Introduction to PCB Design and Manufacturing
Printed Circuit Board (PCB) design and manufacturing is a crucial process in the creation of electronic devices. PCBs are the backbone of modern electronics, connecting and supporting various components to enable the desired functionality. Understanding the fundamentals of PCB design and manufacturing is essential for anyone involved in the electronics industry, from engineers and designers to manufacturers and customers.
In this comprehensive article, we will delve into the key aspects of PCB Design Manufacturing, covering topics such as PCB types, design considerations, manufacturing processes, and frequently asked questions.
Types of PCBs
PCBs can be categorized based on various factors, such as the number of layers, material, and manufacturing process. Let’s explore the different types of PCBs:
Single-Layer PCBs
Single-layer PCBs, also known as single-sided PCBs, have conductive traces on only one side of the board. They are the simplest and most cost-effective type of PCB, suitable for basic electronic projects and low-density designs.
Double-Layer PCBs
Double-layer PCBs, or double-sided PCBs, have conductive traces on both sides of the board. They offer higher component density and more complex routing compared to single-layer PCBs. Double-layer PCBs are commonly used in a wide range of electronic devices.
Multi-Layer PCBs
Multi-layer PCBs consist of three or more conductive layers, with insulating layers sandwiched between them. They provide even higher component density and more complex routing capabilities. Multi-layer PCBs are used in advanced electronic systems, such as smartphones, computers, and aerospace applications.
PCB Type | Layers | Complexity | Cost |
---|---|---|---|
Single-Layer | 1 | Low | Low |
Double-Layer | 2 | Medium | Medium |
Multi-Layer | 3+ | High | High |
Rigid PCBs
Rigid PCBs are the most common type of PCBs, made from a solid substrate material, such as FR-4. They provide excellent mechanical stability and are suitable for a wide range of applications.
Flexible PCBs
Flexible PCBs, or flex PCBs, are made from flexible materials, such as polyimide. They can bend and conform to various shapes, making them ideal for applications with limited space or requiring flexibility, such as wearable electronics and cable assemblies.
Rigid-Flex PCBs
Rigid-flex PCBs combine the features of both rigid and flexible PCBs. They consist of rigid sections connected by flexible sections, allowing for 3D configurations and improved reliability in applications with high vibration or mechanical stress.
PCB Design Considerations
Designing a PCB involves several key considerations to ensure optimal performance, reliability, and manufacturability. Let’s explore some crucial aspects of PCB design:
Schematic Design
The first step in PCB design is creating a schematic diagram that represents the electrical connections and components of the circuit. The schematic should be clear, well-organized, and follow industry standards for symbols and naming conventions.
Component Selection
Selecting the right components is crucial for the success of a PCB design. Factors to consider include component availability, cost, performance, and compatibility with the PCB manufacturing process. It’s essential to choose components that meet the design requirements and are readily available from reliable suppliers.
PCB Layout
Once the schematic is finalized, the next step is to create the PCB layout. The layout determines the physical placement of components and the routing of traces on the board. Key considerations in PCB layout include:
- Component placement for optimal signal integrity and thermal management
- Trace width and spacing for impedance control and signal integrity
- Power and ground plane design for efficient current distribution
- Electromagnetic compatibility (EMC) and interference (EMI) mitigation techniques
Design for Manufacturing (DFM)
Designing a PCB with manufacturability in mind is crucial for ensuring a smooth and cost-effective production process. DFM guidelines include:
- Adherence to minimum feature sizes, such as trace width and spacing
- Proper component footprint design and pad sizing
- Clearance and spacing requirements for assembly and testing
- Consideration of manufacturing tolerances and process capabilities
Simulation and Verification
Before sending a PCB design for manufacturing, it’s essential to perform simulations and verifications to catch any potential issues early in the design process. This includes:
- Signal integrity simulations to ensure proper signal transmission and minimize crosstalk
- Thermal simulations to identify hot spots and ensure adequate heat dissipation
- Design rule checks (DRC) to verify compliance with manufacturing constraints
- Electrical rule checks (ERC) to identify potential short circuits or open connections
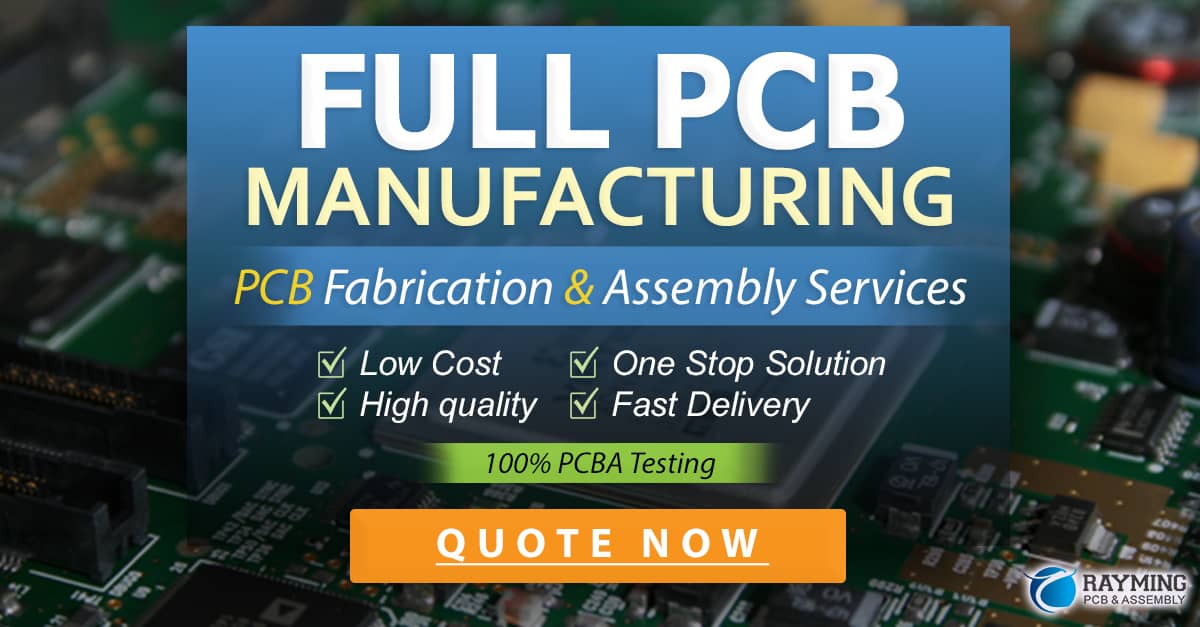
PCB Manufacturing Process
Once the PCB design is finalized and verified, it moves into the manufacturing phase. Let’s explore the key steps involved in PCB manufacturing:
PCB Fabrication
PCB fabrication involves the following steps:
-
Material Selection: The appropriate substrate material, such as FR-4, is selected based on the design requirements and application.
-
Copper Cladding: The substrate is coated with a thin layer of copper on one or both sides, depending on the PCB type.
-
Drilling: Holes are drilled into the substrate for through-hole components and vias.
-
Patterning: The desired circuit pattern is transferred onto the copper layer using photolithography and etching processes.
-
Lamination: For multi-layer PCBs, multiple layers are aligned and bonded together under high pressure and temperature.
-
Surface Finishing: A protective surface finish, such as HASL (Hot Air Solder Leveling) or ENIG (Electroless Nickel Immersion Gold), is applied to the exposed copper to prevent oxidation and improve solderability.
PCB Assembly
After fabrication, the PCB undergoes the assembly process, which involves:
-
Solder Paste Application: Solder paste is applied to the pads on the PCB using a stencil or screen printing process.
-
Component Placement: Surface mount (SMT) and through-hole (THT) components are placed onto the PCB using automated pick-and-place machines or manual assembly.
-
Reflow Soldering: The PCB is heated in a reflow oven, causing the solder paste to melt and form a permanent connection between the components and the PCB.
-
Inspection and Testing: The assembled PCB undergoes visual inspection and electrical testing to ensure proper functionality and quality.
Manufacturing Step | Description |
---|---|
PCB Fabrication | Creating the bare PCB substrate with the desired circuit pattern |
PCB Assembly | Populating the PCB with components and soldering them in place |
Frequently Asked Questions (FAQ)
1. What is the difference between PCB design and PCB layout?
PCB design encompasses the entire process of creating a functional PCB, including schematic design, component selection, and layout. PCB layout specifically refers to the physical arrangement of components and routing of traces on the board.
2. How long does it take to manufacture a PCB?
The lead time for PCB manufacturing varies depending on the complexity of the design, the chosen manufacturer, and the production volume. Typically, PCB fabrication can take anywhere from a few days to several weeks, while assembly may take an additional few days to a week.
3. What are the most common PCB materials?
The most common PCB substrate material is FR-4, a glass-reinforced epoxy laminate. Other materials include polyimide for flexible PCBs, high-frequency laminates for RF applications, and metal core PCBs for enhanced thermal management.
4. What is the minimum feature size in PCB manufacturing?
The minimum feature size, such as trace width and spacing, depends on the PCB manufacturer’s capabilities and the chosen fabrication technology. Typically, standard PCB manufacturing can achieve trace widths and spacing down to 0.1 mm (4 mil), while advanced processes can go even smaller.
5. How can I ensure the quality of my PCB design and manufacturing?
To ensure the quality of your PCB design and manufacturing, follow these best practices:
- Adhere to industry standards and guidelines for PCB design
- Choose reputable component suppliers and PCB manufacturers
- Perform thorough simulations and verifications before manufacturing
- Implement a robust quality control process, including inspections and testing
- Communicate clearly with your PCB manufacturer and provide comprehensive documentation
Conclusion
PCB design manufacturing is a complex and multi-faceted process that requires careful consideration of various factors, from design and component selection to manufacturing processes and quality control. By understanding the fundamentals of PCB design and manufacturing, you can make informed decisions and ensure the success of your electronic projects.
As technology advances and the demand for more complex and compact electronic devices grows, staying up-to-date with the latest trends and best practices in PCB design manufacturing becomes increasingly important. By continually expanding your knowledge and collaborating with experienced professionals, you can navigate the challenges and opportunities in this dynamic field.
0 Comments