Introduction to Coefficient of Thermal Expansion (CTE)
The Coefficient of Thermal Expansion (CTE) is a critical parameter in the design and manufacturing of Printed Circuit Boards (PCBs). It is a measure of how much a material expands or contracts with changes in temperature. In the context of PCBs, CTE plays a crucial role in ensuring the reliability and longevity of the board and its components.
What is a Printed Circuit Board (PCB)?
A Printed Circuit Board (PCB) is a fundamental component in modern electronic devices. It is a flat board made of insulating materials, such as fiberglass or composite epoxy, with conductive pathways etched or printed onto its surface. These pathways, known as traces, connect various electronic components, such as resistors, capacitors, and integrated circuits, to form a functional electronic circuit.
PCBs come in various types, including:
- Single-sided PCBs: Components are mounted on one side of the board, with traces on the opposite side.
- Double-sided PCBs: Components and traces are present on both sides of the board.
- Multi-layer PCBs: These boards have multiple layers of traces separated by insulating layers, allowing for more complex circuitry and better signal integrity.
The Importance of CTE in PCB Design
The Coefficient of Thermal Expansion is a critical factor in PCB design because it directly affects the reliability and performance of the board. When a PCB is subjected to temperature changes, its materials expand or contract at different rates. If the CTE of the PCB substrate and its components are not properly matched, it can lead to various issues, such as:
- Warping or deformation of the board
- Cracking of solder joints
- Delamination of layers in multi-layer PCBs
- Stress on components, leading to premature failure
By understanding and controlling the CTE of the materials used in a PCB, designers can minimize these issues and ensure the long-term reliability of the board.
Factors Affecting CTE in PCBs
Several factors influence the Coefficient of Thermal Expansion in PCBs. These factors must be considered when designing and manufacturing PCBs to ensure optimal performance and reliability.
PCB Substrate Material
The choice of PCB substrate material is one of the most significant factors affecting CTE. Common PCB substrate materials include:
-
FR-4: A composite material made of woven fiberglass and epoxy resin, FR-4 is the most widely used PCB substrate. It has a CTE of approximately 14-17 ppm/°C (parts per million per degree Celsius) in the x and y directions, and 50-70 ppm/°C in the z direction.
-
Polyimide: Polyimide is a high-performance substrate material with excellent thermal stability and a lower CTE compared to FR-4. It has a CTE of about 12-16 ppm/°C in the x and y directions, and 30-60 ppm/°C in the z direction.
-
Ceramic: Ceramic substrates, such as alumina (Al2O3) and aluminum nitride (AlN), have very low CTEs, typically in the range of 4-7 ppm/°C. They are used in high-reliability applications where thermal management is critical.
Substrate Material | CTE (x, y) (ppm/°C) | CTE (z) (ppm/°C) |
---|---|---|
FR-4 | 14-17 | 50-70 |
Polyimide | 12-16 | 30-60 |
Alumina (Al2O3) | 4-7 | 4-7 |
Aluminum Nitride (AlN) | 4-5 | 4-5 |
Component Materials
The materials used in the components mounted on a PCB also contribute to the overall CTE of the board. Common component materials include:
- Silicon: Most integrated circuits (ICs) are made of silicon, which has a CTE of about 2.6 ppm/°C.
- Copper: Copper is used for traces and vias in PCBs, and it has a CTE of approximately 17 ppm/°C.
- Solder: The type of solder used in PCB Assembly affects the CTE. Lead-based solders have a CTE of around 25 ppm/°C, while lead-free solders have a CTE of about 23 ppm/°C.
Component Material | CTE (ppm/°C) |
---|---|
Silicon | 2.6 |
Copper | 17 |
Lead-based solder | 25 |
Lead-free solder | 23 |
Temperature Range
The temperature range experienced by a PCB during its operation also affects the impact of CTE on the board’s reliability. PCBs designed for harsh environments, such as automotive or aerospace applications, must withstand wider temperature ranges and more extreme temperature cycling compared to consumer electronics.
Managing CTE in PCB Design
To minimize the impact of CTE mismatches and ensure the reliability of PCBs, designers can employ various strategies:
Material Selection
Choosing PCB substrate and component materials with similar CTEs can help reduce stress and deformation caused by temperature changes. For example, using a polyimide substrate with a lower CTE can be beneficial when using components with low CTEs, such as ceramic capacitors or silicon ICs.
Thermal Management
Proper thermal management can help minimize temperature gradients across the PCB, reducing the impact of CTE mismatches. This can be achieved through the use of heatsinks, thermal vias, and other cooling techniques.
Flexible Circuit Design
In some cases, using flexible circuits can help absorb the stress caused by CTE mismatches. Flexible circuits, made of materials like polyimide, can deform without causing damage to the components or traces.
Stress Relief Features
Incorporating stress relief features into the PCB design can help mitigate the effects of CTE mismatches. These features include:
- Strain relief cutouts around connectors and large components
- Serpentine traces that can flex and absorb stress
- Selective reinforcement of high-stress areas using materials with lower CTEs
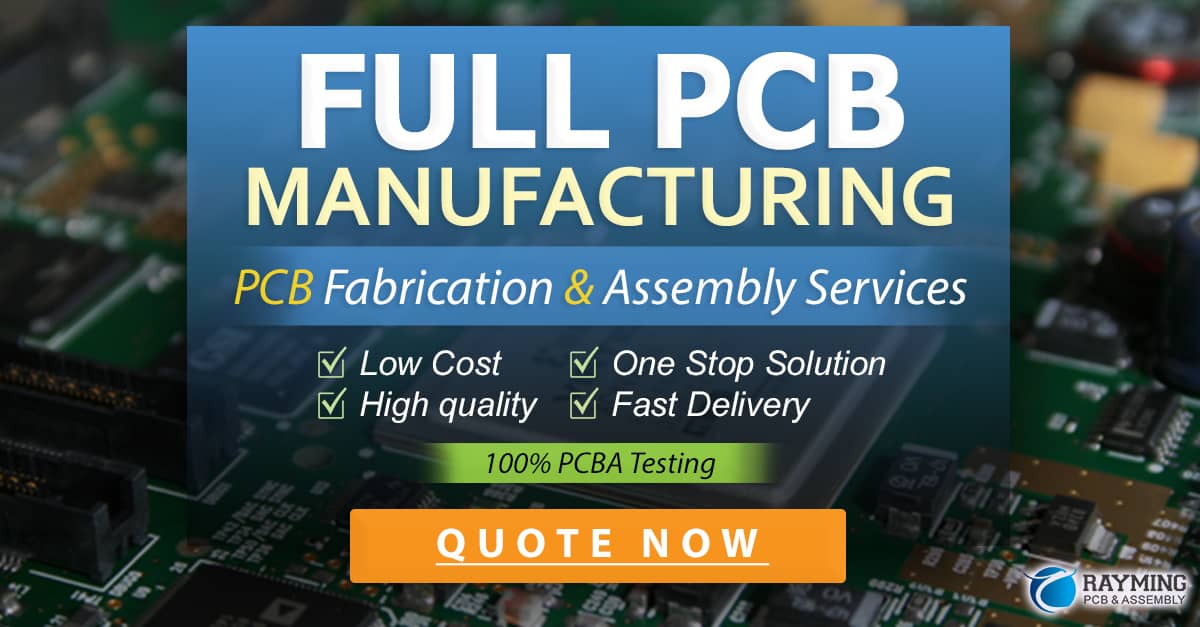
FAQs
-
Q: What is the most common PCB substrate material, and what is its CTE?
A: FR-4 is the most widely used PCB substrate material. It has a CTE of approximately 14-17 ppm/°C in the x and y directions, and 50-70 ppm/°C in the z direction. -
Q: How does the choice of solder affect the CTE of a PCB?
A: Lead-based solders have a CTE of around 25 ppm/°C, while lead-free solders have a CTE of about 23 ppm/°C. The choice of solder can impact the overall CTE of the PCB and the stress on solder joints. -
Q: What are some strategies for managing CTE mismatches in PCB design?
A: Strategies for managing CTE mismatches include careful material selection, proper thermal management, the use of flexible circuits, and the incorporation of stress relief features in the PCB design. -
Q: How does the temperature range affect the impact of CTE on PCB reliability?
A: PCBs designed for harsh environments, such as automotive or aerospace applications, must withstand wider temperature ranges and more extreme temperature cycling compared to consumer electronics. This makes the management of CTE mismatches even more critical in these applications. -
Q: What are some common issues caused by CTE mismatches in PCBs?
A: Common issues caused by CTE mismatches include warping or deformation of the board, cracking of solder joints, delamination of layers in multi-layer PCBs, and stress on components, leading to premature failure.
Conclusion
The Coefficient of Thermal Expansion (CTE) is a crucial parameter in the design and manufacturing of Printed Circuit Boards (PCBs). By understanding the factors affecting CTE, such as substrate materials, component materials, and temperature range, designers can make informed decisions to minimize the impact of CTE mismatches and ensure the reliability and longevity of the board.
Strategies for managing CTE in PCB design include careful material selection, proper thermal management, the use of flexible circuits, and the incorporation of stress relief features. By employing these techniques, designers can create PCBs that can withstand the stresses caused by temperature changes and deliver optimal performance in a wide range of applications.
0 Comments