Why is Conformal Coating Important for PCBs?
Conformal coating plays a crucial role in protecting PCBs from various environmental factors that can lead to premature failure or malfunction. Some of the key reasons why conformal coating is essential for PCBs include:
Protection from Moisture and Humidity
One of the primary functions of conformal coating is to protect PCBs from moisture and humidity. When exposed to high levels of moisture, PCBs can experience corrosion, which can lead to short circuits and other electrical issues. Conformal coating creates a barrier that prevents moisture from reaching the components and circuitry on the board, thereby reducing the risk of corrosion.
Insulation and Dielectric Properties
Conformal coatings also provide insulation and dielectric properties to PCBs. This helps to prevent short circuits and electrical leakage between components, which can cause the device to malfunction or fail. The insulating properties of conformal coatings are particularly important in high-voltage applications, where the risk of electrical discharge is higher.
Protection from Dust and Debris
Dust and debris can accumulate on PCBs over time, leading to various issues such as short circuits, overheating, and reduced performance. Conformal coating creates a smooth, uniform surface that prevents dust and debris from settling on the board, thereby maintaining its integrity and performance.
Resistance to Chemicals and Solvents
In many industrial applications, PCBs may be exposed to harsh chemicals and solvents that can degrade the components and circuitry on the board. Conformal coatings provide a protective barrier that resists the effects of these chemicals, ensuring the long-term reliability and performance of the device.
Enhanced Mechanical Strength
Conformal coatings can also improve the mechanical strength of PCBs by providing a layer of protection against physical damage, such as vibration and impact. This is particularly important in applications where the device is subject to harsh mechanical stresses, such as in automotive or aerospace electronics.
Types of Conformal Coatings
There are several types of conformal coatings available, each with its own unique properties and advantages. The most common types of conformal coatings include:
Acrylic
Acrylic conformal coatings are known for their excellent moisture resistance, dielectric properties, and ease of application. They are also relatively inexpensive compared to other types of coatings. However, acrylic coatings may not provide the same level of protection against harsh chemicals and solvents as other types of coatings.
Silicone
Silicone conformal coatings offer excellent protection against moisture, chemicals, and extreme temperatures. They are also highly flexible, making them ideal for applications where the PCB may be subject to vibration or mechanical stress. However, silicone coatings can be more difficult to apply and remove than other types of coatings.
Polyurethane
Polyurethane conformal coatings provide excellent protection against abrasion, moisture, and chemicals. They are also highly durable and offer good dielectric properties. However, polyurethane coatings may be more expensive than other types of coatings and can be difficult to remove if repairs are needed.
Epoxy
Epoxy conformal coatings are known for their excellent resistance to chemicals, moisture, and abrasion. They also provide good dielectric properties and are highly durable. However, epoxy coatings can be brittle and may crack under excessive mechanical stress. They are also more difficult to remove than other types of coatings.
Parylene
Parylene conformal coatings are ultra-thin, pinhole-free coatings that offer excellent protection against moisture, chemicals, and corrosion. They are also highly conformal, meaning they can cover even the most intricate geometries on a PCB. However, parylene coatings are more expensive than other types of coatings and require specialized equipment for application.
Coating Type | Moisture Resistance | Chemical Resistance | Dielectric Strength | Ease of Application | Ease of Removal |
---|---|---|---|---|---|
Acrylic | Excellent | Good | Good | Easy | Easy |
Silicone | Excellent | Excellent | Good | Moderate | Difficult |
Polyurethane | Excellent | Excellent | Good | Moderate | Difficult |
Epoxy | Excellent | Excellent | Good | Moderate | Difficult |
Parylene | Excellent | Excellent | Excellent | Difficult | Difficult |
Conformal Coating Application Methods
There are several methods for applying conformal coatings to PCBs, each with its own advantages and disadvantages. The choice of application method depends on factors such as the type of coating being used, the size and complexity of the PCB, and the production volume.
Brush Coating
Brush coating is a manual method of applying conformal coatings using a brush or applicator. This method is suitable for small-scale production or for coating specific areas of a PCB. Brush coating is relatively inexpensive and requires minimal equipment, but it can be time-consuming and may result in an uneven coating thickness.
Dip Coating
Dip coating involves immersing the PCB in a bath of conformal coating material and then allowing it to drain and cure. This method is suitable for coating large numbers of PCBs quickly and efficiently. However, dip coating may result in excess coating material on the board, which can lead to issues such as bridging between components.
Spray Coating
Spray coating involves using a spray gun to apply the conformal coating to the PCB. This method is suitable for coating large areas quickly and efficiently, and it allows for better control over the coating thickness compared to dip coating. However, spray coating requires specialized equipment and may result in overspray or uneven coverage.
Selective Coating
Selective coating involves applying the conformal coating only to specific areas of the PCB, such as critical components or connectors. This method is suitable for applications where certain areas of the board need to remain uncoated, such as for testing or assembly purposes. Selective coating can be performed using various methods, such as needle dispensing or masking.
Vapor Deposition
Vapor deposition is a specialized method of applying parylene conformal coatings. In this process, the parylene material is vaporized and then deposited onto the PCB in a vacuum chamber. This method results in an ultra-thin, highly conformal coating that covers even the most intricate geometries on the board. However, vapor deposition requires specialized equipment and is more expensive than other application methods.
Application Method | Coating Uniformity | Speed | Cost | Suitable Coatings |
---|---|---|---|---|
Brush Coating | Low | Slow | Low | Most types |
Dip Coating | Moderate | Fast | Moderate | Most types |
Spray Coating | High | Fast | Moderate | Most types |
Selective Coating | High | Slow | High | Most types |
Vapor Deposition | Very High | Moderate | High | Parylene |
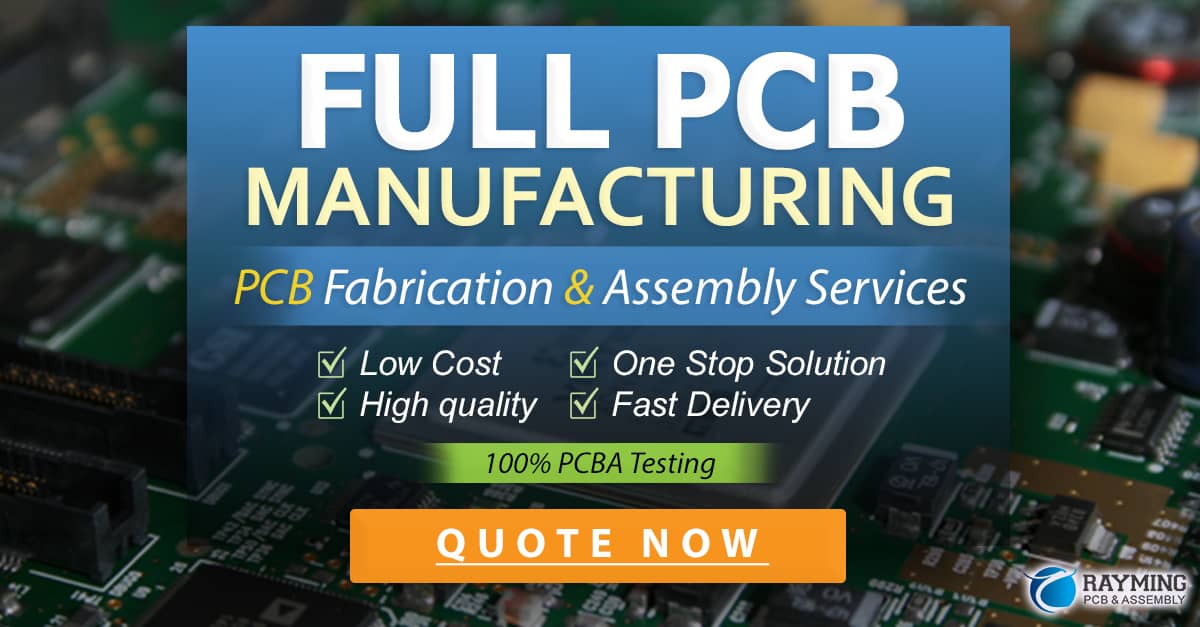
Conformal Coating Inspection and Quality Control
To ensure the effectiveness and reliability of conformal coatings, it is essential to perform thorough inspection and quality control procedures. Some of the key methods for inspecting and verifying the quality of conformal coatings include:
Visual Inspection
Visual inspection is the most basic method of checking the quality of a conformal coating. This involves examining the coated PCB under magnification to look for defects such as bubbles, pinholes, or uneven coverage. Visual inspection is relatively quick and inexpensive, but it may not detect all types of defects.
Thickness Measurement
Measuring the thickness of the conformal coating is important to ensure that it meets the specified requirements for the application. This can be done using various methods, such as using a thickness gauge or performing a cross-sectional analysis. Ensuring the correct coating thickness is critical for achieving the desired level of protection and performance.
Adhesion Testing
Adhesion testing is performed to ensure that the conformal coating is properly bonded to the PCB and will not delaminate or peel off over time. This can be done using methods such as the cross-hatch adhesion test, where a pattern is cut into the coating and then checked for any signs of peeling or flaking.
Dielectric Withstand Testing
Dielectric withstand testing involves applying a high voltage to the coated PCB to ensure that it can withstand the required level of electrical stress without breaking down or experiencing leakage. This test is particularly important for applications where the PCB will be exposed to high voltages or electrical discharges.
Environmental Testing
Environmental testing involves exposing the coated PCB to various environmental conditions, such as humidity, temperature, and vibration, to ensure that the coating provides adequate protection against these factors. This type of testing is essential for applications where the PCB will be exposed to harsh environmental conditions, such as in automotive or aerospace electronics.
Removing and Repairing Conformal Coatings
In some cases, it may be necessary to remove or repair a conformal coating on a PCB, such as for rework or troubleshooting purposes. The method for removing or repairing the coating depends on the type of coating material and the extent of the damage.
Mechanical Removal
Mechanical removal involves using tools such as scrapers, blades, or abrasives to physically remove the conformal coating from the PCB. This method is suitable for small areas or for coatings that are not strongly bonded to the board. However, mechanical removal can be time-consuming and may risk damaging the components or circuitry on the board.
Chemical Removal
Chemical removal involves using solvents or strippers to dissolve the conformal coating material. This method is suitable for larger areas or for coatings that are difficult to remove mechanically. However, chemical removal requires careful selection of the appropriate solvent and may involve safety hazards such as flammability or toxicity.
Spot Repair
Spot repair involves applying additional conformal coating material to specific areas of the PCB where the original coating has been damaged or removed. This method is suitable for small, localized repairs and can be performed using various application methods such as brush coating or needle dispensing. Spot repair can help to restore the protection and performance of the coating without the need for a full removal and reapplication.
Thermal Removal
Thermal removal involves using heat to soften or burn off the conformal coating material. This method is suitable for coatings that are not easily removed by mechanical or chemical means, such as parylene. However, thermal removal requires specialized equipment and can be time-consuming and expensive.
Frequently Asked Questions (FAQ)
1. How do I choose the right conformal coating for my PCB?
Choosing the right conformal coating depends on several factors, such as the environmental conditions the PCB will be exposed to, the required level of protection, and the compatibility with the components and materials on the board. It’s important to consider the specific requirements of your application and consult with a coating supplier or expert to select the most appropriate coating material.
2. Can conformal coatings be applied to PCBs with surface-mount components?
Yes, conformal coatings can be applied to PCBs with surface-mount components. However, it’s important to ensure that the coating material is compatible with the components and that the application method is suitable for the size and geometry of the components. In some cases, selective coating or masking may be necessary to avoid coating certain areas of the board.
3. How long does a conformal coating typically last?
The lifespan of a conformal coating depends on various factors, such as the type of coating material, the environmental conditions, and the quality of the application. In general, conformal coatings can last for several years or even decades, provided they are applied correctly and not subjected to excessive damage or wear. Regular inspections and maintenance can help to extend the lifespan of the coating.
4. Can conformal coatings be applied to flexible PCBs?
Yes, conformal coatings can be applied to flexible PCBs, but it’s important to choose a coating material that is suitable for the specific requirements of the application. Some coating materials, such as silicone or polyurethane, are more flexible and can accommodate the bending and flexing of the PCB. Other materials, such as acrylic or epoxy, may be too rigid and can crack or delaminate under stress.
5. Are there any drawbacks to using conformal coatings on PCBs?
While conformal coatings offer many benefits for protecting PCBs, there are some potential drawbacks to consider. These include added cost and complexity to the manufacturing process, potential compatibility issues with certain components or materials, and the need for specialized equipment and expertise for application and removal. Additionally, conformal coatings can make it more difficult to inspect or repair the PCB if issues arise.
In conclusion, conformal coating is an essential process for protecting PCBs from environmental hazards and ensuring their long-term reliability and performance. By understanding the different types of coatings, application methods, and quality control procedures, manufacturers can select the most appropriate coating solution for their specific application. While there are some potential drawbacks to using conformal coatings, the benefits in terms of improved protection and durability often outweigh these concerns. As electronic devices continue to become more complex and are exposed to increasingly harsh environments, the use of conformal coatings is likely to become even more important in the years ahead.
0 Comments