Introduction to Prototype PCB Manufacturing
Prototype PCB (Printed Circuit Board) manufacturing is a crucial step in the development of electronic devices and systems. It involves creating a small batch of PCBs for testing and validation purposes before moving to full-scale production. Prototype PCBs allow engineers and designers to evaluate the functionality, performance, and reliability of their designs in real-world conditions.
What is a Prototype PCB?
A prototype PCB is a printed circuit board that is manufactured in small quantities for testing and validation purposes. It is used to verify the design, functionality, and performance of an electronic circuit before mass production. Prototype PCBs are typically made using the same materials and processes as the final production boards, but with some modifications to reduce cost and lead time.
Why is Prototype PCB Manufacturing Important?
Prototype PCB manufacturing is important for several reasons:
-
Design Verification: Prototype PCBs allow engineers to verify that their design works as intended. They can test the functionality, performance, and reliability of the circuit in real-world conditions and make necessary modifications before moving to full-scale production.
-
Cost Savings: Prototype PCBs can help identify design flaws and issues early in the development process, saving time and money in the long run. By catching and fixing problems early, companies can avoid costly redesigns and delays in production.
-
Faster Time-to-Market: Prototype PCBs allow companies to quickly test and validate their designs, enabling them to bring their products to market faster. This is especially important in today’s fast-paced and competitive business environment.
-
Improved Quality: Prototype PCBs can help identify and address quality issues early in the development process. By testing and validating the design, engineers can ensure that the final product meets the required quality standards.
Benefits of Prototype PCB Manufacturing
Prototype PCB manufacturing offers several benefits to companies and engineers. Some of the key benefits include:
1. Quick Turnaround Time
One of the main benefits of prototype PCB manufacturing is the quick turnaround time. Unlike full-scale production, which can take weeks or even months, prototype PCBs can be manufactured in a matter of days. This allows engineers to quickly test and validate their designs, making necessary modifications and improvements along the way.
2. Cost-Effective
Prototype PCB manufacturing is also cost-effective compared to full-scale production. Since prototype PCBs are manufactured in small quantities, the setup and tooling costs are lower. This makes it more affordable for companies to test and validate their designs before investing in large-scale production.
3. Flexibility in Design Changes
Prototype PCB manufacturing allows for greater flexibility in design changes. Engineers can make modifications and improvements to their designs based on the results of testing and validation. This iterative process helps ensure that the final product meets the required specifications and performance criteria.
4. Improved Reliability
Prototype PCB manufacturing can also help improve the reliability of the final product. By testing and validating the design in real-world conditions, engineers can identify and address potential issues before they become major problems. This can help reduce the risk of product failures and recalls, improving overall reliability and customer satisfaction.
5. Faster Time-to-Market
Prototype PCB manufacturing can help companies bring their products to market faster. By quickly testing and validating their designs, companies can move to full-scale production more quickly. This can give them a competitive advantage in today’s fast-paced business environment.
Prototype PCB Manufacturing Process
The prototype PCB manufacturing process typically involves the following steps:
-
Design: The first step in the process is to create a design for the PCB. This is usually done using specialized software such as Altium Designer, Eagle, or KiCad.
-
Fabrication: Once the design is complete, the next step is to fabricate the PCB. This involves creating a copper pattern on a substrate material, typically fiberglass or FR4. The copper pattern is created using a process called etching, which removes unwanted copper from the substrate.
-
Drilling: After the copper pattern is created, holes are drilled into the PCB to allow for the placement of components. The holes are typically drilled using a computer-controlled drill machine.
-
Plating: The holes are then plated with a conductive material, typically copper, to ensure good electrical contact between the layers of the PCB.
-
Soldermask and Silkscreen: A soldermask layer is applied to the PCB to protect the copper traces from oxidation and to prevent solder from bridging between adjacent traces. A silkscreen layer is also applied to the PCB to add text and symbols for easy identification of components.
-
Assembly: Finally, the components are placed on the PCB and soldered in place. This can be done manually or using automated assembly machines.
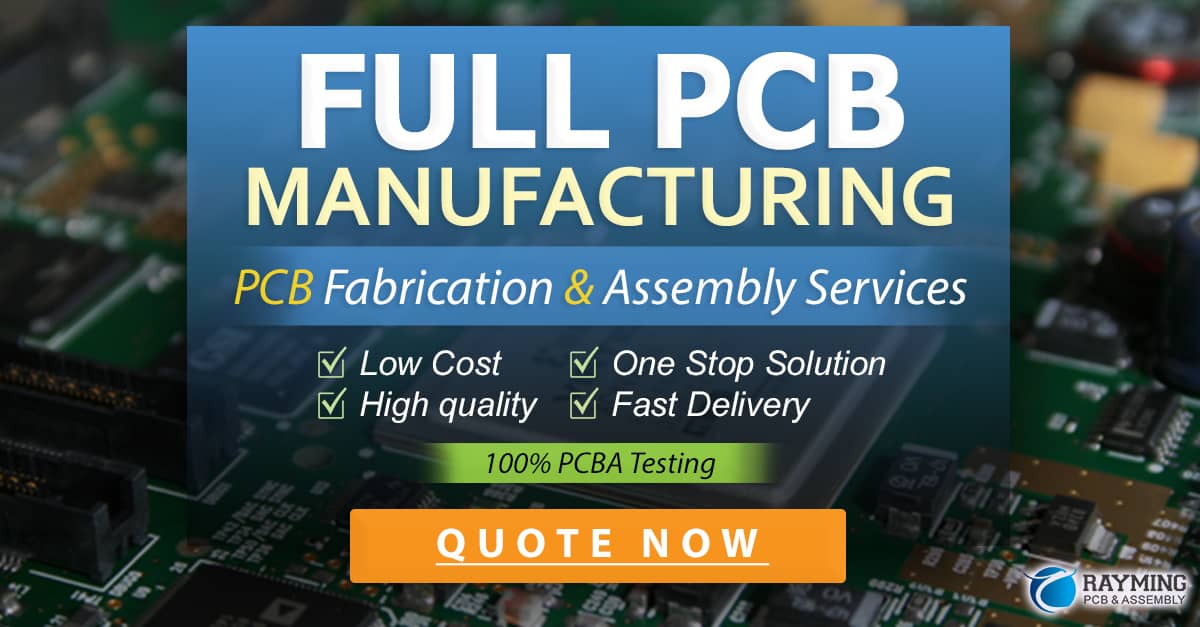
Choosing a Prototype PCB Manufacturer
When choosing a prototype PCB manufacturer, there are several factors to consider:
1. Experience and Expertise
It is important to choose a manufacturer with experience and expertise in prototype PCB manufacturing. Look for a manufacturer with a proven track record of delivering high-quality PCBs on time and within budget.
2. Technology and Equipment
Choose a manufacturer with state-of-the-art technology and equipment. This will ensure that your PCBs are manufactured to the highest quality standards and with the latest manufacturing techniques.
3. Turnaround Time
Turnaround time is a critical factor in prototype PCB manufacturing. Look for a manufacturer that can deliver your PCBs quickly without sacrificing quality.
4. Customer Support
Choose a manufacturer with excellent customer support. Look for a manufacturer that is responsive to your needs and can provide technical support when needed.
5. Price
Price is also an important factor to consider when choosing a prototype PCB manufacturer. Look for a manufacturer that offers competitive pricing without sacrificing quality.
Frequently Asked Questions (FAQ)
1. What is the typical turnaround time for prototype PCBs?
The typical turnaround time for prototype PCBs is 1-5 days, depending on the complexity of the design and the manufacturer’s capabilities.
2. What is the minimum order quantity for prototype PCBs?
The minimum order quantity for prototype PCBs varies by manufacturer, but it is typically lower than for full-scale production. Some manufacturers offer low minimum order quantities, such as 1-5 pieces, while others may require a minimum of 10-20 pieces.
3. What is the cost of prototype PCBs compared to full-scale production?
The cost of prototype PCBs is typically higher than for full-scale production on a per-unit basis, due to the lower volume and higher setup costs. However, the overall cost of prototype PCBs is usually lower than for full-scale production, since fewer boards are produced.
4. What design files are needed for prototype PCB manufacturing?
The design files needed for prototype PCB manufacturing typically include Gerber files, drill files, and a bill of materials (BOM). Some manufacturers may also require additional files, such as pick-and-place files or assembly drawings.
5. Can I make changes to my design after ordering prototype PCBs?
Yes, it is possible to make changes to your design after ordering prototype PCBs, but it may incur additional costs and delays. It is best to thoroughly review and test your design before ordering prototype PCBs to minimize the need for changes.
Conclusion
Prototype PCB manufacturing is a crucial step in the development of electronic devices and systems. It allows engineers and designers to test and validate their designs in real-world conditions before moving to full-scale production. Prototype PCBs offer several benefits, including quick turnaround time, cost-effectiveness, flexibility in design changes, improved reliability, and faster time-to-market.
When choosing a prototype PCB manufacturer, it is important to consider factors such as experience and expertise, technology and equipment, turnaround time, customer support, and price. By selecting the right manufacturer and following best practices for prototype PCB manufacturing, companies can bring their products to market faster, with higher quality and reliability.
0 Comments