What is a Bill of Materials (BOM)?
A Bill of Materials (BOM) is a centralized source of information that lists all the materials, components, and parts required to manufacture a product, along with the quantities of each. It serves as a key document for communication between engineering, manufacturing, and procurement teams. The BOM provides a clear and concise list of what is needed to build a product, helping to streamline the manufacturing process and ensure that all necessary components are available when required.
Key Components of a Bill of Materials
A typical BOM includes the following key components:
- Part Number: A unique identifier for each component or sub-assembly.
- Part Name: A brief description of the part or component.
- Quantity: The number of units required for each component to manufacture the final product.
- Unit of Measure: The standard unit used to quantify the component (e.g., pieces, liters, kilograms).
- Procurement Type: Indicates whether the component is manufactured in-house, purchased from an external supplier, or a combination of both.
- Reference Designators: Specific labels or codes that identify the location of each component within the product.
Types of Bill of Materials
There are several types of BOMs, each serving a specific purpose within the manufacturing process. The most common types include:
1. Engineering Bill of Materials (EBOM)
An Engineering Bill of Materials (EBOM) is a type of BOM created by the engineering department. It lists all the components and sub-assemblies required to create a product, as designed by the engineers. The EBOM focuses on the product’s design and functionality rather than the manufacturing process.
2. Manufacturing Bill of Materials (MBOM)
A Manufacturing Bill of Materials (MBOM) is derived from the EBOM and is tailored to the manufacturing process. It lists all the components and sub-assemblies needed to physically build the product on the factory floor. The MBOM may differ from the EBOM as it takes into account factors such as manufacturing techniques, assembly sequences, and packaging requirements.
3. Sales Bill of Materials (SBOM)
A Sales Bill of Materials (SBOM) is a customer-facing document that lists all the components and sub-assemblies that are included when a product is sold. It is often used in configure-to-order (CTO) or assemble-to-order (ATO) environments, where customers can choose from various options to customize their products.
4. Configurable Bill of Materials (CBOM)
A Configurable Bill of Materials (CBOM) is used for products that have multiple variations or configurations. It defines the different options available for each component, allowing for greater flexibility in product customization. The CBOM is often used in conjunction with the SBOM to create custom product configurations based on customer requirements.
Benefits of Using a Bill of Materials
Implementing a well-structured BOM offers several key benefits to manufacturers:
- Improved Accuracy: A BOM provides a clear and accurate list of all components required for production, reducing the risk of errors or omissions.
- Enhanced Communication: BOMs facilitate better communication between engineering, manufacturing, procurement, and other departments involved in the production process.
- Streamlined Procurement: With a detailed BOM, procurement teams can easily identify and order the necessary components, reducing lead times and ensuring timely availability of materials.
- Increased Efficiency: BOMs help optimize inventory management by providing accurate information on the quantities of each component needed, reducing waste and overstocking.
- Cost Control: By precisely defining the materials required, BOMs help manufacturers control costs and identify opportunities for cost savings through better sourcing or design changes.
- Faster Time-to-Market: A well-maintained BOM enables faster product development and launch by ensuring that all necessary components are identified and available when needed.
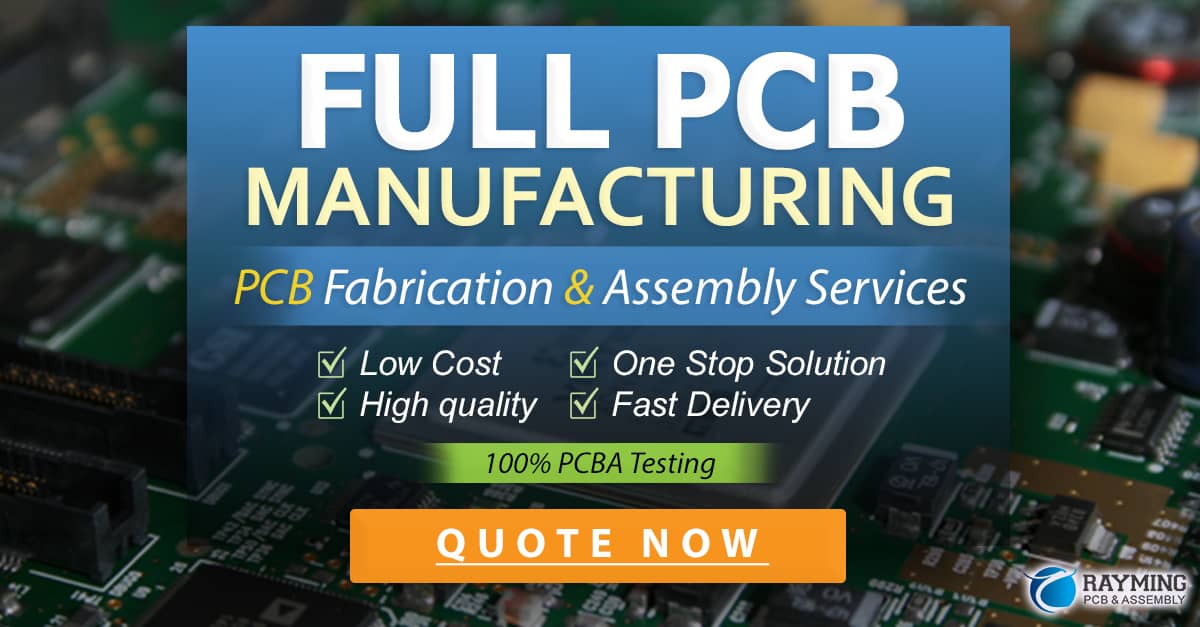
How to Create a Bill of Materials
Creating a comprehensive and accurate BOM involves several key steps:
- Define the Product Structure: Break down the product into its main components, sub-assemblies, and individual parts. Use a hierarchical structure to show the relationships between components.
- Assign Part Numbers: Allocate unique part numbers to each component and sub-assembly to ensure easy identification and tracking.
- Determine Quantities: Specify the quantity of each component required to manufacture one unit of the final product.
- Include Relevant Information: Add details such as part descriptions, unit of measure, procurement type, and reference designators to provide a complete picture of each component.
- Review and Validate: Carefully review the BOM to ensure accuracy and completeness. Validate the BOM with stakeholders from engineering, manufacturing, and procurement to ensure alignment.
- Maintain and Update: Regularly update the BOM to reflect any changes in product design, component specifications, or supplier information.
BOM Example for Download
To help you better understand the structure and content of a Bill of Materials, we have provided a downloadable example in Excel format. This example includes a sample product with its components, quantities, and other relevant information. You can use this example as a template to create your own BOMs or as a reference when working with existing BOMs.
Part Number | Part Name | Quantity | Unit of Measure | Procurement Type | Reference Designator |
---|---|---|---|---|---|
A1000 | Product Assembly | 1 | EA | Make | |
A1100 | Sub-Assembly 1 | 1 | EA | Make | SA1 |
P1101 | Part 1 | 2 | EA | Buy | P1 |
P1102 | Part 2 | 4 | EA | Buy | P2 |
A1200 | Sub-Assembly 2 | 1 | EA | Make | SA2 |
P1201 | Part 3 | 1 | EA | Buy | P3 |
P1202 | Part 4 | 3 | EA | Buy | P4 |
Frequently Asked Questions (FAQ)
1. What is the difference between a BOM and a parts list?
A BOM is a hierarchical document that lists all the components, sub-assemblies, and raw materials required to manufacture a product, along with their quantities and relationships. A parts list, on the other hand, is a simpler document that lists all the individual parts needed for a product, without necessarily showing the hierarchical relationships between them.
2. How often should a BOM be updated?
A BOM should be updated whenever there are changes to the product design, components, or supplier information. It is important to maintain an up-to-date BOM to ensure accurate production planning and avoid potential issues due to outdated information.
3. Can a BOM include non-physical components?
Yes, a BOM can include non-physical components such as software, licenses, or services that are required for the final product. These components should be clearly identified and included in the BOM to provide a complete picture of the product requirements.
4. How does a BOM relate to inventory management?
A BOM provides essential information for inventory management by specifying the exact quantities of each component required to manufacture a product. This information helps in planning and maintaining appropriate inventory levels, ensuring that the necessary components are available when needed and minimizing the risk of stockouts or overstocking.
5. What are the challenges in managing BOMs?
Some common challenges in managing BOMs include:
– Maintaining accuracy and consistency across multiple BOM versions and revisions.
– Ensuring timely updates to reflect changes in product design or component specifications.
– Collaborating effectively with different departments and stakeholders involved in the BOM process.
– Integrating BOM data with other systems such as ERP, MRP, or PLM software.
To overcome these challenges, organizations should establish clear processes for BOM creation, maintenance, and change management, as well as invest in tools and systems that facilitate collaboration and data integration.
Conclusion
A Bill of Materials (BOM) is a critical document in the manufacturing process, providing a comprehensive list of all components, sub-assemblies, and raw materials required to produce a final product. By creating and maintaining accurate BOMs, manufacturers can streamline their production processes, improve communication between departments, and optimize inventory management.
This article has provided an in-depth understanding of BOMs, including their key components, types, benefits, and the steps involved in creating them. With the downloadable BOM example and the knowledge gained from this article, you are well-equipped to create and manage effective BOMs for your manufacturing needs.
0 Comments