Understanding the Importance of PCB Design for Assembly
PCB design for assembly is critical because it directly impacts the manufacturability, reliability, and cost-effectiveness of the final product. A well-designed PCB considers the assembly process requirements, reducing the likelihood of errors, delays, and additional costs during production.
Key Factors in PCB Design for Assembly
- Component placement
- Routing and spacing
- Solder mask and silkscreen
- Panelization
- Design for testing
PCB Assembly Techniques
There are two primary PCB assembly techniques:
- Through-hole mounting (THM)
- Surface mount technology (SMT)
Through-hole Mounting (THM)
THM involves inserting component leads through drilled holes in the PCB and soldering them to pads on the opposite side. This technique is suitable for larger components and provides stronger mechanical connections.
Surface Mount Technology (SMT)
SMT involves placing components directly onto the PCB surface and soldering them to pads. This technique accommodates smaller components and allows for higher component density, resulting in more compact designs.
PCB design guidelines for Assembly
Component Placement
Proper component placement is essential for efficient assembly and optimal PCB performance. Consider the following guidelines:
- Group related components together
- Place components to minimize routing complexity
- Ensure adequate spacing between components for soldering
- Orient components consistently for automated assembly
- Place connectors and large components near the board edges
Routing and Spacing
Routing and spacing guidelines ensure that traces are correctly connected and there is sufficient space for assembly processes.
- Maintain appropriate trace width and spacing based on the current requirements and PCB manufacturing capabilities
- Avoid sharp angles in traces to minimize signal reflections
- Use via-in-pad design when necessary to save space
- Provide sufficient clearance around mounting holes and board edges
Solder Mask and Silkscreen
Solder mask and silkscreen layers provide insulation and component identification, respectively.
- Ensure solder mask openings are appropriately sized for the pads
- Provide clear and concise component identifiers on the silkscreen
- Avoid placing silkscreen on top of pads or traces
- Use contrasting colors for silkscreen and solder mask
Panelization
Panelization involves grouping multiple PCBs into a single panel for efficient manufacturing and assembly.
- Include breakaway tabs or mousebites for easy depanelization
- Provide sufficient spacing between individual boards
- Add fiducial markers for automated assembly alignment
- Consider the panelization requirements of your PCB manufacturer
Design for Testing
Designing for testability ensures that the assembled PCB can be easily tested and debugged.
- Provide test points for critical signals
- Include built-in self-test (BIST) features when applicable
- Ensure access to test pads and connectors
- Consider using boundary scan testing for complex designs
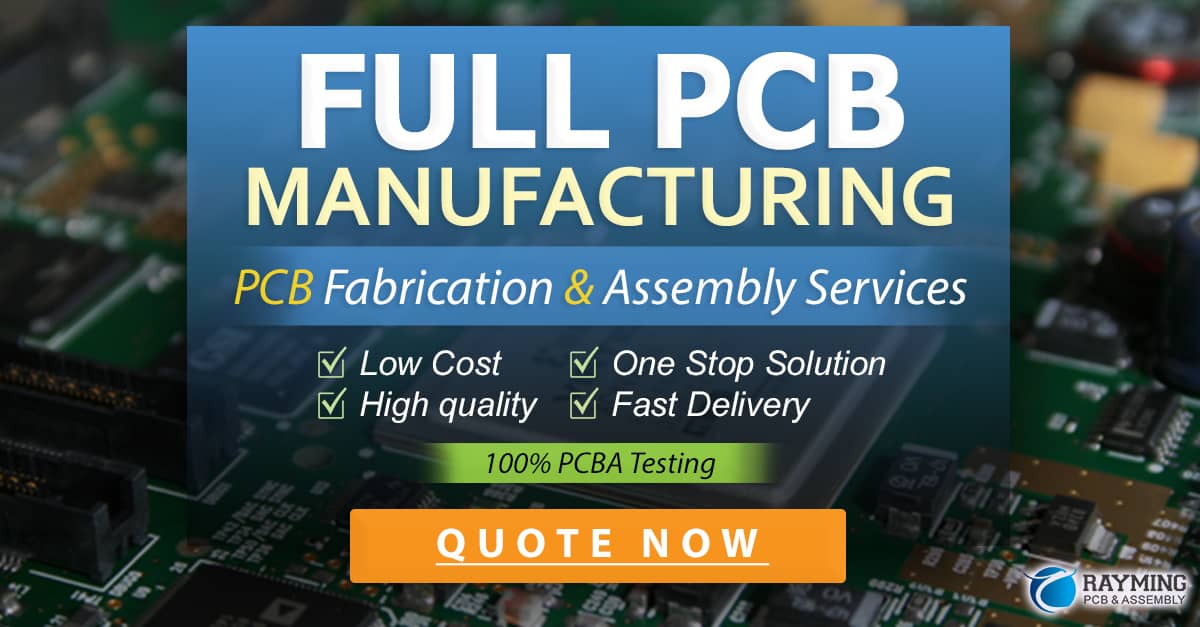
PCB Design Software and Tools
There are numerous PCB design software and tools available to streamline the design process and ensure adherence to assembly guidelines.
Software / Tool | Description |
---|---|
Altium Designer | A comprehensive PCB design software with advanced features and extensive libraries |
KiCad | A free and open-source PCB design software with a growing user community |
Eagle | A popular PCB design software known for its ease of use and extensive component libraries |
Cadence OrCAD | A powerful PCB design software with advanced simulation and analysis capabilities |
Mentor Graphics PADS | A PCB design software suite that offers a range of tools for design, simulation, and manufacturing |
These software tools offer features such as design rule checking (DRC), component libraries, and automated routing to help designers create PCBs that are optimized for assembly.
Collaborating with PCB Manufacturers and Assembly Houses
Effective communication and collaboration with PCB manufacturers and assembly houses are essential for successful PCB design and assembly.
- Provide complete and accurate design files, including Gerber files, drill files, and bill of materials (BOM)
- Discuss any special requirements or constraints with the manufacturer early in the design process
- Request design for manufacturing (DFM) feedback from the manufacturer to identify potential issues
- Maintain open communication throughout the manufacturing and assembly process to address any concerns promptly
Frequently Asked Questions (FAQ)
1. What is the difference between through-hole mounting and surface mount technology?
Through-hole mounting involves inserting component leads through drilled holes in the PCB and soldering them to pads on the opposite side. Surface mount technology involves placing components directly onto the PCB surface and soldering them to pads. SMT accommodates smaller components and allows for higher component density.
2. Why is component placement important in PCB design for assembly?
Proper component placement ensures efficient assembly, minimizes routing complexity, and optimizes PCB performance. Grouping related components, ensuring adequate spacing, and orienting components consistently facilitates automated assembly processes.
3. What is the purpose of solder mask and silkscreen layers in PCB design?
Solder mask provides insulation between conductive parts of the PCB, while silkscreen layers offer component identification and orientation information. These layers help ensure proper assembly and ease of maintenance.
4. How does panelization help in PCB assembly?
Panelization involves grouping multiple PCBs into a single panel, which allows for efficient manufacturing and assembly. It reduces handling time, minimizes material waste, and enables the use of automated assembly equipment.
5. What are some key considerations when designing for PCB testability?
Designing for testability involves providing test points for critical signals, including built-in self-test features when applicable, ensuring access to test pads and connectors, and considering boundary scan testing for complex designs. These measures facilitate easier testing and debugging of the assembled PCB.
Conclusion
PCB design for assembly is a critical aspect of electronic product development that directly impacts the manufacturability, reliability, and cost-effectiveness of the final product. By understanding the importance of assembly techniques, following design guidelines, utilizing PCB design software and tools, and collaborating effectively with manufacturers and assembly houses, designers can create PCBs that are optimized for assembly and ensure the success of their electronic products.
0 Comments