Types of PCB Assembly Problems
PCB assembly problems generally fall into a few main categories:
Soldering Defects
Soldering is one of the most critical steps in PCB assembly. Common soldering defects include:
Defect | Description |
---|---|
Bridging | Solder accidentally connects adjacent pins/pads |
Insufficent solder | Not enough solder forms a weak connection |
Excess solder | Too much solder can cause short circuits |
Cold solder joint | Solder did not melt completely, forms a weak “cold” joint |
Tombstoning | Component stands up on end due to uneven soldering |
Component Issues
Problems with the components being assembled onto the PCB include:
Issue | Description |
---|---|
Wrong component | Incorrect component used by mistake |
Misaligned component | Component placed incorrectly |
Damaged component | Component damaged before or during assembly |
Counterfeit component | Fake/counterfeit component used |
Obsolete component | Component no longer manufactured |
PCB Defects
Issues with the bare PCB itself before assembly include:
Defect | Description |
---|---|
Broken traces | Wiring traces damaged or disconnected |
Contamination | Foreign material on PCB surface |
Warping/twisting | PCB not flat due to moisture, overheating, etc. |
Wrong hole size | Drilled holes too big/small for component leads |
Burn marks | PCB damaged by soldering iron, rework, etc. |
PCB Design Problems to Avoid
Many PCB assembly problems can be prevented by optimizing the PCB design. PCB designers should avoid:
Overly Small Components
While miniaturization allows fitting more functionality in a smaller space, using very tiny chip components can make assembly more difficult. 0201 size and smaller chip resistors and capacitors are hard to place and solder consistently. Larger 0402, 0603, and 0805 sizes are preferred.
Excessive Vias
Vias are necessary to route traces between layers on a PCB. However, too many vias, especially buried/blind vias, make fabrication and assembly more challenging and expensive. The design should optimize and minimize use of vias.
Incompatible Materials
The PCB substrate material, soldermask, silkscreen, and component finishes must all be compatible. For example, lead-free HASL PCB finish is not compatible with tin-lead solder paste. Material compatibility issues can cause solderability and reliability problems.
Inadequate Spacing
Components must have sufficient spacing between their pads, pins, and neighboring components to prevent bridging and short circuits. PCB layout tools have design rule checks (DRC) to verify adequate spacing is maintained.
Unroutable Traces
If the PCB contains too many traces in tight spaces, some connections may be “unroutable” with traces overlapping or violating spacing rules. This requires the designer to reduce component density, use more layers, or resize the board to fit all routes.
Equipment Problems in PCB Assembly
Automated equipment is extensively used in PCB assembly. Problems can occur with the machines and tooling:
Stencil Printer Issues
Problem | Description |
---|---|
Clogged apertures | Stencil apertures blocked by solder paste |
Damaged stencil | Stencil deformed or worn |
Inconsistent print | Uneven solder paste deposit |
Pick-and-Place Defects
Problem | Description |
---|---|
Missed component | Machine failed to pick up/place component |
Skewed placement | Component placed crookedly |
Wrong component | Feeders loaded with incorrect component |
Reflow Oven Troubles
Problem | Description |
---|---|
Incorrect profile | Heating ramp rate/duration not optimal for solder paste |
Cold solder joint | Reflow temperature too low to fully melt solder |
Overheated PCB | Excessive temperature damages components or PCB |
Automated Optical Inspection Faults
Problem | Description |
---|---|
False failure | Good PCB/solder joint flagged as defect |
False pass | Defective PCB passes inspection |
Occlusion | Components block camera view of solder joints |
Frequent calibration, maintenance, and replenishment of solder paste and components is necessary to keep the automated assembly equipment running optimally. Manufacturers must also regularly train equipment operators to follow proper procedures.
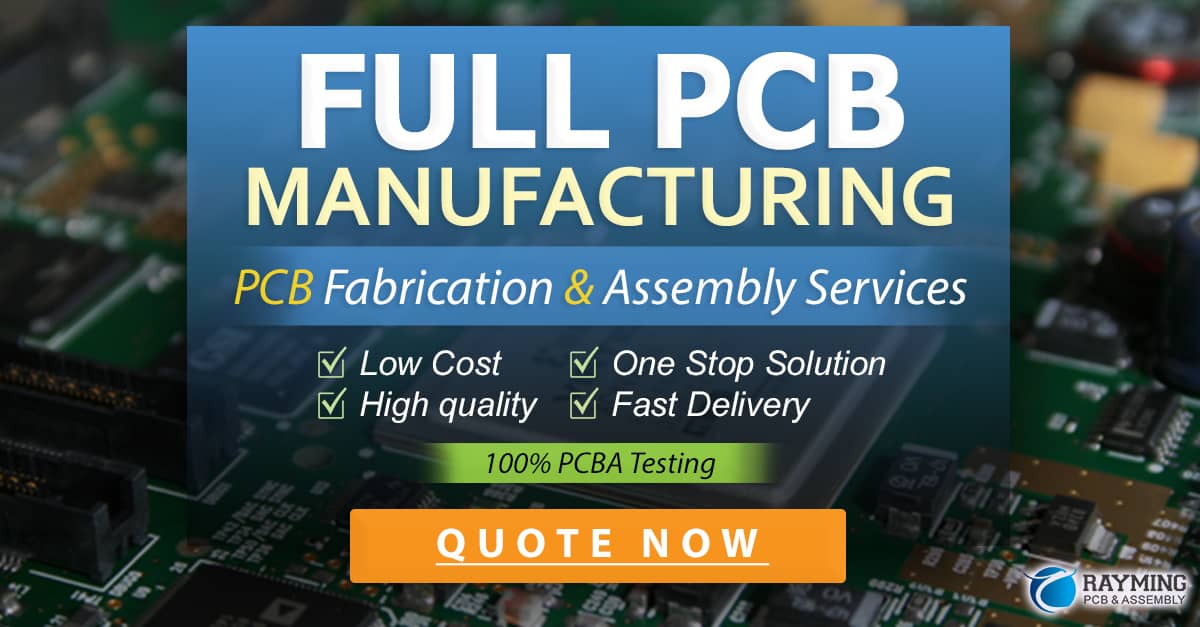
Preventing PCB Rework
A major cause of problems is the need to rework assembled PCBs to fix defects. Rework is time-consuming, expensive, and can potentially damage the PCB. It’s best to prevent defects in the first place vs. repairing them after the fact.
Steps to minimize PCB rework include:
-
Careful Design Review – Thoroughly review PCB design to identify any issues before fabrication. Use DRC and design for manufacturability (DFM) checks.
-
Optimize Manufacturing Process – Select appropriate materials, equipment, and process parameters for reliable assembly. Use best practices for stencil printing, component placement, and reflow soldering.
-
Automated Inspection – Implement automated solder paste inspection (SPI), automated optical inspection (AOI), and X-ray inspection to catch defects early before they require rework.
-
Quality Control – Perform regular quality audits and track key metrics like defects per million (DPMO) opportunities and first pass yield (FPY). Identify and correct root causes of recurring defects.
-
Continuous Improvement – Strive for ongoing improvement of the PCB assembly process. Conduct post-build reviews to gather lessons learned. Invest in training, upgraded equipment, and enhanced techniques over time.
Common Causes of PCB Failure
Even carefully assembled PCBs can encounter failures in the field. Common causes include:
Environmental Stress
Stress | Example |
---|---|
Vibration | Cracks, broken solder joints in high-vibration environment |
Temperature extremes | Component damage, PCB delamination from thermal cycling |
Humidity | Corrosion, electromigration, dendritic growth with moisture |
Power Problems
Problem | Example |
---|---|
Overvoltage | Applying too high voltage damages components |
Reverse polarity | Connecting power backwards damages polarized parts |
ESD | ElectroStatic Discharge shock damages sensitive ICs |
Misuse
Problem | Example |
---|---|
Overloading | Drawing too much current through PCB traces |
Physical damage | PCB cracked or punctured by impact or flexing |
Improper installation | Wrong connections, missing fasteners, poor heatsinking |
Anticipating and guarding against these common failure modes during the design phase is key to enhancing the reliability of the final product. Thorough testing and burn-in can also help identify and weed out potential defects before the product is shipped.
FAQ
Q: What is the most common soldering defect in PCB assembly?
A: Bridging is one of the most frequent soldering defects, where solder inadvertently connects adjacent pins, pads, or traces causing a short circuit. Bridging is often due to applying too much solder paste, poor stencil design, or incorrect reflow temperature profile.
Q: How can PCB manufacturing problems be prevented?
A: PCB manufacturing problems can be minimized by carefully reviewing the PCB design for manufacturability before fabrication. Use design rule checks (DRC) and design for manufacturing (DFM) analysis to identify any issues with trace spacing, drill sizes, annular rings, solder mask, etc. Consulting with the PCB fabricator can also help identify any potential manufacturing challenges early.
Q: What are some common problems with reflow soldering?
A: Typical reflow soldering issues include cold solder joints (solder did not fully melt), tombstoning (chip components standing up on one end), solder beading (balls of solder on surface), and popcorning (moisture damage to components). These can be caused by incorrect reflow temperature profile, contamination, or component quality issues.
Q: How do environmental factors impact PCB reliability?
A: Environmental stresses like vibration, mechanical shock, large temperature swings, and high humidity can all degrade PCB reliability over time. Solder joints may crack, components may come loose, and metallic structures may corrode or grow conductive anodic filaments. Designing the PCB and enclosure to withstand the expected environment is critical for long-term reliability.
Q: What are some of the latest technologies to improve automated PCB assembly?
A: Recent innovations in automated PCB assembly include higher resolution solder paste printers, faster and more precise pick-and-place machines, multi-zone reflow ovens with better thermal control, and 3D automated optical inspection (AOI) and X-ray systems. There is also increased use of robotics, automated material handling, and machine learning algorithms to optimize the assembly process.
0 Comments