What is Rapid PCB Prototyping?
Rapid PCB prototyping is the process of quickly designing, fabricating, and testing printed circuit boards. This process allows engineers and designers to iterate on their designs rapidly, making necessary changes and improvements before finalizing the product for mass production. Rapid PCB prototyping typically involves the use of specialized software, equipment, and materials to create functional prototypes in a matter of days or even hours.
The Benefits of In-House Rapid PCB Prototyping
- Faster Iteration Cycles
- Cost Savings
- Improved Quality Control
- Enhanced Collaboration
- Increased Flexibility
Faster Iteration Cycles
One of the primary benefits of in-house rapid PCB prototyping is the ability to iterate on designs quickly. By having the necessary equipment and expertise in-house, companies can create and test prototypes in a matter of days, rather than weeks or months when outsourcing the process. This faster iteration cycle allows for more experimentation and refinement, ultimately leading to better final products.
Traditional Prototyping | Rapid PCB Prototyping |
---|---|
4-6 weeks | 1-5 days |
Cost Savings
In-house rapid PCB prototyping can also lead to significant cost savings for companies. Outsourcing the prototyping process can be expensive, especially when multiple iterations are required. By bringing the process in-house, companies can eliminate the markup associated with external vendors and reduce shipping costs. Additionally, the ability to catch and correct errors early in the design process can prevent costly mistakes down the line.
Cost Factor | Traditional Prototyping | Rapid PCB Prototyping |
---|---|---|
Vendor Markup | 20-50% | 0% |
Shipping Costs | $50-$200 per shipment | $0 |
Error Correction Costs | High | Low |
Improved Quality Control
When prototyping is done in-house, companies have greater control over the quality of their PCBs. They can closely monitor the fabrication process, ensuring that the boards meet their exact specifications and standards. This level of quality control is particularly important for industries with stringent reliability requirements, such as aerospace, medical devices, and automotive.
Enhanced Collaboration
In-house rapid PCB prototyping can also foster enhanced collaboration between different teams within an organization. When designers, engineers, and manufacturers work together in close proximity, they can communicate more effectively and resolve issues quickly. This collaboration can lead to more innovative designs and faster problem-solving.
Increased Flexibility
Finally, in-house rapid PCB prototyping provides companies with increased flexibility to adapt to changing market demands or customer requirements. With the ability to quickly modify and test designs, companies can respond to new opportunities or challenges without being dependent on external suppliers.
Implementing In-House Rapid PCB Prototyping
To successfully implement in-house rapid PCB prototyping, companies need to invest in the right equipment, software, and personnel. Some key considerations include:
-
PCB Design Software: Choose a software package that suits your company’s needs and is compatible with your manufacturing equipment.
-
Prototyping Equipment: Invest in high-quality equipment for PCB fabrication, such as CNC machines, 3D printers, and reflow ovens.
-
Skilled Personnel: Hire or train employees with expertise in PCB design, fabrication, and testing.
-
Dedicated Workspace: Allocate a dedicated space for your prototyping lab, with proper ventilation and safety measures in place.
-
Standardized Processes: Develop standardized processes for PCB design, fabrication, and testing to ensure consistency and quality.
Real-World Examples
Many companies across various industries have successfully implemented in-house rapid PCB prototyping and reaped the benefits. Here are a few examples:
-
Tesla: The electric vehicle manufacturer uses in-house rapid PCB prototyping to quickly iterate on designs for their advanced battery and powertrain systems.
-
Apple: The tech giant has invested heavily in in-house prototyping capabilities, allowing them to develop and test new products like the iPhone and Apple Watch more efficiently.
-
GE Healthcare: The medical device company uses in-house rapid PCB prototyping to develop and refine their diagnostic imaging equipment, ensuring the highest levels of quality and reliability.
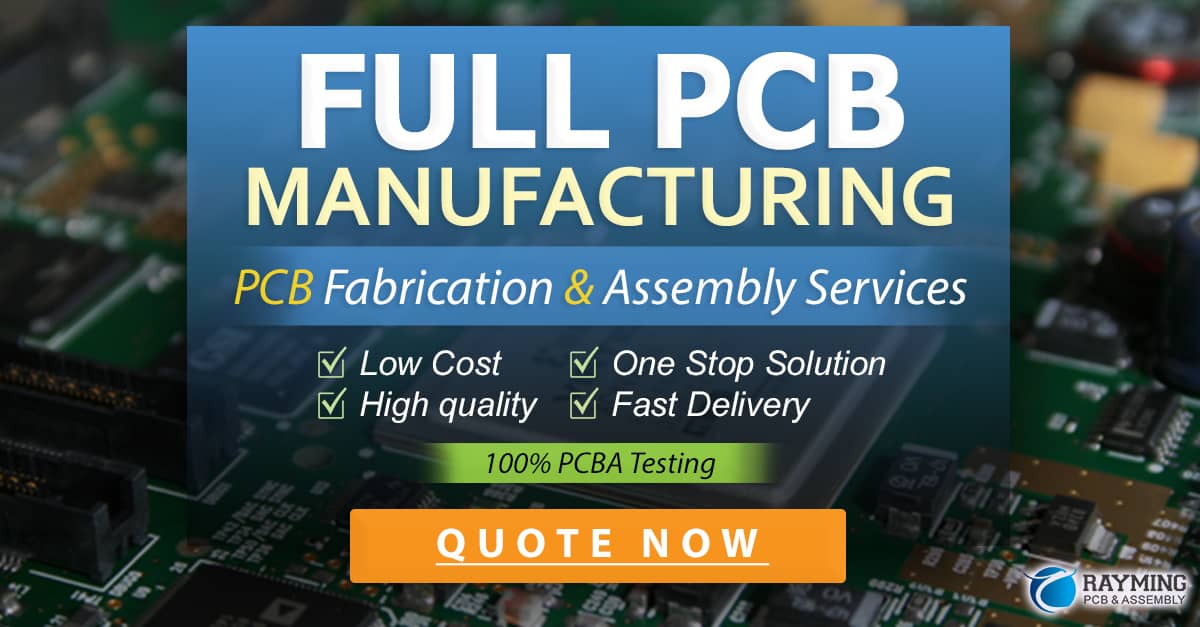
Frequently Asked Questions (FAQ)
1. What is the typical turnaround time for in-house rapid PCB prototyping?
With in-house rapid PCB prototyping, companies can typically create and test prototypes within 1-5 days, depending on the complexity of the design.
2. Is in-house rapid PCB prototyping suitable for all companies?
While in-house rapid PCB prototyping can benefit many companies, it may not be suitable for all. Small businesses or those with limited resources may find it more cost-effective to outsource their prototyping needs.
3. What are the key pieces of equipment needed for in-house rapid PCB prototyping?
The key pieces of equipment for in-house rapid PCB prototyping include PCB design software, CNC machines, 3D printers, and reflow ovens.
4. How does in-house rapid PCB prototyping impact time-to-market?
By enabling faster iteration cycles and reducing dependence on external suppliers, in-house rapid PCB prototyping can significantly reduce time-to-market for new products.
5. What skills are required for personnel involved in in-house rapid PCB prototyping?
Personnel involved in in-house rapid PCB prototyping should have expertise in PCB design, fabrication, and testing. They should be familiar with the relevant software, equipment, and processes.
Conclusion
In-house rapid PCB prototyping has become a critical capability for companies looking to innovate and stay competitive in today’s fast-paced technology landscape. By enabling faster iteration cycles, cost savings, improved quality control, enhanced collaboration, and increased flexibility, in-house prototyping can significantly accelerate product development and time-to-market.
To successfully implement in-house rapid PCB prototyping, companies must invest in the right equipment, software, and personnel, as well as develop standardized processes for design, fabrication, and testing. While not suitable for all businesses, those that can effectively leverage in-house prototyping capabilities stand to gain a significant advantage in their respective markets.
As technology continues to evolve at a rapid pace, the importance of in-house rapid PCB prototyping will only continue to grow. Companies that embrace this capability will be well-positioned to drive innovation, respond to changing market demands, and deliver cutting-edge products to their customers.
0 Comments