Introduction
A PCB fabrication drawing, also known as a PCB manufacturing drawing or PCB production drawing, is a crucial document that provides all the necessary information for the fabrication of a printed circuit board (PCB). It serves as a communication tool between the PCB designer and the manufacturing team, ensuring that the PCB is produced according to the designer’s specifications. In this article, we will discuss the essential elements that should be included in a PCB fabrication drawing to guarantee a smooth and accurate manufacturing process.
Key Components of a PCB Fabrication Drawing
1. Board Outline and Dimensions
The PCB fabrication drawing should clearly indicate the board outline and dimensions. This includes the overall size of the board, the shape of the board (rectangular, circular, or custom), and any cutouts or unique features. The dimensions should be provided in a standard unit of measurement, such as millimeters or inches, and should be accurate to within the manufacturing tolerances.
2. Layer Stackup Information
The layer stackup information is crucial for the manufacturing process as it defines the arrangement of copper layers, insulating layers, and any special materials used in the PCB. The fabrication drawing should specify the number of layers, the thickness of each layer, and the material type (e.g., FR-4, Rogers, or Polyimide). It should also indicate the copper weight for each layer, typically expressed in ounces per square foot (oz/ft²).
Layer | Material | Thickness (mm) | Copper Weight (oz/ft²) |
---|---|---|---|
Top | FR-4 | 0.1524 | 1 |
Ground | FR-4 | 0.2032 | 1 |
Power | FR-4 | 0.2032 | 1 |
Bottom | FR-4 | 0.1524 | 1 |
3. Drill Hole Information
The PCB fabrication drawing should include detailed information about the drill holes required for the board. This includes the hole sizes, locations, and tolerances. The hole sizes should be specified in a standard unit of measurement, such as millimeters or inches, and the locations should be provided using a coordinate system or a grid reference. The tolerances for the hole sizes and locations should also be clearly stated.
4. Soldermask and Silkscreen Specifications
The soldermask and silkscreen specifications are important for the final appearance and functionality of the PCB. The fabrication drawing should indicate the color and type of soldermask to be used (e.g., green, black, or white), as well as the color and type of silkscreen (e.g., white or black). It should also specify the minimum line width and spacing for the silkscreen, and any special requirements for the soldermask, such as peelable mask for exposed copper areas.
5. Surface Finish Requirements
The surface finish of the PCB is critical for its solderability and long-term reliability. The fabrication drawing should specify the type of surface finish to be applied, such as Hot Air Solder Leveling (HASL), Electroless Nickel Immersion Gold (ENIG), or Immersion Silver. It should also indicate any special requirements, such as the thickness of the surface finish or the need for selective plating.
6. Impedance Control Specifications
For high-speed or high-frequency PCBs, impedance control is essential to ensure signal integrity. The fabrication drawing should include the impedance control specifications, such as the target impedance value, the tolerance, and the reference layer for controlled impedance traces. It should also specify the dielectric material and thickness required to achieve the desired impedance.
7. Special Requirements or Instructions
The PCB fabrication drawing should include any special requirements or instructions that are necessary for the manufacturing process. This may include specific handling instructions, special packaging requirements, or any additional testing or inspection steps that need to be performed. These requirements should be clearly communicated to the manufacturing team to avoid any confusion or delays in the production process.
Best Practices for Creating a PCB Fabrication Drawing
1. Use a Standard Drawing Format
It is recommended to use a standard drawing format, such as Gerber files or ODB++, when creating a PCB fabrication drawing. These formats are widely accepted by PCB manufacturers and ensure that the information is accurately conveyed. Gerber files, in particular, are considered the industry standard and are supported by most PCB design software packages.
2. Include a Comprehensive Bill of Materials (BOM)
In addition to the fabrication drawing, it is important to include a comprehensive Bill of Materials (BOM) that lists all the components required for the PCB assembly. The BOM should include the part numbers, quantities, and any special instructions for each component. This information helps the manufacturing team to plan the assembly process and ensure that all the necessary components are available.
3. Provide Clear and Concise Instructions
The PCB fabrication drawing should provide clear and concise instructions to the manufacturing team. Use simple and straightforward language, and avoid ambiguous or open-ended statements. If there are any specific requirements or instructions, make sure they are clearly highlighted and easy to understand.
4. Review and Verify the Drawing
Before submitting the PCB fabrication drawing to the manufacturer, it is crucial to review and verify the information for accuracy and completeness. Double-check all the dimensions, specifications, and instructions to ensure that they are correct and consistent with the design intent. It is also a good practice to have a second person review the drawing to catch any errors or omissions.
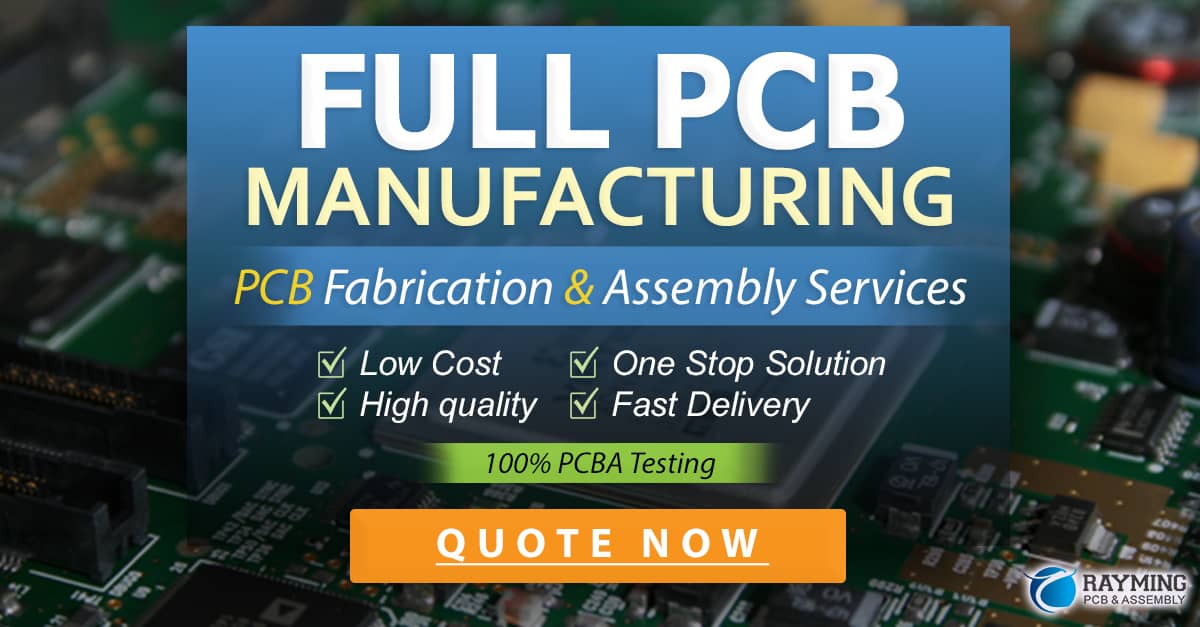
FAQs
-
What is the purpose of a PCB fabrication drawing?
A PCB fabrication drawing provides all the necessary information for the manufacturing of a printed circuit board. It serves as a communication tool between the PCB designer and the manufacturing team, ensuring that the PCB is produced according to the designer’s specifications. -
What are the key components of a PCB fabrication drawing?
The key components of a PCB fabrication drawing include the board outline and dimensions, layer stackup information, drill hole information, soldermask and silkscreen specifications, surface finish requirements, impedance control specifications, and any special requirements or instructions. -
What is the recommended format for creating a PCB fabrication drawing?
It is recommended to use a standard drawing format, such as Gerber files or ODB++, when creating a PCB fabrication drawing. These formats are widely accepted by PCB manufacturers and ensure that the information is accurately conveyed. -
Why is it important to include a Bill of Materials (BOM) with the fabrication drawing?
A comprehensive Bill of Materials (BOM) lists all the components required for the PCB assembly. It helps the manufacturing team to plan the assembly process and ensure that all the necessary components are available. Including a BOM with the fabrication drawing ensures a smooth and efficient manufacturing process. -
What should be done before submitting the PCB fabrication drawing to the manufacturer?
Before submitting the PCB fabrication drawing to the manufacturer, it is crucial to review and verify the information for accuracy and completeness. Double-check all the dimensions, specifications, and instructions to ensure that they are correct and consistent with the design intent. It is also a good practice to have a second person review the drawing to catch any errors or omissions.
Conclusion
A well-prepared PCB fabrication drawing is essential for the successful manufacturing of a printed circuit board. By including all the necessary information, such as the board outline and dimensions, layer stackup, drill hole specifications, soldermask and silkscreen requirements, surface finish, impedance control, and any special instructions, the designer can ensure that the PCB is produced according to their specifications. Following best practices, such as using a standard drawing format, including a comprehensive BOM, providing clear and concise instructions, and reviewing the drawing for accuracy, can help streamline the manufacturing process and avoid costly errors or delays.
0 Comments