Understanding OSP PCB Surface Finish
OSP is a chemical coating applied to the exposed copper pads on a PCB after the etching and plating processes. The organic compounds in OSP form a protective layer that prevents the copper from oxidizing and maintains its solderability for a limited period.
Composition of OSP
The composition of OSP varies depending on the manufacturer, but it typically includes:
- Benzimidazole derivatives
- Azole compounds
- Additives for improved performance
These organic compounds create a thin, transparent layer on the copper surface, usually between 0.2 to 0.5 microns thick.
How OSP Works
When applied to the copper pads, OSP creates a barrier between the copper and the environment, preventing oxidation. The organic compounds in OSP also improve the wettability of the solder, ensuring a strong and reliable solder joint during the assembly process.
Benefits of Using OSP PCB Surface Finish
OSP PCB surface finish offers several advantages over other surface finishes:
-
Cost-effective: OSP is one of the most economical surface finishes available, making it an attractive choice for budget-conscious projects.
-
Flat surface: Unlike other surface finishes that add thickness to the pads, OSP maintains a flat surface, making it ideal for fine-pitch components and high-density designs.
-
Excellent solderability: OSP provides good wettability and solderability, ensuring reliable solder joints during assembly.
-
Environmentally friendly: OSP is an environmentally friendly surface finish as it does not contain lead or other harmful substances.
-
Easier inspection: The transparent nature of OSP allows for easier visual inspection of solder joints compared to opaque surface finishes like ENIG (Electroless Nickel Immersion Gold).
Applications of OSP PCB Surface Finish
OSP PCB surface finish is suitable for a wide range of applications:
-
Consumer electronics: OSP is commonly used in consumer electronic devices such as smartphones, laptops, and home appliances.
-
Automotive industry: OSP PCBs are used in various automotive electronic systems, including infotainment systems and engine control units.
-
Industrial equipment: OSP surface finish is employed in industrial equipment PCBs, such as control panels and sensors.
-
Medical devices: Some medical device PCBs use OSP surface finish, particularly in non-critical applications.
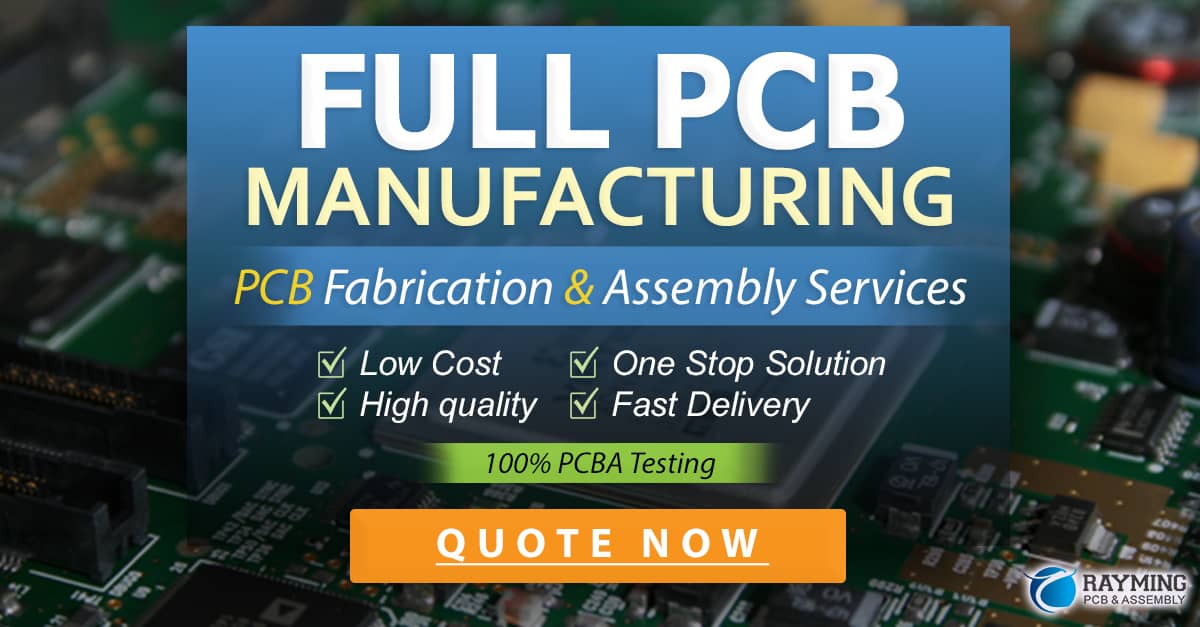
Limitations of OSP PCB Surface Finish
Despite its benefits, OSP PCB surface finish has some limitations:
-
Limited shelf life: OSP provides protection against oxidation for a limited time, typically 6 to 12 months, depending on storage conditions.
-
Sensitivity to handling: OSP is sensitive to handling and can be easily contaminated by fingerprints or other contaminants, affecting its solderability.
-
Not suitable for multiple reflow cycles: OSP is not recommended for PCBs that undergo multiple reflow cycles, as the organic compounds can degrade, leading to reduced solderability.
-
Incompatible with some cleaning processes: Certain cleaning processes, such as ultrasonic cleaning, can remove the OSP coating, exposing the copper to oxidation.
Comparison of OSP with Other PCB Surface Finishes
To better understand the benefits and drawbacks of OSP, let’s compare it with other common PCB surface finishes:
Surface Finish | Pros | Cons |
---|---|---|
OSP | – Cost-effective – Flat surface – Excellent solderability – Environmentally friendly |
– Limited shelf life – Sensitive to handling – Not suitable for multiple reflow cycles |
ENIG | – Excellent solderability – Long shelf life – Suitable for multiple reflow cycles |
– Higher cost – Uneven surface – Possible “black pad” issue |
HASL (Hot Air Solder Leveling) | – Cost-effective – Excellent solderability – Long shelf life |
– Uneven surface – Not suitable for fine-pitch components – Contains lead (in some cases) |
Immersion Silver | – Excellent solderability – Flat surface – Suitable for fine-pitch components |
– Higher cost than OSP – Limited shelf life – Can tarnish over time |
Choosing the Right PCB Surface Finish
When selecting a PCB surface finish, consider the following factors:
-
Budget: OSP is a cost-effective option, while ENIG and Immersion Silver are more expensive.
-
Design requirements: For fine-pitch components and high-density designs, OSP and Immersion Silver are better choices due to their flat surface.
-
Shelf life: If long shelf life is a priority, ENIG and HASL are better options than OSP.
-
Environmental concerns: OSP and lead-free HASL are environmentally friendly options.
-
Assembly process: Consider the number of reflow cycles and the cleaning processes involved in your assembly process when choosing a surface finish.
Frequently Asked Questions (FAQ)
-
Q: How long does OSP protect the copper pads from oxidation?
A: OSP typically provides protection against oxidation for 6 to 12 months, depending on storage conditions. -
Q: Is OSP suitable for PCBs with fine-pitch components?
A: Yes, OSP is suitable for fine-pitch components due to its flat surface, which allows for accurate placement and soldering. -
Q: Can OSP be used for PCBs that undergo multiple reflow cycles?
A: No, OSP is not recommended for PCBs that undergo multiple reflow cycles, as the organic compounds can degrade, leading to reduced solderability. -
Q: Is OSP an environmentally friendly PCB surface finish?
A: Yes, OSP is an environmentally friendly surface finish as it does not contain lead or other harmful substances. -
Q: How does OSP compare to ENIG in terms of cost?
A: OSP is a more cost-effective surface finish compared to ENIG, making it an attractive choice for budget-conscious projects.
Conclusion
OSP PCB surface finish is a popular choice for various applications due to its cost-effectiveness, excellent solderability, and suitability for fine-pitch components. However, it is essential to consider its limitations, such as limited shelf life and sensitivity to handling, when deciding on the best surface finish for your project. By understanding the benefits and drawbacks of OSP and comparing it with other surface finishes, you can make an informed decision that meets your design requirements, budget, and environmental concerns.
0 Comments