PCB Composition: An Overview
The Substrate Layer
The substrate layer is the foundation of a PCB, providing the base material on which the other layers are built. The most common substrate materials are:
-
FR-4: A glass-reinforced epoxy laminate, FR-4 is the most widely used substrate material due to its excellent mechanical and electrical properties, as well as its cost-effectiveness.
-
High-Frequency Laminates: For applications requiring higher frequencies, such as RF and microwave devices, special substrate materials like Rogers, Teflon, or ceramic-based laminates are used.
-
Flexible Substrates: Flexible PCBs utilize substrates like polyimide or polyester, allowing for bendable and conformable designs.
The Copper Layer
The copper layer is responsible for carrying electrical signals and power throughout the PCB. Copper is chosen for its excellent electrical conductivity and relatively low cost. The copper layer is typically applied to the substrate through a process called electroplating or lamination.
Copper Thickness
The thickness of the copper layer is measured in ounces per square foot (oz/ft²). Common copper thicknesses include:
Copper Weight | Thickness (mils) | Thickness (mm) |
---|---|---|
0.5 oz/ft² | 0.7 | 0.018 |
1 oz/ft² | 1.4 | 0.036 |
2 oz/ft² | 2.8 | 0.071 |
3 oz/ft² | 4.2 | 0.107 |
Thicker copper layers are used for high-current applications or to improve heat dissipation.
The Solder Mask Layer
The solder mask layer is a protective coating applied over the copper layer, leaving only the exposed pads and areas where components will be soldered. This layer serves several purposes:
-
Insulation: The solder mask prevents accidental short circuits by insulating the copper traces.
-
Protection: It protects the copper layer from oxidation and corrosion.
-
Aesthetics: Solder masks are available in various colors, with green being the most common, allowing for improved visual inspection and branding.
The Silkscreen Layer
The silkscreen layer is the topmost layer of a PCB, consisting of text, symbols, and logos printed on the solder mask. This layer is typically white but can be any color contrasting with the solder mask. The silkscreen layer provides important information such as:
-
Component Placement: It indicates the location and orientation of components.
-
Reference Designators: It labels components with their reference designators (e.g., R1, C2, U3).
-
Branding: It displays company logos, product names, and version numbers.
Multi-Layer PCBs
While single-layer PCBs are suitable for simple circuits, more complex designs often require multi-layer PCBs. These boards consist of multiple copper layers separated by insulating layers, allowing for higher component density and improved signal integrity.
Inner Layers
Inner layers are the copper layers sandwiched between the substrate and the outer layers. These layers are used for signal routing, power distribution, and ground planes. The number of inner layers varies depending on the complexity of the design, with common configurations ranging from 4 to 12 layers or more.
Prepreg and Core Materials
In multi-layer PCBs, the layers are bonded together using prepreg (pre-impregnated) and core materials.
-
Prepreg: Prepreg is a glass fabric pre-impregnated with a partially cured resin. It is used to bond the copper layers together during the lamination process.
-
Core: Core materials are fully cured laminates, similar to the substrate, used to provide additional structural support and insulation between layers.
Advanced PCB Materials
As technology advances and applications become more demanding, specialized PCB materials have been developed to meet specific requirements.
High-Temperature Materials
For applications exposed to elevated temperatures, such as automotive or aerospace electronics, high-temperature materials like polyimide or high-Tg FR-4 are used. These materials maintain their mechanical and electrical properties at temperatures exceeding 150°C.
Low-Loss Materials
In high-frequency applications, signal integrity is critical. Low-loss materials, such as Rogers or Teflon laminates, are used to minimize signal attenuation and distortion. These materials have a low dielectric constant and dissipation factor, ensuring minimal signal loss.
Thermally Conductive Materials
For applications requiring efficient heat dissipation, thermally conductive materials like metal core PCBs (MCPCBs) or thermally enhanced laminates are used. These materials help transfer heat away from components, preventing overheating and improving reliability.
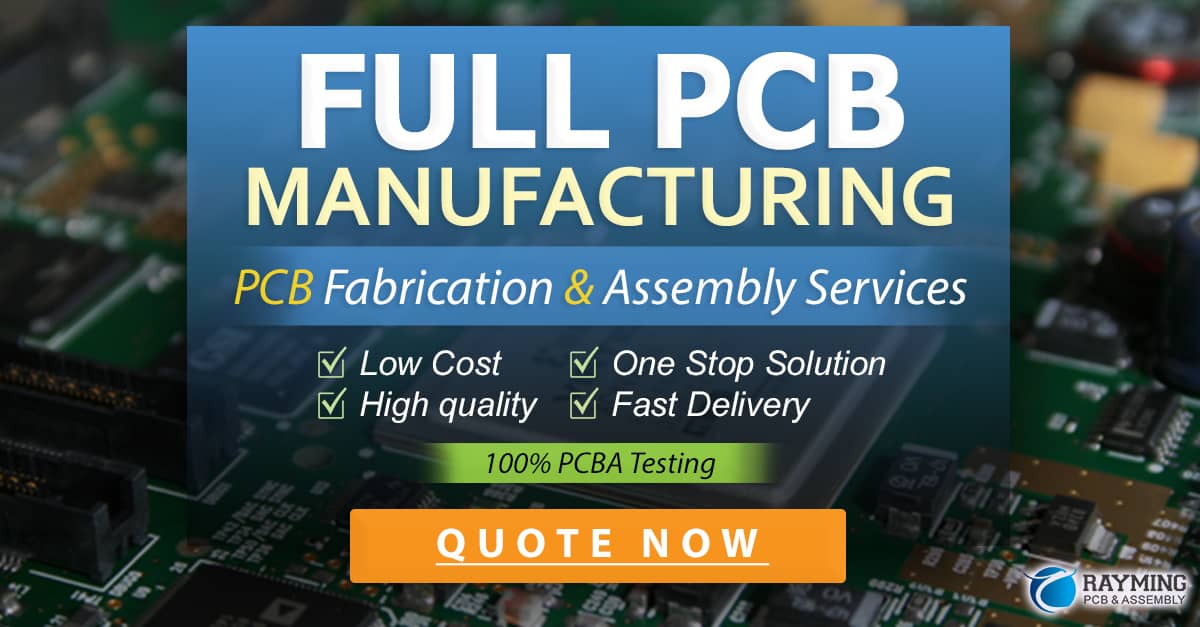
Frequently Asked Questions (FAQ)
- What is the most common substrate material used in PCBs?
-
FR-4, a glass-reinforced epoxy laminate, is the most widely used substrate material in PCBs due to its excellent mechanical and electrical properties, as well as its cost-effectiveness.
-
What is the purpose of the solder mask layer in a PCB?
-
The solder mask layer serves as a protective coating, insulating the copper traces to prevent short circuits, protecting the copper layer from oxidation and corrosion, and providing aesthetic benefits.
-
How is the copper layer thickness measured in PCBs?
-
The copper layer thickness is measured in ounces per square foot (oz/ft²). Common thicknesses include 0.5 oz/ft², 1 oz/ft², 2 oz/ft², and 3 oz/ft².
-
What are the benefits of using multi-layer PCBs?
-
Multi-layer PCBs allow for higher component density, improved signal integrity, and better power distribution compared to single-layer PCBs. They are suitable for complex designs requiring more extensive routing and shielding.
-
What materials are used for high-temperature PCB applications?
- For high-temperature applications, materials like polyimide or high-Tg FR-4 are used. These materials maintain their mechanical and electrical properties at temperatures exceeding 150°C, making them suitable for automotive, aerospace, and other demanding environments.
Conclusion
Understanding the composition of a PCB is crucial for designing, manufacturing, and troubleshooting electronic devices. The substrate, copper, solder mask, and silkscreen layers work together to create a functional and reliable platform for mounting and connecting components. As technology progresses, specialized materials like high-temperature, low-loss, and thermally conductive laminates are being developed to meet the ever-increasing demands of modern electronics.
By familiarizing yourself with the materials and layers that make up a PCB, you can make informed decisions when designing or selecting PCBs for your projects. Whether you are a hobbyist, an engineer, or a manufacturer, a solid understanding of PCB composition is essential for creating robust and efficient electronic devices.
0 Comments