Introduction to PCBs
A Printed Circuit Board (PCB) is a fundamental component in modern electronic devices. It is a flat board made of insulating materials, such as fiberglass or composite epoxy, with conductive pathways etched or printed onto its surface. These pathways, also known as traces, connect various electronic components, such as resistors, capacitors, and integrated circuits (ICs), to create a complete electrical circuit.
PCBs have revolutionized the electronics industry by providing a compact, reliable, and cost-effective solution for assembling electronic circuits. They have replaced the earlier methods of point-to-point wiring and wire wrapping, which were time-consuming, error-prone, and difficult to mass-produce.
Key Benefits of PCBs
- Compact size
- Improved reliability
- Reduced wiring errors
- Easier troubleshooting
- Cost-effective mass production
- Consistent performance
Types of PCBs
There are several types of PCBs, each with its own unique characteristics and applications. The most common types include:
1. Single-sided PCBs
Single-sided PCBs have conductive traces on only one side of the board. They are the simplest and most cost-effective type of PCB, suitable for basic electronic projects and low-density designs.
2. Double-sided PCBs
Double-sided PCBs have conductive traces on both sides of the board, allowing for a higher component density and more complex circuit designs. The two sides are connected through plated holes called vias.
3. Multi-layer PCBs
Multi-layer PCBs consist of three or more conductive layers separated by insulating layers. They offer the highest component density and are used in complex electronic devices, such as smartphones, computers, and aerospace systems.
PCB Type | Layers | Cost | Complexity | Applications |
---|---|---|---|---|
Single-sided | 1 | Low | Low | Simple circuits, hobbyist projects |
Double-sided | 2 | Medium | Medium | Most consumer electronics |
Multi-layer | 3+ | High | High | Complex devices, aerospace, military |
4. Flexible PCBs
Flexible PCBs are made of thin, flexible materials that can bend and twist without damaging the circuit. They are used in applications where space is limited or where the device needs to conform to a specific shape, such as in wearable electronics and medical devices.
5. Rigid-Flex PCBs
Rigid-Flex PCBs combine the benefits of both rigid and flexible PCBs. They consist of rigid sections connected by flexible sections, allowing for three-dimensional circuit designs and improved reliability in applications with high vibration or shock.
PCB Design and Fabrication Process
The PCB design and fabrication process involves several steps, each critical to ensuring the quality and functionality of the final product.
1. Schematic Design
The first step is to create a schematic diagram of the electronic circuit. This diagram represents the electrical connections between components using standardized symbols.
2. PCB Layout
Once the schematic is complete, the PCB layout is created using specialized software. The layout determines the physical placement of components and the routing of conductive traces on the board.
3. Gerber File Generation
After the layout is finalized, Gerber files are generated. These files contain the necessary information for PCB fabrication, including the copper layers, solder mask, silkscreen, and drill holes.
4. PCB Fabrication
The Gerber files are sent to a PCB manufacturer, who uses them to fabricate the physical board. The fabrication process involves several steps, such as:
- Copper deposition
- Photoresist application
- Exposure and development
- Etching
- Solder mask application
- Silkscreen printing
5. PCB Assembly
Once the PCB is fabricated, the electronic components are soldered onto the board using either through-hole or surface-mount technology (SMT). This process can be done manually for small-scale production or using automated pick-and-place machines for large-scale manufacturing.
Step | Process | Output |
---|---|---|
1 | Schematic Design | Schematic Diagram |
2 | PCB Layout | Physical Layout |
3 | Gerber File Generation | Gerber Files |
4 | PCB Fabrication | Bare PCB |
5 | PCB Assembly | Assembled PCB |
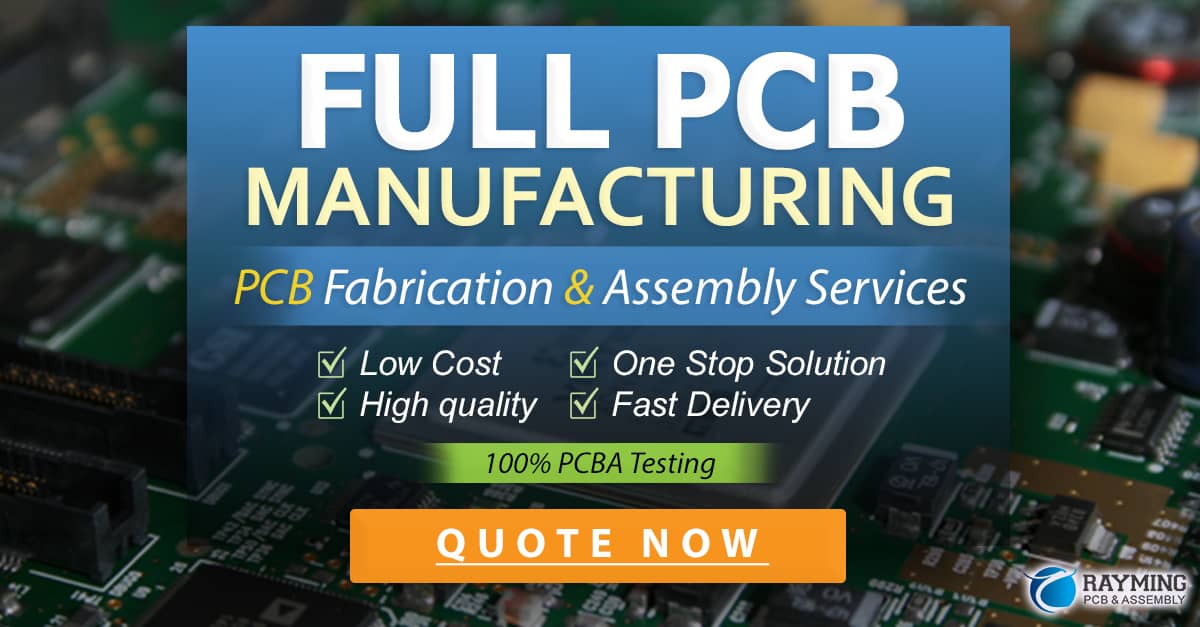
PCB Materials and Components
1. PCB Substrates
The most common PCB substrates are:
- FR-4: A composite material made of fiberglass and epoxy resin, offering good mechanical and electrical properties.
- Polyimide: A flexible material used in flexible PCBs, with high heat resistance and good electrical insulation.
- Aluminum: Used in metal-core PCBs for improved heat dissipation in high-power applications.
2. Copper Traces
Copper is the most common material used for creating conductive traces on PCBs due to its excellent electrical conductivity and relatively low cost. The thickness of the copper layer is measured in ounces per square foot (oz/ft²), with common thicknesses being 1 oz/ft² and 2 oz/ft².
3. Solder Mask
A solder mask is a protective layer applied over the copper traces to prevent accidental short circuits and improve the PCB’s appearance. It is typically green in color but can also be found in other colors, such as blue, red, or black.
4. Silkscreen
The silkscreen is a text and symbol layer printed onto the PCB to help identify components, connectors, and other features. It is usually white in color and is applied on top of the solder mask.
PCB Testing and Inspection
To ensure the quality and reliability of PCBs, several testing and inspection methods are employed during and after the manufacturing process.
1. Automated Optical Inspection (AOI)
AOI uses high-resolution cameras and image processing software to inspect the PCB for defects such as incorrect component placement, solder bridges, and missing components.
2. X-ray Inspection
X-ray inspection is used to detect defects in solder joints, particularly for components with hidden pins, such as Ball Grid Arrays (BGAs) and Quad Flat No-leads (QFNs).
3. In-Circuit Testing (ICT)
ICT involves using a bed-of-nails fixture to make electrical contact with specific points on the PCB, allowing for the testing of individual components and circuits.
4. Functional Testing
Functional testing involves powering up the assembled PCB and verifying that it performs as intended, based on the design specifications.
Applications of PCBs
PCBs are used in a wide range of electronic devices and systems, including:
- Consumer electronics (smartphones, laptops, televisions)
- Automotive electronics (engine control units, infotainment systems)
- Medical devices (pacemakers, blood glucose monitors)
- Aerospace and defense systems (avionics, radar, missiles)
- Industrial automation and control systems (PLCs, sensors, actuators)
Future Trends in PCB Technology
As electronic devices continue to evolve, so do PCBs. Some of the latest trends in PCB technology include:
-
High-Density Interconnect (HDI) PCBs: These PCBs feature finer traces and smaller vias, allowing for even higher component density and improved signal integrity.
-
Embedded components: Passive components, such as resistors and capacitors, can be embedded within the PCB substrate, saving space and improving performance.
-
3D printing: Advancements in 3D printing technology may enable the rapid prototyping and low-volume production of PCBs with complex geometries.
-
Eco-friendly materials: There is a growing interest in using environmentally friendly PCB materials, such as halogen-free substrates and lead-free solders, to reduce the environmental impact of electronic waste.
Frequently Asked Questions (FAQ)
1. What is the difference between a PCB and a breadboard?
A breadboard is a prototyping tool used for temporarily building and testing electronic circuits without soldering. PCBs, on the other hand, are permanent boards with copper traces and components soldered onto them, designed for long-term use in electronic devices.
2. Can I design my own PCB?
Yes, you can design your own PCB using various software tools, such as KiCad, Eagle, and Altium Designer. However, designing a PCB requires knowledge of electronic circuits, PCB layout principles, and design rules.
3. How much does it cost to manufacture a PCB?
The cost of manufacturing a PCB depends on several factors, such as the board size, number of layers, quantity, and turnaround time. Small, single-sided PCBs can cost as little as a few dollars each, while complex, multi-layer PCBs can cost hundreds of dollars per board.
4. What is the typical turnaround time for PCB fabrication?
The turnaround time for PCB fabrication varies depending on the complexity of the board and the manufacturer’s workload. Standard lead times can range from a few days to several weeks, while expedited services may offer faster turnaround times at a higher cost.
5. Can I assemble my own PCB?
Yes, you can assemble your own PCB using a soldering iron and the appropriate tools and techniques. However, for complex boards or large-scale production, it is often more efficient and cost-effective to use professional PCB assembly services.
Conclusion
PCBs are essential components in modern electronic devices, offering a compact, reliable, and cost-effective solution for assembling electronic circuits. By understanding the different types of PCBs, their design and fabrication process, and the materials and components used, you can better appreciate the role they play in our everyday lives. As PCB technology continues to evolve, we can expect to see even more innovative and advanced applications in the future.
0 Comments