Understanding Fiducials and Their Importance in PCB Manufacturing
Fiducials, also known as Fiducial Markers or alignment marks, are small, precise reference points placed on printed circuit boards (PCBs) to ensure accurate alignment during the manufacturing process. These markers play a crucial role in the automated assembly of PCBs, enabling machines to accurately place components and conduct inspections. In this article, we will explore the importance of fiducials, their placement on PCBs, and best practices for incorporating them into your PCB design.
What are Fiducials?
Fiducials are small, round, or cross-shaped copper pads placed on the surface of a PCB. They serve as reference points for machine vision systems used in automated PCB-Assembly-process-techniques-and-best-practices/”>PCB Assembly processes, such as solder paste application, component placement, and inspection. By providing a consistent and accurate reference, fiducials help machines align the PCB correctly and place components with high precision.
The Role of Fiducials in PCB Manufacturing
In modern PCB manufacturing, automated assembly processes rely heavily on machine vision systems to ensure speed, accuracy, and consistency. These systems use cameras to locate and align the PCB based on the position of the fiducials. The fiducials act as a common reference point for all the machines involved in the assembly process, allowing them to work in harmony and maintain precise alignment throughout the manufacturing stages.
Some of the key benefits of using fiducials in PCB manufacturing include:
- Improved accuracy: Fiducials enable machines to place components with high precision, reducing the risk of misalignment and assembly errors.
- Increased efficiency: Automated assembly processes that utilize fiducials are faster and more efficient than manual methods, leading to higher production rates and lower costs.
- Enhanced quality control: Fiducials serve as reference points for automated optical inspection (AOI) systems, which can quickly detect and report any alignment issues or defects in the assembLED PCB.
Fiducial placement Guidelines
Quantity and Location
When placing fiducials on a PCB, it is essential to follow best practices to ensure optimal performance and compatibility with automated assembly processes. Here are some guidelines for the quantity and location of fiducials:
-
Use a minimum of three fiducials: Three fiducials are typically required to establish a reliable reference system for the PCB. This allows the machine vision system to accurately determine the PCB’s orientation and position in three-dimensional space.
-
Place fiducials in non-symmetrical positions: To avoid ambiguity in PCB orientation, place the fiducials in non-symmetrical positions. This ensures that the machine vision system can uniquely identify the correct orientation of the board.
-
Locate fiducials near the corners of the PCB: Placing fiducials near the corners of the board provides a wide baseline for the machine vision system, enhancing the accuracy of alignment and component placement.
-
Keep fiducials away from edges and components: Maintain a minimum distance between fiducials and the edges of the PCB or any nearby components. This clearance helps prevent damage to the fiducials during handling and ensures that the machine vision system can easily detect them.
Size and Shape
The size and shape of fiducials are crucial factors in ensuring their effectiveness. Consider the following guidelines when designing fiducials for your PCB:
-
Use a standard size: Fiducials typically range from 1.0 mm to 2.0 mm in diameter. Consult with your PCB manufacturer to determine the optimal size for your specific assembly process and equipment.
-
Maintain consistent size across fiducials: Ensure that all fiducials on the PCB are of the same size. Consistency in size helps the machine vision system accurately identify and locate the fiducials.
-
Use a simple shape: Round or cross-shaped fiducials are the most common and preferred shapes. These simple shapes are easily recognizable by machine vision systems and minimize the risk of confusion with other features on the PCB.
-
Avoid using complex shapes: Complex shapes, such as squares or triangles, can be more difficult for machine vision systems to identify accurately. Stick to simple, standard shapes for optimal performance.
Material and Finish
The material and finish of fiducials can impact their visibility and compatibility with machine vision systems. Consider the following guidelines:
-
Use copper pads: Fiducials are typically created using copper pads on the PCB surface. Copper provides good contrast against the PCB substrate, making the fiducials easily detectable by machine vision systems.
-
Apply a soldermask opening: Create a soldermask opening around the fiducial to enhance its visibility. The soldermask opening should be slightly larger than the copper pad, exposing the entire fiducial surface.
-
Avoid using soldermask or silkscreen over fiducials: Do not cover fiducials with soldermask or silkscreen, as this can interfere with the machine vision system’s ability to detect and locate the fiducials accurately.
-
Consider the finish: The surface finish of the fiducial can affect its visibility. Bare copper or ENIG (Electroless Nickel Immersion Gold) finishes are commonly used for fiducials, as they provide good contrast and compatibility with machine vision systems.
Best Practices for Incorporating Fiducials in PCB Design
Collaborate with Your PCB Manufacturer
When incorporating fiducials into your PCB design, it is essential to collaborate with your PCB manufacturer. They can provide valuable insights and recommendations based on their specific assembly processes and equipment. Discuss the following aspects with your manufacturer:
- Fiducial size and shape requirements
- Recommended location and quantity of fiducials
- Compatibility with their machine vision systems
- Any specific guidelines or constraints related to their assembly process
By working closely with your PCB manufacturer, you can ensure that your fiducial design is optimized for their assembly process, minimizing the risk of issues and delays.
Consider the PCB Panelization
If your PCB design will be panelized for manufacturing, consider the placement of fiducials in the context of the entire panel. In addition to the fiducials on individual PCBs, you may need to include panel-level fiducials to assist with the depanelization process. Consult with your PCB manufacturer to determine the best approach for incorporating panel-level fiducials.
Use PCB Design Software with Fiducial Support
When creating your PCB design, use PCB design software that supports the placement and management of fiducials. Many popular PCB design tools, such as Altium Designer, Eagle, and KiCad, offer features specifically for fiducial placement and management. These tools can help you adhere to best practices and ensure that your fiducials are correctly positioned and sized.
Conduct a Design Review
Before finalizing your PCB design, conduct a thorough design review to ensure that your fiducials are correctly placed and meet all the necessary guidelines. This review should include:
- Verifying the quantity, location, and spacing of fiducials
- Checking the size and shape of fiducials
- Ensuring that fiducials are free from soldermask and silkscreen
- Confirming compatibility with your PCB manufacturer’s requirements
By conducting a design review, you can catch and address any issues early in the process, avoiding potential problems during manufacturing.
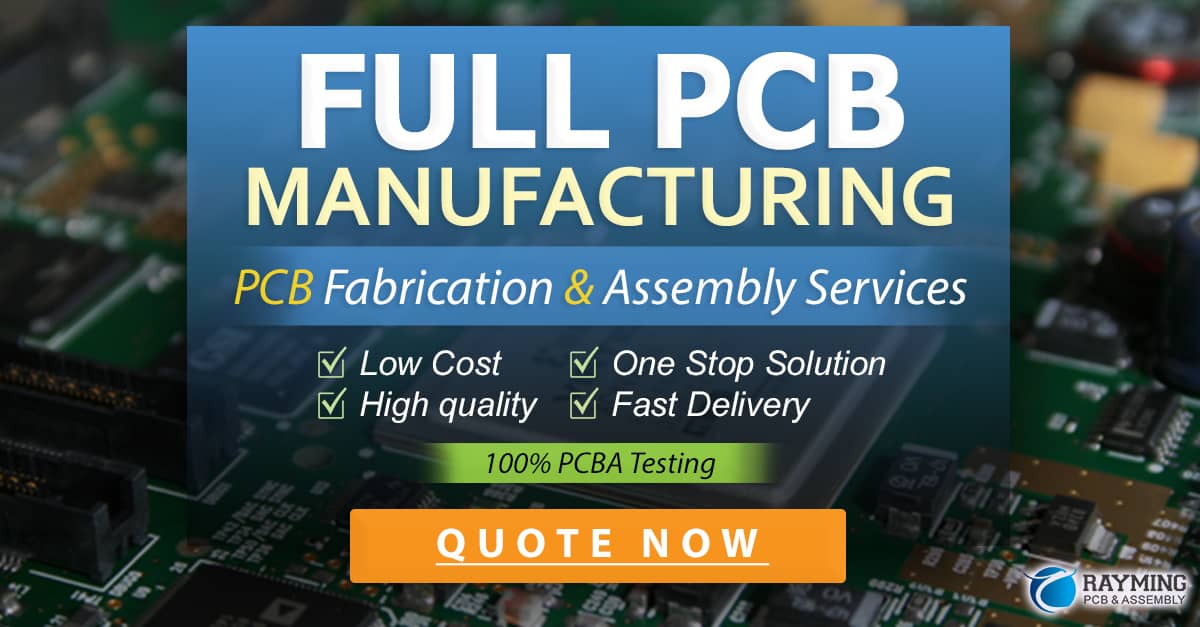
FAQs
1. What happens if I don’t include fiducials on my PCB?
Without fiducials, automated assembly processes may struggle to accurately align and place components on your PCB. This can lead to misalignment, component placement errors, and reduced manufacturing efficiency. In some cases, the absence of fiducials may even prevent the automated assembly of your PCB altogether.
2. Can I use different sizes or shapes for fiducials on the same PCB?
It is generally recommended to use consistent sizes and shapes for all fiducials on a single PCB. Consistency helps the machine vision system accurately identify and locate the fiducials, minimizing the risk of errors or confusion. If you must use different sizes or shapes, consult with your PCB manufacturer to ensure compatibility with their assembly process.
3. How do I determine the optimal size for fiducials on my PCB?
The optimal size for fiducials depends on various factors, such as the specific requirements of your PCB manufacturer’s assembly process and equipment. Generally, fiducials range from 1.0 mm to 2.0 mm in diameter. It is best to consult with your PCB manufacturer to determine the most suitable size for your project.
4. Can I place fiducials on both sides of the PCB?
Yes, you can place fiducials on both sides of the PCB if your design requires components to be placed on both sides. In such cases, ensure that the fiducials on each side meet the placement guidelines and are not obstructed by components or other features on the opposite side.
5. What should I do if my PCB manufacturer’s fiducial requirements differ from general guidelines?
Always prioritize your PCB manufacturer’s specific requirements for fiducials. If their guidelines differ from general best practices, follow their recommendations to ensure compatibility with their assembly process and equipment. Your PCB manufacturer has the expertise and knowledge specific to their production capabilities, and adhering to their requirements can help prevent issues and delays in the manufacturing process.
Conclusion
Fiducials play a critical role in the accurate and efficient automated assembly of PCBs. By understanding the importance of fiducials and following best practices for their placement and design, you can ensure that your PCBs are compatible with automated assembly processes and minimize the risk of manufacturing issues.
Remember to collaborate with your PCB manufacturer, consider PCB panelization, use PCB design software with fiducial support, and conduct thorough design reviews to optimize your fiducial placement. By paying close attention to these details, you can streamline your PCB manufacturing process and achieve high-quality, reliable results.
0 Comments