How Mid-Chip Solder Balls Work
Mid-chip solder balls are typically arranged in an array pattern on the active side of the semiconductor chip. The solder balls are deposited onto the chip’s bond pads, which are the metal connection points that link the chip’s circuitry to the outside world. The bond pads have a metallization stack that is compatible with the solder material, usually consisting of layers such as copper, nickel, and gold.
During the flip chip assembly process, the chip with the mid-chip solder balls is flipped over and aligned with the corresponding bond pads on the substrate or package. The assembly is then subjected to a reflow process, where the solder balls are heated above their melting point. The molten solder wets the bond pads on both the chip and substrate, forming a metallurgical bond as it cools and solidifies. This creates a strong mechanical and electrical connection between the chip and substrate.
Advantages of Mid-Chip Solder Balls
Mid-chip solder balls offer several advantages over traditional wire bonding:
-
Higher I/O density: Mid-chip solder balls enable a much higher input/output (I/O) density compared to wire bonding. The solder balls can be arranged in a dense array, allowing for hundreds or thousands of connections in a small area.
-
Improved electrical performance: The short and direct path provided by mid-chip solder balls reduces inductance and resistance, enabling faster signal transmission and lower power consumption.
-
Better thermal management: The flip chip configuration facilitated by mid-chip solder balls allows for better heat dissipation from the chip to the substrate or package.
-
Smaller form factor: By eliminating the need for wire loops, mid-chip solder balls enable a smaller package size and a lower profile.
-
Enhanced reliability: Mid-chip solder balls provide a more robust mechanical connection compared to wire bonds, improving the package’s resistance to shock, vibration, and thermal stress.
Challenges and Considerations
While mid-chip solder balls offer numerous benefits, there are also some challenges and considerations associated with their use:
-
Coefficient of thermal expansion (CTE) mismatch: The CTE difference between the chip and substrate can lead to thermal stress and strain on the solder joints during temperature cycling. This can cause solder joint fatigue and reliability issues.
-
Underfill material: To mitigate the CTE mismatch and improve reliability, an underfill material is often used to fill the gap between the chip and substrate. The underfill helps distribute the stress and protects the solder joints.
-
Solder composition: The choice of solder composition is essential for mid-chip solder balls. Lead-based solders were traditionally used, but environmental regulations have led to the adoption of lead-free solders. Common lead-free compositions include tin-silver-copper (SAC) alloys.
-
Bump pitch and size: As the demand for higher I/O density increases, the pitch (distance) between solder balls and their size continue to decrease. This poses challenges in terms of manufacturing, inspection, and reliability.
-
Substrate and package design: The substrate and package must be designed to accommodate the mid-chip solder balls, with appropriate bond pad layout, surface finish, and routing.
Mid-Chip Solder Ball Materials and Compositions
The selection of solder material and composition is crucial for the performance and reliability of mid-chip solder balls. The solder must have the right melting point, wettability, electrical conductivity, and mechanical properties.
Lead-Based Solders
Traditionally, lead-based solders were widely used for mid-chip solder balls due to their favorable properties. The most common composition was tin-lead (SnPb), typically with a ratio of 63% tin and 37% lead (Sn63Pb37). Lead-based solders offer several advantages:
-
Low melting point: Sn63Pb37 has a melting point of around 183°C, which is suitable for reflow processes and minimizes thermal stress on the chip and substrate.
-
Good wettability: Lead-based solders have excellent wettability on various metal surfaces, ensuring good bonding and joint formation.
-
Ductility: The ductility of lead-based solders helps absorb stress and strain, improving the reliability of the solder joints.
However, due to environmental and health concerns, the use of lead in electronics has been restricted by regulations such as the Restriction of Hazardous Substances (RoHS) directive. This has led to the development and adoption of lead-free solders.
Lead-Free Solders
Lead-free solders have become the standard for mid-chip solder balls in recent years. The most common lead-free solder compositions are based on tin-silver-copper (SAC) alloys. Some popular SAC compositions include:
-
SAC305 (Sn96.5Ag3.0Cu0.5): This composition has been widely adopted as a lead-free alternative. It offers good mechanical strength, reliability, and compatibility with various surface finishes.
-
SAC105 (Sn98.5Ag1.0Cu0.5): This composition has a lower silver content compared to SAC305, which reduces cost while maintaining acceptable performance.
-
SAC0307 (Sn99.0Ag0.3Cu0.7): This composition has an even lower silver content and is used in some low-cost applications.
Other lead-free solder compositions may include elements such as bismuth, indium, or antimony to fine-tune properties like melting point, wettability, or mechanical strength.
Solder Composition | Melting Point (°C) | Key Characteristics |
---|---|---|
Sn63Pb37 | 183 | Excellent wettability, ductility, low melting point |
SAC305 | 217-220 | Good mechanical strength, reliability, compatibility |
SAC105 | 217-227 | Lower cost compared to SAC305, acceptable performance |
SAC0307 | 217-228 | Even lower cost, used in some low-cost applications |
Manufacturing Process for Mid-Chip Solder Balls
The manufacturing process for mid-chip solder balls involves several key steps to ensure reliable and high-quality solder bumps on the semiconductor chip.
Wafer Bumping
The first step is wafer bumping, where the solder balls are deposited onto the bond pads of the entire wafer before it is diced into individual chips. There are different methods for wafer bumping, including:
-
Evaporation: In this method, the solder material is evaporated through a metal mask onto the wafer. The mask defines the location and size of the solder bumps. After evaporation, the solder is reflowed to form spherical balls.
-
Electroplating: This method involves depositing the solder material by electroplating. A photoresist layer is patterned on the wafer to define the bump locations. The solder is then electroplated into the openings, followed by photoresist removal and reflow.
-
Printing: Solder paste, which is a mixture of solder powder and flux, can be printed onto the bond pads using a stencil. The paste is then reflowed to form solder balls.
Flip Chip Assembly
After the wafer is bumped and diced, the individual chips are ready for flip chip assembly. The key steps in flip chip assembly are:
-
Flux application: A thin layer of flux is applied to the substrate or the chip to remove oxides and enhance solder wettability.
-
Chip placement: The bumped chip is picked up, aligned, and placed onto the substrate with the solder balls facing the corresponding bond pads.
-
Reflow: The assembly is subjected to a controlled reflow process in a convection oven or using local heating methods. The solder balls melt and form a metallurgical bond with the substrate pads.
-
Underfill dispensing: After reflow, an underfill material is dispensed into the gap between the chip and substrate. The underfill is then cured, providing mechanical support and stress relief to the solder joints.
-
Inspection and testing: The assembled package undergoes inspection and electrical testing to ensure proper connections and functionality.
Step | Purpose |
---|---|
Wafer Bumping | Deposit solder balls onto chip bond pads |
Flux Application | Remove oxides and enhance solder wettability |
Chip Placement | Align and place bumped chip onto substrate |
Reflow | Melt solder to form metallurgical bond |
Underfill Dispensing | Provide mechanical support and stress relief |
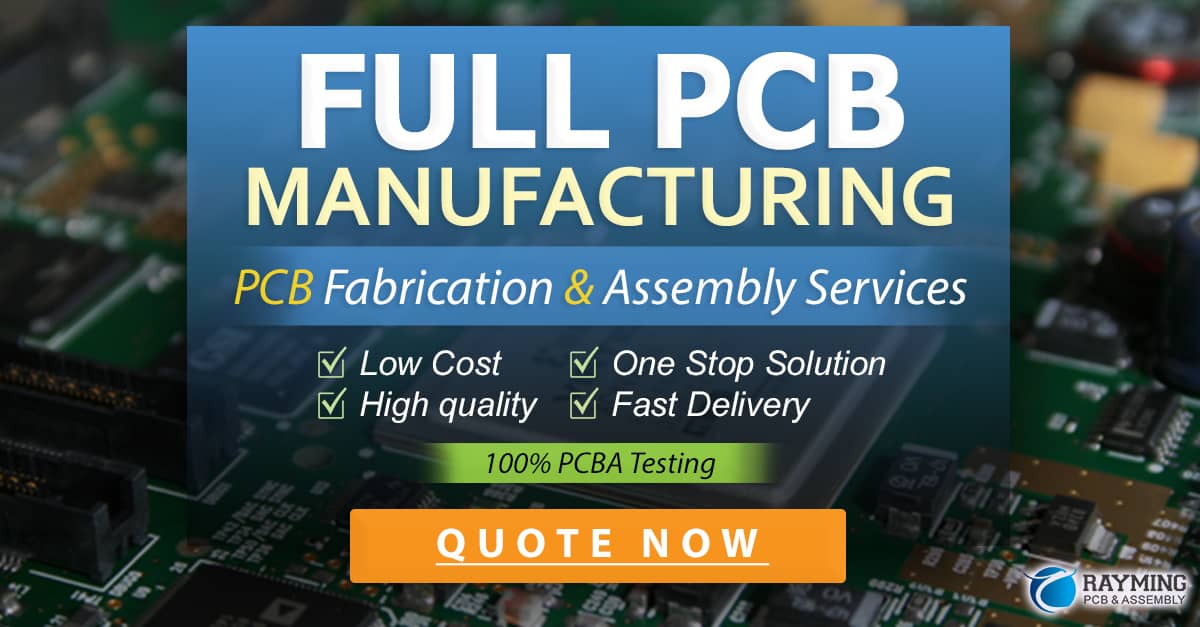
Reliability and Failure Mechanisms
The reliability of mid-chip solder balls is critical for the overall performance and lifetime of the electronic package. Several factors can impact the reliability of solder joints, and various failure mechanisms can occur.
Factors Affecting Reliability
-
Thermal cycling: Temperature fluctuations during operation can cause thermal stress and strain on the solder joints due to CTE mismatch between the chip and substrate. Repeated thermal cycling can lead to solder joint fatigue and cracking.
-
Mechanical stress: Mechanical stress from shock, vibration, or bending can impact the integrity of the solder joints. The package design and underfill material play a role in mitigating mechanical stress.
-
Solder composition: The choice of solder composition affects the mechanical properties, melting point, and resistance to electromigration and other failure mechanisms.
-
Manufacturing defects: Defects introduced during wafer bumping or flip chip assembly, such as voids, bridging, or misalignment, can compromise the reliability of the solder joints.
Common Failure Mechanisms
-
Solder joint fatigue: Repeated thermal cycling can cause the solder joints to undergo plastic deformation and eventually develop cracks. The cracks can propagate and lead to electrical failures.
-
Electromigration: Under high current density, the flow of electrons can cause the migration of solder atoms, leading to the formation of voids and hillocks. This can result in increased resistance or open circuits.
-
Intermetallic compound (IMC) growth: The reaction between the solder and the bond pad metallization can form IMCs at the interface. Excessive IMC growth can lead to brittle joints and reduced reliability.
-
Kirkendall voids: In some cases, the diffusion rate of atoms in the solder and the bond pad metallization can be different, leading to the formation of voids known as Kirkendall voids. These voids can weaken the solder joint and cause reliability issues.
To mitigate these failure mechanisms and improve reliability, several strategies are employed, such as:
- Optimizing the solder composition and reflow profile
- Using underfill materials to reduce stress and strain
- Implementing robust bond pad metallization and surface finishes
- Conducting thorough inspection and testing to detect and address manufacturing defects
Future Trends and Developments
As the demand for higher performance, smaller form factors, and increased functionality in electronic devices continues to grow, mid-chip solder balls are evolving to meet these requirements.
Smaller Pitch and Finer Solder Balls
One of the key trends is the reduction of solder ball pitch and size to accommodate higher I/O density. Researchers and manufacturers are developing technologies to enable finer pitch solder balls, such as:
-
Copper pillar bumps: Instead of using solder balls, copper pillar bumps with a thin solder cap are being explored. Copper pillars offer better electrical and thermal performance and can be fabricated with finer pitches.
-
Advanced packaging technologies: Packaging technologies like fan-out wafer-level packaging (FOWLP) and 2.5D/3D integration are being developed to enable higher I/O density and heterogeneous integration.
Advanced Solder Compositions
Research is ongoing to develop advanced solder compositions that offer improved reliability, thermal stability, and electromigration resistance. Some areas of interest include:
-
Composite solders: Solder compositions that incorporate nanoparticles or reinforcing materials to enhance mechanical and thermal properties are being investigated.
-
Low-temperature solders: Solders with lower melting points are being developed to reduce thermal stress during reflow and enable temperature-sensitive applications.
Wafer-Level Packaging
Wafer-level packaging (WLP) is gaining traction as a way to achieve smaller form factors and lower costs. In WLP, the entire wafer is packaged before being diced into individual chips. Mid-chip solder balls play a crucial role in WLP, enabling the interconnection between the chip and the redistribution layer (RDL).
3D Integration
3D integration technologies, such as through-silicon vias (TSVs) and stacked die packaging, are becoming increasingly important for high-performance applications. Mid-chip solder balls are used to interconnect the stacked dies, enabling shorter signal paths and higher bandwidth.
Trend | Key Developments |
---|---|
Smaller Pitch and Finer Solder Balls | Copper pillar bumps, advanced packaging technologies |
Advanced Solder Compositions | Composite solders, low-temperature solders |
Wafer-Level Packaging | Packaging entire wafer before dicing |
3D Integration | TSVs, stacked die packaging, shorter signal paths |
Frequently Asked Questions (FAQ)
-
Q: What is the difference between mid-chip solder balls and traditional wire bonding?
A: Mid-chip solder balls provide a direct electrical and mechanical connection between the chip and substrate, enabling higher I/O density, improved electrical performance, and smaller form factors compared to wire bonding. -
Q: Why is underfill material used in flip chip packages with mid-chip solder balls?
A: Underfill material is used to fill the gap between the chip and substrate to reduce thermal stress and strain on the solder joints caused by the CTE mismatch. It provides mechanical support and improves the reliability of the package. -
Q: What are the common failure mechanisms associated with mid-chip solder balls?
A: Common failure mechanisms include solder joint fatigue due to thermal cycling, electromigration caused by high current density, excessive intermetallic compound growth, and Kirkendall void formation. -
Q: How are mid-chip solder balls manufactured?
A: Mid-chip solder balls are typically manufactured through wafer bumping processes such as evaporation, electroplating, or printing. The solder balls are deposited onto the bond pads of the entire wafer before it is diced into individual chips. -
Q: What are some of the future trends and developments in mid-chip solder ball technology?
A: Future trends include the development of smaller pitch and finer solder balls, advanced solder compositions for improved reliability, wafer-level packaging for smaller form factors, and 3D integration technologies like TSVs and stacked die packaging.
Mid-chip solder balls have revolutionized semiconductor packaging, enabling the development of high-performance, compact, and reliable electronic devices. As technology advances, mid-chip solder balls will continue to evolve to meet the ever-increasing demands of the electronics industry.
0 Comments