Introduction to Heavy Copper PCB
Heavy Copper PCB, also known as thick copper PCB or high current PCB, is a type of printed circuit board that uses thicker copper traces than standard PCBs. The increased thickness of the copper allows for higher current carrying capacity and better thermal management, making Heavy Copper PCBs ideal for applications that require high power delivery or heat dissipation.
Key Features of Heavy Copper PCB
- Thicker copper traces (typically 3 oz or more)
- Higher current carrying capacity
- Improved thermal management
- Enhanced mechanical strength
- Suitable for high power applications
Applications of Heavy Copper PCB
Heavy copper PCBs find applications in various industries where high power delivery and efficient heat dissipation are crucial. Some common applications include:
Power Electronics
- Switching mode power supplies (SMPS)
- Inverters and converters
- Motor drives
- Uninterruptible power supplies (UPS)
Automotive Industry
- Electric vehicle (EV) battery management systems
- High-power lighting systems
- Engine control units (ECUs)
- Hybrid electric vehicle (HEV) power systems
Industrial Equipment
- Welding machines
- Induction heating systems
- High-power laser systems
- Large-scale manufacturing equipment
Telecommunications
- Base station power amplifiers
- High-power radio frequency (RF) transmitters
- Satellite communication systems
- 5G network infrastructure
Advantages of Using Heavy Copper PCB
Higher Current Carrying Capacity
One of the primary advantages of using heavy copper PCBs is their higher current carrying capacity compared to standard PCBs. The thicker copper traces allow for increased current flow without excessive heating or voltage drop. This makes heavy copper PCBs suitable for applications that require high power delivery, such as power electronics and industrial equipment.
Improved Thermal Management
Heavy copper PCBs offer better thermal management than standard PCBs due to the increased copper thickness. The thicker copper traces act as efficient heat spreaders, allowing for better heat dissipation from high-power components. This helps in maintaining the overall temperature of the PCB within acceptable limits, enhancing the reliability and longevity of the electronic system.
Enhanced Mechanical Strength
The increased copper thickness in heavy copper PCBs also contributes to their enhanced mechanical strength. The thicker copper traces provide better support for heavy components and connectors, reducing the risk of mechanical failures due to vibration or physical stress. This is particularly important in applications that are subjected to harsh environmental conditions or mechanical shocks.
Lower Resistance and Voltage Drop
The thicker copper traces in heavy copper PCBs result in lower electrical resistance compared to standard PCBs. This reduction in resistance leads to lower voltage drops across the traces, ensuring better power delivery to the connected components. The lower voltage drop also helps in maintaining the signal integrity and reducing the overall power loss in the system.
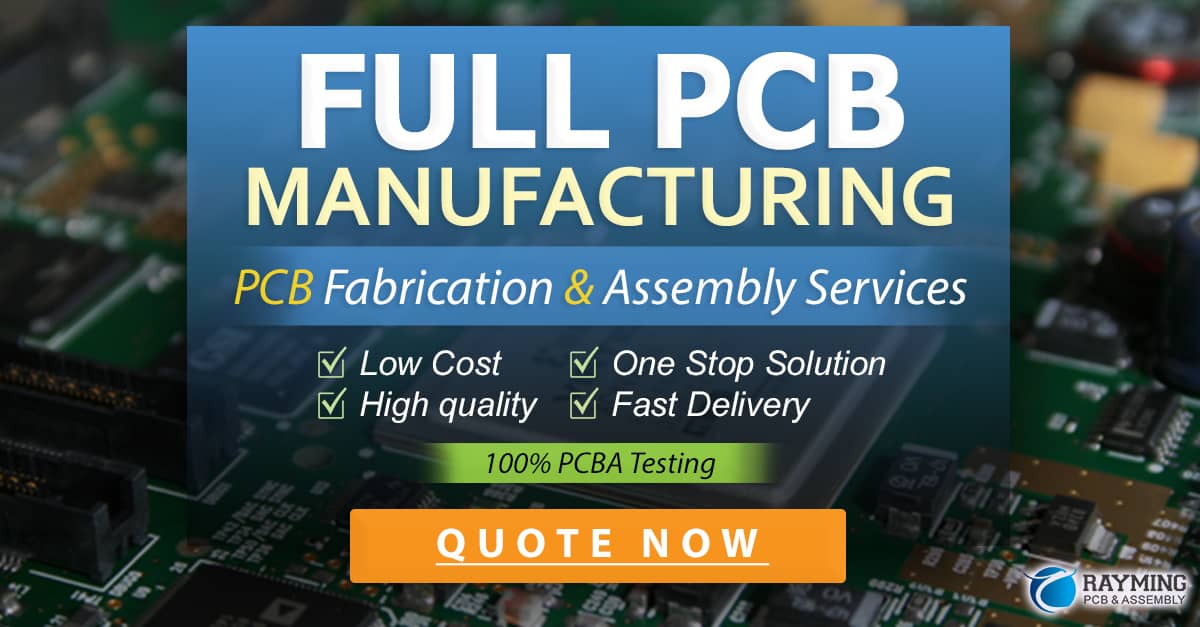
Design Considerations for Heavy Copper PCB
When designing heavy copper PCBs, several key factors need to be considered to ensure optimal performance and manufacturability. These include:
Copper Thickness Selection
The copper thickness for heavy copper PCBs is typically specified in ounces per square foot (oz/ft²). Common thicknesses range from 3 oz to 20 oz, with higher thicknesses used for more demanding applications. The selection of copper thickness depends on the specific requirements of the application, such as current carrying capacity, thermal management, and mechanical strength.
Trace Width and Spacing
The width and spacing of the copper traces on a heavy copper PCB should be carefully designed to ensure proper current carrying capacity and to minimize electromagnetic interference (EMI). Wider traces can carry higher currents, but they also occupy more space on the PCB. The spacing between traces should be sufficient to prevent short circuits and to maintain the required clearance for the intended operating voltage.
Thermal Management Techniques
Effective thermal management is crucial for heavy copper PCBs to prevent overheating and ensure reliable operation. Some common thermal management techniques include:
- Using thermal vias to transfer heat from the top layer to the bottom layer or inner layers of the PCB
- Incorporating heat sinks or heat spreaders to dissipate heat from high-power components
- Utilizing thermal interface materials (TIMs) to enhance heat transfer between components and the PCB
- Designing adequate airflow paths and using forced air cooling when necessary
Manufacturing Considerations
Heavy copper PCBs require specialized manufacturing processes due to the increased copper thickness. Some key manufacturing considerations include:
- Selecting the appropriate laminate material that can withstand the high temperatures and pressures during the lamination process
- Using advanced drilling techniques, such as stepped drilling or via-in-pad, to create reliable electrical connections through the thick copper layers
- Employing proper etching and plating techniques to ensure uniform copper thickness and to avoid undercuts or overhangs
- Conducting thorough electrical and thermal testing to verify the performance and reliability of the manufactured PCBs
Comparison with Standard PCB
Parameter | Standard PCB | Heavy Copper PCB |
---|---|---|
Copper Thickness | 1-2 oz | 3 oz or more |
Current Carrying Capacity | Low to Medium | High |
Thermal Management | Limited | Enhanced |
Mechanical Strength | Moderate | High |
Manufacturing Complexity | Low | High |
Cost | Lower | Higher |
Frequently Asked Questions (FAQ)
1. What is the typical copper thickness used in heavy copper PCBs?
Heavy copper PCBs typically use copper thicknesses of 3 oz or more, with common thicknesses ranging from 3 oz to 20 oz. The specific thickness chosen depends on the requirements of the application, such as current carrying capacity and thermal management.
2. Can heavy copper PCBs be used for high-frequency applications?
While heavy copper PCBs are primarily used for high-power applications, they can also be used for high-frequency applications with proper design considerations. The thicker copper traces can help in reducing the skin effect and providing better shielding against electromagnetic interference (EMI).
3. Are heavy copper PCBs more expensive than standard PCBs?
Yes, heavy copper PCBs are generally more expensive than standard PCBs due to the increased copper thickness and the specialized manufacturing processes required. The cost increase is justified by the enhanced performance and reliability offered by heavy copper PCBs in high-power applications.
4. How do heavy copper PCBs enhance thermal management?
Heavy copper PCBs enhance thermal management by providing thicker copper traces that act as efficient heat spreaders. The increased copper thickness allows for better heat dissipation from high-power components, helping to maintain the overall temperature of the PCB within acceptable limits.
5. What are the challenges in manufacturing heavy copper PCBs?
Manufacturing heavy copper PCBs presents several challenges, including the need for specialized laminate materials, advanced drilling techniques, and proper etching and plating processes. Ensuring uniform copper thickness and avoiding defects such as undercuts or overhangs requires precise control over the manufacturing process.
Conclusion
Heavy copper PCBs offer significant advantages over standard PCBs in applications that require high power delivery and efficient thermal management. The increased copper thickness allows for higher current carrying capacity, better heat dissipation, and enhanced mechanical strength. These benefits make heavy copper PCBs ideal for use in power electronics, automotive systems, industrial equipment, and telecommunications infrastructure.
When designing heavy copper PCBs, careful consideration must be given to factors such as copper thickness selection, trace width and spacing, thermal management techniques, and manufacturing processes. By addressing these design considerations and working closely with experienced PCB manufacturers, engineers can leverage the capabilities of heavy copper PCBs to develop high-performance electronic systems that meet the demanding requirements of modern applications.
As technology continues to advance and the demand for high-power electronics grows, heavy copper PCBs are poised to play an increasingly important role in enabling the development of robust and reliable electronic systems across a wide range of industries.
0 Comments