Introduction to Solder Paste Tack
Solder paste tack is a crucial property in the surface mount technology (SMT) assembly process. It refers to the ability of solder paste to hold components in place during the placement and reflow stages. Tack is essential for maintaining component alignment and preventing tombstoning, which can lead to defects and reduced yields. Understanding solder paste tack is vital for optimizing the SMT process and achieving high-quality PCB assemblies.
Definition of Solder Paste Tack
Solder paste tack can be defined as the adhesive force that exists between the solder paste and the component after placement. It is a measure of how well the solder paste can resist the movement of components due to vibration, handling, or other disturbances before the reflow process. Tack is a time-dependent property, and it can be influenced by various factors such as solder paste composition, storage conditions, and environmental factors.
Importance of Solder Paste Tack in SMT Assembly
Solder paste tack plays a critical role in the SMT assembly process for several reasons:
-
Component Placement Accuracy: High tack ensures that components remain in their designated positions after placement, maintaining the desired alignment and spacing.
-
Preventing Tombstoning: Tombstoning occurs when one end of a component lifts off the PCB during reflow, resulting in a defective solder joint. Adequate tack minimizes the risk of tombstoning by holding the component securely in place.
-
Handling and Transportation: Tack allows PCBs to be handled and transported between the placement and reflow stages without component displacement.
-
Accommodating Variations: Tack helps accommodate minor variations in component placement, ensuring that components are held in place even if they are slightly misaligned.
Factors Affecting Solder Paste Tack
Several factors can influence the tack of solder paste, including:
Solder Paste Composition
The composition of solder paste, particularly the flux system and the metal alloy, has a significant impact on tack.
Flux System
The flux system in solder paste serves multiple purposes, including promoting wetting, removing oxides, and providing tack. Different types of fluxes, such as rosin-based, water-soluble, or no-clean fluxes, can exhibit varying levels of tack. The choice of flux depends on the specific application requirements, such as the need for cleanability, compatibility with the PCB and components, and environmental considerations.
Metal Alloy
The metal alloy used in solder paste also affects tack. Common alloys include tin-lead (SnPb) and lead-free alloys such as tin-silver-copper (SAC). Lead-free alloys generally have higher melting points and may require different tack characteristics compared to SnPb alloys. The particle size distribution and shape of the metal particles in the solder paste can also influence tack.
Storage Conditions
Proper storage conditions are crucial for maintaining the tack of solder paste.
Temperature
Solder paste should be stored at a controlled temperature, typically between 0°C and 10°C (32°F to 50°F). Exposure to high temperatures can cause the solder paste to dry out, reducing its tack and performance.
Humidity
Humidity control is essential for preserving solder paste tack. Excessive humidity can lead to moisture absorption, which can negatively affect the rheological properties and tack of the solder paste. Ideal humidity levels for storage are usually below 60% relative humidity.
Shelf Life
Solder paste has a limited shelf life, and using solder paste beyond its expiration date can result in reduced tack and poor performance. The shelf life of solder paste varies depending on the manufacturer and the specific formulation, but it typically ranges from 3 to 6 months when stored under recommended conditions.
Environmental Factors
Environmental factors during the SMT assembly process can also impact solder paste tack.
Temperature and Humidity
The ambient temperature and humidity in the production environment can affect solder paste tack. High temperatures can cause the solder paste to dry out, while high humidity can lead to moisture absorption. Maintaining a consistent and controlled environment is crucial for optimal tack performance.
Airflow
Excessive airflow in the production area can accelerate the drying of solder paste, reducing its tack. Proper ventilation and airflow management are necessary to minimize the impact on solder paste tack.
Measuring Solder Paste Tack
Measuring solder paste tack is essential for process control and quality assurance. There are several methods used to quantify tack, including:
Tack Test Methods
Probe Tack Test
The probe tack test involves lowering a probe onto the surface of the solder paste, allowing it to dwell for a specified time, and then lifting the probe to measure the force required to separate it from the paste. This test provides a quantitative measure of tack and can be used to compare different solder paste formulations or monitor tack over time.
Slump Test
The slump test assesses the ability of solder paste to resist slumping or spreading after deposition. A pattern of solder paste is printed on a test board, and the board is then inclined at a specific angle for a set duration. The amount of slump or spreading is measured, providing an indication of the paste’s tack and stability.
Tack Measurement Equipment
Various equipment is available for measuring solder paste tack, including:
- Tack testers: Specialized instruments that measure the force required to separate a probe from the solder paste surface.
- Rheometers: Instruments that measure the rheological properties of solder paste, including tack, viscosity, and yield stress.
- Slump testers: Equipment that measures the slump or spreading of solder paste patterns on inclined test boards.
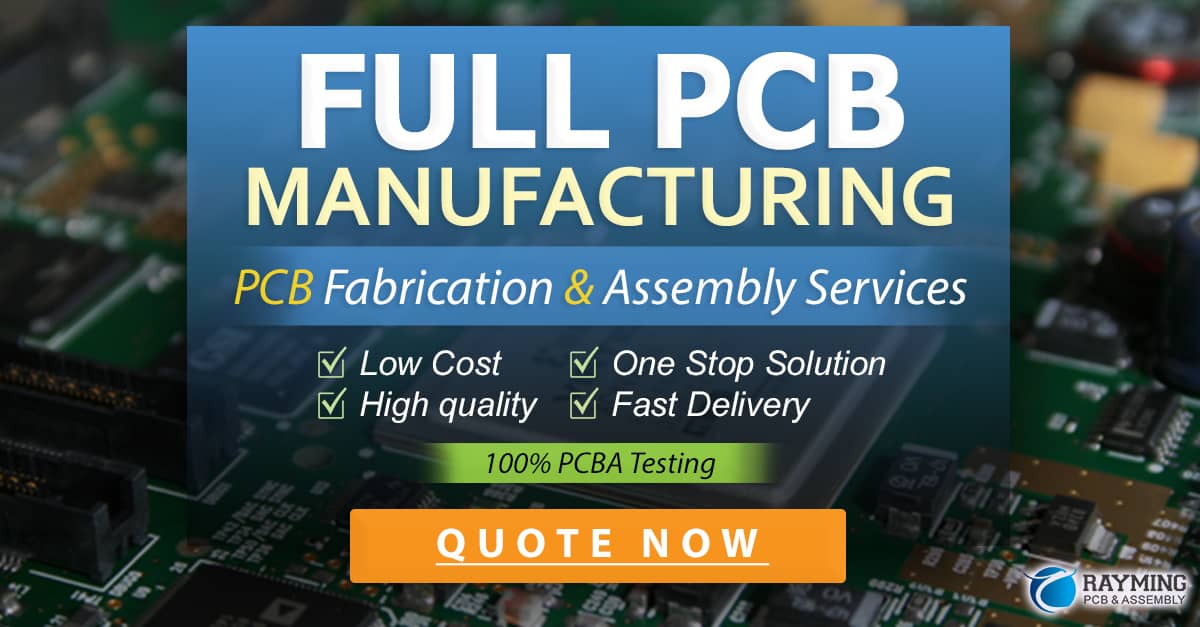
Optimizing Solder Paste Tack
To optimize solder paste tack and improve SMT assembly performance, consider the following strategies:
Solder Paste Selection
Select a solder paste with the appropriate tack characteristics for your specific application. Consult with solder paste manufacturers and review technical datasheets to choose a paste that meets your requirements for tack, printability, and reflow performance.
Storage and Handling
Ensure proper storage and handling of solder paste to maintain its tack. Follow the manufacturer’s recommendations for storage temperature, humidity, and shelf life. Implement a first-in, first-out (FIFO) inventory system to use older solder paste first and prevent expiration.
Process Control
Monitor and control the SMT assembly process parameters that can affect solder paste tack, such as:
- Stencil printing parameters (squeegee pressure, speed, separation speed)
- Component placement force and speed
- Reflow profile (ramp rates, peak temperature, time above liquidus)
Regularly measure and track solder paste tack using appropriate test methods and equipment to ensure consistency and identify any deviations from the desired tack level.
Environmental Control
Maintain a controlled environment in the production area to minimize the impact of temperature, humidity, and airflow on solder paste tack. Use air conditioning and humidity control systems to keep the environment within the recommended ranges for optimal tack performance.
Frequently Asked Questions (FAQ)
-
What is solder paste tack, and why is it important?
Solder paste tack refers to the adhesive force that holds components in place after placement and before reflow. It is important because it ensures component alignment, prevents tombstoning, and allows for handling and transportation of PCBs without component displacement. -
What factors can affect solder paste tack?
Solder paste tack can be affected by several factors, including the solder paste composition (flux system and metal alloy), storage conditions (temperature, humidity, and shelf life), and environmental factors during the SMT assembly process (temperature, humidity, and airflow). -
How is solder paste tack measured?
Solder paste tack can be measured using various methods, such as the probe tack test, which measures the force required to separate a probe from the solder paste surface, and the slump test, which assesses the ability of solder paste to resist slumping or spreading after deposition. Specialized equipment like tack testers and rheometers are used for tack measurement. -
What can be done to optimize solder paste tack?
To optimize solder paste tack, consider selecting a solder paste with the appropriate tack characteristics for your application, ensuring proper storage and handling, implementing process control measures, and maintaining a controlled environment in the production area. -
How does solder paste tack differ from solder paste viscosity?
Solder paste tack and viscosity are related but distinct properties. Tack refers to the adhesive force between the solder paste and components, while viscosity is a measure of the paste’s resistance to flow. Both tack and viscosity are important for the performance of solder paste in the SMT assembly process, but they serve different purposes. Tack is crucial for holding components in place, while viscosity affects the printability and dispensing of solder paste.
Conclusion
Solder paste tack is a critical property in the SMT assembly process, ensuring component alignment, preventing defects, and enabling the handling and transportation of PCBs. Understanding the factors that influence tack, such as solder paste composition, storage conditions, and environmental factors, is essential for optimizing the SMT process and achieving high-quality PCB assemblies.
By selecting the appropriate solder paste, implementing proper storage and handling procedures, monitoring tack using suitable measurement methods, and maintaining a controlled production environment, manufacturers can optimize solder paste tack and improve the overall performance of their SMT assembly process. This, in turn, leads to higher yields, fewer defects, and more reliable electronic products.
As the electronics industry continues to evolve, with increasingly complex and miniaturized components, the importance of solder paste tack will only grow. Staying informed about the latest developments in solder paste technology, testing methods, and best practices will be essential for manufacturers to remain competitive and meet the ever-changing demands of the market.
0 Comments