Introduction to Core PCB
A printed circuit board (PCB) is a fundamental component in modern electronics, providing a platform for electrical components to be mounted and interconnected. The core of a PCB plays a crucial role in determining the board’s mechanical and electrical properties. In this article, we will explore the concept of the PCB core, its materials, types, and the impact it has on the overall performance of the circuit board.
What is a PCB Core?
The core of a PCB is the central layer of the board, typically made of a dielectric material. It serves as the foundation for the copper layers and provides mechanical support to the entire structure. The core material is selected based on the desired electrical, thermal, and mechanical properties of the PCB.
Key Functions of a PCB Core
- Mechanical support: The core provides structural integrity to the PCB, ensuring that it can withstand the stresses of manufacturing, assembly, and operation.
- Electrical insulation: The dielectric properties of the core material prevent electrical signals from interfering with each other, maintaining signal integrity.
- Thermal management: The core material’s thermal conductivity helps dissipate heat generated by the components, preventing overheating and ensuring reliable operation.
Common PCB Core Materials
Several materials are commonly used for PCB cores, each with its unique properties and applications.
FR-4
FR-4 (Flame Retardant 4) is the most widely used core material in the PCB industry. It is a composite material made of woven fiberglass cloth impregnated with an epoxy resin. FR-4 offers excellent mechanical strength, good electrical insulation, and reasonable thermal stability.
Property | Value |
---|---|
Dielectric Constant | 4.5 @ 1 MHz |
Dissipation Factor | 0.02 @ 1 MHz |
Thermal Conductivity | 0.3 W/mK |
Glass Transition Temperature | 130-140°C |
Polyimide
Polyimide is a high-performance polymer known for its exceptional thermal stability and mechanical strength. It is often used in applications that require operation at elevated temperatures or exposure to harsh environments. Polyimide PCBs are commonly found in aerospace, military, and automotive industries.
Property | Value |
---|---|
Dielectric Constant | 3.5 @ 1 MHz |
Dissipation Factor | 0.002 @ 1 MHz |
Thermal Conductivity | 0.2 W/mK |
Glass Transition Temperature | 260°C |
PTFE
Polytetrafluoroethylene (PTFE), also known as Teflon, is a fluoropolymer with excellent dielectric properties and low dissipation factor. PTFE PCBs are used in high-frequency applications, such as radar systems and wireless communications, where signal integrity is critical.
Property | Value |
---|---|
Dielectric Constant | 2.1 @ 1 MHz |
Dissipation Factor | 0.0002 @ 1 MHz |
Thermal Conductivity | 0.25 W/mK |
Glass Transition Temperature | 327°C |
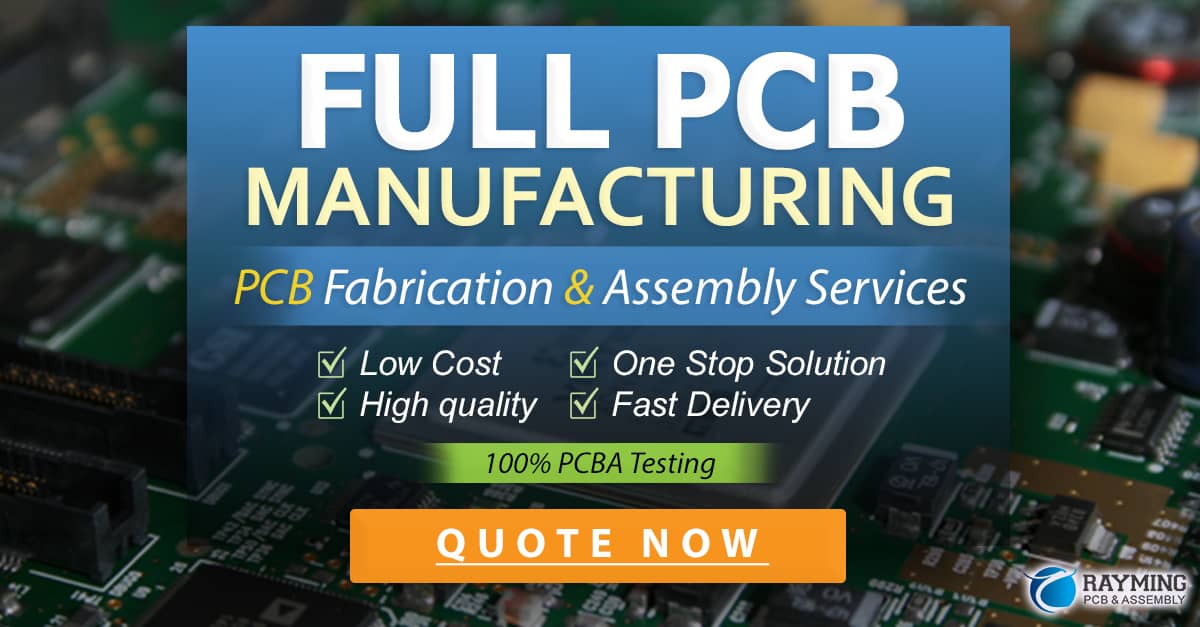
Types of PCB Cores
PCB cores can be classified based on their construction and the number of layers.
Single-sided PCB Core
A single-sided PCB has copper traces on only one side of the core material. These boards are simple and cost-effective, making them suitable for low-complexity circuits and prototypes.
Double-sided PCB Core
Double-sided PCBs have copper traces on both sides of the core material, allowing for higher component density and more complex routing compared to single-sided boards. The two copper layers are interconnected using plated through-holes (PTHs).
Multi-layer PCB Core
Multi-layer PCBs consist of multiple core layers laminated together, with each core containing copper traces on both sides. The cores are separated by prepreg (pre-impregnated) layers, which are partially cured fiberglass sheets with a resin system. Multi-layer PCBs offer the highest level of complexity and density, enabling the design of advanced electronic systems.
Impact of Core Material on PCB Performance
The choice of core material significantly affects the performance of a PCB in various aspects.
Signal Integrity
The dielectric constant and dissipation factor of the core material influence the signal propagation and loss in the PCB. Materials with lower dielectric constants, such as PTFE, are preferred for high-frequency applications to minimize signal distortion and attenuation.
Thermal Management
The thermal conductivity of the core material determines how efficiently heat is dissipated from the components. PCBs with better thermal management can operate at higher power levels and have improved reliability. Materials like aluminum and copper can be used as core substrates for enhanced thermal performance.
Mechanical Strength
The mechanical properties of the core material, such as tensile strength and flexural modulus, affect the PCB’s ability to withstand physical stresses during manufacturing, assembly, and operation. High-strength materials, such as polyimide, are used in applications that require robustness and durability.
Advanced Core Technologies
As the demand for high-performance electronics grows, new core technologies have emerged to address the challenges of signal integrity, thermal management, and miniaturization.
Metal Core PCBs
Metal core PCBs (MCPCBs) use a metal substrate, typically aluminum, as the core material. The metal core offers excellent thermal conductivity, allowing for efficient heat dissipation from power-hungry components like LEDs and power transistors. MCPCBs are commonly used in lighting applications, power electronics, and automotive systems.
High-Frequency Laminates
High-frequency laminates are specialized core materials designed for applications operating at microwave and millimeter-wave frequencies. These materials, such as Rogers RO4000 series and Isola Astra MT77, have low dielectric constants and dissipation factors, ensuring minimal signal loss and distortion. They are used in 5G wireless networks, radar systems, and satellite communications.
Embedded Component Technology
Embedded component technology involves integrating passive components, such as resistors and capacitors, within the PCB core. This approach saves space on the board surface, reduces parasitic effects, and improves signal integrity. Embedded components are fabricated using specialized materials and processes, such as resistive foils and high-k dielectric layers.
Conclusion
The core of a PCB is a critical element that determines the board’s electrical, thermal, and mechanical characteristics. Understanding the properties and types of core materials is essential for designing reliable and high-performance electronic systems. As technology advances, new core materials and technologies will continue to emerge, enabling the development of more compact, efficient, and robust PCBs.
Frequently Asked Questions
1. What is the most common PCB core material?
FR-4 is the most widely used PCB core material due to its good balance of mechanical, electrical, and thermal properties, as well as its cost-effectiveness.
2. Can a PCB have multiple core layers?
Yes, multi-layer PCBs consist of multiple core layers laminated together, separated by prepreg layers. This allows for higher component density and more complex routing compared to single-layer boards.
3. What are the advantages of using a metal core PCB?
Metal core PCBs offer excellent thermal conductivity, allowing for efficient heat dissipation from power-hungry components. This improves the reliability and performance of the electronic system, particularly in applications like LED lighting and power electronics.
4. How does the choice of core material affect signal integrity?
The dielectric constant and dissipation factor of the core material influence signal propagation and loss in the PCB. Materials with lower dielectric constants and dissipation factors, such as PTFE, are preferred for high-frequency applications to minimize signal distortion and attenuation.
5. What is embedded component technology in PCBs?
Embedded component technology involves integrating passive components, such as resistors and capacitors, within the PCB core. This approach saves space on the board surface, reduces parasitic effects, and improves signal integrity. It is achieved using specialized materials and fabrication processes.
0 Comments