Introduction to Flexible PCBs
Flexible printed circuit boards (PCBs) have revolutionized the electronics industry with their versatility, durability, and lightweight design. Unlike traditional rigid PCBs, flexible PCBs can bend, twist, and conform to various shapes, making them ideal for applications where space is limited or where the device needs to move or flex. One such application where flexible PCBs have proven to be the best choice is in satellite technology.
What are Flexible PCBs?
Flexible PCBs, also known as flex circuits or flex PCBs, are a type of printed circuit board that consists of a thin, flexible substrate made of materials such as polyimide or polyester. These substrates are laminated with conductive traces, typically made of copper, which allow electrical signals to be routed throughout the circuit. The flexibility of the substrate allows the PCB to bend and twist without breaking or losing its electrical connectivity.
Advantages of Flexible PCBs
Flexible PCBs offer several advantages over traditional rigid PCBs, including:
- Flexibility: The ability to bend and twist allows flexible PCBs to be used in applications where space is limited or where the device needs to move or flex.
- Lightweight: Flexible PCBs are typically much lighter than rigid PCBs, which is essential in applications where weight is a critical factor, such as in aerospace and satellite technology.
- Durability: Flexible PCBs are highly resistant to vibration, shock, and extreme temperatures, making them ideal for use in harsh environments.
- Improved Signal Integrity: The thin, flexible nature of flex PCBs allows for shorter signal paths, which can improve signal integrity and reduce electromagnetic interference (EMI).
Why Flexible PCBs are the Best Choice for Satellite Applications
Satellite technology requires electronics that are reliable, durable, and able to withstand the harsh conditions of space. Flexible PCBs have proven to be the best choice for satellite applications due to their unique properties and advantages.
Lightweight Design
One of the most critical factors in satellite design is weight. Every gram of weight added to a satellite increases the cost of launching it into space. Flexible PCBs are much lighter than traditional rigid PCBs, which makes them an ideal choice for satellite applications. The lightweight design of flexible PCBs allows for more payload capacity and reduces the overall cost of the satellite.
Durability in Harsh Environments
Satellites are exposed to extreme temperatures, radiation, and vacuum conditions in space. Flexible PCBs are highly resistant to these harsh environments, making them an ideal choice for satellite applications. The materials used in flexible PCBs, such as polyimide and polyester, are able to withstand extreme temperatures ranging from -200°C to +200°C. Additionally, flexible PCBs are resistant to radiation and vacuum conditions, which can cause damage to traditional rigid PCBs.
Vibration and Shock Resistance
During launch and operation, satellites are subjected to high levels of vibration and shock. Flexible PCBs are highly resistant to vibration and shock, which is essential for ensuring the reliability and longevity of the satellite’s electronics. The flexible nature of the PCB allows it to absorb and dissipate the energy from vibrations and shocks, reducing the risk of damage to the electronic components.
Improved Signal Integrity
Satellite electronics require high-speed data transmission and reliable signal integrity. Flexible PCBs offer improved signal integrity compared to traditional rigid PCBs due to their thin, flexible nature. The shorter signal paths in flexible PCBs reduce the risk of signal loss and distortion, ensuring reliable data transmission throughout the satellite’s electronics.
Space Savings
Satellites have limited space for electronics, and every centimeter counts. Flexible PCBs offer significant space savings compared to traditional rigid PCBs due to their ability to bend and conform to various shapes. This allows for more efficient use of space within the satellite, enabling the integration of more electronic components and sensors.
Examples of Flexible PCBs in Satellite Applications
Flexible PCBs have been used in various satellite applications, including:
-
Solar Array Deployment Mechanisms: Flexible PCBs are used in the deployment mechanisms of solar arrays, which provide power to the satellite. The flexibility of the PCB allows it to bend and fold during the deployment process, ensuring reliable power delivery to the satellite’s electronics.
-
Antenna Deployment Systems: Flexible PCBs are used in the deployment systems of satellite antennas, which are essential for communication and data transmission. The flexibility of the PCB allows it to bend and conform to the shape of the antenna, ensuring reliable signal transmission.
-
Sensor Integration: Flexible PCBs are used to integrate various sensors within the satellite, such as temperature sensors, pressure sensors, and radiation detectors. The flexibility of the PCB allows for efficient placement of sensors within the limited space of the satellite.
Manufacturing Considerations for Flexible PCBs in Satellite Applications
When designing and manufacturing flexible PCBs for satellite applications, several considerations need to be taken into account to ensure the reliability and performance of the electronics.
Material Selection
The choice of materials for flexible PCBs in satellite applications is critical. The materials must be able to withstand the harsh conditions of space, including extreme temperatures, radiation, and vacuum conditions. Polyimide is the most commonly used substrate material for flexible PCBs in satellite applications due to its excellent thermal stability, mechanical strength, and radiation resistance.
Conductor Selection
The choice of conductor material for flexible PCBs in satellite applications is also important. Copper is the most commonly used conductor material due to its excellent electrical conductivity and mechanical properties. However, in some cases, other conductor materials such as silver or gold may be used to improve the PCB’s performance in specific environments.
Shielding and Grounding
Proper shielding and grounding are essential for ensuring the reliability and performance of flexible PCBs in satellite applications. Shielding helps to reduce electromagnetic interference (EMI) and protect the electronics from radiation and other environmental factors. Grounding helps to ensure a stable reference voltage and prevent electrical noise from interfering with the signal integrity.
Testing and Qualification
Rigorous testing and qualification procedures are required to ensure the reliability and performance of flexible PCBs in satellite applications. This includes environmental testing to simulate the harsh conditions of space, such as thermal cycling, vacuum testing, and radiation exposure. Additionally, functional testing is performed to ensure that the electronics perform as intended and meet the required specifications.
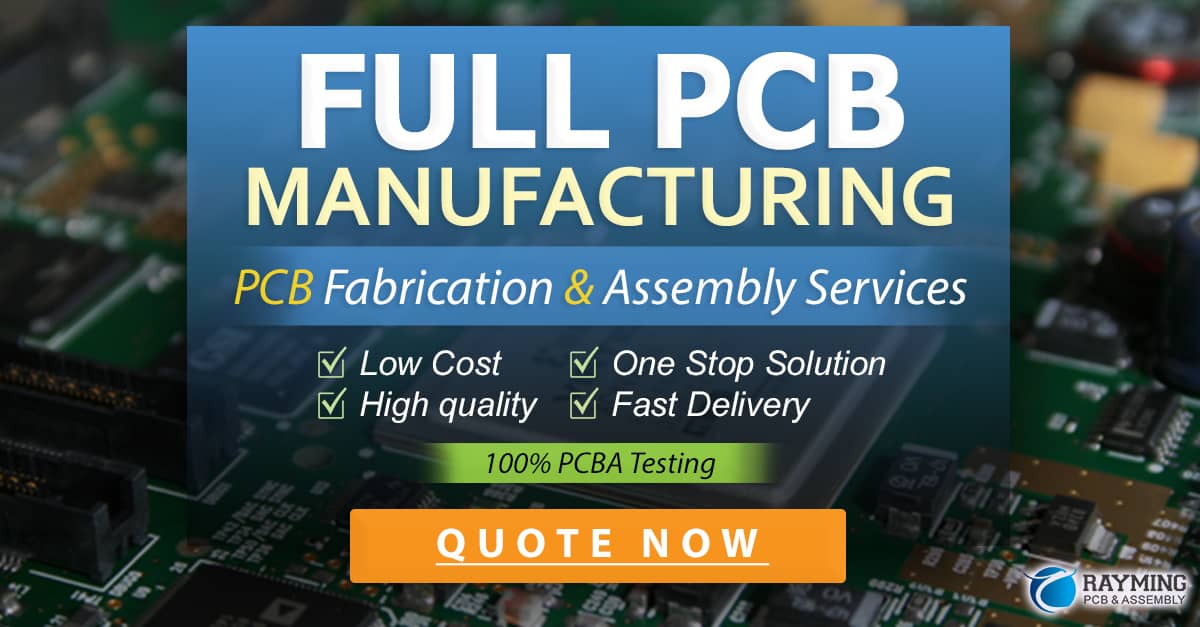
Conclusion
Flexible PCBs have proven to be the best choice for satellite applications due to their lightweight design, durability in harsh environments, vibration and shock resistance, improved signal integrity, and space savings. The unique properties of flexible PCBs make them ideal for use in solar array deployment mechanisms, antenna deployment systems, and sensor integration within satellites.
When designing and manufacturing flexible PCBs for satellite applications, careful consideration must be given to material selection, conductor selection, shielding and grounding, and testing and qualification procedures. By following these considerations, engineers can ensure the reliability and performance of the satellite’s electronics in the harsh conditions of space.
As satellite technology continues to advance, the use of flexible PCBs will become increasingly important. The ability to integrate more electronics and sensors within the limited space of a satellite while maintaining reliability and performance will be essential for enabling new scientific discoveries and technological advancements in space exploration.
Frequently Asked Questions (FAQ)
1. What are the main advantages of using flexible PCBs in satellite applications?
The main advantages of using flexible PCBs in satellite applications include their lightweight design, durability in harsh environments, vibration and shock resistance, improved signal integrity, and space savings. These properties make flexible PCBs ideal for use in solar array deployment mechanisms, antenna deployment systems, and sensor integration within satellites.
2. What materials are commonly used for flexible PCBs in satellite applications?
Polyimide is the most commonly used substrate material for flexible PCBs in satellite applications due to its excellent thermal stability, mechanical strength, and radiation resistance. Copper is the most commonly used conductor material due to its excellent electrical conductivity and mechanical properties.
3. Why is shielding and grounding important for flexible PCBs in satellite applications?
Proper shielding and grounding are essential for ensuring the reliability and performance of flexible PCBs in satellite applications. Shielding helps to reduce electromagnetic interference (EMI) and protect the electronics from radiation and other environmental factors. Grounding helps to ensure a stable reference voltage and prevent electrical noise from interfering with the signal integrity.
4. What kind of testing is required for flexible PCBs in satellite applications?
Rigorous testing and qualification procedures are required to ensure the reliability and performance of flexible PCBs in satellite applications. This includes environmental testing to simulate the harsh conditions of space, such as thermal cycling, vacuum testing, and radiation exposure. Additionally, functional testing is performed to ensure that the electronics perform as intended and meet the required specifications.
5. How will the use of flexible PCBs in satellite applications evolve in the future?
As satellite technology continues to advance, the use of flexible PCBs will become increasingly important. The ability to integrate more electronics and sensors within the limited space of a satellite while maintaining reliability and performance will be essential for enabling new scientific discoveries and technological advancements in space exploration. Flexible PCBs will play a crucial role in making these advancements possible.
0 Comments