Handling Hazardous Chemicals
One of the biggest disadvantages of home PCB Etching is the need to handle hazardous chemicals. The most common etchant used is ferric chloride, an acidic and corrosive solution. Ferric chloride can cause chemical burns, respiratory issues if inhaled, and eye damage. It must be used with proper protective equipment in a well-ventilated area.
Other chemicals sometimes used in the process, like hydrochloric acid, sodium hydroxide, hydrogen peroxide, and acetone, also pose health and safety risks. Mishandling any of these substances can lead to serious injury.
Proper Disposal of Chemicals
In addition to the dangers of handling the chemicals, you also need to properly dispose of used etchant and rinse water. Pouring these chemicals down the drain or into the ground is illegal and harmful to the environment. Many of the substances are toxic to wildlife.
You’ll need to collect all contaminated liquid waste and either take it to a hazardous waste disposal facility or find a company that can pick it up from you. This is an added cost and inconvenience compared to industrial PCB fabrication where disposal is handled in-house.
Inconsistent Results
Getting consistent, high-quality results with home PCB etching is very difficult. Many variables can affect the outcome, including:
- Concentration and freshness of etchant solution
- Etching time and temperature
- Thoroughness of cleaning the board beforehand
- Quality and consistency of applying the etch resist
- Rinsing and drying afterward
If any of these factors are off, you can end up with problems like incomplete etching, over-etching that eats away at traces, etchant bleeding under the resist, or unwanted copper left behind. Professional PCB manufacturers have the equipment and expertise to control these variables much more precisely.
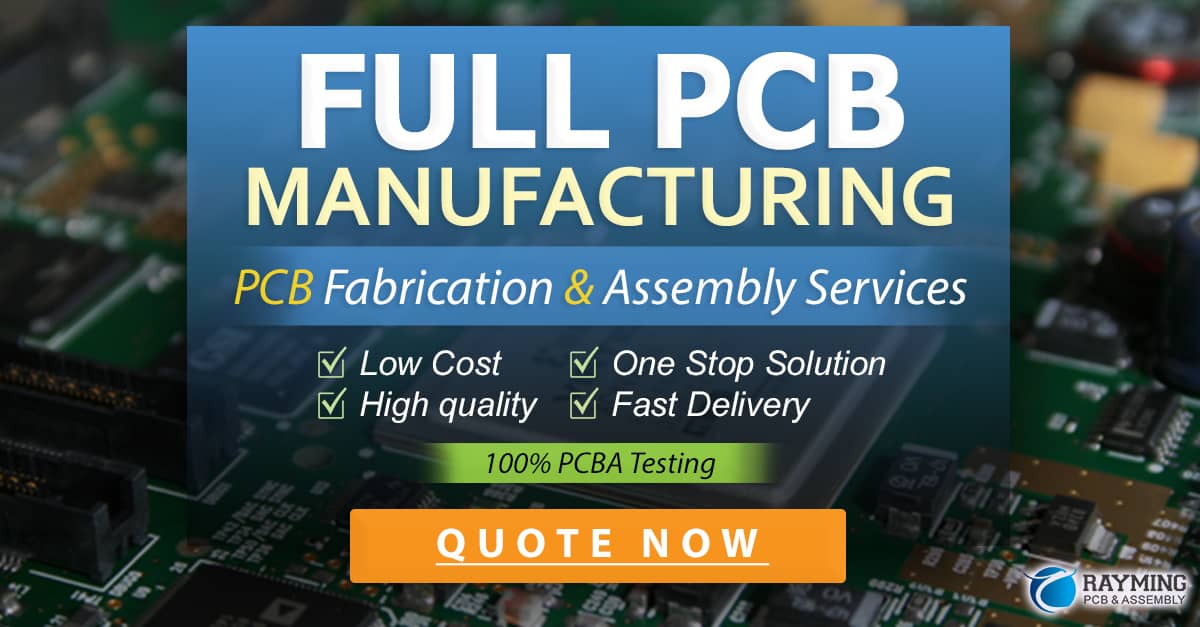
Time-Consuming Process
PCB etching, especially for double-sided or multilayer boards, is a very time-consuming process when done at home. The many steps involved include:
- Designing the PCB layout
- Printing the design onto transfer paper
- Transferring the layout to the copper clad board
- Carefully inspecting and touching up the transfer
- Allowing the etch resist to fully cure
- Preparing the etchant solution
- Etching the board for 20-60 minutes with regular agitation
- Washing the board thoroughly
- Stripping the remaining resist
- Drilling holes and cutting out the board
A single board can easily take several hours spread across multiple sessions. For more than a couple boards, this become prohibitively time-consuming compared to the rapid turnaround of professional fabrication houses.
Equipment and Setup Costs
While it’s cheaper than professional PCB fabrication for small numbers of boards, home PCB etching still requires investing in some equipment and supplies:
Item | Approximate Cost |
---|---|
Laser printer for transfer paper | $50 – $200 |
Laminator for heat transfer | $30 – $100 |
Etchant tank and heater | $40 – $100 |
Drill press for holes | $70 – $200 |
Protective equipment (goggles, gloves, apron, respirator) | $70+ |
Copper clad boards, etchant, resist, transfer paper, drill bits | $50+ |
You’re looking at $300-$700+ in startup costs for a basic setup, plus ongoing material costs. This only makes sense if you’ll be making a lot of PCBs and have the time to invest in the process. For occasional projects, it’s usually more economical to have them made by a PCB fab.
Lack of Advanced Features
Modern PCBs often incorporate advanced features that are extremely difficult or impossible to do with home etching, such as:
- Plated through-holes
- Solder mask and silkscreen
- Vias
- Fine pitch traces and spacing
- Controlled impedance
- Multiple copper weights
Without these capabilities, the types of PCBs you can make are limited. Most digital designs with SMT components require professionally made boards to function correctly and reliably. Home-etched boards are better suited to simpler through-hole designs.
Limited Board Size
The size of boards you can make at home is constrained by the size of your etching tank and the size of copper clad blanks you can source. Most home setups are limited to around 100x200mm, with 200x300mm about the maximum achievable.
If your PCB design exceeds these dimensions, you’ll need to have it professionally made or panelize it into multiple smaller boards that are physically connected. The latter requires additional design considerations and assembly steps.
Single or Double Layer Only
Home PCB etching setups are realistically limited to single or double layer boards. Multilayer boards with internal layers and blind/buried vias require precise alignment, lamination, drilling, and plating that is infeasible outside of a professional fabrication facility.
For many modern digital designs that are pushing the limits of board space, often the only solution is a 4+ layer board. If your project reaches this level of complexity, home etching is no longer an option.
Potentially Unreliable
Even if you manage to produce decent looking boards through home etching, there are several potential reliability issues to consider:
- Incomplete etching can leave shorts between traces
- Over-etching can result in fragile, thin, or broken traces
- Insufficiently cleaned boards may corrode or fail over time
- Etchant bleeding under resist can cause intermittent issues
- Connecting multiple boards for larger designs introduces potential failure points
For any kind of product development or commercial project, this level of unreliability is unacceptable. Professionally manufactured PCBs go through rigorous electrical testing, inspection, and quality control to ensure high reliability. This is very difficult to replicate at home.
Requires Skill and Experience
Finally, making high quality PCBs through etching requires a non-trivial amount of skill and experience to master. There is a big learning curve to getting all the steps consistently correct:
- Properly sizing and laying out traces, pads, and isolation
- Choosing the right transfer method and getting a perfect print
- Correctly developing and etching the resist without errors
- Drilling holes cleanly and accurately
- Troubleshooting problems and knowing how to adjust the process
It can take dozens of attempts and a lot of practice to become proficient at the process. For a beginner, expect a high failure rate and a lot of wasted time and materials. Combined with the various disadvantages above, this barrier to entry leads many to conclude that home PCB etching simply isn’t worth it.
FAQ
What are the main disadvantages of etching PCBs at home?
The main disadvantages are:
1. Handling dangerous chemicals
2. Waste disposal issues
3. Inconsistent quality
4. Very time consuming
5. Requires equipment investment
6. Can’t do advanced features like plating
7. Limited to smaller boards
8. Only single or double layer
9. Potentially unreliable results
10. Steep learning curve
Is it cheaper to etch PCBs yourself or have them made?
For small numbers of simple boards it can be cheaper to etch them yourself, but there are high initial equipment and setup costs. For anything more than a few boards or complex multilayer designs, it’s usually more economical to use a professional PCB fabrication service.
How difficult is it to get good results etching boards at home?
Getting consistently good results is quite difficult and requires a lot of practice to master the process. Many things can go wrong and ruin boards along the way. Expect a high failure rate and frustration until you gain a fair bit of experience.
What is the most hazardous part of etching circuit boards?
Handling the concentrated acidic etchant solution, most commonly ferric chloride, which can cause chemical burns and respiratory damage. It must be used cautiously with proper protective gear. Disposal of the used etchant is also challenging as it is toxic waste that can’t be poured down the drain.
Is home PCB etching suitable for producing commercial products?
No, home etched PCBs are generally not reliable enough for commercial products or production use. The process is too inconsistent and prone to failures. It’s better suited for one-off prototypes and personal hobby projects where some unreliability is acceptable. Professional PCB fabrication is a must for commercial use.
While enticing as a way to quickly make your own circuit boards, etching PCBs at home has many significant drawbacks and limitations. From the hazardous chemicals and tricky process to the inconsistent quality and steep learning curve, there’s a lot that can go wrong. For any kind of serious or commercial use, professionally manufactured PCBs are a better choice. But if you enjoy the challenge and can accept the limitations, home PCB etching can be a rewarding hobby to pursue.
0 Comments