What is Solder Mask?
Solder mask, also known as solder resist or solder stop mask, is a thin layer of polymer that is applied to the copper traces of a PCB. Its primary purpose is to protect the copper traces from oxidation, prevent solder bridges from forming between closely spaced pads, and provide electrical insulation.
Solder mask is typically applied to both sides of the PCB using a silkscreen printing process or photoimaging technique. The most common colors for solder mask are green, red, blue, and black, although other colors are available for specific applications.
Functions of Solder Mask
-
Insulation: Solder mask acts as an insulating layer, preventing short circuits and protecting the copper traces from environmental factors such as moisture and dust.
-
Solder Control: By covering the copper traces, solder mask prevents solder from adhering to areas where it’s not needed, ensuring that solder only flows onto the exposed pads and component leads.
-
Corrosion Protection: Solder mask shields the copper traces from oxidation and corrosion, extending the lifespan of the PCB.
-
Aesthetics: Solder mask gives the PCB a clean, professional appearance and can be used to display text, logos, or other markings.
What is Solder Paste Mask?
Solder paste mask, also referred to as a stencil or solder paste stencil, is a thin sheet of stainless steel or polyimide with openings that correspond to the pads on a PCB. It is used to apply solder paste onto the pads before component placement in the surface mount technology (SMT) assembly process.
Solder paste is a mixture of tiny solder particles suspended in a flux medium. When applied to the pads through the solder paste mask, it creates a temporary adhesive that holds the components in place until the solder melts during the reflow soldering process.
Functions of Solder Paste Mask
-
Precise Solder Paste Application: The solder paste mask ensures that the correct amount of solder paste is deposited onto each pad, which is crucial for forming reliable solder joints.
-
Consistent Solder Paste Height: By controlling the thickness of the solder paste mask, the height of the solder paste deposit can be kept consistent across the entire PCB.
-
Prevents Solder Bridging: The solder paste mask helps prevent solder paste from spreading to adjacent pads, minimizing the risk of solder bridges forming during the reflow process.
-
Enables High-Density Layouts: Solder Paste Masks allow for the precise application of solder paste on small, closely spaced pads, enabling the assembly of high-density PCB designs.
Differences between Solder Mask and Paste Mask
Now that we’ve covered the basics of solder mask and paste mask, let’s summarize the key differences between the two:
Feature | Solder Mask | Solder Paste Mask |
---|---|---|
Purpose | Insulation, protection, and solder control | Precise solder paste application |
Material | Polymer (ink or film) | Stainless steel or polyimide |
Application Method | Silkscreen printing or photoimaging | Stencil printing |
Stage in PCB Production | Applied after copper etching, before assembly | Used during SMT assembly process |
Permanent or Temporary | Permanent part of the finished PCB | Temporary, removed after solder paste application |
Solder Mask Application Process
The solder mask application process typically involves the following steps:
-
Cleaning: The bare PCB is cleaned to remove any contaminants or debris that may affect the adhesion of the solder mask.
-
Solder Mask Application: The solder mask is applied to the PCB using either silkscreen printing or photoimaging techniques. In silkscreen printing, the solder mask ink is pushed through a fine mesh screen onto the PCB surface. In photoimaging, a photosensitive solder mask film is laminated onto the PCB, exposed to UV light through a photomask, and developed to create the desired pattern.
-
Curing: After application, the solder mask is cured using heat or UV light to harden and permanently bond it to the PCB surface.
-
Inspection: The PCB is inspected to ensure that the solder mask has been applied correctly, with no defects or inconsistencies.
Solder Paste Mask Application Process
The solder paste mask application process involves the following steps:
-
Alignment: The solder paste mask is aligned with the pads on the PCB using fiducial markers or machine vision systems.
-
Solder Paste Application: Solder paste is applied to the PCB through the openings in the solder paste mask using a squeegee or automated paste dispenser. The amount of solder paste deposited is controlled by the thickness of the mask and the size of the openings.
-
Inspection: After solder paste application, the PCB is inspected using automated optical inspection (AOI) systems to ensure that the solder paste has been deposited correctly and consistently.
-
Component Placement: Once the solder paste has been applied, the components are placed onto the pads using pick-and-place machines or manual assembly techniques.
-
Reflow Soldering: The PCB is then subjected to a reflow soldering process, where it is heated to melt the solder paste and form permanent solder joints between the components and the pads.
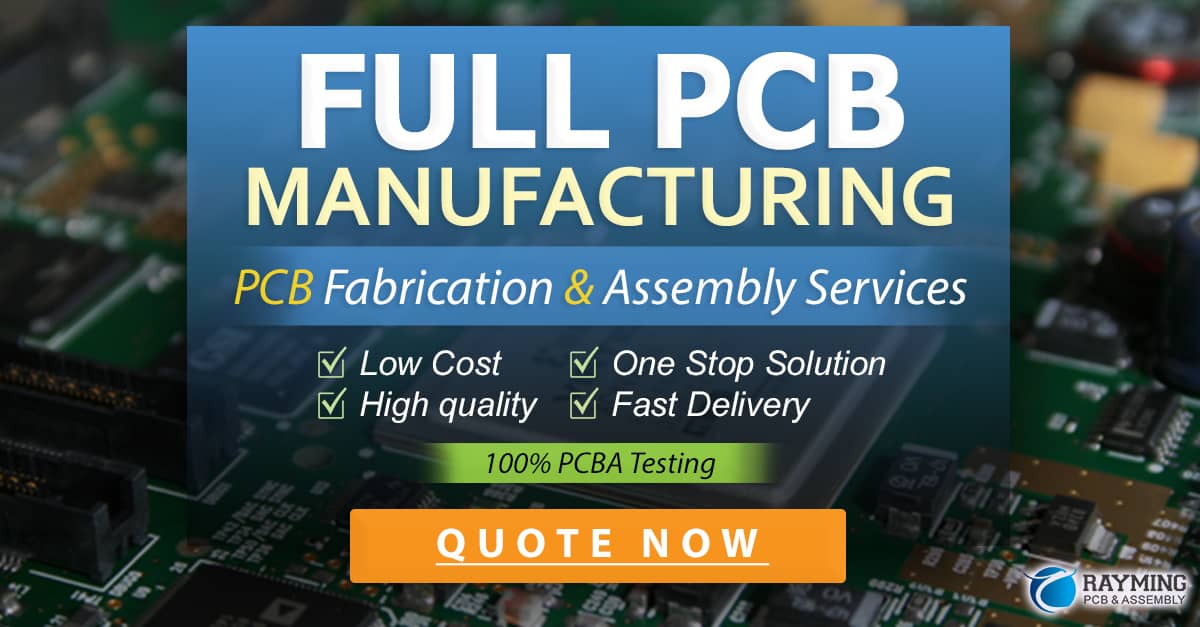
Choosing the Right Solder Mask and Paste Mask
When designing and manufacturing a PCB, it’s essential to choose the appropriate solder mask and paste mask to ensure reliable performance and manufacturability. Here are some factors to consider:
Solder Mask Selection
-
Material Properties: Consider the electrical, mechanical, and thermal properties of the solder mask material, such as dielectric strength, flexibility, and temperature resistance.
-
Color: Choose a solder mask color that provides good contrast with the silkscreen markings and component colors for ease of assembly and inspection.
-
Thickness: Select a solder mask thickness that provides adequate insulation and protection without compromising the solderable area of the pads.
-
Compatibility: Ensure that the solder mask is compatible with the PCB fabrication process and the intended application environment.
Solder Paste Mask Selection
-
Material: Choose between stainless steel or polyimide solder paste masks based on the required durability, cost, and performance.
-
Thickness: Select a solder paste mask thickness that deposits the appropriate amount of solder paste for the component types and sizes used in the design.
-
Aperture Size: Ensure that the solder paste mask apertures are sized correctly to accommodate the pad dimensions and provide sufficient solder paste coverage.
-
Compatibility: Verify that the solder paste mask is compatible with the solder paste chemistry and the reflow soldering process parameters.
Frequently Asked Questions (FAQ)
-
Can solder mask be applied selectively to specific areas of the PCB?
Yes, solder mask can be selectively applied to specific areas of the PCB using a process called selective masking. This involves using a separate mask or stencil to apply solder mask only to the desired areas, leaving other areas exposed. -
What is the typical thickness of a solder paste mask?
The typical thickness of a solder paste mask ranges from 0.1 mm to 0.2 mm (4 to 8 mils), depending on the component sizes and solder paste requirements. Thicker masks are used for larger components or higher solder paste volumes, while thinner masks are used for finer pitch components or lower solder paste volumes. -
How does solder mask affect the impedance of PCB traces?
Solder mask can affect the impedance of PCB traces by altering the dielectric constant of the substrate and changing the effective width of the traces. When designing high-speed or impedance-controlled PCBs, it’s important to consider the effects of solder mask and adjust the trace dimensions accordingly to maintain the desired impedance. -
Can solder paste masks be reused?
Solder paste masks can be reused multiple times, depending on their material and condition. Stainless steel masks are more durable and can be cleaned and reused many times, while polyimide masks have a limited lifespan and may need to be replaced more frequently. It’s important to inspect the solder paste mask for damage or wear before each use to ensure consistent solder paste application. -
What is the difference between liquid photoimageable (LPI) and dry film solder masks?
Liquid photoimageable (LPI) solder masks are applied as a liquid ink and then exposed and developed using photoimaging techniques, while dry film solder masks are applied as a solid film that is laminated onto the PCB surface. LPI solder masks offer higher resolution and finer feature definition, while dry film solder masks are faster to apply and provide better conformity to surface irregularities. The choice between LPI and dry film solder masks depends on the specific requirements of the PCB design and manufacturing process.
Conclusion
Understanding the differences between solder mask and paste mask is crucial for designing and manufacturing reliable, high-quality PCBs. Solder mask provides insulation, protection, and solder control for the copper traces, while solder paste mask enables precise application of solder paste for SMT assembly.
By selecting the appropriate solder mask and paste mask materials, thicknesses, and aperture sizes, PCB designers and manufacturers can ensure optimal performance and manufacturability of their boards. As PCB technology continues to advance, staying up-to-date with the latest developments in solder mask and paste mask materials and processes will be essential for staying competitive in the industry.
0 Comments