What is a High TG PCB?
A High TG PCB, also known as a High Glass Transition Temperature PCB, is a type of printed circuit board that is designed to withstand higher temperatures compared to standard PCBs. The term “TG” refers to the glass transition temperature, which is the temperature at which the material transitions from a rigid, glassy state to a more flexible, rubbery state.
High TG PCBs are manufactured using materials that have a higher glass transition temperature, typically above 170°C. This higher temperature resistance allows the PCB to maintain its structural integrity and electrical properties even when exposed to extreme heat.
Characteristics of High TG PCBs
-
Temperature Resistance: High TG PCBs are designed to withstand temperatures above 170°C, making them suitable for applications that involve exposure to high heat.
-
Dimensional Stability: The materials used in High TG PCBs have a lower coefficient of thermal expansion (CTE), which means they are less likely to expand or contract when exposed to temperature changes. This dimensional stability is crucial for maintaining the integrity of the circuit and preventing issues such as warping or delamination.
-
Improved Reliability: The ability to withstand higher temperatures and maintain dimensional stability contributes to the overall reliability of High TG PCBs. They are less prone to failure due to thermal stress and can operate consistently in demanding environments.
-
Enhanced Electrical Properties: High TG materials often have improved electrical properties, such as lower dielectric constant and dissipation factor. These properties can contribute to better signal integrity and reduced signal loss, especially at higher frequencies.
-
Compatibility with Lead-Free Soldering: High TG PCBs are well-suited for lead-free soldering processes, which typically require higher soldering temperatures compared to traditional lead-based soldering. The increased temperature resistance of High TG PCBs ensures they can withstand the higher soldering temperatures without compromising the integrity of the board.
Applications of High TG PCBs
High TG PCBs find applications in various industries and sectors where reliable performance under high-temperature conditions is essential. Some common applications include:
-
Automotive Electronics: High TG PCBs are widely used in automotive electronics, especially in engine control units (ECUs), power modules, and sensors. These components are often exposed to high temperatures due to their proximity to the engine or exhaust system.
-
Aerospace and Defense: In aerospace and defense applications, electronic systems may be subjected to extreme temperature variations and high-stress environments. High TG PCBs are used in avionics, radar systems, and satellite communications to ensure reliable operation in these demanding conditions.
-
Industrial Equipment: Industrial equipment, such as power inverters, motor drives, and welding machines, often generates significant heat during operation. High TG PCBs are used in these applications to withstand the high temperatures and maintain reliable performance.
-
LED Lighting: High-power LED lighting systems generate a considerable amount of heat, which can affect the longevity and performance of the electronics. High TG PCBs are used in LED drivers and control circuits to ensure stable operation and long-term reliability.
-
Medical Devices: Some medical devices, such as surgical instruments and sterilization equipment, require PCBs that can withstand high temperatures. High TG PCBs are used in these applications to ensure the devices can function reliably in sterilization processes and other high-temperature environments.
Advantages of High TG PCBs
Using High TG PCBs offers several advantages over standard PCBs, particularly in applications that involve exposure to high temperatures. Some of the key advantages include:
-
Enhanced Thermal Stability: The higher glass transition temperature of High TG PCBs allows them to maintain their structural integrity and electrical properties even when subjected to high temperatures. This thermal stability reduces the risk of PCB failure due to thermal stress and ensures reliable operation in challenging environments.
-
Improved Durability: High TG PCBs are more durable and resistant to thermal cycling, which involves repeated exposure to temperature variations. This durability translates to a longer lifespan and reduced risk of failure, especially in applications where the PCB is subjected to frequent temperature changes.
-
Reduced Warping and Delamination: The materials used in High TG PCBs have a lower coefficient of thermal expansion (CTE), which means they are less likely to expand or contract when exposed to temperature changes. This dimensional stability reduces the risk of warping or delamination, which can cause issues such as cracking or separation of layers in the PCB.
-
Better Signal Integrity: High TG materials often have improved electrical properties, such as lower dielectric constant and dissipation factor. These properties contribute to better signal integrity and reduced signal loss, particularly at higher frequencies. This is important for applications that require high-speed data transmission or sensitive analog signals.
-
Compatibility with Lead-Free Soldering: The transition to lead-free soldering processes has led to higher soldering temperatures, which can pose challenges for standard PCBs. High TG PCBs are designed to withstand these higher temperatures, making them compatible with lead-free soldering processes without compromising the integrity of the board.
-
Cost-Effectiveness in High-Temperature Applications: While High TG PCBs may have a higher initial cost compared to standard PCBs, they offer cost-effectiveness in the long run for applications that involve high temperatures. The enhanced reliability and durability of High TG PCBs reduce the need for frequent replacements or repairs, ultimately saving costs associated with maintenance and downtime.
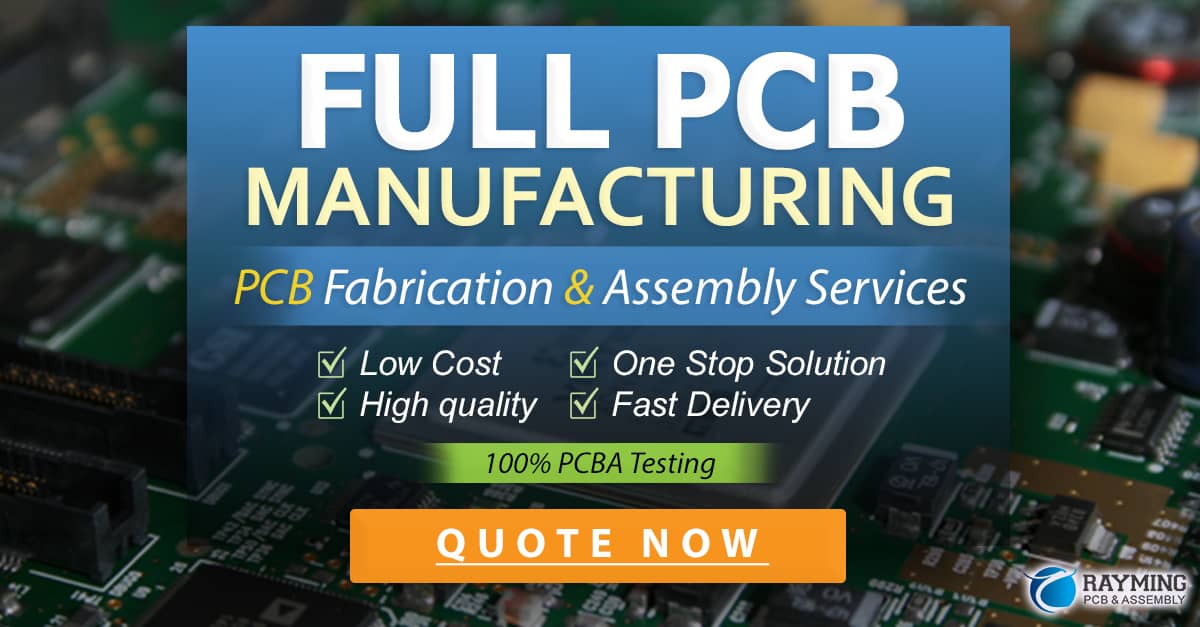
Manufacturing Process of High TG PCBs
The manufacturing process of High TG PCBs is similar to that of standard PCBs, with a few key differences in material selection and processing parameters. The general steps involved in manufacturing High TG PCBs are as follows:
-
Material Selection: The first step in manufacturing High TG PCBs is selecting the appropriate materials. The base material, typically a high-temperature epoxy laminate, is chosen based on its glass transition temperature and other required properties. Copper foil is also selected based on the desired thickness and electrical properties.
-
Circuit Design: The circuit design is created using electronic design automation (EDA) software. The design includes the layout of the conductive traces, component placement, and any necessary vias or holes.
-
PCB Fabrication: The fabrication process involves several sub-steps:
- Lamination: The base material and copper foil are laminated together under high temperature and pressure to form a solid board.
- Drilling: Holes are drilled into the board for component placement and vias.
- Plating: The holes are plated with copper to create electrical connections between layers.
- Etching: The unwanted copper is etched away, leaving only the desired conductive traces.
- Solder Mask Application: A solder mask is applied to the board to protect the conductive traces and prevent short circuits.
-
Silkscreen Printing: Text and symbols are printed on the board for component identification and assembly guidance.
-
Surface Finishing: The exposed copper areas are coated with a protective finish, such as immersion gold (ENIG) or electroless nickel immersion gold (ENEPIG), to prevent oxidation and improve solderability.
-
Inspection and Testing: The manufactured High TG PCBs undergo rigorous inspection and testing to ensure they meet the required quality standards. This includes visual inspection, electrical testing, and thermal stress testing to verify their performance under high-temperature conditions.
The manufacturing process of High TG PCBs requires strict control over the materials and processing parameters to ensure the desired thermal and electrical properties are achieved. Manufacturers specializing in High TG PCBs have the expertise and equipment necessary to produce high-quality boards that meet the specific requirements of high-temperature applications.
Frequently Asked Questions (FAQ)
-
What is the difference between a High TG PCB and a standard PCB?
The main difference between a High TG PCB and a standard PCB lies in the glass transition temperature (TG) of the materials used. High TG PCBs are manufactured using materials with a higher glass transition temperature, typically above 170°C, while standard PCBs use materials with lower glass transition temperatures. This higher temperature resistance allows High TG PCBs to withstand extreme heat and maintain their structural integrity and electrical properties in high-temperature environments. -
What are the typical applications of High TG PCBs?
High TG PCBs are commonly used in applications that involve exposure to high temperatures, such as: - Automotive electronics (engine control units, power modules, sensors)
- Aerospace and defense (avionics, radar systems, satellite communications)
- Industrial equipment (power inverters, motor drives, welding machines)
- LED lighting (high-power LED drivers and control circuits)
-
Medical devices (surgical instruments, sterilization equipment)
-
What are the advantages of using High TG PCBs?
The advantages of using High TG PCBs include: - Enhanced thermal stability, allowing reliable operation in high-temperature environments
- Improved durability and resistance to thermal cycling
- Reduced risk of warping and delamination due to lower coefficient of thermal expansion
- Better signal integrity and reduced signal loss, particularly at higher frequencies
- Compatibility with lead-free soldering processes
-
Cost-effectiveness in high-temperature applications due to reduced maintenance and downtime
-
How does the manufacturing process of High TG PCBs differ from standard PCBs?
The manufacturing process of High TG PCBs is similar to that of standard PCBs, but with key differences in material selection and processing parameters. High TG PCBs use materials with higher glass transition temperatures, such as high-temperature epoxy laminates. The manufacturing process involves strict control over the materials and processing parameters to ensure the desired thermal and electrical properties are achieved. Specialized equipment and expertise are required to produce high-quality High TG PCBs. -
Are High TG PCBs more expensive than standard PCBs?
Yes, High TG PCBs generally have a higher initial cost compared to standard PCBs due to the specialized materials and manufacturing processes involved. However, in applications that involve high temperatures, High TG PCBs offer cost-effectiveness in the long run. The enhanced reliability and durability of High TG PCBs reduce the need for frequent replacements or repairs, ultimately saving costs associated with maintenance and downtime.
Conclusion
High TG PCBs are a specialized type of printed circuit board designed to withstand higher temperatures compared to standard PCBs. With their enhanced thermal stability, improved durability, and better signal integrity, High TG PCBs are well-suited for applications that involve exposure to extreme heat, such as automotive electronics, aerospace and defense systems, industrial equipment, LED lighting, and medical devices.
The manufacturing process of High TG PCBs requires strict control over materials and processing parameters to ensure the desired thermal and electrical properties are achieved. While High TG PCBs may have a higher initial cost, they offer cost-effectiveness in the long run for high-temperature applications by reducing the need for frequent replacements and repairs.
As technology advances and the demand for reliable electronics in challenging environments grows, the use of High TG PCBs is expected to increase. Manufacturers specializing in High TG PCBs continue to innovate and refine their processes to meet the evolving needs of various industries, ensuring the availability of high-quality, temperature-resistant PCBs for demanding applications.
0 Comments