Introduction to SMT
Surface Mount Technology (SMT) is a method for constructing electronic circuits in which the components are mounted directly onto the surface of printed circuit boards (PCBs). It has largely replaced the through-hole technology construction method of fitting components with wire leads into holes in the circuit board. SMT allows for smaller components, higher circuit densities, and faster automated assembly compared to through-hole technology.
How SMT Works
The basic steps in the SMT process are:
-
Solder paste is applied to the PCB pads where components will be placed. The paste is typically applied using a stencil printer.
-
The components are placed on the PCB. This is usually done by an automated pick-and-place machine, but can also be done manually for low volume production or prototypes.
-
The PCB is sent through a reflow oven. The solder paste melts and forms the electrical and mechanical connection between the component and PCB pad.
-
The PCB may go through additional processes like cleaning, inspection, and testing before the SMT assembly process is complete.
SMT Component Packages
SMT components come in a variety of package types. Some of the most common are:
Package | Description |
---|---|
Chip (XSMN) | Small, rectangular components with metallized terminals on 2 or 4 sides |
SOT (Small Outline Transistor) | Transistors and diodes in a small molded package |
SOIC (Small Outline Integrated Circuit) | ICs in a molded package with gull-wing leads on 2 sides |
QFP (Quad Flat Package) | Square IC package with gull-wing leads on all 4 sides |
BGA (Ball Grid Array) | IC package with solder balls on the bottom in a grid pattern |
The trend has been towards smaller packages over time. Smaller packages allow for denser PCB layouts but require more precise manufacturing processes.
Solder Paste
Solder paste is a mixture of tiny solder balls (powder) suspended in flux. It is a gray, putty-like material. The composition of the alloy and flux depends on the application.
The most common alloys for SMT are tin-lead (SnPb) and lead-free SAC alloys, which contain tin, silver and copper. Tin-lead solder paste is eutectic at about 63% tin and has a melting point of 183°C. Lead-free alloys melt at higher temperatures, typically 217-220°C.
Solder paste is classified by its particle size, metal content, flux type, and viscosity. Particle size is given by mesh designations like Type 3 (-325/+500 mesh) and Type 4 (-400/+635 mesh), where the numbers refer to the mesh sizes of the sieves used to classify the powder.
The flux type can be rosin (R), organic (OR) or inorganic (IN). The letters L, M, and H designate low, medium and high activity levels. So a solder paste with an ROL1 flux would be a rosin flux with low activity.
Pick and Place Machines
An automated pick and place (P&P) machine is used to place SMT components on a PCB. Basic elements of a P&P machine are:
- Feeders that hold the component reels, sticks or trays and present them to the machine
- A head with multiple nozzles to pick up components from the feeders and place them on the PCB
- A conveyor system to transport PCBs through the machine
- A vision system to inspect the PCB and components and provide alignment data to the placement head
- Software to optimize the component placement sequence and routing
P&P machines are available in a wide range of speeds and capabilities depending on the intended production volume.Very high-speed machines can place over 100,000 components per hour.
Reflow Soldering
After component placement, the PCBs are run through a reflow oven to melt the solder paste and permanently attach the components. The reflow process generally follows a temperature profile that looks like this:
(Image credit: Wikipedia)
- Preheat: The PCB is heated to 150-180°C to activate the flux and remove solvents
- Thermal soak: Temperature is stabilized to minimize differences across the PCB
- Reflow: The solder melts at 220-250°C and wets the component leads and pads
- Cooling: The PCB cools and solder solidifies to create solder joints
The exact temperatures and durations of each phase will vary based on the solder paste composition, component types, and PCB design. Convection reflow ovens with multiple heating zones are used to achieve the desired profile.
Benefits of SMT
SMT provides many benefits compared to through-hole technology:
Smaller Size
SMT components are much smaller than their through-hole counterparts – often less than half the size. This allows for much higher circuit density on a PCB.
Faster Assembly
All the components for one side of a PCB can be placed and soldered in a single automated operation, greatly reducing assembly time. Some through-hole components like connectors may still be needed, but the bulk of the components can be placed with SMT.
Lower Cost
While SMT requires a higher initial investment in equipment, the cost per assembled PCB is lower due to the reduced manual labor and faster production speeds. Component costs are also generally lower for SMT parts.
Better Performance
SMT provides better mechanical performance under shake and vibration conditions. The smaller leads and direct attachment to the PCB result in lower parasitic resistance and inductance, a benefit for high-frequency circuits.
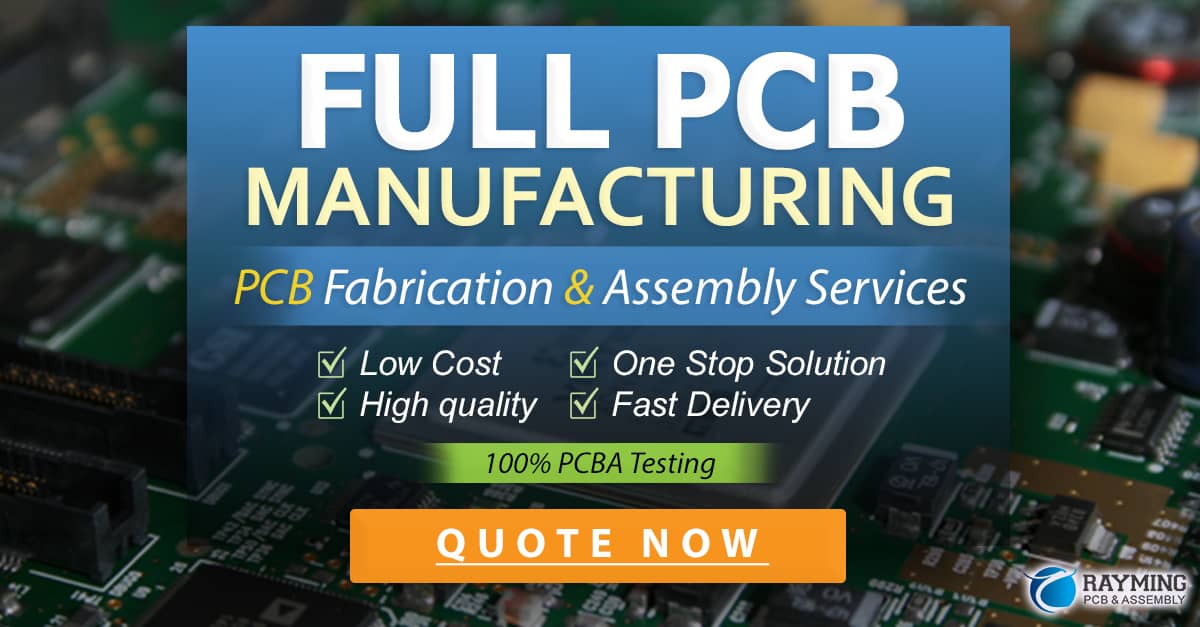
Disadvantages of SMT
There are some disadvantages to SMT as well:
- More complex design rules and smaller pad geometries make PCB layout more difficult
- Some components may not be available in SMT packages
- Smaller pitches require more precise solder paste printing and component placement
- Manual prototype assembly and rework is more difficult due to the smaller component sizes
- X-ray inspection may be needed for some packages like BGAs where the solder joints are not visible
Despite the disadvantages, SMT has become the dominant technology for PCB Assembly. Advances in equipment and processes continue to push the limits of component size and density.
FAQ
Q: What is the difference between SMT and through-hole technology?
A: In through-hole technology, component leads are inserted into holes drilled in the PCB and soldered to pads on the opposite side. In SMT, the components are soldered directly to pads on the surface of the PCB. SMT components are smaller and do not require drilled holes.
Q: Can SMT and through-hole components be used on the same PCB?
A: Yes, a PCB can be assembled with a combination of SMT and through-hole components. This is often done for parts like connectors and large power components that are not available in SMT packages. When both types are used it’s referred to as a “mixed technology” or “hybrid” assembly.
Q: What is a stencil printer?
A: A stencil printer is a machine used to apply solder paste to a PCB prior to component placement. It uses a metal stencil with apertures that correspond to the pad locations on the PCB. Solder paste is dispensed onto the stencil and a wiper blade is used to squeegee the paste through the apertures and onto the pads.
Q: What is the difference between tin-lead and lead-free solder?
A: Tin-lead solder is an alloy of approximately 60% tin and 40% lead. It has a melting point of around 180°C. Lead-free solder is usually made of a tin-silver-copper (SAC) alloy and melts at a higher temperature, around 220°C. The use of lead-free solder has increased due to RoHS regulations restricting hazardous substances in electronic products.
Q: How are SMT component packages classified?
A: SMT components come in a variety of package styles, which are classified according to the lead type and pitch (distance between leads). Common package types are chip resistors and capacitors, small outline transistors (SOT), small outline ICs (SOIC), quad flat packs (QFP) and ball grid arrays (BGA). The trend has been towards smaller pitches and higher pin counts over time.
0 Comments