How Does CNC Work?
The CNC process involves the following steps:
-
Designing the CAD Model: The process begins with creating a 2D or 3D CAD (Computer-Aided Design) model of the part to be produced. This model is then converted into a CNC program using CAM (Computer-Aided Manufacturing) software.
-
Preparing the CNC Machine: The program is loaded into the CNC machine, and the operator sets up the machine with the necessary tools, attaches the workpiece, and performs any required calibration.
-
Executing the CNC Program: The CNC machine executes the programmed sequence of controlled steps. The program directs the machine to use various tools to cut the workpiece into the desired shape, with the machine controlling the tool speed, rotation, and movement.
-
Post-Processing: After the CNC machining process, the part is inspected, cleaned, and, if necessary, further processed (e.g., painted or coated) before it is ready for use.
Types of CNC Machines
There are several types of CNC machines, each designed for specific purposes:
CNC Mills
CNC mills, or machining centers, are computer-controlled vertical mills with the ability to move the spindle vertically along the Z-axis. This enables the creation of parts with a variety of shapes and features, such as slots, pockets, and holes.
CNC Lathes
CNC lathes are used to produce cylindrical parts by rotating the workpiece while a tool is applied to it. These machines can perform multiple operations like turning, facing, threading, and drilling.
CNC Routers
CNC routers are used for cutting softer materials like wood, foam, and plastics. They are commonly used in woodworking, sign making, and prototyping applications.
Other CNC Machines
Some other types of CNC machines include:
– Plasma cutters
– Laser Cutters
– Water jet cutters
– Electric discharge machines (EDM)
– CNC grinding machines
Advantages of CNC Machining
CNC machining offers several advantages over traditional manufacturing methods:
-
Precision: CNC machines can produce parts with extremely tight tolerances, often within +/- 0.001 inches, which is difficult to achieve with manual machining.
-
Repeatability: Once a CNC program is created, it can be used to produce identical parts repeatedly without any variation in quality.
-
Efficiency: CNC machines can work continuously without breaks, reducing production time and increasing output.
-
Complexity: CNC machining can produce complex geometries and intricate details that would be challenging or impossible to achieve with manual methods.
-
Flexibility: CNC machines can be quickly reprogrammed to produce different parts, making them ideal for small-batch production and prototyping.
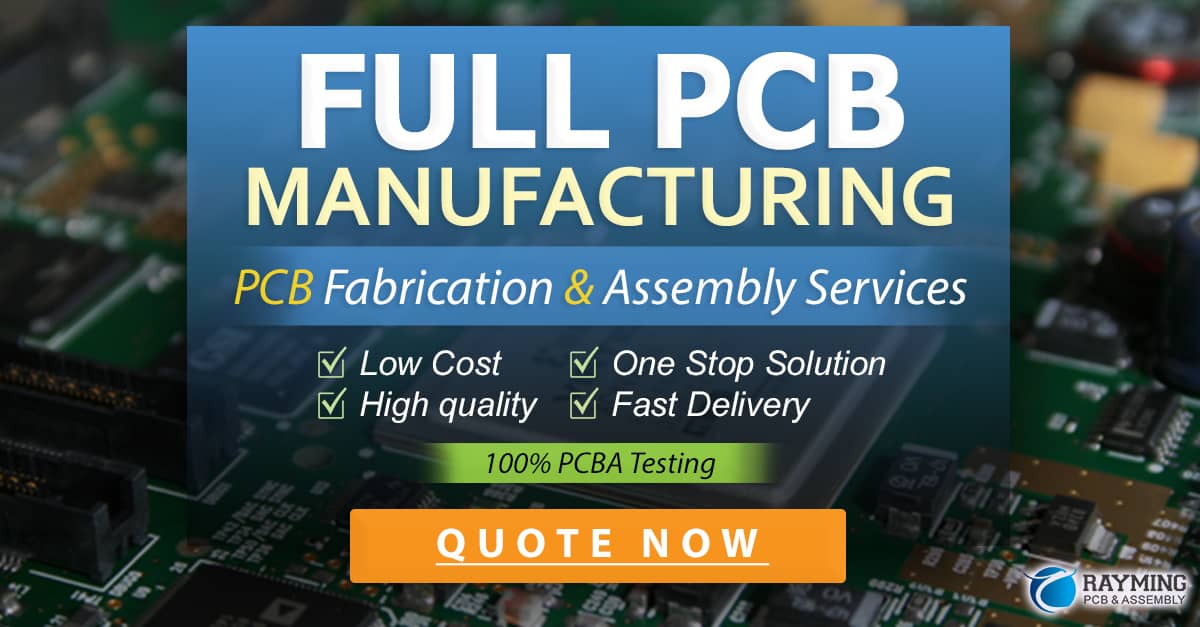
Applications of CNC Machining
CNC machining finds application in various industries, including:
- Aerospace
- Automotive
- Medical devices
- Electronics
- Consumer products
- Defense
- Oil and gas
Some specific examples of CNC machined parts include:
- Engine components
- Molds and dies
- Prosthetics and implants
- Electronic housings
- Furniture components
- Firearm parts
- Valves and fittings
CNC Programming
CNC programming involves creating a set of instructions that direct the CNC machine to perform specific operations. There are two main methods of CNC programming:
-
CAM Programming: CAM (Computer-Aided Manufacturing) software is used to create a CNC program from a CAD model. The software generates tool paths based on the geometry of the part and the specified machining operations.
-
G-Code Programming: G-code is the most common CNC programming language. It consists of a series of commands that tell the machine where to move, how fast to move, and what operations to perform. G-code can be written manually or generated by CAM software.
Here’s an example of a simple G-code program:
O1000
N10 G90 G54 G49 G80
N20 M06 T01
N30 G43 H01 M03 S1000
N40 G00 X0 Y0 Z0.1
N50 G01 Z-0.1 F100
N60 X1 Y1
N70 X2 Y2
N80 G00 Z0.1
N90 M05
N100 M30
This program does the following:
- Sets the coordinate system and cancels any active tool compensation or canned cycles (N10).
- Changes the tool to tool number 1 (N20).
- Activates tool length compensation, turns on the spindle clockwise at 1000 RPM (N30).
- Rapid moves to X0, Y0, and Z0.1 (N40).
- Linear moves to Z-0.1 at a feed rate of 100 mm/min (N50).
- Linear moves to X1, Y1 (N60).
- Linear moves to X2, Y2 (N70).
- Rapid moves to Z0.1 (N80).
- Stops the spindle (N90).
- Ends the program (N100).
CNC Machine Components
A typical CNC machine consists of the following components:
-
Bed: The bed is the base of the machine, providing a stable platform for the other components.
-
Column: The column is mounted on the bed and provides support for the spindle and other moving parts.
-
Spindle: The spindle holds and rotates the cutting tool. It is driven by an electric motor and can rotate at high speeds, typically between 1,000 and 20,000 RPM.
-
Axes: CNC machines typically have three linear axes (X, Y, and Z) and may also have rotary axes (A, B, and C). These axes allow the machine to move the tool or workpiece in different directions.
-
Tool Changer: The tool changer holds multiple cutting tools and automatically changes them as needed during the machining process.
-
Control Panel: The control panel is the interface between the operator and the machine. It includes a display, keyboard, and various buttons and switches for controlling the machine.
-
Coolant System: The coolant system supplies a steady stream of coolant to the cutting tool and workpiece to reduce heat and friction, prolonging tool life and improving the quality of the cut.
Factors Affecting CNC Machining Quality
Several factors can affect the quality of CNC machined parts:
-
Material: The type and quality of the material being machined can significantly impact the final part. Some materials, like aluminum and brass, are easier to machine than others, like stainless steel or titanium.
-
Cutting Tools: The selection of appropriate cutting tools, including the material, coating, and geometry, is critical for achieving the desired surface finish and dimensional accuracy.
-
Machining Parameters: Feed rate, spindle speed, and depth of cut must be carefully selected based on the material and tool being used. Incorrect parameters can lead to poor surface finish, tool wear, or even breakage.
-
Fixturing: Proper fixturing is essential for holding the workpiece securely and preventing vibration during machining. Inadequate fixturing can result in dimensional inaccuracies or damage to the part.
-
Machine Condition: Regular maintenance and calibration of the CNC machine are necessary to ensure consistent accuracy and performance.
Choosing a CNC Machine
When selecting a CNC machine, consider the following factors:
-
Workspace: The size of the machine’s workspace should accommodate the largest part you plan to produce.
-
Spindle Power: The spindle power determines the machine’s ability to cut through harder materials and take deeper cuts.
-
Axis Travel: The axis travel determines the maximum size of the part that can be machined in a single setup.
-
Tool Changer Capacity: A larger tool changer capacity allows for more tools to be used in a single program, reducing setup time.
-
Control System: The control system should be user-friendly and compatible with your CAD/CAM software.
-
Precision: Consider the machine’s repeatability and positioning accuracy, which are critical for producing high-quality parts.
-
Price: CNC machines can vary greatly in price, from small desktop models to large industrial machines. Choose a machine that fits your budget and production needs.
Frequently Asked Questions (FAQ)
1. What is the difference between CNC and conventional machining?
Conventional machining relies on manual control of the machine tools, while CNC machining uses computer-controlled movements. CNC machining offers greater precision, repeatability, and efficiency compared to conventional machining.
2. What materials can be machined with a CNC machine?
CNC machines can work with a wide range of materials, including metals (aluminum, steel, brass, titanium), plastics (ABS, nylon, polycarbonate), wood, composites, and foam.
3. How long does it take to learn CNC programming?
The time required to learn CNC programming varies depending on the individual’s background and the complexity of the projects. Basic CNC programming can be learned in a few weeks, while more advanced programming may take several months or even years of practice.
4. What is the accuracy of a CNC machine?
The accuracy of a CNC machine depends on several factors, including the machine’s design, calibration, and maintenance. High-end CNC machines can achieve accuracies of +/- 0.001 inches or better.
5. How much does a CNC machine cost?
The cost of a CNC machine can range from a few thousand dollars for a small desktop model to hundreds of thousands of dollars for a large industrial machine. The price depends on factors such as the size, precision, and features of the machine.
Conclusion
CNC machining is a versatile and precise manufacturing process that has revolutionized the production of complex parts and components. By understanding the basics of CNC technology, including machine types, programming methods, and factors affecting quality, manufacturers can leverage the power of CNC machining to produce high-quality parts efficiently and consistently. As CNC technology continues to advance, it will undoubtedly play an increasingly important role in shaping the future of manufacturing.
0 Comments