you informed throughout the production process.
9. Review Certifications and Standards
Depending on your industry and target market, your PCBs may need to comply with specific certifications and standards. Some common certifications and standards include:
- ISO 9001 (Quality Management)
- ISO 14001 (Environmental Management)
- UL (Underwriters Laboratories)
- IPC (Association Connecting Electronics Industries)
- RoHS (Restriction of Hazardous Substances)
- REACH (Registration, Evaluation, Authorization, and Restriction of Chemicals)
Choose a PCB assembly service provider that holds the necessary certifications and adheres to the relevant standards for your industry. This ensures that your PCBs meet the required quality and safety standards and can help you avoid potential legal and regulatory issues.
10. Consider Cost and Value
While cost is an important factor when choosing a PCB assembly service provider, it shouldn’t be the only consideration. Lower prices may be tempting, but they often come at the expense of quality, reliability, and service. Instead of focusing solely on cost, consider the overall value provided by the provider.
Look for companies that offer competitive pricing without compromising on quality. Consider factors such as:
- The provider’s reputation and track record
- The level of service and support offered
- The quality of the materials and components used
- The provider’s investment in advanced technology and equipment
Choosing a provider that offers the best value for your money will help ensure that you receive high-quality PCBs that meet your requirements and exceed your expectations.
Frequently Asked Questions (FAQ)
1. How do I know if a PCB assembly service provider is reliable?
To determine if a PCB assembly service provider is reliable, consider the following factors:
- Their experience and expertise in the industry
- Customer reviews and testimonials
- Their quality control measures and certifications
- The level of customer support and communication they provide
- Their ability to meet your project’s timeline and requirements
2. What should I look for in a PCB assembly service provider’s quality control process?
A robust quality control process should include:
- Automated Optical Inspection (AOI) to detect surface-level defects
- X-ray inspection to identify hidden defects and component placement issues
- In-circuit testing to verify the functionality of individual components
- Functional testing to ensure the overall performance of the assembled PCB
- Detailed quality reports and documentation
3. How can I ensure that my PCBs will be delivered on time?
To ensure timely delivery of your PCBs:
- Choose a provider with a proven track record of meeting deadlines
- Clearly communicate your project timeline and requirements upfront
- Consider the provider’s location and logistics capabilities
- Inquire about expedited services for urgent projects
- Maintain regular communication with the provider to stay informed of project progress
4. What certifications should I look for in a PCB assembly service provider?
The certifications you should look for depend on your industry and specific requirements. Some common certifications include:
- ISO 9001 for quality management
- ISO 14001 for environmental management
- UL for safety standards
- IPC for industry-specific standards
- RoHS and REACH for environmental compliance
5. How do I balance cost and quality when choosing a PCB assembly service provider?
To balance cost and quality:
- Prioritize providers that offer competitive pricing without compromising on quality
- Consider the overall value provided, including service, support, and expertise
- Avoid providers with significantly lower prices, as this may indicate subpar materials or processes
- Look for providers that invest in advanced technology and equipment to ensure consistent quality
- Choose a provider with a strong reputation and track record of delivering high-quality PCBs
Factor | Importance |
---|---|
Experience and Expertise | High |
Quality Control Measures | High |
Manufacturing Capabilities | Medium |
Turnaround Time and Flexibility | High |
Comprehensive Services | Medium |
Location and Logistics | Medium |
Customer Support and Communication | High |
Certifications and Standards | High |
Cost and Value | Medium |
Choosing the right PCB assembly service provider is a critical decision that can significantly impact the success of your electronic device manufacturing. By following these 10 tips and carefully evaluating potential providers based on your specific needs and requirements, you can find a partner that will deliver high-quality PCBs, provide excellent service and support, and help you bring your products to market efficiently and effectively.
Remember to prioritize experience, expertise, quality control, and customer support when making your decision, and don’t hesitate to ask questions and request documentation to ensure that the provider you choose is the best fit for your business. With the right PCB assembly service provider by your side, you can focus on innovating and growing your business, knowing that your PCBs are in capable hands.
0 Comments