Introduction to Heavy-Duty PCBs
Heavy-duty PCBs, also known as thick copper PCBs or extreme environment PCBs, are specialized printed circuit boards designed to withstand harsh conditions and extreme temperatures. These PCBs are built with thicker copper layers, ranging from 4 oz to 20 oz or more, compared to the standard 1 oz to 2 oz copper used in regular PCBs. The increased copper thickness enables heavy-duty PCBs to handle higher current loads, improve thermal management, and provide better mechanical stability in demanding applications.
Key Features of Heavy-Duty PCBs
-
Thick Copper Layers: Heavy-duty PCBs utilize copper layers that are significantly thicker than those found in standard PCBs. The increased copper thickness allows for better current carrying capacity and improved thermal dissipation.
-
High Temperature Resistance: These PCBs are designed to operate in high-temperature environments, often exceeding 150°C. They can withstand extreme heat without compromising their performance or reliability.
-
Mechanical Stability: The thicker copper layers and robust construction of heavy-duty PCBs provide enhanced mechanical stability, making them resistant to vibrations, shocks, and physical stress.
-
Improved Thermal Management: The increased copper thickness enables better thermal conductivity, allowing heat to be dissipated more efficiently from the PCB. This helps prevent overheating and ensures stable operation in high-temperature conditions.
-
Wide Range of Applications: Heavy-duty PCBs find applications in various industries, including automotive, aerospace, military, industrial equipment, power electronics, and renewable energy systems.
Advantages of Heavy Copper PCBs in Extreme Environments
1. Enhanced Current Carrying Capacity
One of the primary advantages of Heavy Copper PCBs is their ability to handle higher current loads compared to standard PCBs. The thicker copper layers provide a larger cross-sectional area for current flow, allowing the PCB to carry more current without overheating or suffering from voltage drops. This is particularly important in power-intensive applications, such as motor drives, inverters, and high-power amplifiers.
The current carrying capacity of a PCB is determined by several factors, including the copper thickness, trace width, and the maximum allowable temperature rise. The following table provides a comparison of the current carrying capacity for different copper thicknesses:
Copper Thickness (oz) | Current Carrying Capacity (A/mm) |
---|---|
1 oz | 1.4 |
2 oz | 2.8 |
4 oz | 5.6 |
6 oz | 8.4 |
8 oz | 11.2 |
10 oz | 14.0 |
As evident from the table, increasing the copper thickness significantly enhances the current carrying capacity of the PCB. This allows heavy copper PCBs to handle higher power levels and withstand extreme electrical loads without compromising their performance or reliability.
2. Improved Thermal Management
In high-temperature environments, effective thermal management is crucial for the reliable operation of electronic devices. Heavy copper PCBs excel in this aspect due to their superior thermal conductivity and heat dissipation capabilities. The thicker copper layers act as efficient heat spreaders, quickly transferring heat away from critical components and distributing it evenly across the PCB.
The thermal conductivity of copper is approximately 400 W/mK, which is significantly higher than that of the PCB substrate materials, such as FR-4 (0.3 W/mK). By increasing the copper thickness, heavy-duty PCBs can effectively manage the heat generated by high-power components, preventing localized hot spots and ensuring a more uniform temperature distribution.
Moreover, heavy copper PCBs often incorporate additional thermal management techniques, such as the use of thermal vias, heat sinks, and copper pours. Thermal vias are strategically placed to create a thermal path between the heat-generating components and the copper layers, facilitating efficient heat transfer. Heat sinks can be attached to the PCB to further enhance heat dissipation, while copper pours on the outer layers help spread the heat evenly across the board.
The improved thermal management capabilities of heavy copper PCBs make them ideal for applications involving high-power components, such as power converters, motor controllers, and high-performance processors. By effectively dissipating heat, these PCBs can operate reliably in extreme temperature conditions, reducing the risk of component failure and extending the overall system lifespan.
3. Mechanical Stability and Durability
Heavy copper PCBs offer superior mechanical stability and durability compared to standard PCBs, making them suitable for applications that involve vibrations, shocks, and physical stress. The thicker copper layers provide a more robust foundation for the PCB, reducing the likelihood of copper trace cracking or delamination under mechanical stress.
The increased copper thickness also contributes to the overall rigidity of the PCB. This enhanced stiffness helps prevent warping and bending, which can occur due to thermal expansion and contraction in high-temperature environments. By maintaining its structural integrity, a heavy copper PCB can withstand the mechanical challenges posed by extreme operating conditions.
Furthermore, heavy-duty PCBs often incorporate additional reinforcement techniques to enhance their durability. These techniques include the use of thicker PCB substrates, additional support layers, and the application of conformal coatings or encapsulation materials. Thicker substrates provide a more stable base for the copper layers, while support layers, such as aluminum or stainless steel backing, can be added to increase the PCB’s mechanical strength.
Conformal coatings and encapsulation materials serve as protective barriers against environmental factors, such as moisture, dust, and chemical contaminants. These coatings help prevent corrosion and improve the PCB’s resistance to harsh environments, ensuring long-term reliability and functionality.
The mechanical stability and durability of heavy copper PCBs make them well-suited for applications that require rugged and reliable performance. These applications include automotive electronics, aerospace systems, industrial equipment, and military devices, where the PCBs are subjected to extreme conditions and must withstand constant wear and tear.
Design Considerations for Heavy Copper PCBs
1. Copper Weight Selection
When designing a heavy copper PCB, one of the key considerations is selecting the appropriate copper weight or thickness. The copper weight is typically expressed in ounces per square foot (oz/ft²), with common options ranging from 4 oz to 20 oz or more. The choice of copper weight depends on the specific requirements of the application, such as current carrying capacity, thermal management, and mechanical stability.
Here are some guidelines for selecting the copper weight based on the application:
Copper Weight (oz/ft²) | Typical Applications |
---|---|
4 oz – 6 oz | Power electronics, automotive, industrial control |
8 oz – 10 oz | High-power motor drives, welding equipment, renewable energy |
12 oz – 16 oz | Aerospace, military, extreme environment applications |
18 oz – 20 oz or more | Specialized high-current applications, research and development |
It’s important to note that increasing the copper weight also affects other aspects of the PCB design, such as the minimum trace width and spacing, via size, and drilling capabilities. Thicker copper layers require wider traces and larger vias to maintain manufacturability and reliability. Therefore, the copper weight selection should be balanced with other design constraints and manufacturing limitations.
2. Trace Width and Spacing
When designing heavy copper PCBs, it’s crucial to consider the trace width and spacing requirements to ensure proper current carrying capacity and manufacturability. As the copper thickness increases, the minimum trace width and spacing also need to be adjusted to accommodate the thicker copper layers.
The following table provides general guidelines for minimum trace width and spacing based on different copper weights:
Copper Weight (oz/ft²) | Minimum Trace Width (mm) | Minimum Spacing (mm) |
---|---|---|
4 oz | 0.2 | 0.2 |
6 oz | 0.3 | 0.3 |
8 oz | 0.4 | 0.4 |
10 oz | 0.5 | 0.5 |
12 oz | 0.6 | 0.6 |
These values are just guidelines, and the actual trace width and spacing may vary depending on the specific design requirements, manufacturing capabilities, and the PCB fabricator’s guidelines. It’s essential to consult with the PCB manufacturer to determine the optimal trace width and spacing for the desired copper weight and to ensure manufacturability.
In addition to the minimum trace width and spacing, designers should also consider the current carrying capacity of the traces. The trace width should be sufficient to handle the expected current load without excessive heating or voltage drop. Various online calculators and tools are available to determine the appropriate trace width based on the copper weight, current requirements, and maximum allowable temperature rise.
3. Via Design and Drilling
Via design and drilling are important aspects of heavy copper PCB design, as they impact the interconnection between layers and the overall manufacturability of the board. When working with thicker copper layers, the via size and drilling requirements need to be carefully considered to ensure reliable electrical connections and avoid manufacturing issues.
Here are some key points to keep in mind when designing vias for heavy copper PCBs:
-
Via Diameter: As the copper thickness increases, the minimum via diameter also needs to be increased to accommodate the thicker layers. Larger via diameters are required to ensure proper plating and to maintain the integrity of the via structure.
-
Aspect Ratio: The aspect ratio, which is the ratio of the via depth to its diameter, should be kept within manufacturable limits. High aspect ratios can lead to difficulties in plating and drilling, resulting in incomplete or unreliable vias. A common guideline is to keep the aspect ratio below 8:1 for heavy copper PCBs.
-
Plated Through-Holes (PTHs): PTHs are commonly used in heavy copper PCBs to provide reliable interconnections between layers. The hole size and plating thickness should be carefully specified to ensure adequate electrical and mechanical properties. The plating thickness should be sufficient to handle the expected current load and withstand thermal stress.
-
Filled Vias: In some cases, filled vias may be used to improve thermal conductivity and mechanical stability. Filled vias are created by filling the via holes with a conductive material, such as copper or a high-temperature epoxy. This technique can help dissipate heat more efficiently and provide additional structural support to the PCB.
-
Drilling Capabilities: The drilling process for heavy copper PCBs requires specialized equipment and techniques to handle the thicker copper layers. The drill bits used should be capable of cutting through the thick copper without excessive wear or breakage. It’s important to consult with the PCB manufacturer to ensure that they have the necessary drilling capabilities for the desired copper weight.
When designing vias for heavy copper PCBs, it’s essential to follow the manufacturer’s guidelines and recommendations. Each PCB fabricator may have specific requirements and limitations based on their manufacturing processes and equipment. Collaborating closely with the manufacturer during the design phase can help optimize the via design, ensure manufacturability, and minimize potential issues during fabrication.
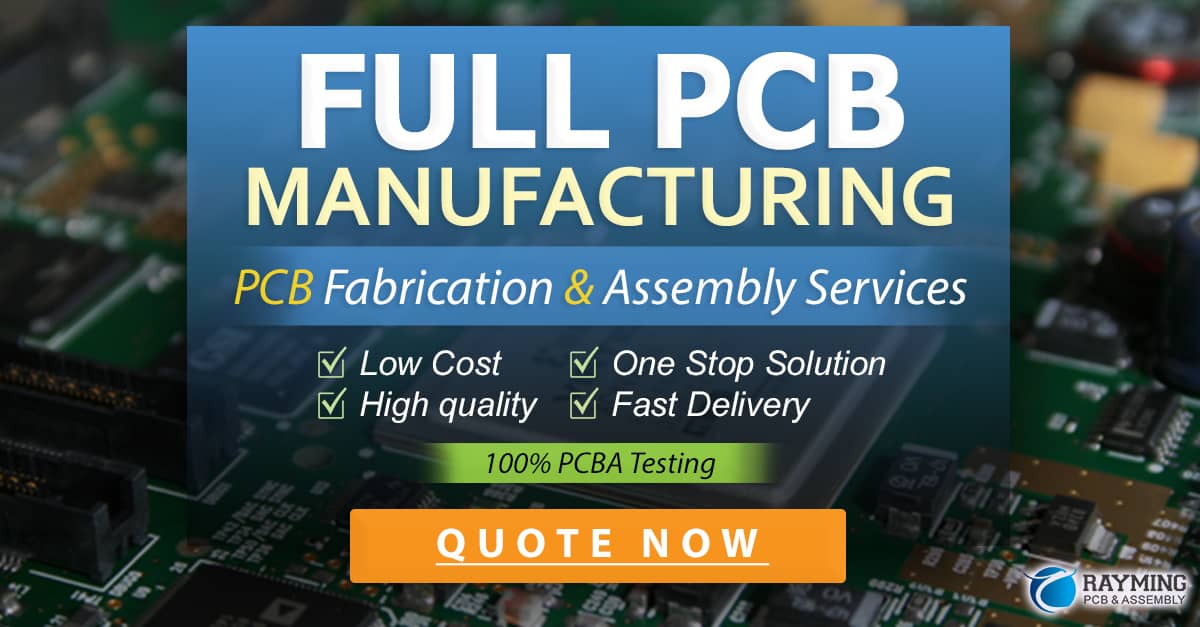
Manufacturing Considerations for Heavy Copper PCBs
1. PCB Fabrication Process
The fabrication process for heavy copper PCBs involves several specialized techniques and considerations to accommodate the thicker copper layers and ensure reliable manufacturing. Here are the key steps involved in the manufacturing of heavy copper PCBs:
-
Material Selection: The PCB substrate material should be carefully selected based on the application requirements, such as the operating temperature range, dielectric constant, and mechanical properties. Common substrate materials for heavy copper PCBs include FR-4, high-Tg FR-4, polyimide, and ceramic.
-
Copper Foil Lamination: The thick copper foils are laminated onto the substrate material using high pressure and temperature. The lamination process ensures a strong bond between the copper layers and the substrate, preventing delamination and ensuring the mechanical integrity of the PCB.
-
Drilling: The via holes and other required holes are drilled through the laminated PCB stack using specialized drilling equipment. The drilling process for heavy copper PCBs requires careful control of the drill feed rate, spindle speed, and drill bit selection to ensure clean and accurate holes.
-
Plating: After drilling, the holes are plated with copper to create electrical connections between the layers. The plating process for heavy copper PCBs may involve additional steps or specialized plating chemistries to ensure uniform coverage and adequate adhesion of the plated copper.
-
Patterning: The copper layers are patterned using photolithography and etching processes to create the desired circuit layout. The patterning process for heavy copper PCBs may require adjusted exposure times and etching parameters to account for the thicker copper layers.
-
Solder Mask and Silkscreen: A solder mask is applied to the PCB to protect the copper traces and prevent short circuits. Silkscreen printing is used to add component labels, logos, and other markings to the PCB surface.
-
Surface Finish: A surface finish, such as HASL (Hot Air Solder Leveling), ENIG (Electroless Nickel Immersion Gold), or OSP (Organic Solderability Preservative), is applied to the exposed copper areas to prevent oxidation and enhance solderability.
-
Electrical Testing: The manufactured PCBs undergo rigorous electrical testing to ensure continuity, insulation resistance, and other critical parameters. Electrical testing is crucial to identify any manufacturing defects or issues before the PCBs are assembled.
Throughout the fabrication process, strict quality control measures are implemented to ensure the consistency and reliability of the heavy copper PCBs. The PCB manufacturer should have experience and expertise in handling thick copper layers and be equipped with the necessary equipment and processes to meet the specific requirements of heavy copper PCB fabrication.
2. Quality Control and Testing
Quality control and testing are critical aspects of heavy copper PCB manufacturing to ensure the reliability and performance of the finished boards. Rigorous testing and inspection procedures are implemented at various stages of the fabrication process to identify and address any potential issues or defects.
Here are some key quality control and testing measures employed in heavy copper PCB manufacturing:
-
Incoming Material Inspection: The raw materials, including the PCB substrate, copper foils, and other components, are inspected for quality and conformance to specifications. Material certificates and test reports are reviewed to ensure the materials meet the required standards.
-
In-Process Inspection: During the fabrication process, various in-process inspections are carried out to monitor the quality and consistency of the PCBs. These inspections may include visual checks, dimensional measurements, and electrical testing at intermediate stages.
-
Automated Optical Inspection (AOI): AOI systems are used to inspect the PCBs for surface defects, such as missing or incorrect components, solder bridges, and trace anomalies. AOI helps identify and resolve issues early in the manufacturing process, reducing the risk of defective boards.
-
Electrical Testing: Comprehensive electrical testing is performed on the finished PCBs to ensure they meet the specified electrical requirements. This may include continuity testing, insulation resistance testing, and high-voltage testing, depending on the application and standards.
-
Microsectioning: Microsectioning involves cross-sectioning the PCB and examining the internal structure under a microscope. This technique is used to verify the integrity of the copper layers, plated through-holes, and other internal features. Microsectioning helps identify any internal defects or manufacturing issues.
-
Environmental Testing: In some cases, heavy copper PCBs may undergo environmental testing to validate their performance under extreme conditions. This may include thermal cycling, thermal shock, vibration testing, and humidity testing, depending on the application requirements.
-
Burn-In Testing: Burn-in testing involves operating the PCBs under elevated temperatures and electrical loads for an extended period to identify any early-life failures or weaknesses. This testing helps ensure the long-term reliability of the PCBs in high-temperature environments.
-
Final Inspection: Before packaging and shipping, the PCBs undergo a final visual inspection to check for any surface defects, cleanliness, and conformance to customer specifications. This final inspection ensures that only high-quality boards are delivered to the customer.
Throughout the quality control process, detailed records and traceability are maintained to track the manufacturing history of each PCB. If any issues or defects are identified, corrective actions are taken, and the affected boards are quarantined or reworked as necessary.
By implementing a robust quality control and testing program, PCB Manufacturers can ensure the reliability, performance, and consistency of heavy copper PCBs, even in the most demanding applications and extreme environments.
Applications of Heavy Copper PCBs
Heavy copper PCBs find applications in various industries and sectors where high current carrying capacity, improved thermal management, and mechanical stability are critical. Some of the key applications of heavy copper PCBs include:
-
Power Electronics: Heavy copper PCBs are extensively used in power electronic applications, such as power converters, inverters, and motor drives. The thick copper layers enable efficient handling of high currents and help dissipate heat generated by power components.
-
Automotive Electronics: In the automotive industry, heavy copper PCBs are used in applications such as electric vehicle battery management systems, power distribution modules, and high-current controllers. The PCBs must withstand harsh environmental conditions, including high temperatures, vibrations, and electrical transients.
-
Aerospace and Defense: Heavy copper PCBs are employed in aerospace and defense applications that require high reliability and performance in extreme environments. These applications include avionics systems, radar modules
0 Comments