How Pin-in-Paste Technology Works
The PIP process begins with the application of solder paste onto the PCB using a stencil printer. The solder paste is precisely deposited onto the surface mount pads and into the through-hole component holes. Next, both surface mount and through-hole components are placed onto the PCB using a pick-and-place machine or by manual placement.
The through-hole components are inserted into the solder paste-filled holes, and their leads are trimmed to the appropriate length. The solder paste serves as a temporary adhesive, holding the components in place during the reflow soldering process. Once all the components are placed, the PCB undergoes reflow soldering, where the board is heated to melt the solder paste and create permanent electrical and mechanical connections between the components and the PCB.
Advantages of Pin-in-Paste Technology
-
Streamlined Assembly Process: PIP technology eliminates the need for separate wave soldering or selective soldering processes for through-hole components. By combining SMT and through-hole assembly into a single step, PIP reduces the overall assembly time and simplifies the production process.
-
Cost Reduction: Implementing PIP technology leads to significant cost savings by minimizing the number of assembly steps, reducing the need for additional equipment, and decreasing labor costs associated with separate through-hole soldering processes.
-
Improved Product Quality: PIP technology ensures better alignment and positioning of through-hole components compared to traditional wave soldering methods. The solder paste provides a more consistent and reliable solder joint, reducing the risk of defects such as bridging or insufficient solder fillets.
-
Increased Design Flexibility: With PIP technology, designers have more freedom to incorporate through-hole components alongside surface mount components on the same side of the PCB. This flexibility allows for more compact and efficient board layouts, as well as the ability to use a wider range of component packages.
-
Enhanced Thermal Management: PIP technology enables better thermal dissipation for through-hole components. The solder paste fills the holes completely, providing a larger contact area between the component leads and the PCB, which improves heat transfer and overall thermal performance.
Challenges and Considerations
While PIP technology offers numerous benefits, there are some challenges and considerations to keep in mind:
-
Solder Paste Selection: Choosing the right solder paste is crucial for successful PIP assembly. The paste must have the appropriate viscosity, particle size, and flux activity to ensure proper filling of the through-holes and adequate adhesion of the components during the reflow process.
-
Hole Size and Aspect Ratio: The through-hole size and aspect ratio (hole depth to diameter ratio) must be carefully considered when designing for PIP technology. Holes that are too small or have a high aspect ratio may be difficult to fill with solder paste, leading to incomplete hole fill and potential reliability issues.
-
Component Placement Accuracy: Accurate placement of through-hole components is essential for PIP assembly. Misaligned or tilted components can cause
Consideration | Description |
---|---|
Solder Paste Selection | Choose a solder paste with appropriate viscosity, particle size, and flux activity for proper hole fill and component adhesion. |
Hole Size and Aspect Ratio | Ensure through-hole sizes and aspect ratios are suitable for solder paste filling to avoid incomplete hole fill and reliability issues. |
Component Placement Accuracy | Maintain accurate placement of through-hole components to prevent shorts, opens, or tombstoning. |
Reflow Profile Optimization | Optimize the reflow profile to account for the thermal requirements of both surface mount and through-hole components. |
Inspection and Quality Control | Implement appropriate inspection and quality control measures to identify and address any PIP-related defects or issues. |
Pin-in-Paste Technology in Action
Several industries have adopted PIP technology to improve their electronics manufacturing processes:
Automotive Electronics
The automotive industry has embraced PIP technology for the production of various electronic control modules, sensors, and power distribution systems. By using PIP, automotive manufacturers can create more compact and reliable electronic assemblies that can withstand the harsh environmental conditions encountered in vehicles.
Medical Devices
Medical device manufacturers employ PIP technology to produce high-density, mixed-technology PCB assemblies for applications such as patient monitoring systems, diagnostic equipment, and implantable devices. PIP enables the integration of both surface mount and through-hole components, ensuring the reliability and performance required for critical medical applications.
Industrial Controls and Automation
PIP technology is widely used in the production of industrial control systems, such as programmable logic controllers (PLCs), human-machine interfaces (HMIs), and sensor modules. The enhanced thermal management and design flexibility offered by PIP make it well-suited for the demanding requirements of industrial environments.
Consumer Electronics
Consumer electronics manufacturers leverage PIP technology to create compact and cost-effective products, such as smartphones, wearables, and IoT devices. PIP allows for the efficient assembly of high-density PCBs with a mix of surface mount and through-hole components, enabling the development of feature-rich and reliable consumer devices.
Future Trends and Developments
As the electronics industry continues to evolve, PIP technology is expected to advance and adapt to new challenges:
-
Miniaturization: With the ongoing trend towards miniaturization, PIP technology will need to accommodate smaller through-hole components and higher-density PCB designs. This may require the development of advanced solder pastes and placement techniques to ensure reliable assembly of miniaturized components.
-
Advanced Materials: The introduction of new PCB materials, such as high-temperature laminates and flexible substrates, may necessitate the development of compatible solder pastes and processes for PIP assembly. Research into novel paste formulations and curing methods will be essential to support the adoption of advanced materials.
-
Automation and Process Optimization: As the demand for high-volume production grows, further automation and optimization of the PIP assembly process will be necessary. This may involve the development of more sophisticated pick-and-place machines, inline inspection systems, and data-driven process control techniques to ensure consistent quality and efficiency.
-
Environmental Considerations: With increasing environmental regulations and the drive towards sustainability, the electronics industry will need to develop more eco-friendly PIP solutions. This may include the use of lead-free solder pastes, bio-based flux materials, and recyclable packaging options.
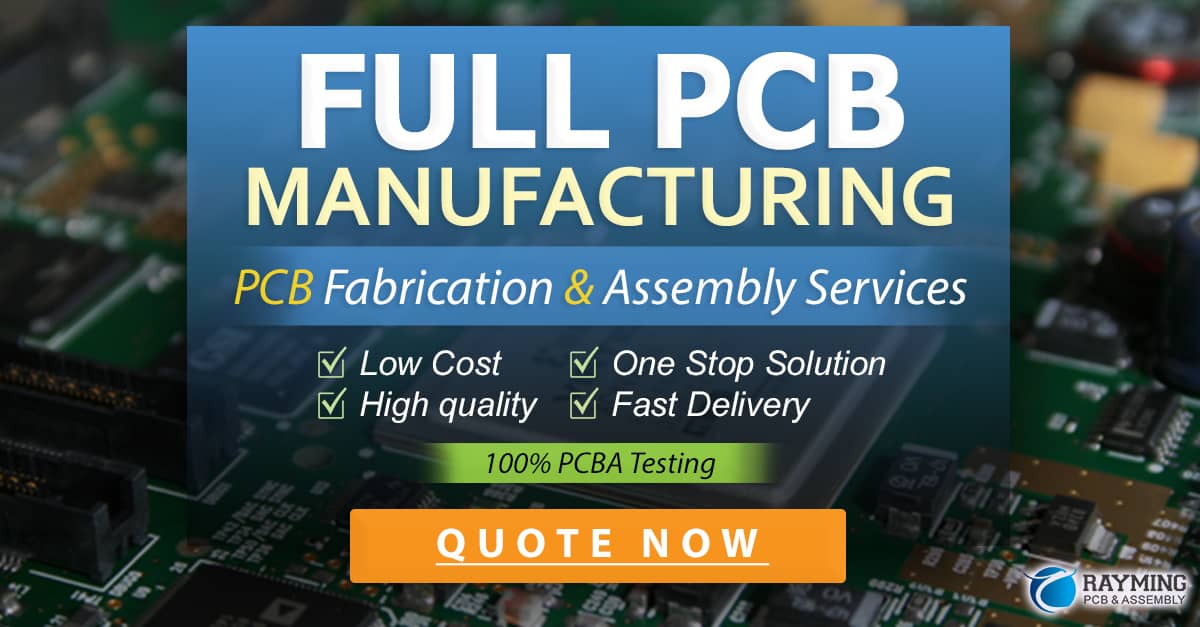
Frequently Asked Questions
Q: Is PIP technology suitable for all types of through-hole components?
A: PIP technology is compatible with most through-hole components, including connectors, switches, and passive components. However, some components with very large or unusually shaped leads may not be suitable for PIP assembly. It is essential to consult with the component manufacturer and assess the compatibility of specific components with the PIP process.
Q: Can PIP technology be used for double-sided PCB Assembly?
A: Yes, PIP technology can be applied to double-sided PCB assembly. In this case, the PCB undergoes a two-step reflow soldering process. The first step involves placing and soldering the surface mount and through-hole components on one side of the board. The second step repeats the process on the opposite side, ensuring that the previously soldered components are not dislodged during the second reflow cycle.
Q: How does PIP technology compare to wave soldering for through-hole components?
A: PIP technology offers several advantages over wave soldering for through-hole components. PIP provides better control over solder joint quality, as the solder paste is precisely deposited into the holes. This results in more consistent and reliable solder joints compared to wave soldering, where the solder flow can be affected by factors such as board orientation and component shadowing. Additionally, PIP eliminates the need for a separate wave soldering process, reducing equipment costs and simplifying the assembly process.
Q: What are the limitations of PIP technology?
A: One of the main limitations of PIP technology is the hole size and aspect ratio. Very small holes or holes with high aspect ratios (deep holes with small diameters) can be challenging to fill with solder paste, leading to incomplete hole fill and potential reliability issues. Additionally, PIP may not be suitable for certain types of through-hole components with very large or unusually shaped leads, as they may not fit properly into the solder paste-filled holes.
Q: How can I ensure the success of PIP assembly in my manufacturing process?
A: To ensure the success of PIP assembly, consider the following factors:
1. Select the appropriate solder paste with the right viscosity, particle size, and flux activity for your specific application.
2. Design your PCB with suitable hole sizes and aspect ratios to facilitate proper solder paste filling.
3. Ensure accurate placement of through-hole components to prevent shorts, opens, or tombstoning.
4. Optimize your reflow profile to account for the thermal requirements of both surface mount and through-hole components.
5. Implement robust inspection and quality control measures to identify and address any PIP-related defects or issues.
By carefully considering these factors and working closely with your PCB assembly partner, you can successfully implement PIP technology and reap its benefits in your manufacturing process.
Conclusion
Pin-in-Paste (PIP) technology has revolutionized the electronics manufacturing industry by offering a streamlined, cost-effective, and reliable method for assembling PCBs with a mix of surface mount and through-hole components. By combining the placement and soldering of through-hole components into a single reflow soldering process, PIP technology simplifies the assembly process, reduces costs, and enhances product quality.
As the electronics industry continues to evolve, PIP technology is expected to advance and adapt to new challenges, such as miniaturization, advanced materials, automation, and environmental considerations. By staying informed about the latest developments in PIP technology and working closely with experienced PCB assembly partners, manufacturers can leverage the benefits of this innovative approach to create high-quality, reliable, and cost-effective electronic products.
0 Comments