Introduction to Multi-Layer PCBs
A Multi-Layer PCB, or Multi-Layer Printed Circuit Board, is a complex type of circuit board that consists of multiple layers of conductive copper foil laminated together with insulating material. These layers are interconnected through a series of drilled holes called vias, which allow electrical signals to pass from one layer to another. Multi-Layer PCBs are essential in modern electronics, as they enable the creation of highly dense and compact circuits with improved signal integrity and reduced electromagnetic interference (EMI).
Advantages of Multi-Layer PCBs
- Increased circuit density
- Improved signal integrity
- Reduced electromagnetic interference (EMI)
- Enhanced mechanical stability
- Smaller form factors
Layers in a Multi-Layer PCB
A typical Multi-Layer PCB consists of several different types of layers, each serving a specific purpose:
Signal Layers
Signal layers are the primary layers in a Multi-Layer PCB, responsible for carrying electrical signals between components. These layers are typically made of copper and are etched with the desired circuit pattern. The number of signal layers in a Multi-Layer PCB can vary depending on the complexity of the circuit and the desired functionality.
Power and Ground Planes
Power and ground planes are dedicated layers that provide a low-impedance path for power distribution and grounding. These planes help to minimize voltage drops, reduce noise, and improve overall signal integrity. By placing power and ground planes adjacent to signal layers, the PCB designer can also create a controlled impedance environment, which is essential for high-speed digital circuits.
Insulating Layers
Insulating layers, also known as dielectric layers, are placed between the conductive layers to provide electrical isolation and mechanical support. The most common insulating material used in Multi-Layer PCBs is FR-4, a glass-reinforced epoxy laminate. Other materials, such as polyimide or ceramic, may be used for high-frequency or high-temperature applications.
Manufacturing Process
The manufacturing process for Multi-Layer PCBs is more complex than that of single or double-layer boards. The basic steps involved in the production of a Multi-Layer PCB are as follows:
-
Layer Preparation: Each conductive layer is designed and printed onto a thin sheet of copper foil.
-
Lamination: The prepared layers are stacked together with insulating material between them and laminated under high pressure and temperature to form a solid board.
-
Drilling: Holes are drilled through the board to create vias and component mounting holes.
-
Plating: The drilled holes are plated with copper to establish electrical connections between layers.
-
Etching: The outer layers are etched to create the desired circuit pattern.
-
Solder Mask Application: A protective solder mask is applied to the outer layers to prevent short circuits and improve durability.
-
Silkscreen Printing: Component placement indicators, labels, and other markings are printed onto the board using silkscreen printing.
-
Surface Finishing: A surface finish, such as HASL (Hot Air Solder Leveling) or ENIG (Electroless Nickel Immersion Gold), is applied to the exposed copper to prevent oxidation and improve solderability.
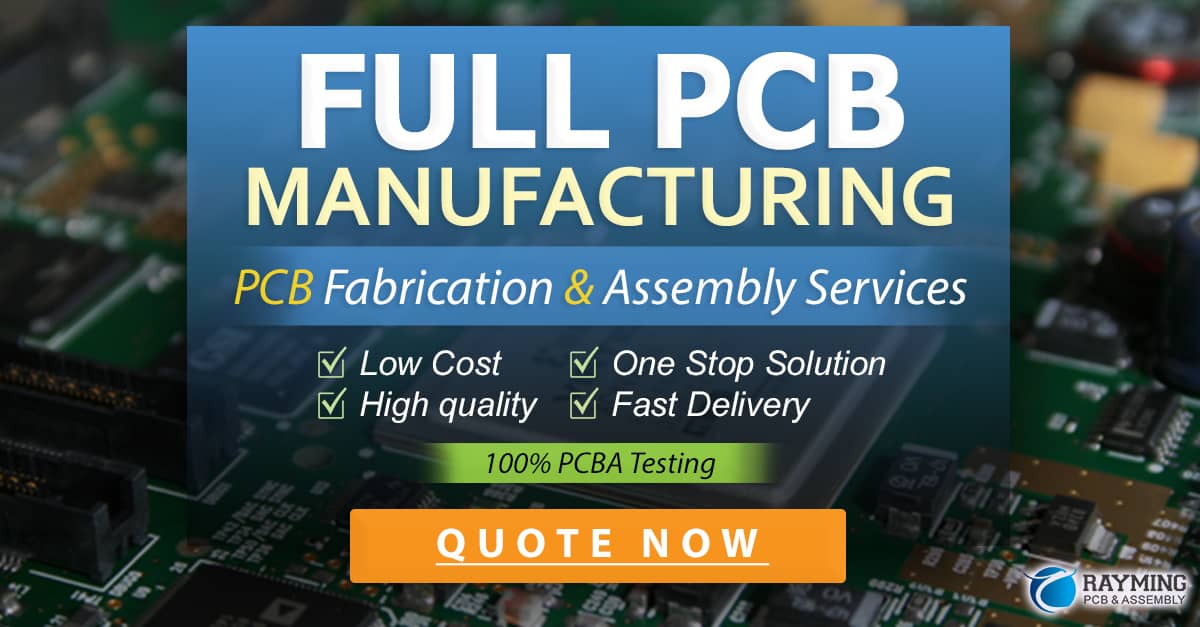
Design Considerations
When designing a Multi-Layer PCB, several factors must be taken into account to ensure optimal performance and manufacturability:
Layer Stack-up
The arrangement of layers in a Multi-Layer PCB, known as the layer stack-up, is a critical design consideration. The stack-up determines the overall thickness of the board, the impedance of the signal traces, and the EMI performance. A well-designed stack-up should have a symmetrical arrangement of layers to minimize warpage and ensure consistent impedance.
Via Types and Placement
Vias are an essential component of Multi-Layer PCBs, enabling interconnections between layers. There are several types of vias, each with its own advantages and limitations:
Via Type | Description | Advantages | Limitations |
---|---|---|---|
Through Hole Via | Drilled through the entire board | Strong mechanical connection | Consumes board space |
Blind Via | Drilled from an outer layer to an inner layer | Saves board space | Higher manufacturing cost |
Buried Via | Drilled between two inner layers | Saves board space | Higher manufacturing cost |
Microvias | Laser-drilled, typically less than 0.15mm in diameter | High density interconnects | Limited to connecting adjacent layers |
The placement of vias is also critical, as it can affect signal integrity and manufacturability. Vias should be placed as close to the source and destination points as possible to minimize the length of the signal path. However, placing vias too close together can lead to manufacturing issues, such as drill breakout or insufficient copper plating.
Controlled Impedance
Controlled impedance is a design technique used to maintain a consistent impedance along a signal trace, which is essential for high-speed digital circuits. By carefully selecting the width and spacing of the signal traces, as well as the properties of the insulating material, designers can create a controlled impedance environment that minimizes signal reflections and distortions.
Electromagnetic Compatibility (EMC)
Multi-Layer PCBs must be designed with EMC in mind to ensure that they do not interfere with other electronic devices and that they are not susceptible to external electromagnetic interference. Some key EMC design considerations include:
- Proper grounding and shielding
- Minimizing loop areas and trace lengths
- Using power and ground planes to provide a low-impedance return path
- Filtering power supplies and signals
- Placing components strategically to minimize crosstalk
Applications of Multi-Layer PCBs
Multi-Layer PCBs are used in a wide range of applications, from consumer electronics to aerospace and defense systems. Some common applications include:
Smartphones and Tablets
The compact and highly integrated nature of modern smartphones and tablets requires the use of Multi-Layer PCBs to accommodate the large number of components and functions in a small form factor. These devices often feature PCBs with 8 or more layers, enabling the integration of processors, memory, sensors, and wireless connectivity modules.
Automotive Electronics
As vehicles become increasingly reliant on electronic systems for safety, performance, and infotainment, Multi-Layer PCBs have become essential in automotive electronics. These boards must be designed to withstand harsh environmental conditions, such as extreme temperatures, vibrations, and moisture. Automotive Multi-Layer PCBs are used in applications such as engine control units, advanced driver assistance systems (ADAS), and in-vehicle infotainment systems.
Medical Devices
Medical devices, such as patient monitors, imaging systems, and implantable devices, require highly reliable and compact electronic circuits. Multi-Layer PCBs enable the creation of these complex systems in a small form factor, while also providing the necessary signal integrity and EMI protection. Medical Multi-Layer PCBs must also adhere to strict regulatory requirements, such as ISO 13485 and IEC 60601-1, to ensure patient safety and device performance.
Industrial Control Systems
Industrial control systems, such as programmable logic controllers (PLCs) and distributed control systems (DCS), rely on Multi-Layer PCBs to implement complex control algorithms and communicate with sensors and actuators. These boards must be designed to operate reliably in harsh industrial environments, withstanding factors such as extreme temperatures, vibrations, and electromagnetic interference.
Aerospace and Defense
Multi-Layer PCBs are used extensively in aerospace and defense applications, such as avionics systems, radar, and satellite communication equipment. These boards must be designed to meet stringent performance and reliability requirements, as well as withstand extreme environmental conditions. Aerospace and defense Multi-Layer PCBs often feature advanced materials, such as polyimide or ceramic, to ensure optimal performance in challenging environments.
Future Trends in Multi-Layer PCBs
As electronic systems continue to become more complex and compact, the demand for advanced Multi-Layer PCB technologies will continue to grow. Some key trends shaping the future of Multi-Layer PCBs include:
High Density Interconnect (HDI)
HDI PCBs feature smaller vias, finer trace widths, and tighter spacing, enabling even higher component density and improved signal integrity. These boards often incorporate microvias and blind/buried vias to maximize interconnect density.
Embedded Components
Embedding active and passive components within the layers of a Multi-Layer PCB can further increase circuit density and reduce the overall size of the board. Embedded components also offer improved signal integrity and reduced EMI, as the shorter interconnects minimize parasitic effects.
Advanced Materials
The development of advanced PCB materials, such as low-loss dielectrics and high-temperature laminates, will enable the creation of Multi-Layer PCBs for even more demanding applications. These materials will be essential for the development of 5G wireless networks, high-speed data centers, and advanced aerospace systems.
3D Printing
The emergence of 3D printing technologies for PCB fabrication could revolutionize the way Multi-Layer PCBs are designed and manufactured. 3D printing allows for the creation of complex, non-planar structures and the integration of embedded components, potentially leading to even more compact and highly integrated electronic systems.
Frequently Asked Questions (FAQ)
-
Q: What is the difference between a Multi-Layer PCB and a single or double-layer PCB?
A: Multi-Layer PCBs consist of three or more layers of conductive material, while single and double-layer PCBs have one or two layers, respectively. Multi-Layer PCBs offer higher circuit density, improved signal integrity, and reduced EMI compared to single or double-layer boards. -
Q: How many layers can a Multi-Layer PCB have?
A: The number of layers in a Multi-Layer PCB can vary depending on the complexity of the circuit and the application requirements. Common layer counts range from 4 to 12 layers, but some advanced PCBs may have 20 or more layers. -
Q: What materials are used in the construction of Multi-Layer PCBs?
A: The most common materials used in Multi-Layer PCBs are copper (for conductive layers) and FR-4 (for insulating layers). Other materials, such as polyimide, ceramic, or low-loss dielectrics, may be used for high-frequency or high-temperature applications. -
Q: What are the advantages of using blind and buried vias in Multi-Layer PCBs?
A: Blind and buried vias offer several advantages in Multi-Layer PCBs, including increased circuit density, improved signal integrity, and reduced EMI. These types of vias also allow for more efficient use of board space, as they do not consume real estate on all layers of the board. -
Q: How do I ensure proper signal integrity in a Multi-Layer PCB design?
A: To ensure proper signal integrity in a Multi-Layer PCB design, consider the following factors: use controlled impedance design techniques, minimize trace lengths and loop areas, use power and ground planes for low-impedance return paths, and carefully place components and route traces to minimize crosstalk and EMI. Additionally, work closely with your PCB manufacturer to ensure that your design is optimized for manufacturability and performance.
Conclusion
Multi-Layer PCBs are essential components in modern electronic systems, enabling the creation of highly dense, compact, and high-performance circuits. By understanding the structure, manufacturing process, and design considerations of Multi-Layer PCBs, engineers and designers can create innovative solutions for a wide range of applications, from consumer electronics to aerospace and defense systems.
As electronic systems continue to advance, the demand for more sophisticated Multi-Layer PCB technologies will only continue to grow. By staying up-to-date with the latest trends and best practices in Multi-Layer PCB design and manufacturing, engineers can ensure that they are well-positioned to meet the challenges of an increasingly connected and technology-driven world.
0 Comments