Introduction to PCB Assembly
PCB assembly is the process of soldering or mounting electronic components onto a printed circuit board (PCB). It is a crucial step in the manufacturing of electronic devices, as it involves attaching various components such as resistors, capacitors, integrated circuits (ICs), and connectors to the PCB. The assembled PCB forms the foundation of the electronic device, enabling it to function as intended.
In this comprehensive guide, we will explore the fundamentals of PCB assembly, covering topics such as PCB design, component selection, soldering techniques, and quality control measures. Whether you are a beginner in the field of electronics or an experienced professional looking to expand your knowledge, this guide will provide you with valuable insights into the world of PCB assembly.
Understanding Printed Circuit Boards (PCBs)
Before delving into the assembly process, it is essential to understand what a printed circuit board (PCB) is and its role in electronic devices.
What is a PCB?
A PCB is a flat insulating board made of fiberglass, composite epoxy, or other laminate material. It serves as the base for mounting and interconnecting electronic components using conductive tracks, pads, and other features etched from copper sheets laminated onto the non-conductive substrate.
PCBs come in various types, depending on the number of layers and the density of the components:
PCB Type | Description |
---|---|
Single-sided PCB | Components are mounted on one side of the board, with conductive tracks on the opposite side. |
Double-sided PCB | Components are mounted on both sides of the board, with conductive tracks on both sides. |
Multi-layer PCB | Consists of three or more conductive layers separated by insulating layers, allowing for more complex circuitry and higher component density. |
The Role of PCBs in Electronic Devices
PCBs play a crucial role in the functioning of electronic devices by providing a platform for the following:
-
Component placement: PCBs provide a stable and organized surface for mounting electronic components, ensuring proper spacing and alignment.
-
Electrical connectivity: The conductive tracks on the PCB allow for the flow of electricity between components, enabling the device to function as intended.
-
Mechanical support: PCBs offer mechanical support to the components, protecting them from physical stress and vibration.
-
Heat dissipation: PCBs can be designed with thermal management features, such as heat sinks and thermal vias, to dissipate heat generated by components.
PCB Design and Layout
Before the assembly process can begin, a PCB must be designed and laid out according to the specific requirements of the electronic device.
Schematic Design
The first step in PCB design is creating a schematic diagram, which is a graphical representation of the electronic circuit. The schematic shows the components and their interconnections using standardized symbols and labels.
PCB Layout
Once the schematic is complete, the next step is to create the PCB layout. This involves arranging the components on the board and routing the conductive tracks to establish the necessary electrical connections. PCB layout software, such as Altium Designer or KiCad, is used to create the layout, taking into account factors such as:
- Component placement and orientation
- Track width and spacing
- Via placement and size
- Ground and power planes
- Electromagnetic interference (EMI) and signal integrity considerations
Design for Manufacturing (DFM)
To ensure that the PCB can be efficiently and reliably manufactured, it is essential to follow Design for Manufacturing (DFM) guidelines. These guidelines take into account the limitations and capabilities of the manufacturing process, such as:
- Minimum track width and spacing
- Minimum hole size and spacing
- Soldermask and silkscreen requirements
- Panelization and board outline considerations
By adhering to DFM guidelines, designers can minimize the risk of manufacturing defects and improve the overall quality of the assembled PCB.
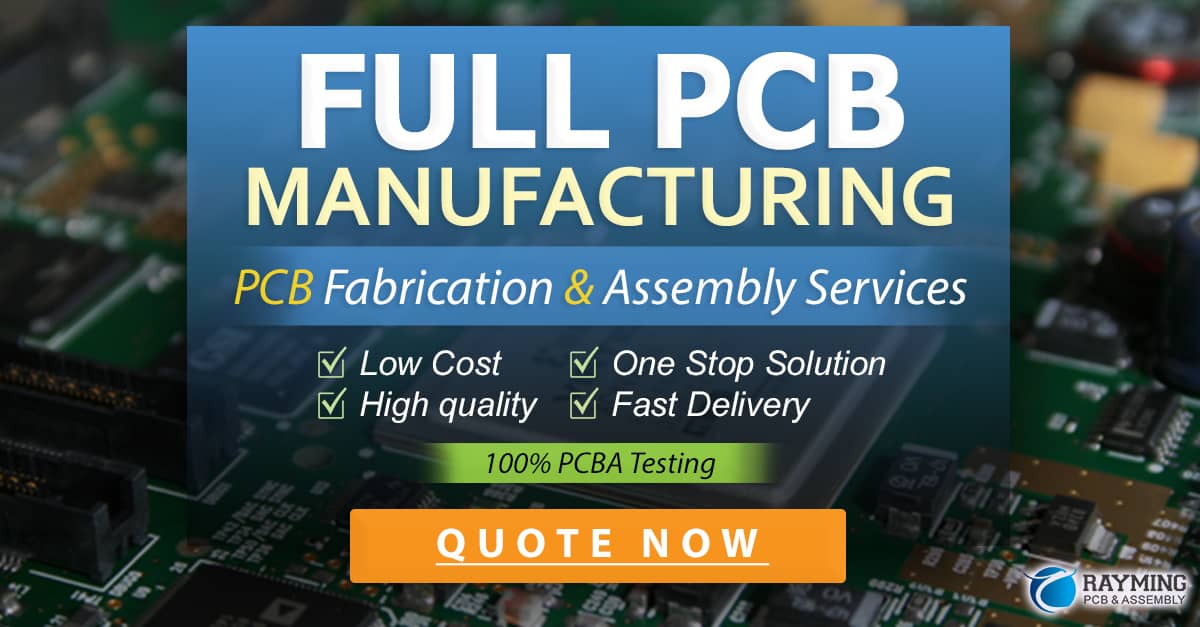
Component Selection and Procurement
Selecting the right components is crucial for the successful assembly and functioning of the PCB.
Types of Components
Electronic components can be broadly categorized into two types:
-
Through-hole components: These components have long leads that are inserted through holes drilled in the PCB and soldered on the opposite side. Examples include resistors, capacitors, and some types of connectors.
-
Surface-mount components: These components are mounted directly onto the surface of the PCB, without the need for drilled holes. They are smaller and more compact than through-hole components, allowing for higher component density. Examples include chip resistors, chip capacitors, and most ICs.
Component Specification and Sourcing
When selecting components for a PCB, it is essential to consider the following factors:
- Electrical specifications (e.g., resistance, capacitance, voltage rating)
- Package type and size
- Temperature rating
- Availability and lead time
- Cost and minimum order quantity (MOQ)
Components can be sourced from various suppliers, such as distributors (e.g., Digi-Key, Mouser, RS Components) or directly from manufacturers. It is important to ensure that the components are authentic and meet the required specifications to avoid issues during assembly and device operation.
Soldering Techniques
Soldering is the process of joining two or more metal items by melting and putting a filler metal (solder) into the joint, the filler metal having a lower melting point than the adjoining metal.
Types of Soldering
There are two main types of soldering used in PCB assembly:
-
Through-hole soldering: This method involves inserting the component leads through holes drilled in the PCB and soldering them on the opposite side. Through-hole soldering can be done manually using a soldering iron or automatically using wave soldering machines.
-
Surface-mount soldering: This method involves soldering components directly onto the surface of the PCB. Surface-mount soldering can be done using reflow soldering, where solder paste is applied to the PCB pads, components are placed, and the board is heated in a reflow oven to melt the solder and form the connections.
Soldering Tools and Equipment
To perform soldering effectively, the following tools and equipment are commonly used:
- Soldering iron or soldering station
- Solder wire (lead-based or lead-free)
- Solder paste (for surface-mount soldering)
- Flux (to improve solder flow and prevent oxidation)
- Tweezers and picks (for handling small components)
- Solder wick or desoldering pump (for removing excess solder or correcting mistakes)
Soldering Best Practices
To ensure reliable and high-quality solder joints, it is important to follow these best practices:
- Use the appropriate solder wire diameter and type for the job
- Maintain the soldering iron tip clean and tinned
- Apply the right amount of solder and heat to form a concave fillet
- Avoid bridging or insufficient solder coverage
- Inspect the solder joints visually for defects such as cold joints, blowholes, or solder spikes
PCB Assembly Process
The PCB assembly process typically involves the following steps:
-
Solder paste application (for surface-mount components): Solder paste is applied to the PCB pads using a stencil or syringe. The paste consists of tiny solder spheres suspended in a flux medium.
-
Component placement: Components are placed onto the PCB, either manually or using automated pick-and-place machines. Proper alignment and orientation of components are crucial for ensuring correct functionality.
-
Reflow soldering (for surface-mount components): The PCB with the placed components is sent through a reflow oven, where it is subjected to a controlled temperature profile. The heat melts the solder paste, forming the electrical and mechanical connections between the components and the PCB.
-
Wave soldering (for through-hole components): The PCB is passed over a molten solder wave, which selectively solders the through-hole component leads to the PCB pads.
-
Inspection and quality control: The assembled PCB undergoes visual inspection and automated optical inspection (AOI) to detect any defects or issues, such as misaligned components, solder bridges, or insufficient solder coverage.
-
Rework and repair (if necessary): If defects are found during inspection, the PCB may need to be reworked or repaired. This involves removing and replacing defective components or correcting soldering issues.
-
Functional testing: The assembled PCB is tested to ensure that it functions as intended, meeting the specified performance and reliability requirements.
-
Conformal coating (optional): In some cases, a conformal coating may be applied to the PCB to protect it from environmental factors such as moisture, dust, or chemical contaminants.
Quality Control and Inspection
Ensuring the quality of the assembled PCB is essential for the reliable operation of the electronic device. Quality control measures are implemented throughout the assembly process to identify and rectify any issues.
Visual Inspection
Visual inspection is the first line of defense in catching assembly defects. Operators visually check the PCB for issues such as:
- Component placement and orientation
- Solder joint quality (e.g., insufficient solder, bridging, cold joints)
- Cleanliness and any foreign object debris (FOD)
Automated Optical Inspection (AOI)
AOI systems use cameras and image processing algorithms to automatically detect assembly defects. These systems can quickly scan the PCB and identify issues such as:
- Component presence and polarity
- Solder paste coverage and alignment
- Solder joint quality and defects
AOI systems provide fast and consistent inspection results, reducing the risk of human error and increasing throughput.
X-Ray Inspection
For complex PCBs with high component density or hidden solder joints (e.g., ball grid arrays or BGAs), X-ray inspection may be necessary. X-ray systems allow operators to see through the PCB and inspect the quality of solder joints that are not visible from the surface.
Functional Testing
Functional testing verifies that the assembled PCB performs as intended, meeting the specified electrical and performance requirements. This may involve:
- In-circuit testing (ICT): Probes are used to test individual components and their interconnections
- Flying probe testing: Movable probes are used to test specific points on the PCB
- Boundary scan testing: Utilizes built-in test features in ICs to test the interconnections between components
Functional testing helps identify any issues that may have been missed during visual or automated inspection, ensuring that the PCB is fully operational before being integrated into the final product.
Rework and Repair
Despite best efforts, assembly defects may still occur. In such cases, rework and repair are necessary to correct the issues and salvage the PCB.
Rework Techniques
Common rework techniques include:
- Desoldering and removing defective components using desoldering tools (e.g., desoldering iron, hot air pencil, or desoldering station)
- Cleaning the PCB pads and removing any residual solder
- Replacing the defective component with a new one
- Resoldering the component using the appropriate soldering technique
Repair Considerations
When performing rework and repair, it is important to consider the following:
- The impact of heat on the PCB and surrounding components during desoldering and resoldering
- The risk of damaging the PCB pads or tracks during component removal
- The need for proper handling and storage of sensitive components (e.g., electrostatic discharge or ESD precautions)
- The importance of thorough cleaning and inspection after the repair to ensure the issue has been resolved and no new defects have been introduced
Advanced PCB Assembly Techniques
As electronic devices become more complex and compact, advanced PCB assembly techniques may be required to meet the challenges of higher component density and smaller form factors.
Ball Grid Array (BGA) Assembly
BGAs are surface-mount components that utilize an array of solder balls on the underside of the package to connect to the PCB. BGA Assembly requires precise alignment and specialized equipment, such as:
- BGA placement machines with high accuracy and vision systems
- Reflow ovens with tightly controlled temperature profiles
- X-ray inspection systems for verifying solder joint quality
Chip-on-Board (COB) Assembly
COB assembly involves mounting bare semiconductor die directly onto the PCB substrate, without the use of a package. This technique allows for higher component density and improved electrical performance. COB assembly requires specialized equipment and processes, such as:
- Die bonding machines for attaching the bare die to the PCB
- Wire bonding machines for making electrical connections between the die and the PCB pads
- Encapsulation or potting to protect the bare die from environmental factors
Flexible and Rigid-Flex PCB Assembly
Flexible and rigid-flex PCBs offer unique challenges in assembly due to their non-planar nature and the need to accommodate bending and folding. Special considerations for flexible and rigid-flex PCB assembly include:
- Handling and fixturing to prevent damage to the flexible portions of the PCB
- Selecting appropriate components and soldering techniques that can withstand the expected flexing and bending
- Ensuring proper strain relief and support for the flexible sections to minimize stress on the components and solder joints
FAQ
1. What are the most common PCB assembly defects?
Some of the most common PCB assembly defects include:
- Solder bridges: Unintended connections between adjacent solder joints
- Cold solder joints: Solder joints that have not been heated sufficiently, resulting in a weak or unreliable connection
- Component misalignment or shifting: Components that are not placed accurately or have moved during the soldering process
- Insufficient or excessive solder: Too little or too much solder on the joints, leading to poor connections or short circuits
- Tombstoning: Surface-mount components standing up on one end due to uneven heating or solder paste application
2. What is the difference between lead-based and lead-free solder?
Lead-based solder typically contains a mixture of tin and lead, while lead-free solder is usually composed of tin, silver, and copper. The main differences between the two types are:
- Melting point: Lead-free solder has a higher melting point than lead-based solder, requiring higher soldering temperatures
- Environmental impact: Lead-free solder is more environmentally friendly, as lead is a toxic substance that can cause health and environmental issues
- Wetting and flow characteristics: Lead-based solder tends to have better wetting and flow properties, making it easier to work with in some cases
3. How can I prevent electrostatic discharge (ESD) damage during PCB assembly?
To prevent ESD damage during PCB assembly, follow these best practices:
- Use an ESD-safe workspace, including grounded workbenches, flooring, and wrist straps
- Wear ESD-protective clothing, such as ESD lab coats and shoes
- Handle sensitive components using ESD-safe tools and equipment, such as ESD tweezers and mats
- Store sensitive components in ESD-safe packaging when not in use
- Regularly test and maintain ESD protection equipment to ensure its effectiveness
4. What is the purpose of conformal coating on a PCB?
Conformal coating is a thin, protective layer applied to the surface of a PCB to protect it from environmental factors such as:
- Moisture and humidity
- Dust and debris
- Chemical contaminants
- Extreme temperatures
Conformal coating helps to improve the reliability and longevity of the PCB by preventing corrosion, leakage currents, and short circuits caused by environmental factors.
5. How do I choose the right PCB assembly partner?
When choosing a PCB assembly partner, consider the following factors:
- Technical capabilities and experience: Ensure the partner has the necessary equipment, processes, and expertise to handle your specific PCB assembly requirements
- Quality management system: Look for a partner with a robust quality management system, such as ISO 9001 certification, to ensure consistent and reliable results
- Communication and support: Choose a partner that provides clear communication, responsive support, and a collaborative approach to problem-solving
- Cost and lead time: Consider the partner’s pricing structure and their ability to meet your required lead times and delivery schedules
- Reputation and references: Research the partner’s reputation in the industry and seek references from their existing clients to gauge their performance and reliability
Conclusion
PCB assembly is a critical process in the manufacturing of electronic devices, requiring a combination of technical expertise, precision, and attention to detail. By understanding the fundamentals of PCB design, component selection, soldering techniques, and quality control, you can ensure the successful assembly of high-quality, reliable PCBs.
This comprehensive guide has provided an overview of the key aspects of PCB assembly, from the basics of PCBs and their role in electronic devices to advanced techniques like BGA and COB assembly. By following best practices and partnering with experienced PCB assembly providers, you can navigate the complexities of PCB assembly and bring your electronic projects to life.
As technology continues to evolve, staying up-to-date with the latest developments in PCB assembly is crucial for staying competitive in the electronics industry. With the knowledge gained from this guide, you are well-equipped to tackle the challenges of PCB assembly and create innovative, reliable electronic devices.
0 Comments