Introduction to PCB Composition
Printed Circuit Boards (PCBs) are the backbone of modern electronic devices. They are used in a wide range of applications, from simple consumer electronics to complex aerospace systems. PCBs are composed of various materials that work together to provide a reliable and efficient platform for electronic components. In this article, we will explore the composition of PCB boards in detail.
The Substrate Material
What is a PCB Substrate?
The substrate is the foundation of a PCB. It is the base material on which the conductive traces and components are placed. The substrate provides mechanical support and electrical insulation for the components and traces.
Common PCB Substrate Materials
There are several materials used for PCB substrates, each with its own properties and advantages. The most common PCB substrate materials are:
-
FR-4: FR-4 is the most widely used PCB substrate material. It is a composite material made of fiberglass and epoxy resin. FR-4 offers good mechanical strength, electrical insulation, and thermal stability.
-
Polyimide: Polyimide is a high-performance substrate material used in applications that require high temperature resistance and flexibility. It is commonly used in flexible PCBs (FPCBs).
-
Ceramic: Ceramic substrates are used in high-frequency and high-power applications. They offer excellent thermal conductivity and low dielectric loss.
-
Aluminum: Aluminum substrates are used in applications that require high heat dissipation, such as LED lighting and power electronics.
Substrate Material | Advantages | Applications |
---|---|---|
FR-4 | Good mechanical strength, electrical insulation, and thermal stability | General-purpose PCBs |
Polyimide | High temperature resistance and flexibility | Flexible PCBs |
Ceramic | Excellent thermal conductivity and low dielectric loss | High-frequency and high-power applications |
Aluminum | High heat dissipation | LED lighting and power electronics |
The Conductive Layer
What is a Conductive Layer?
The conductive layer is responsible for carrying electrical signals between components on a PCB. It is typically made of copper, which is an excellent conductor of electricity.
Copper Foil Thickness
The thickness of the copper foil used in PCBs is measured in ounces per square foot (oz/ft²). The most common copper foil thicknesses are:
- 1/2 oz/ft² (17.5 μm)
- 1 oz/ft² (35 μm)
- 2 oz/ft² (70 μm)
Thicker copper foil is used in applications that require higher current carrying capacity or better heat dissipation.
Copper Trace Width and Spacing
The width and spacing of copper traces on a PCB are important factors in determining the board’s electrical characteristics and manufacturing feasibility. The trace width and spacing are typically specified in mils (thousandths of an inch).
Copper Foil Thickness (oz/ft²) | Typical Trace Width (mils) | Typical Trace Spacing (mils) |
---|---|---|
1/2 | 5-10 | 5-10 |
1 | 10-20 | 10-20 |
2 | 20-50 | 20-50 |
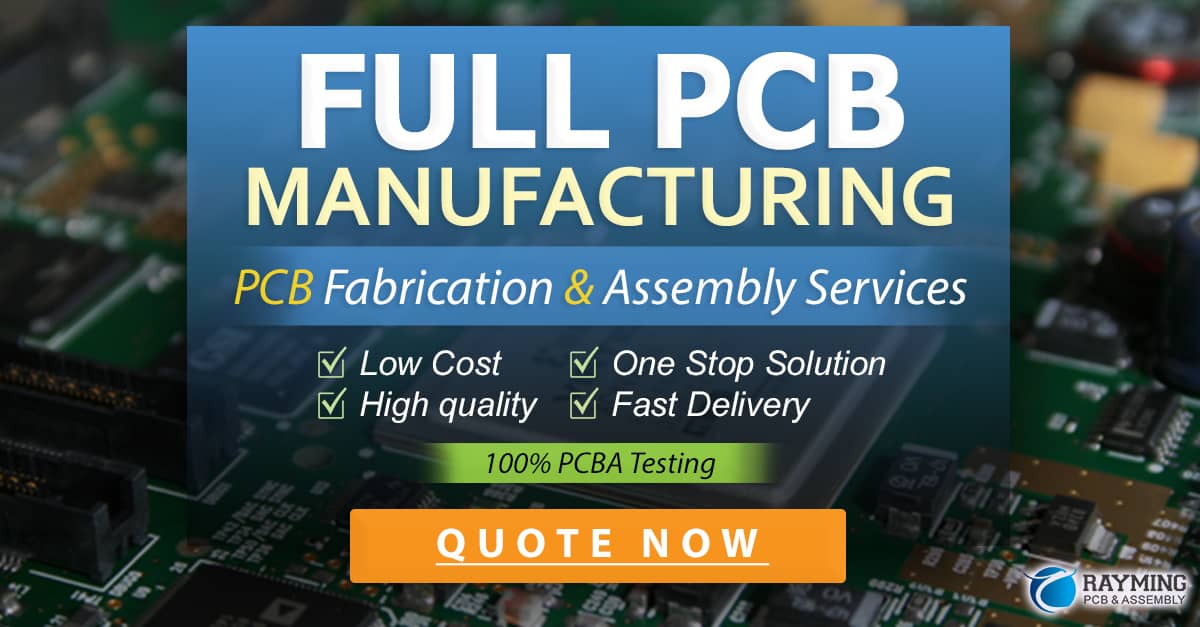
The Solder Mask
What is a Solder Mask?
The solder mask is a protective layer applied over the copper traces on a PCB. It serves several purposes:
- Insulates the copper traces from accidental short circuits
- Protects the copper from oxidation and corrosion
- Provides a surface for printing component designators and other markings
- Improves the aesthetics of the PCB
Solder Mask Materials
The most common solder mask materials are:
-
Liquid Photoimageable Solder Mask (LPISM): LPISM is a liquid coating that is applied to the PCB and then exposed to UV light through a photomask. The unexposed areas are then removed, leaving the desired solder mask pattern.
-
Dry Film Solder Mask (DFSM): DFSM is a solid film that is laminated onto the PCB and then exposed to UV light through a photomask. The unexposed areas are then removed, leaving the desired solder mask pattern.
Solder Mask Colors
Solder masks are available in a variety of colors, with green being the most common. Other popular colors include:
- Red
- Blue
- Yellow
- Black
- White
The choice of solder mask color is often based on aesthetic preferences or to improve the visibility of component markings.
The Silkscreen
What is a Silkscreen?
The silkscreen is a layer of text and graphics printed on top of the solder mask. It is used to provide information about the components and their placement on the PCB.
Silkscreen Materials
Silkscreen ink is typically a single-component epoxy-based ink that is cured using heat or UV light. The most common silkscreen colors are white and yellow, as they provide good contrast against the solder mask.
Silkscreen Information
The silkscreen layer typically includes the following information:
- Component designators (e.g., R1, C2, U3)
- Component values (e.g., 10K, 0.1uF, 74HC00)
- Polarity markers for polarized components (e.g., electrolytic capacitors, diodes)
- Fiducial markers for automated assembly
- Company logos and product information
The Surface Finish
What is a Surface Finish?
The surface finish is a coating applied to the exposed copper on a PCB to protect it from oxidation and to improve solderability. There are several types of surface finishes, each with its own advantages and disadvantages.
Common Surface Finishes
-
Hot Air Solder Leveling (HASL): HASL is the most common surface finish. It involves dipping the PCB in molten solder and then using hot air to level the solder on the surface. HASL provides good solderability and is relatively inexpensive.
-
Electroless Nickel Immersion Gold (ENIG): ENIG is a two-layer surface finish consisting of a nickel layer and a thin gold layer. It provides excellent solderability, flatness, and shelf life, but is more expensive than HASL.
-
Immersion Silver (IAg): IAg is a single-layer surface finish that provides good solderability and is less expensive than ENIG. However, it has a shorter shelf life and can tarnish over time.
-
Immersion Tin (ISn): ISn is a single-layer surface finish that provides good solderability and is less expensive than ENIG and IAg. However, it has a shorter shelf life and can form whiskers over time.
Surface Finish | Advantages | Disadvantages |
---|---|---|
HASL | Good solderability, relatively inexpensive | Uneven surface, potential for thermal shock |
ENIG | Excellent solderability, flatness, and shelf life | More expensive than other finishes |
IAg | Good solderability, less expensive than ENIG | Shorter shelf life, can tarnish over time |
ISn | Good solderability, less expensive than ENIG and IAg | Shorter shelf life, can form whiskers over time |
Frequently Asked Questions (FAQ)
1. What is the most common PCB substrate material?
The most common PCB substrate material is FR-4, which is a composite material made of fiberglass and epoxy resin. FR-4 offers good mechanical strength, electrical insulation, and thermal stability, making it suitable for a wide range of applications.
2. What is the purpose of the solder mask on a PCB?
The solder mask serves several purposes:
- Insulates the copper traces from accidental short circuits
- Protects the copper from oxidation and corrosion
- Provides a surface for printing component designators and other markings
- Improves the aesthetics of the PCB
3. What is the difference between HASL and ENIG surface finishes?
HASL (Hot Air Solder Leveling) and ENIG (Electroless Nickel Immersion Gold) are two common surface finishes for PCBs. The main differences are:
- HASL involves dipping the PCB in molten solder and using hot air to level the solder on the surface, while ENIG is a two-layer finish consisting of a nickel layer and a thin gold layer.
- ENIG provides better solderability, flatness, and shelf life compared to HASL, but is more expensive.
4. What information is typically included on the silkscreen layer of a PCB?
The silkscreen layer typically includes:
- Component designators (e.g., R1, C2, U3)
- Component values (e.g., 10K, 0.1uF, 74HC00)
- Polarity markers for polarized components (e.g., electrolytic capacitors, diodes)
- Fiducial markers for automated assembly
- Company logos and product information
5. Why are copper trace width and spacing important in PCB design?
The width and spacing of copper traces on a PCB are important factors in determining the board’s electrical characteristics and manufacturing feasibility. Wider traces can carry more current and provide better heat dissipation, but require more space on the board. Narrower traces allow for denser layouts but may have limitations in terms of current carrying capacity and manufacturing capabilities. Proper trace spacing is necessary to prevent signal interference and short circuits.
Conclusion
In this article, we have explored the composition of PCB boards in detail. We have discussed the various materials used in PCB Construction, including the substrate, conductive layer, solder mask, silkscreen, and surface finish. Each of these components plays a crucial role in the performance and reliability of the PCB.
Understanding the composition of PCBs is essential for designers, manufacturers, and end-users alike. By selecting the appropriate materials and specifying the correct parameters, designers can ensure that their PCBs meet the required electrical, mechanical, and environmental specifications. Manufacturers can optimize their processes to produce high-quality boards efficiently and consistently. End-users can benefit from a deeper understanding of the technology behind the electronic devices they use every day.
As technology continues to advance, the composition of PCBs will likely evolve to meet new challenges and requirements. However, the fundamental principles and materials discussed in this article will remain relevant for the foreseeable future.
0 Comments