How Does Wave Soldering Work?
The wave soldering process consists of several key steps:
-
Fluxing: The PCB is first passed through a fluxing station, where a thin layer of flux is applied to the bottom side of the board. The flux helps to remove oxides from the metal surfaces and promotes better solder adhesion.
-
Preheating: The fluxed PCB then enters a preheating zone, where it is heated to a temperature just below the melting point of the solder. This helps to evaporate any remaining solvents in the flux and prevents thermal shock when the board contacts the molten solder.
-
Solder Wave: The preheated PCB is then transported over a wave of molten solder. The solder wave is created by a pump that forces the molten solder through a nozzle, forming a standing wave. As the board moves over the wave, the solder adheres to the exposed metal surfaces of the PCB and the component leads, creating electrical connections.
-
Cooling: After passing over the solder wave, the PCB enters a cooling zone where the solder solidifies, forming permanent electrical and mechanical bonds.
Advantages of Wave Soldering
Wave soldering offers several advantages over other soldering methods:
- High-speed production: Wave soldering allows for the rapid soldering of multiple components on a PCB, making it ideal for high-volume manufacturing.
- Consistency: The automated nature of the wave soldering process ensures consistent solder joint quality across large numbers of PCBs.
- Versatility: Wave soldering can accommodate a wide range of component types and sizes, including through-hole and surface mount components.
- Cost-effectiveness: Due to its high throughput and automation, wave soldering is a cost-effective solution for large-scale PCB Assembly.
Types of Wave Soldering Machines
There are two main types of wave soldering machines:
-
Dual Wave Soldering Machine: This type of machine features two separate solder waves – a turbulent wave and a laminar wave. The turbulent wave is responsible for ensuring good solder penetration and filling of through-holes, while the laminar wave provides a smooth, even finish to the solder joints.
-
Single Wave Soldering Machine: As the name suggests, this type of machine uses a single solder wave. While less versatile than dual wave machines, single wave soldering machines are simpler and more affordable, making them suitable for smaller-scale production or specialized applications.
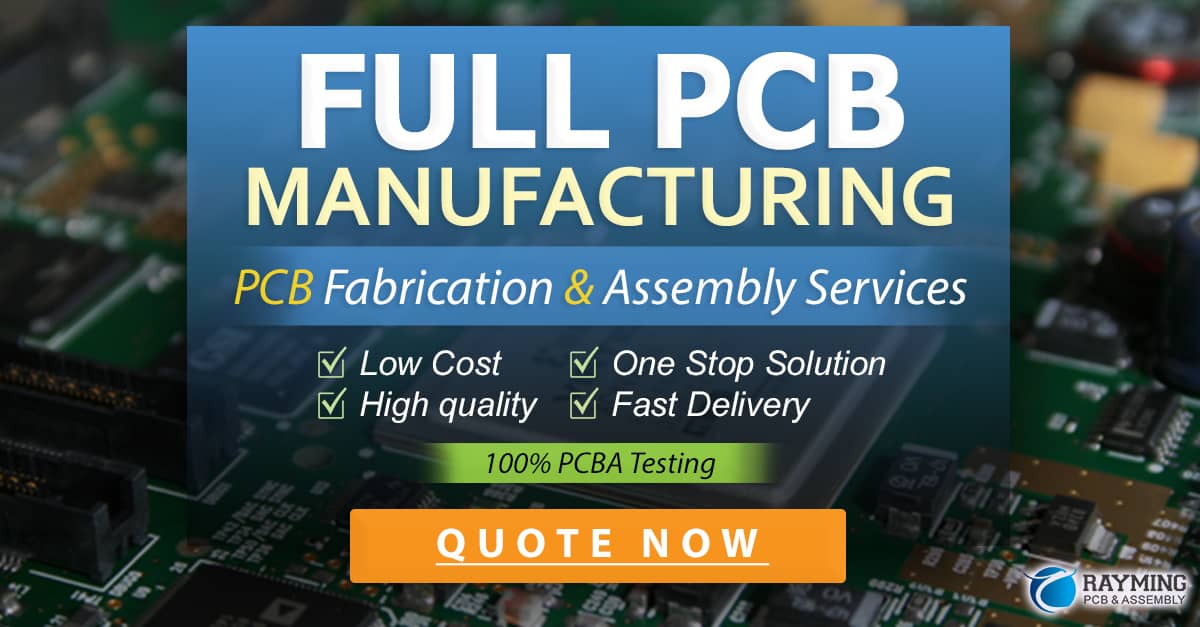
Key Parameters in Wave Soldering
To ensure optimal results, several key parameters must be controlled during the wave soldering process:
- Solder temperature: The temperature of the molten solder must be carefully maintained to ensure proper flow and adhesion. Typical solder temperatures range from 240°C to 260°C.
- Conveyor speed: The speed at which the PCB passes over the solder wave must be adjusted based on factors such as the board size, component density, and solder type. Proper conveyor speed ensures adequate solder contact time without causing bridging or other defects.
- Flux type and application: The choice of flux and its application method can significantly impact the quality of the solder joints. The flux must be compatible with the solder alloy and the PCB material, and it must be applied in the correct amount to promote good solder wetting without leaving excessive residue.
- Preheat temperature: The preheat temperature should be high enough to activate the flux and prevent thermal shock but not so high as to damage the components or the PCB substrate.
Solder Alloys Used in Wave Soldering
The most common solder alloys used in wave soldering are tin-lead (Sn-Pb) and lead-free alloys. Tin-lead solders, such as Sn63Pb37, have been widely used due to their low melting point, good wetting properties, and reliable performance. However, with the introduction of the Restriction of Hazardous Substances (RoHS) directive, lead-free alloys have become increasingly popular. Common lead-free alternatives include:
- Tin-silver-copper (SAC) alloys, such as SAC305 (Sn96.5Ag3.0Cu0.5)
- Tin-copper (SnCu) alloys, such as Sn99.3Cu0.7
- Tin-silver (SnAg) alloys, such as Sn96.5Ag3.5
Each alloy has its own unique properties, such as melting point, wetting behavior, and mechanical strength, which must be considered when selecting the appropriate solder for a given application.
Defects in Wave Soldered PCBs
Despite the advantages of wave soldering, several types of defects can occur during the process:
- Bridging: This occurs when solder inadvertently connects two or more adjacent pads or component leads, creating a short circuit.
- Insufficient solder: Also known as “dry joint,” this defect occurs when there is not enough solder to form a proper connection between the component lead and the PCB pad.
- Solder balls: These are small spheres of solder that can form on the PCB surface due to excessive solder or improper flux activation.
- Icicles: These are sharp, pointed projections of solder that can form on the bottom side of the PCB due to excessive solder or incorrect conveyor speed.
- Disturbed joints: This occurs when components are displaced or rotated during the soldering process, resulting in misaligned or weakened solder joints.
To minimize the occurrence of these defects, it is essential to maintain proper control over the key process parameters and to follow best practices for PCB design and component placement.
Designing PCBs for Wave Soldering
When designing PCBs for wave soldering, several guidelines should be followed to ensure optimal results:
- Pad size and spacing: Pads should be sized and spaced appropriately to accommodate the component leads and prevent bridging. Industry standards, such as IPC-7351, provide recommended pad dimensions for various component types.
- Thermal relief: Thermal relief patterns, which consist of spokes or webs connecting the pad to the surrounding copper, should be used to minimize thermal stress on the components during soldering.
- Solder mask: A properly designed solder mask helps to prevent bridging and solder ball formation by confining the solder to the desired areas of the PCB.
- Component orientation: Components should be oriented in a manner that promotes good solder flow and minimizes shadowing effects. Generally, components should be oriented parallel to the direction of travel over the solder wave.
- Fiducial marks: These are reference points used by automated systems to align the PCB during the soldering process. Fiducial marks should be included in the PCB design to ensure accurate component placement and soldering.
By adhering to these design guidelines, manufacturers can improve the quality and reliability of their wave-soldered PCBs.
Inspection and Quality Control
After the wave soldering process, it is essential to inspect the PCBs to ensure that they meet the required quality standards. Several inspection methods can be used:
- Visual inspection: This involves the use of the human eye, often aided by magnification, to check for visible defects such as bridging, insufficient solder, or component misalignment.
- Automated optical inspection (AOI): AOI systems use cameras and image processing software to automatically detect defects on the PCB surface. These systems can quickly scan large numbers of PCBs and identify potential issues.
- X-ray inspection: For defects that are not visible on the surface, such as voids or cracks in the solder joints, X-ray inspection can be used. This method allows for the non-destructive examination of the internal structure of the solder joints.
- Electrical testing: Functional testing of the PCB can be performed to verify that the soldered connections are electrically sound and that the board performs as intended.
By implementing a rigorous inspection and quality control process, manufacturers can identify and correct defects early in the production cycle, reducing costs and improving overall product quality.
Environmental Considerations
Wave soldering, like many industrial processes, can have an environmental impact. The use of lead-based solders, for example, has been a concern due to the toxicity of lead and its potential to contaminate soil and water sources. As a result, many countries have implemented regulations, such as the RoHS directive, to restrict the use of lead and other hazardous substances in electronics manufacturing.
In response to these regulations, the industry has developed lead-free solder alloys and adapted the wave soldering process to accommodate these new materials. However, lead-free solders often require higher processing temperatures and may have different wetting and mechanical properties compared to traditional tin-lead solders. Manufacturers must carefully consider these differences when transitioning to lead-free soldering to ensure that product quality and reliability are maintained.
Another environmental concern associated with wave soldering is the use of fluxes. Many fluxes contain volatile organic compounds (VOCs) that can be released into the atmosphere during the soldering process. To mitigate this issue, manufacturers can use low-VOC or VOC-free fluxes and implement fume extraction systems to capture and filter any emissions.
Future Trends in Wave Soldering
As the electronics industry continues to evolve, wave soldering technology must adapt to keep pace with new challenges and requirements. Some of the key trends shaping the future of wave soldering include:
- Miniaturization: As electronic devices become smaller and more complex, PCBs must accommodate a greater number of components in a smaller space. This trend requires wave soldering systems to be capable of precisely soldering very small components without causing defects.
- Increased automation: To improve efficiency and reduce costs, many manufacturers are turning to fully automated wave soldering systems. These systems integrate robotics, conveyors, and inspection technology to create a seamless, end-to-end soldering process.
- Selective soldering: For PCBs with a mix of through-hole and surface mount components, selective soldering systems are becoming more popular. These systems use targeted solder waves or nozzles to solder specific areas of the board, allowing for greater flexibility and customization.
- Energy efficiency: As energy costs rise and environmental concerns grow, manufacturers are seeking ways to reduce the energy consumption of their wave soldering processes. This may involve the use of more efficient heating systems, improved insulation, and optimized process parameters.
By staying abreast of these trends and investing in advanced wave soldering technology, manufacturers can position themselves for success in an increasingly competitive and demanding market.
FAQ
-
Q: What is the difference between wave soldering and reflow soldering?
A: Wave soldering is used primarily for through-hole components and involves passing the PCB over a wave of molten solder. Reflow soldering, on the other hand, is used for surface mount components and involves applying solder paste to the PCB pads and then heating the entire board to melt the solder and form connections. -
Q: Can wave soldering be used for surface mount components?
A: While wave soldering is primarily used for through-hole components, it can be used for some surface mount components with the use of adhesives to hold the components in place during the soldering process. However, reflow soldering is generally preferred for surface mount components due to its greater precision and reliability. -
Q: How does the use of lead-free solder affect the wave soldering process?
A: Lead-free solders typically have higher melting points than traditional tin-lead solders, which means that the wave soldering process must be adjusted to accommodate these higher temperatures. This may involve changes to the preheat temperature, solder wave temperature, and conveyor speed to ensure proper solder wetting and joint formation. -
Q: What is the role of flux in wave soldering?
A: Flux is a chemical compound that is applied to the PCB prior to soldering. Its primary functions are to remove oxides from the metal surfaces, promote solder wetting, and prevent reoxidation during the soldering process. The choice of flux is important, as it can affect the quality of the solder joints and the level of post-soldering residue on the PCB. -
Q: How can defects in wave-soldered PCBs be prevented?
A: Defects in wave-soldered PCBs can be prevented by properly designing the PCB for wave soldering, selecting appropriate components and materials, optimizing the process parameters, and implementing robust inspection and quality control procedures. This may involve following industry guidelines for pad size and spacing, using thermal relief patterns, adjusting the solder wave height and conveyor speed, and conducting regular maintenance on the wave soldering equipment.
Aspect | Wave Soldering | Reflow Soldering |
---|---|---|
Primary Use | Through-hole components | Surface mount components |
Process | PCB passed over molten solder wave | Solder paste applied to pads, then heated |
Solder Temperature | 240°C to 260°C (lead-based) | 220°C to 250°C (lead-based) |
Flux Application | Separate fluxing step prior to soldering | Flux included in solder paste |
Defect Types | Bridging, insufficient solder, solder balls, icicles | Tombstoning, bridging, Solder Beading, voiding |
In conclusion, wave soldering is a critical process in the manufacture of high-quality, reliable PCBs. By understanding the fundamentals of the process, designing PCBs with wave soldering in mind, and implementing best practices for process control and inspection, manufacturers can ensure that their wave-soldered products meet the demanding requirements of today’s electronics industry. As the industry continues to evolve, staying informed about new technologies, materials, and trends will be essential for success in the competitive world of PCB assembly.
0 Comments