Understanding SMT stencil area ratio
What is SMT Stencil Area Ratio?
SMT (Surface Mount Technology) stencil area ratio is a crucial parameter in the SMT assembly process. It refers to the ratio of the aperture opening area to the wall area of the stencil. The area ratio determines the amount of solder paste deposited on the PCB (Printed Circuit Board) pads, which directly affects the quality of the solder joint.
The area ratio is calculated using the following formula:
Area Ratio = (Aperture Opening Area) / (Aperture Wall Area)
For example, if the aperture opening is 0.5mm x 0.5mm and the stencil thickness is 0.1mm, the area ratio would be:
Area Ratio = (0.5mm x 0.5mm) / (4 x 0.1mm x 0.5mm) = 1.25
Why is SMT Stencil Area Ratio Important?
The area ratio is crucial in determining the printability of the solder paste. A high area ratio means more solder paste will be deposited on the PCB pads, while a low area ratio results in less solder paste deposition. Too much or too little solder paste can lead to defects such as bridging, insufficients, or tombstoning.
The ideal area ratio depends on various factors such as the solder paste type, stencil thickness, and aperture size. Generally, an area ratio between 0.66 and 1.5 is considered acceptable for most SMT applications.
Factors Affecting SMT Stencil Area Ratio
Several factors can influence the area ratio and the resulting solder paste deposition:
-
Stencil Thickness: Thicker stencils have a lower area ratio, while thinner stencils have a higher area ratio. The stencil thickness is usually determined by the component pitch and the required solder volume.
-
Aperture Size: Larger apertures have a higher area ratio compared to smaller apertures. The aperture size is determined by the component pad size and the required solder volume.
-
Solder Paste Type: Different solder paste formulations have different printability characteristics. Some pastes may require a higher or lower area ratio for optimal performance.
-
PCB Pad Design: The shape and size of the PCB pads can affect the area ratio. Pads with a larger surface area will have a higher area ratio compared to smaller pads.
Optimizing SMT Stencil Area Ratio
Stencil Design Guidelines
To ensure optimal solder paste deposition and minimize defects, follow these stencil design guidelines:
-
Use appropriate stencil thickness: Select the stencil thickness based on the component pitch and the required solder volume. Thicker stencils are suitable for larger components, while thinner stencils are better for smaller components.
-
Optimize aperture size: Choose the aperture size based on the component pad size and the required solder volume. The aperture should be slightly larger than the pad to allow for proper solder paste release.
-
Consider solder paste type: Select a solder paste that is compatible with the stencil design and the desired area ratio. Some pastes may require adjustments to the stencil design for optimal performance.
-
Minimize stencil distortion: Use a high-quality stencil material and proper mounting techniques to minimize stencil distortion during printing. Distortion can affect the area ratio and lead to inconsistent solder paste deposition.
PCB design guidelines
In addition to stencil design, the PCB layout can also impact the area ratio and solderability:
-
Use appropriate pad sizes: Design the PCB pads to match the component size and the required solder volume. Pads that are too small or too large can lead to soldering defects.
-
Maintain proper pad spacing: Ensure sufficient spacing between pads to avoid bridging or solder paste contamination. The spacing should be based on the stencil thickness and the solder paste type.
-
Avoid pad shape irregularities: Use simple, rectangular pad shapes whenever possible. Irregular pad shapes can affect the area ratio and lead to inconsistent solder paste deposition.
-
Consider via-in-pad design: If using via-in-pad technology, ensure the via size and location do not interfere with the solder paste deposition. The via should be small enough to maintain a sufficient area ratio.
Troubleshooting SMT Stencil Area Ratio Issues
Common Defects Related to Area Ratio
Improper area ratio can lead to various soldering defects, such as:
-
Bridging: Excessive solder paste deposition due to a high area ratio can cause solder bridges between adjacent pads.
-
Insufficients: Insufficient solder paste deposition due to a low area ratio can result in weak or open solder joints.
-
Tombstoning: Uneven solder paste deposition due to an inconsistent area ratio can cause components to stand up vertically during reflow.
-
Solder Balls: Excessive solder paste deposition can lead to the formation of small solder balls around the solder joint.
Corrective Actions
If encountering area ratio-related defects, consider the following corrective actions:
-
Adjust stencil thickness: If the area ratio is too high or too low, consider changing the stencil thickness to achieve the desired solder paste volume.
-
Modify aperture size: Adjust the aperture size to optimize the area ratio based on the component pad size and the required solder volume.
-
Change solder paste type: If the current solder paste is not compatible with the stencil design, consider switching to a paste with better printability characteristics.
-
Improve PCB pad design: If the PCB pads are contributing to area ratio issues, modify the pad size, shape, or spacing to ensure proper solder paste deposition.
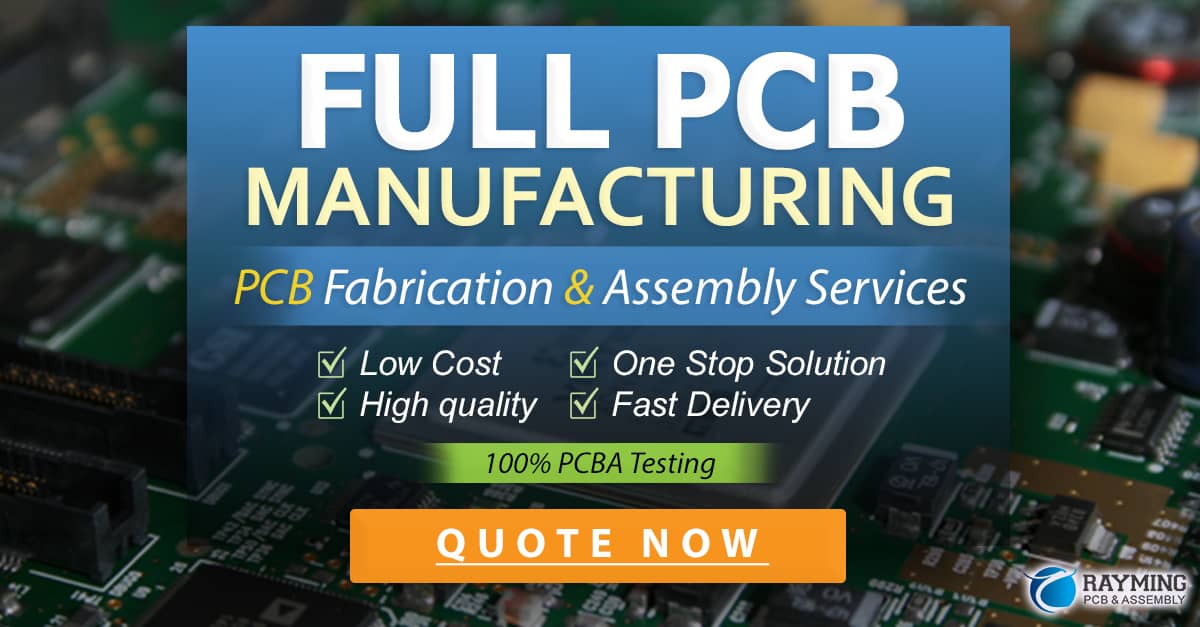
Best Practices for SMT Stencil Area Ratio
To achieve optimal solder paste deposition and minimize defects, follow these best practices:
-
Conduct thorough stencil design review: Before manufacturing the stencil, review the design carefully to ensure the area ratio is within the acceptable range for all apertures.
-
Perform regular stencil maintenance: Clean and inspect the stencil regularly to prevent solder paste buildup or damage that can affect the area ratio.
-
Monitor solder paste print quality: Regularly check the solder paste print quality using a solder paste inspection system to detect any area ratio-related issues early in the process.
-
Implement a robust process control system: Establish a process control system that includes monitoring and controlling critical parameters such as stencil tension, print pressure, and print speed to maintain consistent area ratio.
-
Collaborate with suppliers: Work closely with your stencil and solder paste suppliers to select the best materials and designs for your specific application and area ratio requirements.
Frequently Asked Questions (FAQ)
-
What is the ideal area ratio for SMT stencils?
The ideal area ratio depends on various factors such as the solder paste type, stencil thickness, and aperture size. Generally, an area ratio between 0.66 and 1.5 is considered acceptable for most SMT applications. -
How does stencil thickness affect the area ratio?
Thicker stencils have a lower area ratio, while thinner stencils have a higher area ratio. The stencil thickness is usually determined by the component pitch and the required solder volume. -
Can the PCB pad design impact the area ratio?
Yes, the shape and size of the PCB pads can affect the area ratio. Pads with a larger surface area will have a higher area ratio compared to smaller pads. It is important to design the pads to match the component size and the required solder volume. -
What are some common defects caused by improper area ratio?
Improper area ratio can lead to various soldering defects, such as bridging (excessive solder paste), insufficients (insufficient solder paste), tombstoning (uneven solder paste), and solder balls (excessive solder paste). -
How can I troubleshoot area ratio-related issues?
To troubleshoot area ratio-related issues, consider adjusting the stencil thickness, modifying the aperture size, changing the solder paste type, or improving the PCB pad design. It is also important to conduct regular stencil maintenance, monitor solder paste print quality, and implement a robust process control system.
Conclusion
SMT stencil area ratio is a critical parameter that directly affects the quality of solder paste deposition and the resulting solder joint. By understanding the factors that influence the area ratio, following stencil and PCB design guidelines, and implementing best practices for process control, manufacturers can optimize their SMT assembly process and minimize defects related to improper area ratio.
Regular monitoring, maintenance, and collaboration with suppliers are essential to ensure consistent and reliable solder paste deposition. By paying close attention to the area ratio and its impact on the SMT process, manufacturers can improve yield, reduce rework, and enhance the overall quality of their electronic assemblies.
0 Comments