Introduction to Medical PCB Standards
Medical devices are critical components in the healthcare industry, and printed circuit boards (PCBs) play a vital role in their functionality and reliability. To ensure the safety and effectiveness of medical devices, strict standards and regulations have been established for the design, manufacturing, and testing of medical PCBs. These standards and regulations are set by various organizations, including the International Organization for Standardization (ISO), the International Electrotechnical Commission (IEC), and the U.S. Food and Drug Administration (FDA).
The Importance of Medical PCB Standards
Medical PCB standards are essential for several reasons:
-
Patient Safety: Medical devices are used to diagnose, treat, and monitor patients. Any malfunction or failure of these devices can have serious consequences, including injury or even death. Medical PCB standards ensure that PCBs used in medical devices are reliable, safe, and effective.
-
Regulatory Compliance: Medical device manufacturers must comply with various regulations set by regulatory bodies such as the FDA. Adherence to medical PCB standards helps manufacturers meet these regulatory requirements and avoid costly penalties or product recalls.
-
Quality Assurance: Medical PCB standards provide guidelines for design, manufacturing, and testing processes, ensuring that PCBs meet the highest quality standards. This helps to minimize defects, improve reliability, and extend the lifespan of medical devices.
Key Medical PCB Standards and Regulations
Several standards and regulations govern the design, manufacturing, and testing of medical PCBs. Some of the most important ones include:
IPC Standards
The Association Connecting Electronics Industries (IPC) is a global trade association that develops standards for the electronic interconnect industry. Several IPC standards are relevant to medical PCBs:
Standard | Description |
---|---|
IPC-A-600 | Acceptability of Printed Boards |
IPC-6012 | Qualification and Performance Specification for Rigid Printed Boards |
IPC-6013 | Qualification and Performance Specification for Flexible Printed Boards |
IPC-6018 | Microwave End Product Board Inspection and Test |
These standards provide guidelines for the design, fabrication, and quality assessment of PCBs, including requirements for material selection, conductor spacing, hole size, and more.
ISO 13485
ISO 13485 is an international standard that specifies requirements for a quality management system specific to the medical device industry. It is based on the ISO 9001 standard but includes additional requirements for medical devices, such as risk management, cleanliness, and traceability.
IEC 60601
IEC 60601 is a series of technical standards for the safety and effectiveness of medical electrical equipment. It consists of a general standard (IEC 60601-1) and several collateral and particular standards that apply to specific types of medical devices.
Some key requirements of IEC 60601 for medical PCBs include:
- Electrical safety: PCBs must be designed to prevent electrical shock, fire, and other hazards.
- Electromagnetic compatibility (EMC): PCBs must be designed to minimize electromagnetic interference (EMI) and withstand electromagnetic disturbances.
- Environmental protection: PCBs must be designed to withstand specified environmental conditions, such as temperature, humidity, and vibration.
FDA Regulations
In the United States, the FDA regulates medical devices to ensure their safety and effectiveness. Medical device manufacturers must comply with FDA regulations, including:
- 21 CFR Part 820: Quality System Regulation (QSR), which sets requirements for the design, manufacture, packaging, labeling, storage, installation, and servicing of medical devices.
- 21 CFR Part 11: Electronic Records and Electronic Signatures, which sets requirements for the use of electronic records and signatures in FDA-regulated industries.
Medical PCB Design Considerations
When designing medical PCBs, several factors must be considered to ensure compliance with relevant standards and regulations:
Material Selection
Medical PCBs must be made from materials that are biocompatible, non-toxic, and resistant to chemicals and sterilization processes. Common materials used in medical PCBs include:
- FR-4: A flame-retardant epoxy laminate that is widely used in PCBs.
- Polyimide: A high-temperature, flexible material that is often used in implantable devices.
- Ceramic: A non-conductive, heat-resistant material that is used in high-frequency applications.
Circuit Design
Medical PCBs must be designed to minimize the risk of electrical shock, fire, and other hazards. Some key considerations include:
- Isolation: Medical PCBs often require isolation between different parts of the circuit to prevent electrical shock and interference.
- Grounding: Proper grounding is essential to ensure electrical safety and minimize EMI.
- Creepage and Clearance: Adequate spacing must be maintained between conductors to prevent arcing and short circuits.
Component Selection
Components used in medical PCBs must be reliable, accurate, and able to withstand the intended environment. Some key considerations include:
- Tolerance: Components must have tight tolerances to ensure accurate and reliable performance.
- Temperature Range: Components must be able to operate within the specified temperature range of the medical device.
- Moisture Resistance: Components must be resistant to moisture and humidity to prevent corrosion and other failures.
Manufacturing and Testing
Medical PCBs must be manufactured and tested in accordance with relevant standards and regulations. Some key considerations include:
- Cleanliness: Medical PCBs must be manufactured in a clean environment to prevent contamination and ensure biocompatibility.
- Traceability: Each PCB must be traceable throughout the manufacturing process to ensure quality control and facilitate product recalls if necessary.
- Testing: Medical PCBs must undergo rigorous testing to ensure they meet all performance and safety requirements. This may include electrical, environmental, and functional testing.
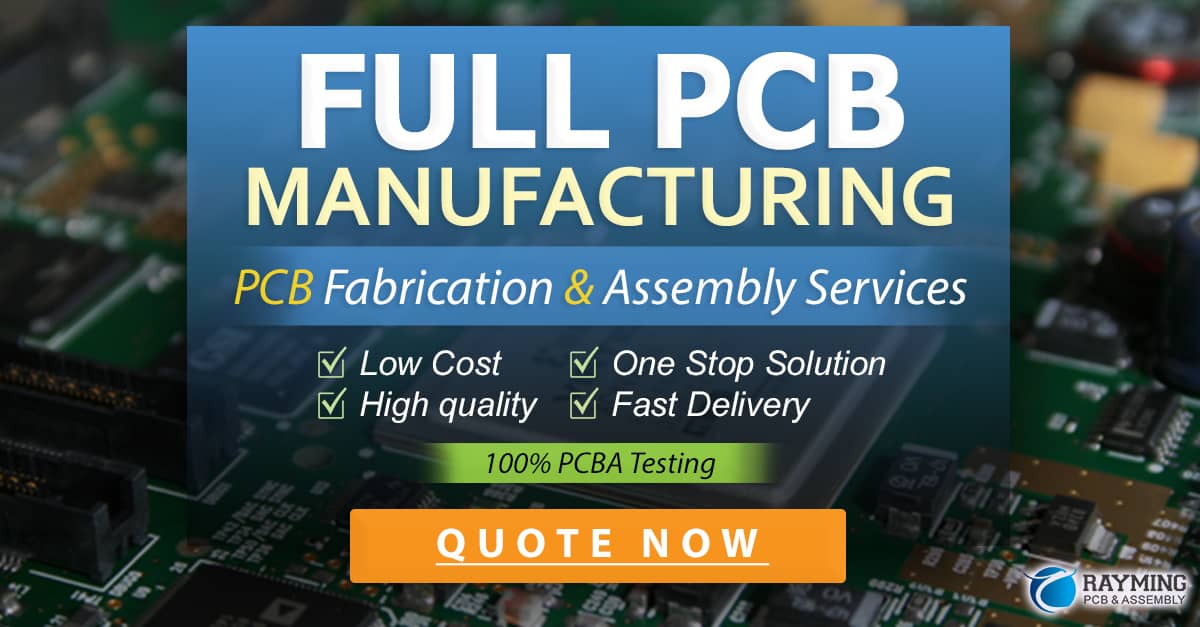
Frequently Asked Questions (FAQ)
-
What is the difference between ISO 13485 and ISO 9001?
ISO 13485 is a quality management system standard specific to the medical device industry, while ISO 9001 is a general quality management system standard. ISO 13485 includes additional requirements for medical devices, such as risk management and traceability. -
What is the purpose of IEC 60601?
IEC 60601 is a series of technical standards that specify requirements for the safety and effectiveness of medical electrical equipment. It aims to ensure that medical devices are safe for patients and operators and can function reliably in their intended environment. -
What materials are commonly used in medical PCBs?
Common materials used in medical PCBs include FR-4, polyimide, and ceramic. These materials are chosen for their biocompatibility, non-toxicity, and resistance to chemicals and sterilization processes. -
Why is traceability important in medical PCB manufacturing?
Traceability is important in medical PCB manufacturing to ensure quality control and facilitate product recalls if necessary. Each PCB must be traceable throughout the manufacturing process, allowing manufacturers to identify and address any issues that may arise. -
What types of testing are required for medical PCBs?
Medical PCBs must undergo rigorous testing to ensure they meet all performance and safety requirements. This may include electrical testing (e.g., continuity, insulation resistance), environmental testing (e.g., temperature, humidity), and functional testing (e.g., signal integrity, power consumption).
Conclusion
Medical PCBs are critical components in the healthcare industry, and adherence to relevant standards and regulations is essential to ensure their safety, effectiveness, and reliability. Key standards and regulations for medical PCBs include IPC standards, ISO 13485, IEC 60601, and FDA regulations.
When designing medical PCBs, careful consideration must be given to material selection, circuit design, component selection, manufacturing, and testing. By following best practices and complying with relevant standards and regulations, medical device manufacturers can produce high-quality PCBs that meet the stringent requirements of the healthcare industry and ensure the best possible outcomes for patients.
0 Comments