Introduction to PCB Stackup
A printed circuit board (PCB) stackup refers to the arrangement of copper and insulating layers that make up a PCB. The stackup defines the number of layers, their order, and the materials used in the fabrication process. A well-designed PCB stackup ensures proper functionality, signal integrity, and manufacturability of the circuit board.
Common PCB Stackups
PCBs can have various layer configurations, depending on the complexity and requirements of the electronic design. Some common PCB stackups include:
Layers | Description |
---|---|
1 | Single-sided PCB with components on one side |
2 | Double-sided PCB with components on both sides |
4 | Four-layer PCB with two internal layers for power and ground |
6 | Six-layer PCB with four internal layers for signal routing |
8+ | High-density PCBs with eight or more layers |
In this article, we will focus on the 4-layer PCB stackup, which is a popular choice for many electronic applications.
Anatomy of a 4-Layer PCB Stackup
A typical 4-layer PCB stackup consists of the following layers:
- Top Layer (Layer 1): Signal layer and component placement
- Inner Layer 1 (Layer 2): Ground plane
- Inner Layer 2 (Layer 3): Power plane
- Bottom Layer (Layer 4): Signal layer and component placement
Layer 1: Top Layer
The top layer is the outermost layer of the PCB and is primarily used for component placement and signal routing. It usually contains:
- Surface mount and through-hole components
- Signal traces
- Solder mask for protecting the copper traces
- Silkscreen for component labels and annotations
Layer 2: Ground Plane
The first inner layer, often referred to as the ground plane, is a solid copper layer connected to the ground of the circuit. The ground plane serves several purposes:
- Provides a low-impedance return path for currents
- Reduces electromagnetic interference (EMI) and crosstalk
- Acts as a heat sink for power dissipation
Layer 3: Power Plane
The second inner layer, known as the power plane, is a solid copper layer connected to the power supply of the circuit. The power plane offers several benefits:
- Distributes power evenly across the PCB
- Minimizes voltage drop and power supply noise
- Acts as a reference plane for controlled impedance traces
Layer 4: Bottom Layer
The bottom layer is similar to the top layer and is used for additional component placement and signal routing. It contains:
- Surface mount and through-hole components
- Signal traces
- Solder mask and silkscreen
Advantages of a 4-Layer PCB Stackup
Using a 4-layer PCB stackup offers several advantages over simpler 1-layer or 2-layer designs:
-
Improved Signal Integrity: The dedicated ground and power planes help minimize noise, crosstalk, and EMI, resulting in cleaner signals and better overall performance.
-
Increased Routing Density: With two additional layers for signal routing, designers can accommodate more components and traces in a smaller area, enabling more compact designs.
-
Better Power Distribution: The power plane ensures an even distribution of power across the PCB, reducing voltage drop and improving power supply stability.
-
Enhanced Thermal Management: The inner layers act as heat sinks, dissipating heat generated by components more efficiently than in 1-layer or 2-layer designs.
-
Reduced EMI: The ground plane helps shield the signals from external electromagnetic interference, making the design more robust and less susceptible to noise.
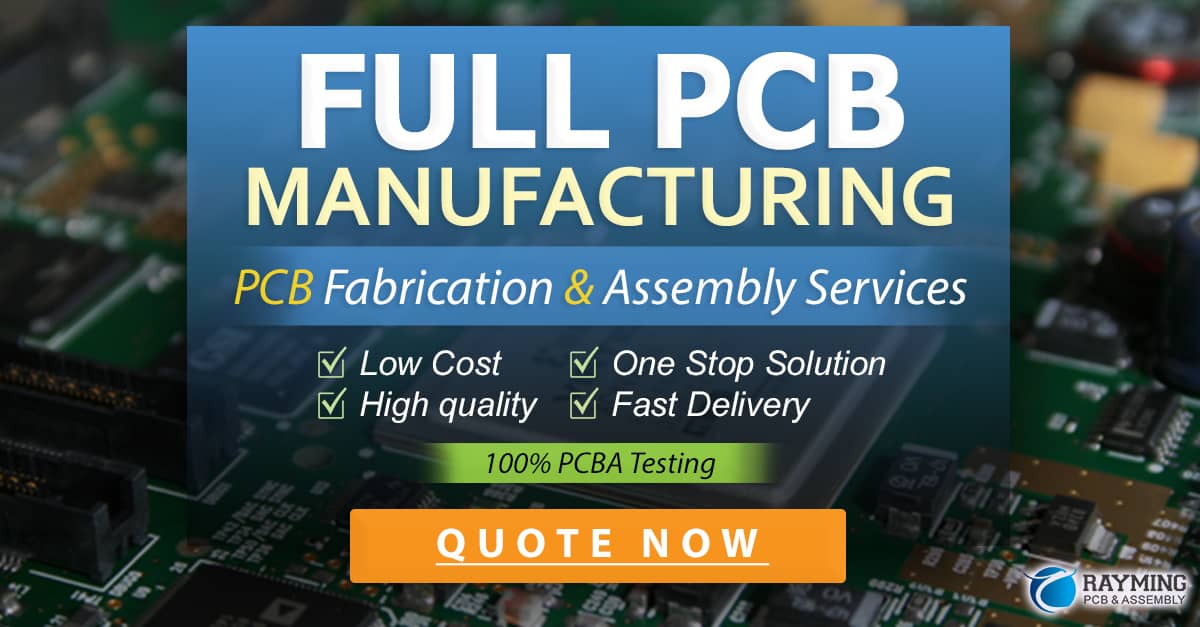
Designing a 4-Layer PCB Stackup
When designing a 4-layer PCB stackup, several factors must be considered to ensure optimal performance and manufacturability:
Material Selection
Choose the appropriate PCB substrate material based on the application requirements, such as:
- FR-4: Most common, cost-effective, and suitable for general-purpose designs
- High-Tg FR-4: Better thermal stability and suitable for high-temperature applications
- Rogers: Low-loss materials for high-frequency and RF applications
- Polyimide: Flexible substrates for flexible and rigid-flex PCBs
Layer Thickness
Specify the thickness of each layer in the stackup, considering:
- Copper weight: Typically measured in ounces per square foot (oz/ft²), with common values being 0.5 oz, 1 oz, and 2 oz
- Dielectric thickness: The thickness of the insulating material between layers, affecting the PCB’s overall thickness and impedance control
Impedance Control
For high-speed designs, control the characteristic impedance of the traces by:
- Adjusting trace width and spacing
- Selecting appropriate dielectric materials
- Specifying the proper dielectric thickness between layers
Via Management
Optimize via placement and design to minimize signal integrity issues:
- Use blind and buried vias to reduce the number of through-hole vias
- Minimize via stub length to reduce reflections and signal distortion
- Implement via stitching for better power and ground plane connections
Manufacturing Considerations
When manufacturing a 4-layer PCB, keep the following considerations in mind:
-
Design for Manufacturability (DFM): Adhere to the fabrication house’s design guidelines for minimum trace widths, spacing, drill sizes, and annular rings to ensure successful manufacturing.
-
Panelization: Group multiple PCBs into a single panel to optimize fabrication efficiency and reduce costs.
-
Solder Mask and Silkscreen: Specify the color and finish of the solder mask and silkscreen to enhance the PCB’s appearance and protect the copper traces.
-
Testing and Inspection: Perform necessary tests and inspections, such as electrical testing, visual inspection, and X-ray inspection, to ensure the quality and reliability of the manufactured PCBs.
Frequently Asked Questions (FAQ)
-
Q: What is the difference between a 2-layer and a 4-layer PCB stackup?
A: A 2-layer PCB has only two layers of copper (top and bottom), while a 4-layer PCB has four layers (top, inner layer 1, inner layer 2, and bottom). The additional inner layers in a 4-layer PCB are typically used for power and ground planes, improving signal integrity and power distribution. -
Q: When should I choose a 4-layer PCB over a 2-layer PCB?
A: Consider using a 4-layer PCB when your design requires better signal integrity, improved power distribution, higher component density, or enhanced thermal management. 4-layer PCBs are suitable for more complex designs with higher speeds, analog signals, or mixed-signal circuits. -
Q: Can I have more than two signal layers in a 4-layer PCB stackup?
A: Yes, it is possible to have more than two signal layers in a 4-layer PCB by using the inner layers for signal routing instead of power and ground planes. However, this approach may compromise signal integrity and power distribution, so it is generally recommended to use the inner layers for power and ground in a 4-layer stackup. -
Q: How does the choice of dielectric material affect the performance of a 4-layer PCB?
A: The dielectric material’s properties, such as dielectric constant (Dk) and dissipation factor (Df), influence the PCB’s performance. Low-loss materials with a stable Dk and low Df are preferred for high-speed and high-frequency applications to minimize signal loss and distortion. -
Q: Are 4-layer PCBs more expensive than 2-layer PCBs?
A: Yes, 4-layer PCBs are generally more expensive than 2-layer PCBs due to the additional materials, processing steps, and complexity involved in fabrication. However, the improved performance and functionality offered by a 4-layer stackup often justify the increased cost for many applications.
Conclusion
A 4-layer PCB stackup is a versatile and widely used configuration that offers numerous benefits over simpler 1-layer and 2-layer designs. By incorporating dedicated power and ground planes, a 4-layer stackup improves signal integrity, power distribution, and thermal management while enabling higher component density and more compact designs.
When designing a 4-layer PCB, it is essential to consider factors such as material selection, layer thickness, impedance control, and via management to ensure optimal performance and manufacturability. By adhering to best practices and collaborating with experienced PCB fabrication houses, designers can successfully create high-quality 4-layer PCBs for a wide range of electronic applications.
0 Comments