Understanding the Basics of Core PCB
A printed circuit board (PCB) is a fundamental component in modern electronic devices. It serves as a platform for mounting and interconnecting electronic components, such as resistors, capacitors, and integrated circuits. The core of a PCB plays a crucial role in determining its performance, durability, and reliability.
What is a Core PCB?
A core PCB refers to the central layer of a multi-layer PCB. It is typically made of a dielectric material, such as FR-4, which is a composite of fiberglass and epoxy resin. The core provides a stable foundation for the copper layers and other components that make up the PCB.
The Importance of Core PCB
The core PCB serves several essential functions:
-
Structural support: The core provides mechanical strength and rigidity to the PCB, preventing warping and ensuring the stability of the mounted components.
-
Electrical insulation: The dielectric material of the core acts as an insulator, preventing short circuits and ensuring proper electrical isolation between the copper layers.
-
Thermal management: The core helps to dissipate heat generated by the electronic components, preventing overheating and ensuring optimal performance.
Types of Core PCB Materials
There are various materials used for core PCBs, each with its own properties and advantages. Some common core materials include:
FR-4
FR-4 is the most widely used core material in PCBs. It is a composite of fiberglass and epoxy resin, offering excellent mechanical strength, electrical insulation, and thermal stability. FR-4 is suitable for a wide range of applications, from consumer electronics to industrial equipment.
High Tg FR-4
High Tg FR-4 is a variant of standard FR-4 with improved thermal properties. It has a higher Glass Transition Temperature (Tg), typically above 170°C, making it more resistant to heat and suitable for high-temperature applications.
Polyimide
Polyimide is a high-performance core material known for its exceptional thermal and chemical resistance. It can withstand temperatures up to 260°C and is often used in aerospace, military, and medical applications.
Aluminum
Aluminum core PCBs use an aluminum substrate as the core material. They offer excellent thermal conductivity, making them ideal for applications that require efficient heat dissipation, such as high-power LEDs and automotive electronics.
Core PCB Thickness and Layer Count
The thickness and layer count of a core PCB can vary depending on the specific application and design requirements.
Core Thickness
The most common core thicknesses for PCBs are:
Core Thickness (mm) | Typical Applications |
---|---|
0.2 – 0.4 | Thin, Flexible PCBs for wearable electronics |
0.8 – 1.6 | Standard PCBs for consumer electronics |
2.0 – 3.2 | Heavy-Duty PCBs for industrial applications |
Layer Count
PCBs can have different numbers of layers, depending on the complexity of the circuit and the available space. Common layer counts include:
Layer Count | Description |
---|---|
1 – 2 | Single or double-sided PCBs for simple circuits |
4 – 8 | Multi-layer PCBs for more complex circuits |
10 – 16 | High-density PCBs for advanced electronic devices |
18+ | Specialized PCBs for demanding applications |
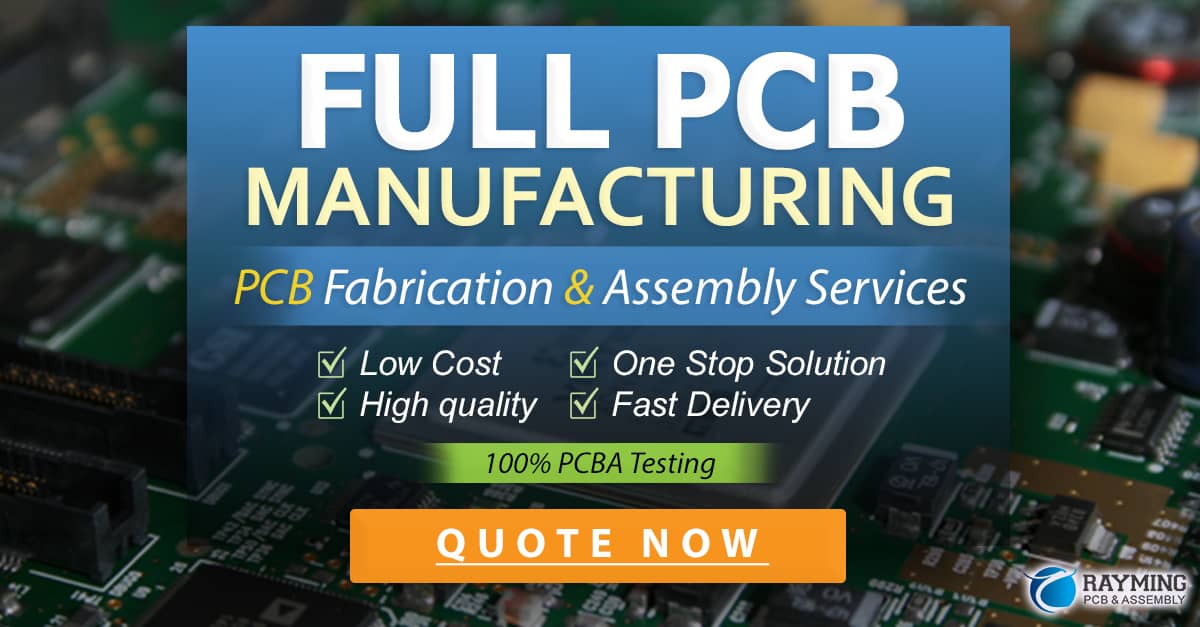
Manufacturing Process of Core PCB
The manufacturing process of a core PCB involves several steps:
-
Material preparation: The core material is cut to the desired size and shape, and any necessary holes are drilled.
-
Copper lamination: Thin layers of copper foil are laminated onto both sides of the core material using heat and pressure.
-
Patterning: The desired circuit pattern is transferred onto the copper layers using photolithography and etching techniques.
-
Layering: Multiple core layers are stacked and laminated together to form a multi-layer PCB.
-
Drilling: Holes are drilled through the PCB to accommodate through-hole components and create electrical connections between layers.
-
Surface finishing: The PCB undergoes various surface treatments, such as solder mask application and surface plating, to protect the copper and facilitate component assembly.
Designing with Core PCB
When designing a PCB, consider the following factors related to the core:
Material Selection
Choose the appropriate core material based on the application requirements, such as thermal stability, electrical insulation, and mechanical strength. Consider factors like operating temperature, environmental conditions, and cost.
Thickness and Layer Count
Determine the optimal core thickness and layer count based on the complexity of the circuit, available space, and manufacturing capabilities. Thicker cores and higher layer counts can accommodate more complex circuits but may increase manufacturing costs.
Thermal Management
Consider the thermal management requirements of the PCB. If the circuit generates significant heat, choose a core material with good thermal conductivity, such as aluminum, or incorporate thermal vias and heatsinks into the design.
Signal Integrity
Ensure proper signal integrity by designing the PCB with appropriate layer stackup and impedance control. Consider factors like dielectric constant, dielectric thickness, and copper thickness to minimize signal distortion and crosstalk.
Frequently Asked Questions (FAQ)
-
What is the most common core material used in PCBs?
FR-4 is the most widely used core material in PCBs due to its excellent mechanical, electrical, and thermal properties. -
Can a PCB have multiple core layers?
Yes, PCBs can have multiple core layers. Multi-layer PCBs are created by stacking and laminating several core layers together. -
What is the purpose of the core in a PCB?
The core in a PCB provides structural support, electrical insulation, and thermal management for the circuit and its components. -
How does the core thickness affect the PCB’s performance?
Thicker cores offer better mechanical strength and thermal dissipation but may increase the overall thickness and weight of the PCB. Thinner cores are suitable for compact and flexible designs but may have limitations in terms of circuit complexity and power handling. -
What are the advantages of using aluminum as a core material?
Aluminum core PCBs offer excellent thermal conductivity, making them ideal for applications that require efficient heat dissipation. They are commonly used in high-power LED lighting, automotive electronics, and other heat-intensive applications.
Conclusion
The core of a PCB plays a vital role in the overall performance and reliability of electronic devices. Understanding the properties and characteristics of different core materials, thicknesses, and layer counts is essential for designing and manufacturing high-quality PCBs. By selecting the appropriate core material and designing the PCB with thermal management, signal integrity, and manufacturing considerations in mind, engineers can create robust and efficient electronic systems.
0 Comments