What Does “High Tg” Mean?
The term “Tg” stands for Glass Transition Temperature, which is the temperature at which a polymer material transitions from a hard, glassy state to a soft, rubbery state. In the context of PCBs, the Tg value refers to the maximum temperature at which the PCB substrate maintains its mechanical and electrical properties.
Standard PCBs typically have a Tg value of around 130°C to 140°C, while High TG PCBs have a Tg value of 170°C or higher. This higher Tg value allows High Tg PCBs to operate reliably in high-temperature environments without experiencing significant degradation or failure.
Advantages of High Tg PCBs
1. Enhanced Thermal Stability
The primary advantage of High Tg PCBs is their enhanced thermal stability. With a higher glass transition temperature, these PCBs can withstand elevated temperatures without deforming, warping, or losing their mechanical strength. This makes them suitable for applications that generate significant heat or operate in high-temperature environments.
2. Improved Reliability
High Tg PCBs offer improved reliability compared to standard PCBs. The higher thermal stability reduces the risk of thermal stress-induced failures, such as delamination, cracking, or conductor breakdown. This translates to longer product lifetimes and reduced maintenance costs.
3. Better Signal Integrity
The enhanced thermal stability of High Tg PCBs also contributes to better signal integrity. At higher temperatures, standard PCBs may experience increased dielectric loss and signal attenuation, which can lead to signal distortion and reduced performance. High Tg PCBs maintain their dielectric properties at elevated temperatures, ensuring more stable and reliable signal transmission.
4. Compatibility with Lead-Free Soldering
High Tg PCBs are well-suited for lead-free soldering processes, which typically require higher soldering temperatures compared to traditional Lead-based Soldering. The increased thermal stability of High Tg PCBs allows them to withstand the higher temperatures associated with lead-free soldering without experiencing damage or degradation.
Applications of High Tg PCBs
High Tg PCBs find applications in various industries and sectors where thermal stability and reliability are critical. Some of the common applications include:
1. Aerospace and Defense
In aerospace and defense applications, PCBs are often exposed to extreme temperature fluctuations, vibrations, and other harsh environmental conditions. High Tg PCBs provide the necessary thermal stability and reliability to ensure the proper functioning of electronic systems in these demanding environments.
2. Automotive Electronics
Modern automobiles rely heavily on electronic systems for various functions, such as engine control, safety features, and infotainment. High Tg PCBs are used in automotive electronics to withstand the high temperatures generated by the engine compartment and other heat sources, ensuring reliable operation over the vehicle’s lifetime.
3. Industrial Equipment
Industrial equipment, such as power supplies, motor drives, and process control systems, often operates in high-temperature environments. High Tg PCBs are used in these applications to provide the necessary thermal stability and reliability, reducing the risk of equipment failure and downtime.
4. High-Performance Computing
High-performance computing systems, such as servers and data centers, generate significant amounts of heat due to the high processing power and density of electronic components. High Tg PCBs are used in these systems to ensure reliable operation and prevent thermal-induced failures, even under heavy computational loads.
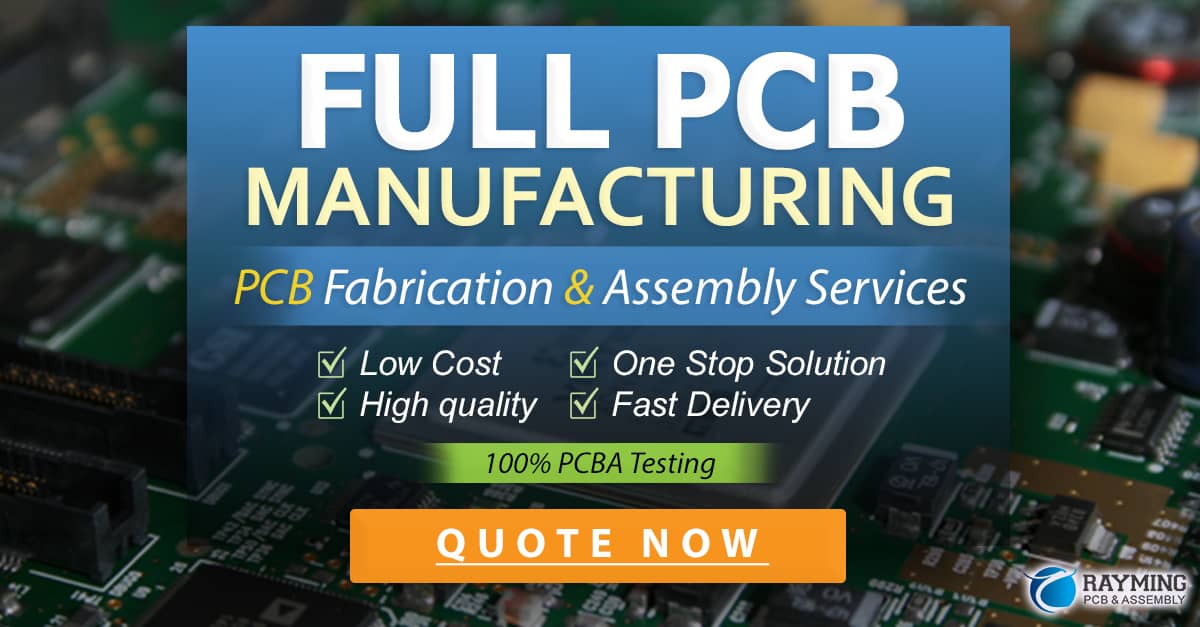
Manufacturing Process of High Tg PCBs
The manufacturing process of High Tg PCBs is similar to that of standard PCBs, with a few key differences in the materials and processing conditions used.
1. Substrate Material
High Tg PCBs use a substrate material with a higher glass transition temperature compared to standard PCBs. Common substrate materials for High Tg PCBs include:
- Polyimide (PI): Tg values ranging from 250°C to 400°C
- High Tg FR-4: Tg values ranging from 170°C to 200°C
- Bismaleimide Triazine (BT): Tg values ranging from 210°C to 250°C
The choice of substrate material depends on the specific application requirements, such as the operating temperature range, mechanical properties, and cost considerations.
2. Lamination Process
The lamination process for High Tg PCBs involves bonding the copper foil to the substrate material under high temperature and pressure. The lamination temperature for High Tg PCBs is typically higher than that for standard PCBs, ranging from 200°C to 250°C, depending on the substrate material used.
3. Drilling and Plating
After lamination, the High Tg PCB undergoes drilling and plating processes to create the necessary holes and vias for component mounting and interconnections. The drilling and plating processes for High Tg PCBs are similar to those for standard PCBs, with adjustments made to accommodate the higher thermal stability of the substrate material.
4. Solder Mask and Silkscreen
The solder mask and silkscreen application processes for High Tg PCBs are also similar to those for standard PCBs. However, the solder mask and silkscreen materials used for High Tg PCBs must be compatible with the higher operating temperatures and have adequate thermal stability to prevent degradation or delamination.
Comparison of High Tg PCBs with Standard PCBs
The following table compares the key characteristics of High Tg PCBs and standard PCBs:
Characteristic | High Tg PCB | Standard PCB |
---|---|---|
Glass Transition Temperature (Tg) | 170°C or higher | 130°C to 140°C |
Thermal Stability | Enhanced | Standard |
Reliability | Improved | Standard |
Signal Integrity | Better at high temperatures | Degrades at high temperatures |
Lead-Free Soldering Compatibility | Excellent | Good |
Cost | Higher | Lower |
As evident from the table, High Tg PCBs offer superior thermal stability, reliability, and signal integrity compared to standard PCBs, making them the preferred choice for applications that demand high performance in elevated temperature environments. However, this enhanced performance comes at a higher cost due to the specialized materials and processing requirements.
Frequently Asked Questions (FAQ)
1. What is the difference between High Tg PCB and standard PCB?
The main difference between High Tg PCB and standard PCB lies in their glass transition temperatures (Tg). High Tg PCBs have a Tg value of 170°C or higher, while standard PCBs have a Tg value of 130°C to 140°C. This higher Tg value gives High Tg PCBs enhanced thermal stability, reliability, and signal integrity compared to standard PCBs.
2. What are the applications of High Tg PCBs?
High Tg PCBs find applications in various industries where thermal stability and reliability are critical, such as aerospace and defense, automotive electronics, industrial equipment, and high-performance computing.
3. What substrate materials are used for High Tg PCBs?
Common substrate materials for High Tg PCBs include polyimide (PI), high Tg FR-4, and bismaleimide triazine (BT). The choice of substrate material depends on the specific application requirements, such as the operating temperature range, mechanical properties, and cost considerations.
4. Are High Tg PCBs compatible with lead-free soldering?
Yes, High Tg PCBs are well-suited for lead-free soldering processes, which typically require higher soldering temperatures compared to traditional lead-based soldering. The increased thermal stability of High Tg PCBs allows them to withstand the higher temperatures associated with lead-free soldering without experiencing damage or degradation.
5. Are High Tg PCBs more expensive than standard PCBs?
Yes, High Tg PCBs are generally more expensive than standard PCBs due to the specialized materials and processing requirements. The higher cost is justified by the enhanced thermal stability, reliability, and signal integrity offered by High Tg PCBs, which are essential for applications operating in high-temperature environments.
Conclusion
High Tg PCBs are a specialized type of printed circuit board designed to withstand higher temperatures and provide enhanced thermal stability, reliability, and signal integrity compared to standard PCBs. With their ability to operate reliably in demanding environments, High Tg PCBs find applications in various industries, such as aerospace, automotive, industrial equipment, and high-performance computing.
While High Tg PCBs come at a higher cost compared to standard PCBs, their superior performance in high-temperature environments makes them an essential component in ensuring the proper functioning and longevity of electronic systems. As technology continues to advance and the demand for reliable, high-performance electronics grows, the importance of High Tg PCBs in enabling these advancements will only continue to increase.
0 Comments