Introduction to Laser Cut PCBs
Laser-cut PCBs, or printed circuit boards, are a revolutionary technology that has transformed the electronics industry. These PCBs are manufactured using a precise laser cutting process that offers numerous advantages over traditional PCB fabrication methods. In this article, we will explore the world of laser-cut PCBs, their manufacturing process, benefits, applications, and the future of this innovative technology.
How are Laser Cut PCBs Manufactured?
The Laser Cutting Process
Laser cutting is a highly precise and efficient method for manufacturing PCBs. The process involves using a high-powered laser to cut the desired circuit pattern into a copper-clad substrate. The laser vaporizes the unwanted copper, leaving behind the designed circuit traces. This process is computer-controlled, ensuring high accuracy and repeatability.
Advantages of Laser Cutting over Traditional Methods
Traditional PCB manufacturing methods, such as chemical etching, have several drawbacks. These include:
- Long processing times
- High material waste
- Environmental concerns due to the use of hazardous chemicals
- Limited design flexibility
In contrast, laser cutting offers the following advantages:
-
Rapid prototyping: Laser cutting significantly reduces the time required to produce PCB prototypes, enabling faster iteration and development cycles.
-
Increased precision: Laser cutting achieves much higher precision compared to traditional methods, allowing for the creation of fine-pitch traces and intricate designs.
-
Reduced material waste: As laser cutting is a subtractive process, it generates less material waste compared to chemical etching, making it a more environmentally friendly option.
-
Design flexibility: Laser cutting enables the creation of complex geometries and unconventional board shapes that are difficult or impossible to achieve with traditional methods.
Benefits of Laser Cut PCBs
Cost-effectiveness
Laser-cut PCBs offer significant cost savings compared to traditionally manufactured PCBs. The rapid prototyping capabilities and reduced material waste contribute to lower overall production costs. Additionally, the high precision of laser cutting minimizes the need for manual adjustments and rework, further reducing labor costs.
Enhanced Electrical Performance
The precise nature of laser cutting results in improved electrical performance of the PCBs. The clean and sharp edges of the laser-cut traces minimize signal reflections and impedance mismatches, leading to better signal integrity. This is particularly important for high-frequency applications where signal quality is critical.
Increased Durability
Laser-cut PCBs exhibit increased durability compared to their traditionally manufactured counterparts. The laser cutting process creates clean and burr-free edges, reducing the risk of mechanical stress and improving the overall structural integrity of the board. This enhanced durability translates to longer product life and reduced failure rates.
Rapid Prototyping and Faster Time-to-Market
One of the most significant advantages of laser-cut PCBs is the ability to rapidly prototype and iterate designs. The laser cutting process allows for quick turnaround times, enabling engineers to test and refine their designs in a matter of days rather than weeks. This accelerated prototyping process significantly reduces the overall development time and allows companies to bring their products to market faster.
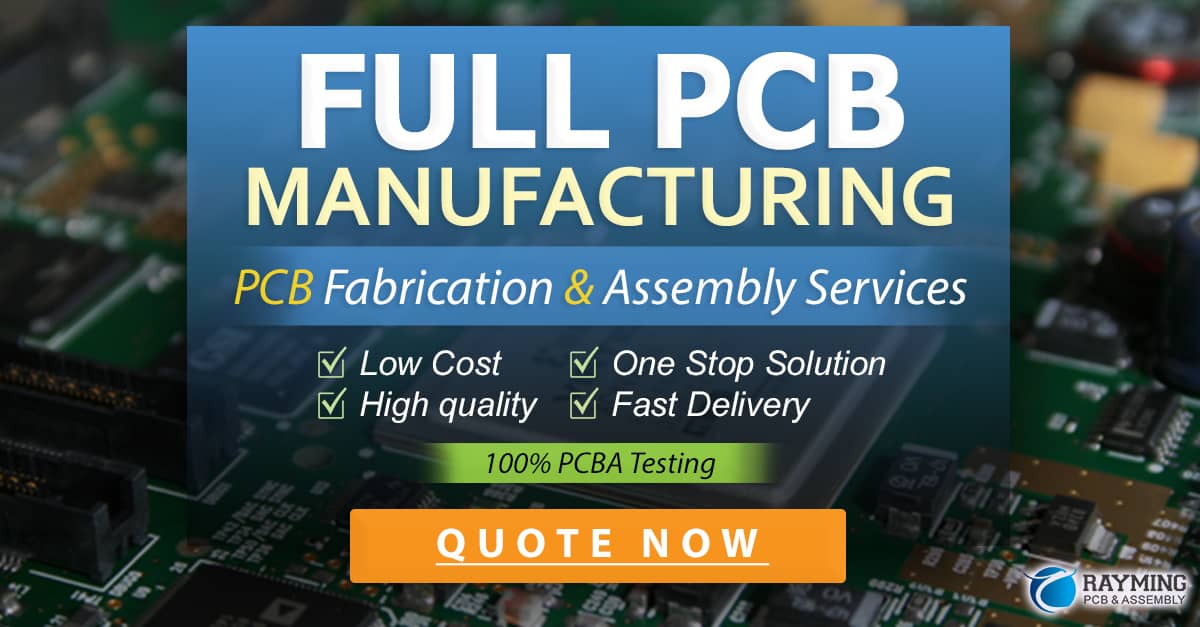
Applications of Laser Cut PCBs
Consumer Electronics
Laser-cut PCBs find extensive use in the consumer electronics industry. From smartphones and tablets to wearable devices and gaming consoles, these PCBs enable the creation of compact, high-performance electronic products. The precision and design flexibility offered by laser cutting allow for the integration of advanced features and functionality within limited space constraints.
Automotive Electronics
The automotive industry is increasingly adopting laser-cut PCBs for various electronic systems. These PCBs are used in engine control units, infotainment systems, advanced driver assistance systems (ADAS), and other critical automotive electronics. The enhanced durability and reliability of laser-cut PCBs make them well-suited for the demanding automotive environment.
Medical Devices
Laser-cut PCBs are crucial components in medical devices and equipment. From diagnostic instruments and patient monitoring systems to implantable devices, these PCBs enable the development of compact, reliable, and high-performance medical electronics. The precision and cleanliness achieved through laser cutting are essential for meeting the stringent requirements of the medical industry.
Aerospace and Defense
The aerospace and defense sectors rely on laser-cut PCBs for a wide range of applications, including avionics, radar systems, communication equipment, and military vehicles. The high precision, durability, and reliability of laser-cut PCBs make them ideal for the demanding environmental conditions and performance requirements of these industries.
The Future of Laser Cut PCBs
Advancements in Laser Technology
As laser technology continues to evolve, we can expect further advancements in laser-cut PCB manufacturing. Improvements in laser power, beam quality, and control systems will enable even higher precision, faster cutting speeds, and the ability to process a wider range of materials. These advancements will unlock new possibilities for PCB design and functionality.
Integration with Additive Manufacturing
The integration of laser cutting with additive manufacturing techniques, such as 3D printing, is an exciting prospect for the future of PCB fabrication. This combination would allow for the creation of fully three-dimensional circuit structures, enabling the development of highly integrated and compact electronic devices. The synergy between laser cutting and additive manufacturing has the potential to revolutionize the way we design and manufacture electronics.
Sustainable and Eco-friendly Manufacturing
Laser cutting offers a more environmentally friendly approach to PCB manufacturing compared to traditional methods. As sustainability becomes an increasingly important consideration, the adoption of laser-cut PCBs is expected to grow. The reduced material waste, elimination of hazardous chemicals, and lower energy consumption associated with laser cutting contribute to a more sustainable and eco-friendly manufacturing process.
Frequently Asked Questions (FAQ)
-
What materials can be used for laser-cut PCBs?
Laser-cut PCBs are typically made using copper-clad substrates such as FR-4, polyimide, or flexible materials like Kapton. The laser cutting process is compatible with a wide range of substrate materials, allowing for the creation of PCBs with specific properties and characteristics. -
How does the cost of laser-cut PCBs compare to traditionally manufactured PCBs?
Laser-cut PCBs often have a lower overall cost compared to traditionally manufactured PCBs. The rapid prototyping capabilities, reduced material waste, and minimal manual intervention associated with laser cutting contribute to cost savings. However, the specific cost comparison may vary depending on factors such as design complexity, production volume, and material choice. -
What are the limitations of laser-cut PCBs?
While laser cutting offers numerous advantages, there are some limitations to consider. Laser-cut PCBs may have slightly lower copper trace thickness compared to chemically etched PCBs due to the nature of the cutting process. Additionally, laser cutting may not be suitable for extremely high-volume production runs, where traditional manufacturing methods may be more cost-effective. -
Can laser cutting be used for multilayer PCBs?
Yes, laser cutting can be used for the fabrication of multilayer PCBs. The laser cutting process can be applied to individual layers, which are then laminated together to form the final multilayer structure. However, the complexity and precision requirements of multilayer PCBs may necessitate specialized equipment and processes. -
How do I choose a laser-cut PCB manufacturer?
When selecting a laser-cut PCB manufacturer, consider factors such as their experience, technical capabilities, quality control processes, and customer support. Look for manufacturers with a proven track record in producing high-quality laser-cut PCBs and those who can meet your specific design requirements. It’s also important to consider the manufacturer’s lead times, pricing, and ability to handle your production volume.
Conclusion
Laser-cut PCBs represent a significant advancement in the world of electronics manufacturing. With their precision, design flexibility, cost-effectiveness, and environmental benefits, laser-cut PCBs are transforming the way we create and innovate electronic products. From consumer electronics and automotive systems to medical devices and aerospace applications, laser-cut PCBs are enabling the development of more advanced, reliable, and compact electronic solutions.
As laser technology continues to evolve and integrate with other manufacturing techniques, the future of laser-cut PCBs looks incredibly promising. The ability to rapidly prototype, iterate, and bring products to market faster will drive innovation and competitiveness in the electronics industry. Moreover, the sustainable and eco-friendly nature of laser cutting aligns with the growing need for environmentally responsible manufacturing practices.
In conclusion, laser-cut PCBs are a game-changing technology that is reshaping the landscape of electronics manufacturing. By embracing this innovative approach, companies can unlock new possibilities, improve product performance, and stay ahead in an increasingly competitive market. As we move forward, laser-cut PCBs will undoubtedly play a crucial role in shaping the future of electronics and enabling the next generation of groundbreaking devices and applications.
0 Comments